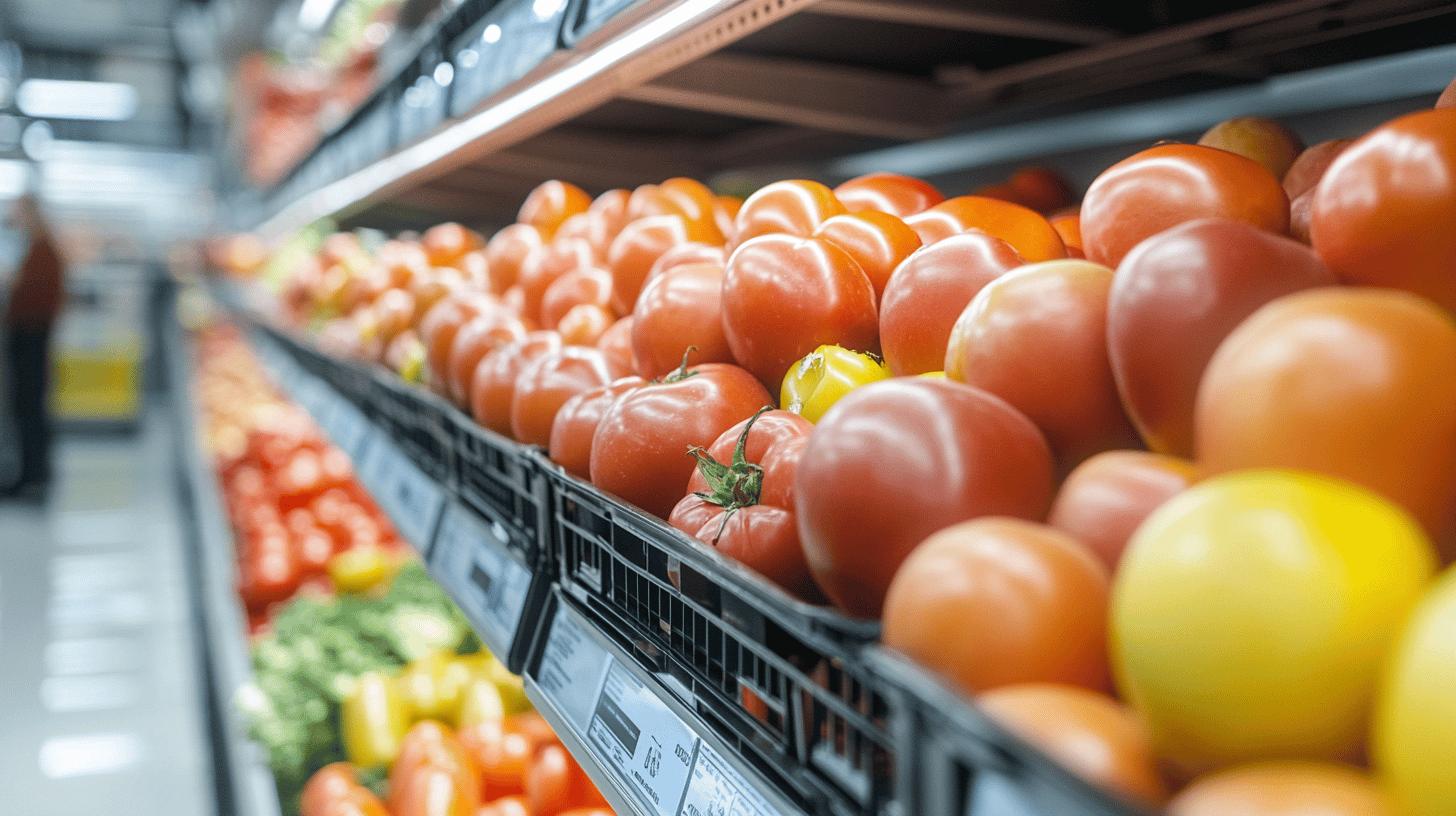
ERP Integration Boosts Traceability in Food Operations
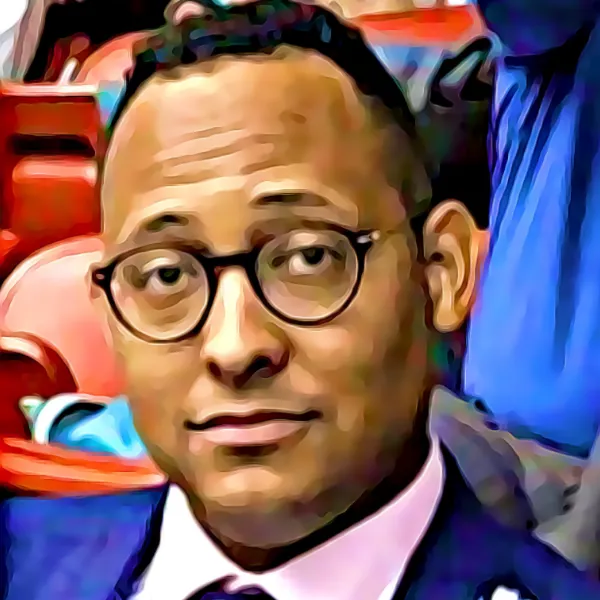
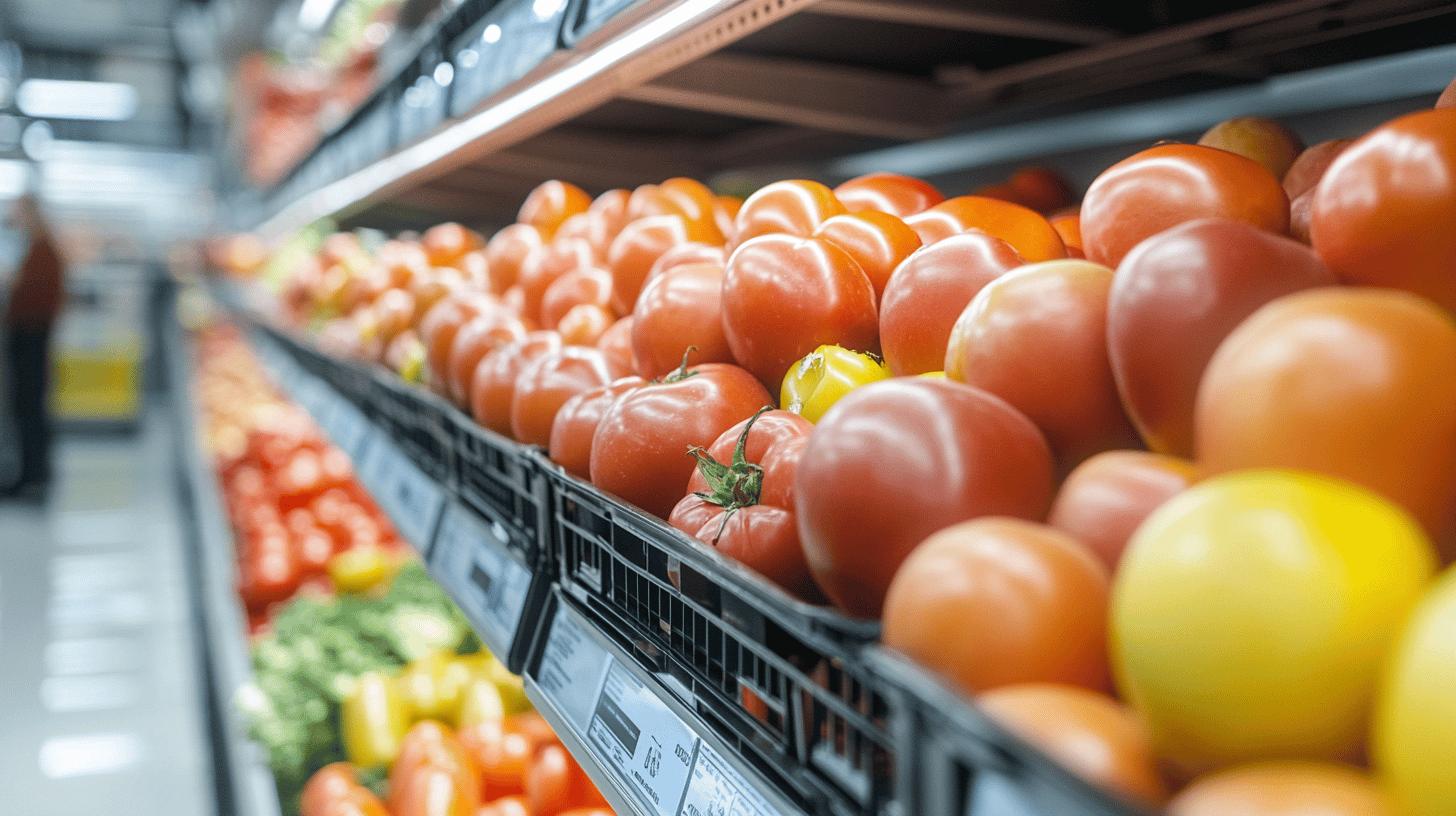
ERP Integration Boosts Traceability in Food Operations
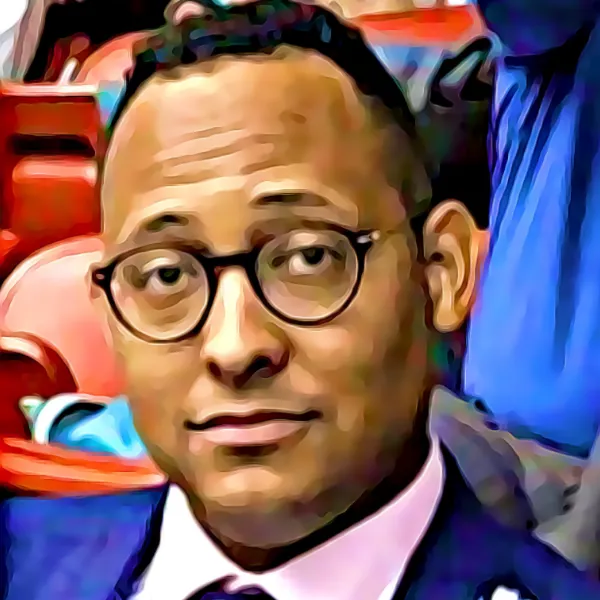
How ERP Integration Enhances Traceability in Food Processing Operations
ERP integration enhancing traceability management within food processing operations has evolved from optional to essential in today's complex supply chains. Modern food processors require robust systems that monitor products from farm to fork while ensuring regulatory compliance. Q-Hub's specialised software solutions address this need by creating unified frameworks that centralise data, streamline workflows, and enhance visibility across operations. Without such integration, food manufacturers risk not only inefficiencies but significant compliance gaps and potential consumer safety issues.
ERP systems transform food traceability by connecting previously siloed data across procurement, production, and logistics. Batch tracking capabilities allow manufacturers to follow ingredients throughout the entire production journey. When contamination concerns arise, these systems enable precise identification of affected products in minutes rather than days—saving time, resources, and potentially, lives. This precision aligns with rigorous standards like ISO 22000 while building consumer confidence through demonstrated commitment to safety.
The Digital Backbone of Modern Food Safety
