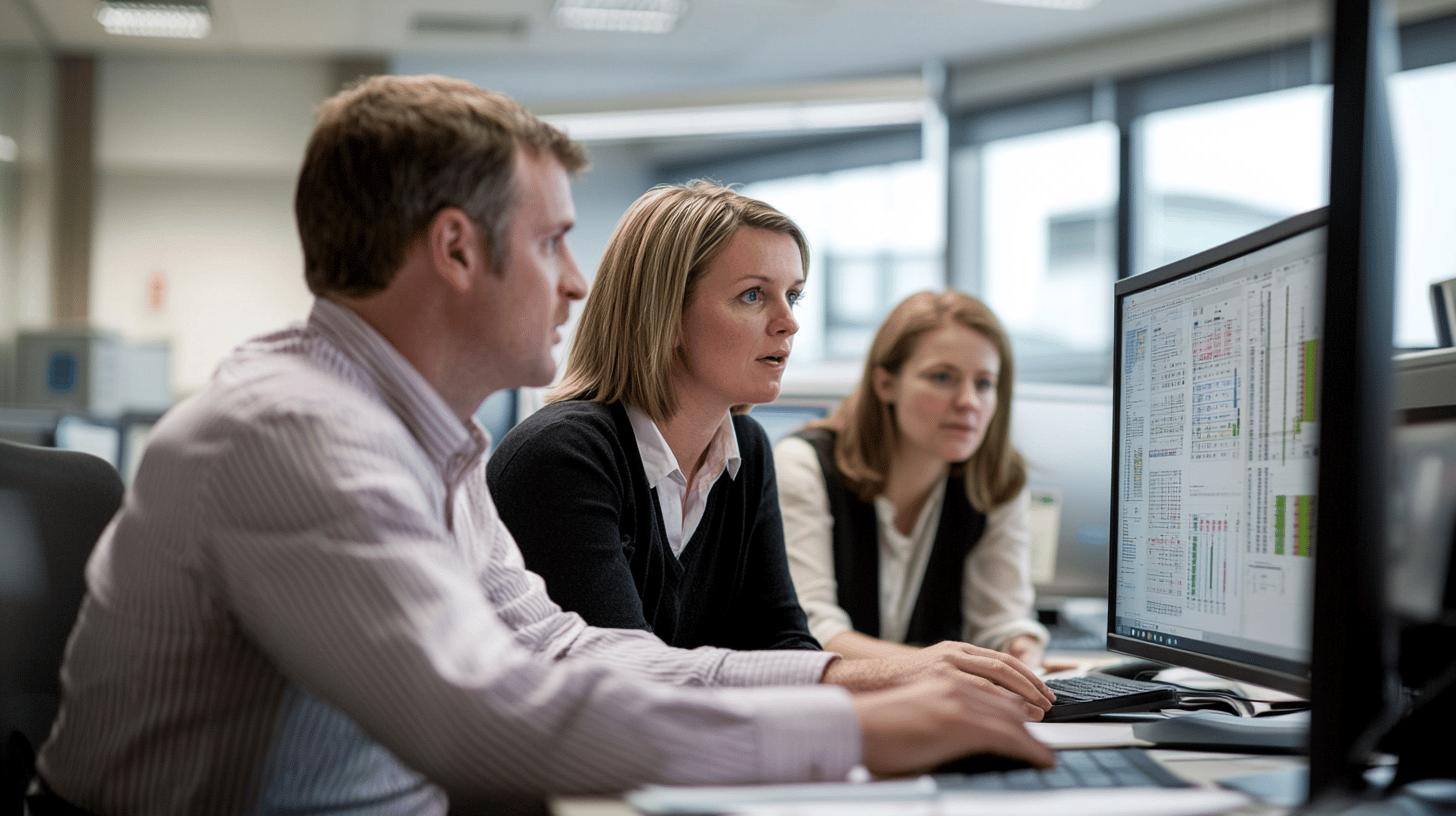
Integration with ERP Systems Boosts Safety and Quality
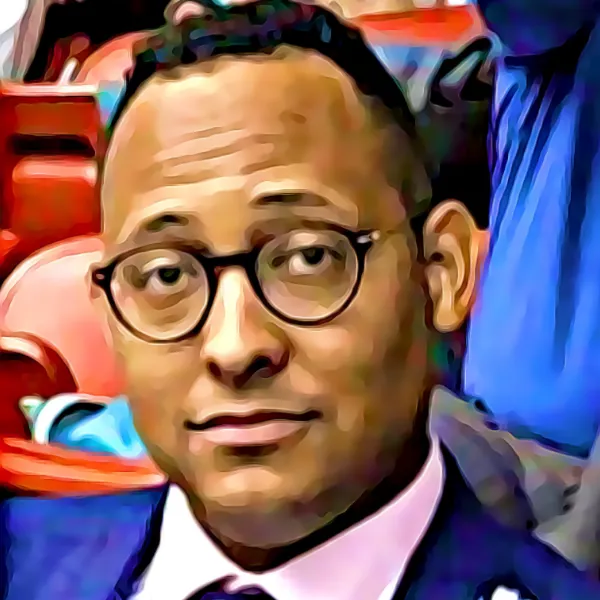
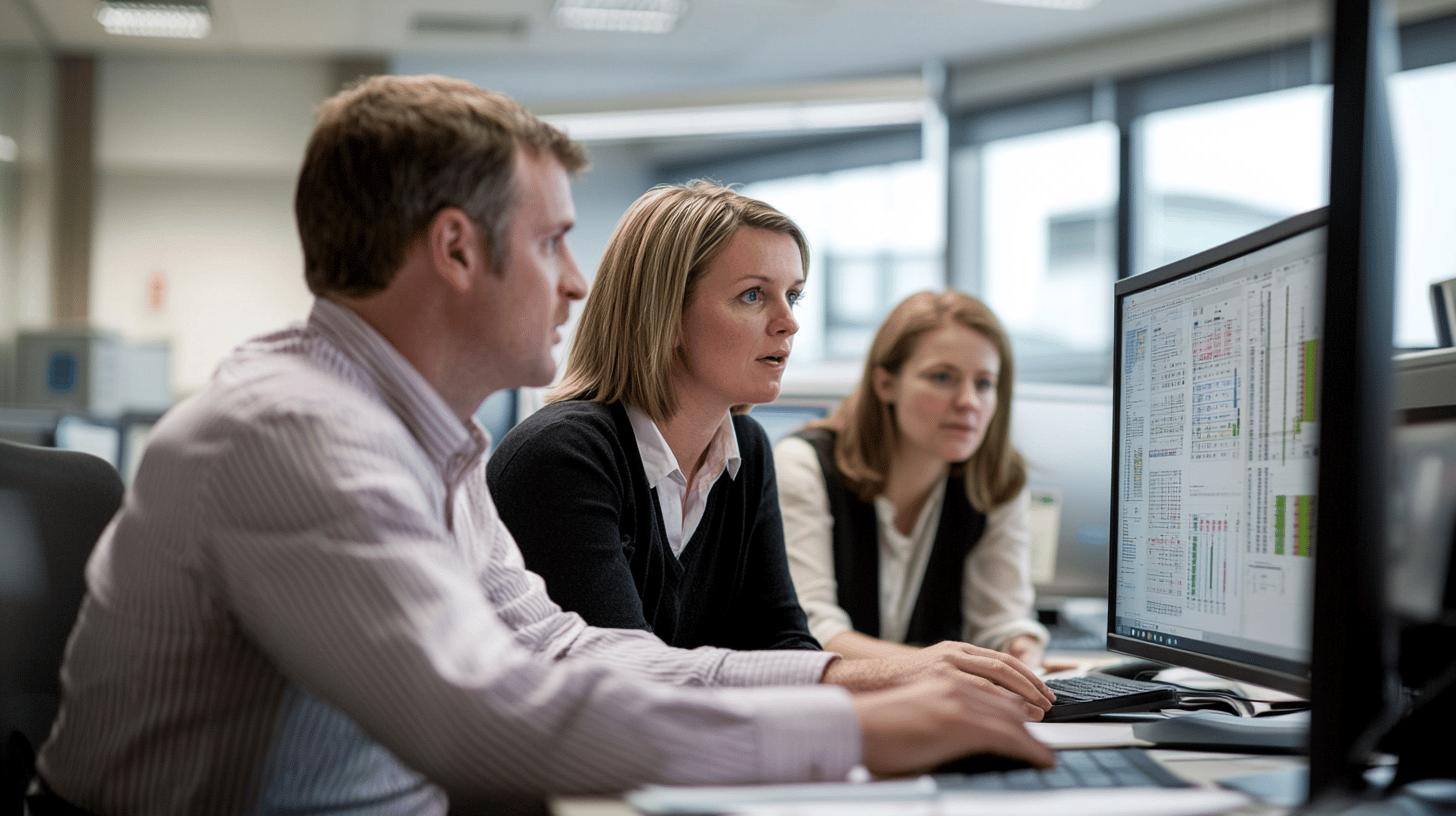
Integration with ERP Systems Boosts Safety and Quality
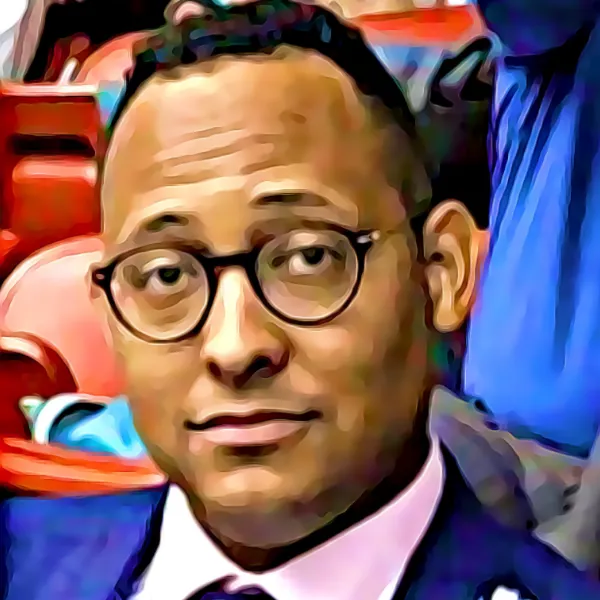
How ERP Integration Enhances Product Safety and Quality Assurance in Facilities Operations
Integration with ERP systems transforms how organisations manage product safety and quality assurance in facilities operations.
By integrating ERP systems into operational workflows, companies not only secure their quality standards but also harness a unified data approach that streamlines safety measures. integration with ERP systems is at the heart of these modern improvements, illustrating how digital transformation can elevate both security and operational precision. Q-Hub's specialised solutions create a centralised hub for operational data, replacing error-prone manual methods with streamlined automation. The common challenges in facilities management – disconnected systems, inconsistent data, and limited visibility – are effectively addressed through proper ERP integration, ensuring safety protocols and quality standards are consistently maintained.
Without integrated systems, facilities rely on spreadsheets, disparate software, or paper documentation to track crucial safety and quality data. This fragmented approach inevitably leads to errors and compliance gaps. ERP integration solves this by automating critical processes like batch tracking, where products are monitored from raw material receipt through to final delivery, ensuring complete traceability and regulatory compliance.
Real-time visibility represents another significant advantage. Modern ERP platforms provide immediate access to performance metrics and safety indicators, enabling teams to identify and address potential issues before they escalate. For example, quality managers can spot defect patterns emerging and implement corrective measures promptly, significantly reducing risks of recalls or compliance violations.
Transforming Data into Actionable Intelligence
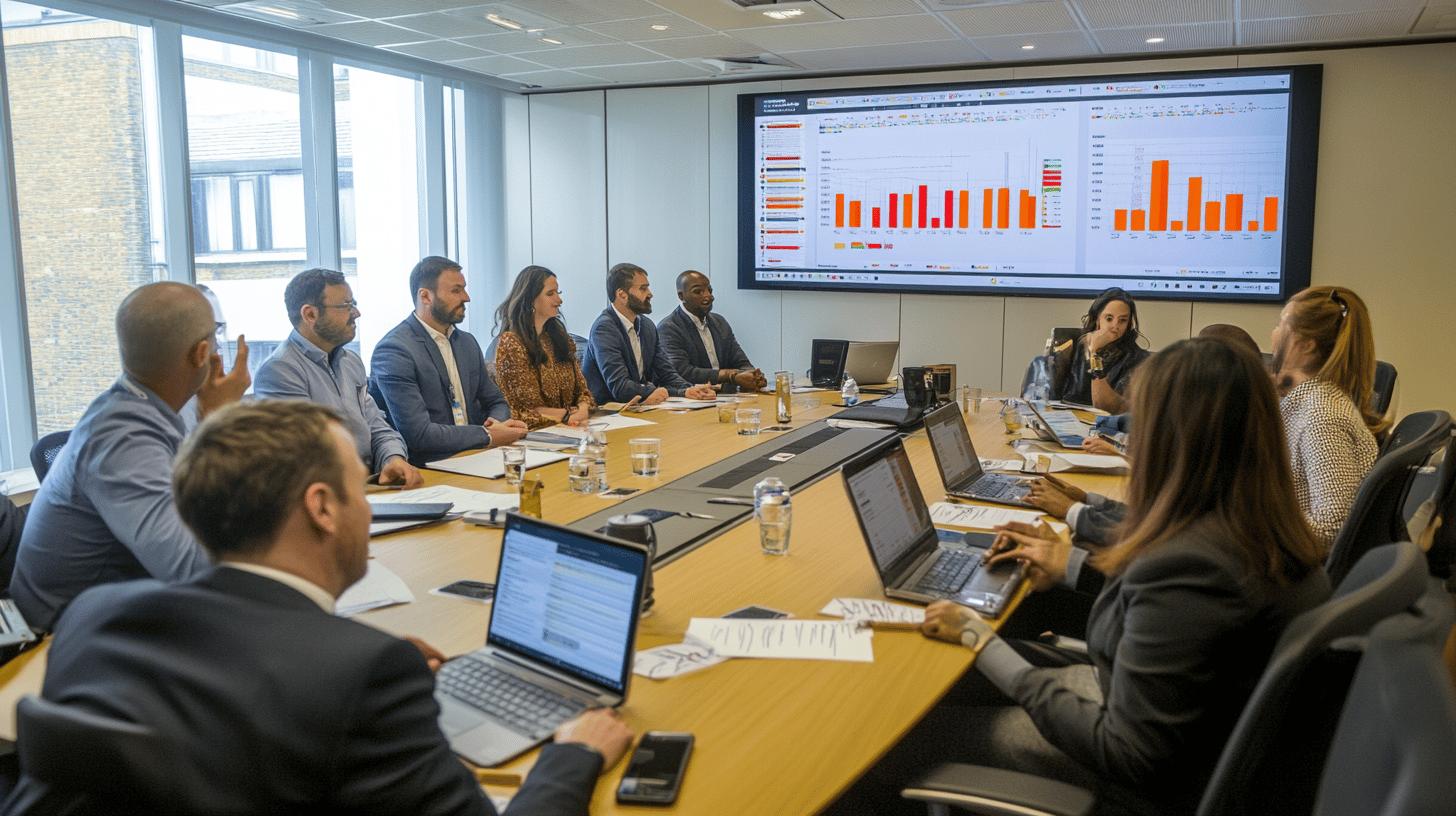
The real power of ERP integration lies in its ability to transform raw operational data into meaningful insights. Rather than simply collecting information, these systems help facilities teams interpret data patterns and make informed decisions. For manufacturers dealing with complex production processes, this capability proves invaluable for maintaining consistent quality and safety standards.
By implementing Q-Hub's customised QHSE solutions, organisations gain access to sophisticated analytics tools that highlight trends and correlations which might otherwise remain hidden in siloed systems.
The integration of modern data management solutions is a cornerstone of this digital evolution. These solutions not only enable facilities to process vast amounts of operational data with enhanced accuracy but also empower decision-makers to respond swiftly to quality issues, creating a resilient system where safety and reliability are continuously reinforced. Have you noticed how quickly quality issues can cascade through production when teams don't have visibility across departmental boundaries? ERP integration solves this by creating a single source of truth accessible to all stakeholders.
The transition from paper-based systems saved us countless hours while dramatically improving our safety compliance. Qhub digitised our processes, making everything more accessible and actionable for employees at all levels.
This real-world impact is evident in how Scottish Leather Group revolutionised their compliance management through digital transformation. By implementing Q-Hub's platform, they successfully unified processes across multiple ISO standards, streamlining everything from audit preparation to safety reporting.
Breaking Down Departmental Barriers
One of the most valuable benefits of ERP integration is improved cross-functional collaboration. When quality, safety, production, and maintenance teams all work from the same dataset, miscommunication decreases dramatically. This synchronisation is especially critical in high-risk environments where safety protocols must be meticulously followed.
Consider a pharmaceutical manufacturing facility where temperature control directly impacts product safety. With an integrated ERP system, production can immediately alert quality assurance about potential deviations, while maintenance receives automated alerts about equipment requiring attention – all through the same platform. This level of coordination simply isn't possible with disconnected systems.
Let's examine the key benefits that facilities operations gain through ERP integration:
- Enhanced data accuracy with automated collection and verification
- Improved regulatory compliance through standardised processes
- Faster incident response times with real-time alerts
- Reduced quality incidents through proactive monitoring
- Better resource allocation based on performance analytics
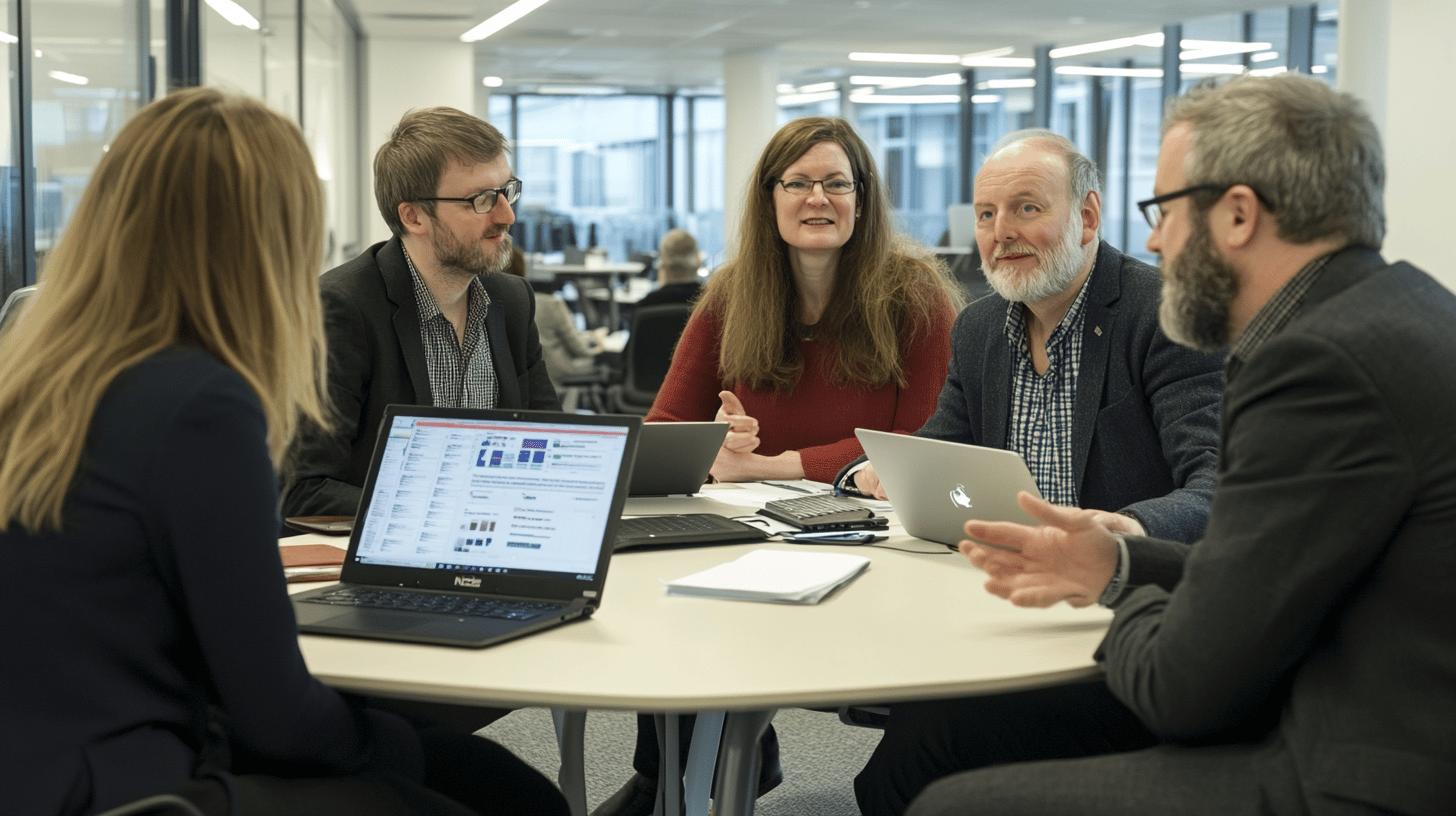
Overcoming Implementation Hurdles
While the benefits are compelling, successful ERP integration isn't without challenges. Data migration represents one of the biggest hurdles – how do you ensure decades of quality records transition smoothly into a new system? The answer lies in thorough preparation and cleansing.
Before implementation, organisations should conduct comprehensive data audits, identifying critical information and standardising formats. For example, Weston Aerospace faced significant inefficiencies with their legacy systems before implementing Q-Hub's solution. Their transformation involved carefully mapping existing processes and prioritising which data elements were essential for compliance and operational excellence.
Change management presents another significant challenge. Even the most advanced system will underperform if staff resist adoption. Successful implementations involve early stakeholder engagement, tailored training programmes, and clearly communicating the "why" behind the change.
Challenge | Solution Approach | Expected Outcome |
---|---|---|
Data silos and inconsistency | Comprehensive data mapping and cleansing | Single source of truth for quality/safety data |
User resistance to new systems | Tailored training and change champions | High adoption rates and system engagement |
Complex compliance requirements | Configurable workflows and automated checks | Simplified audit processes and fewer non-conformances |
Real-World Impact: Measurable Improvements
The practical benefits of ERP integration become clear when examining real-world case studies. For instance, Fowlers of Bristol struggled with outdated paper-based systems that created bottlenecks in their quality assurance processes. After implementing Q-Hub's platform, they successfully centralised their document management and quality workflows, driving significant improvements in their "Right First Time" performance metrics.
Similarly, Rocal Insulating Panels transformed their safety management by digitising accident reporting and investigations. Their previous paper-based approach resulted in incomplete records and delayed investigations. With an integrated ERP solution, they achieved faster resolution times and better departmental accountability through automated workflows and dashboards.
These examples demonstrate how ERP integration delivers tangible improvements in both product safety and quality assurance:
- Reduced time spent on compliance documentation by up to 60%
- Decreased quality-related incidents through proactive monitoring
- Improved audit outcomes with comprehensive digital evidence
- Enhanced visibility across departmental boundaries
The Future of Safety and Quality Management
Looking ahead, ERP integration will continue evolving alongside emerging technologies. IoT sensors are already transforming how facilities collect quality and safety data, with equipment providing real-time measurements directly into ERP systems without human intervention. This automation eliminates transcription errors while providing unprecedented visibility into operations.
Artificial intelligence and machine learning represent the next frontier, enabling predictive quality assurance rather than reactive approaches. By analysing historical data patterns, these systems can identify subtle indicators that often precede quality issues, allowing intervention before problems occur.
Blockchain technology is also gaining traction for its ability to create immutable records of quality checks and safety verifications throughout supply chains. This capability proves especially valuable in heavily regulated industries where demonstrating compliance history is critical.
As these technologies mature, Q-Hub continues developing customised QHSE solutions that help organisations not just maintain compliance, but transform their approach to quality and safety management. The future belongs to operations that can leverage data effectively to prevent issues rather than simply documenting them after the fact.
Ready to transform your approach to safety and quality management? Discover how Q-Hub's tailored ERP solutions can streamline your facilities operations while enhancing compliance and operational excellence.
Start using Q-Hub today
- Manage compliance in one place
- Streamline your teams and tasks
- Use Q-Hub free for 30 days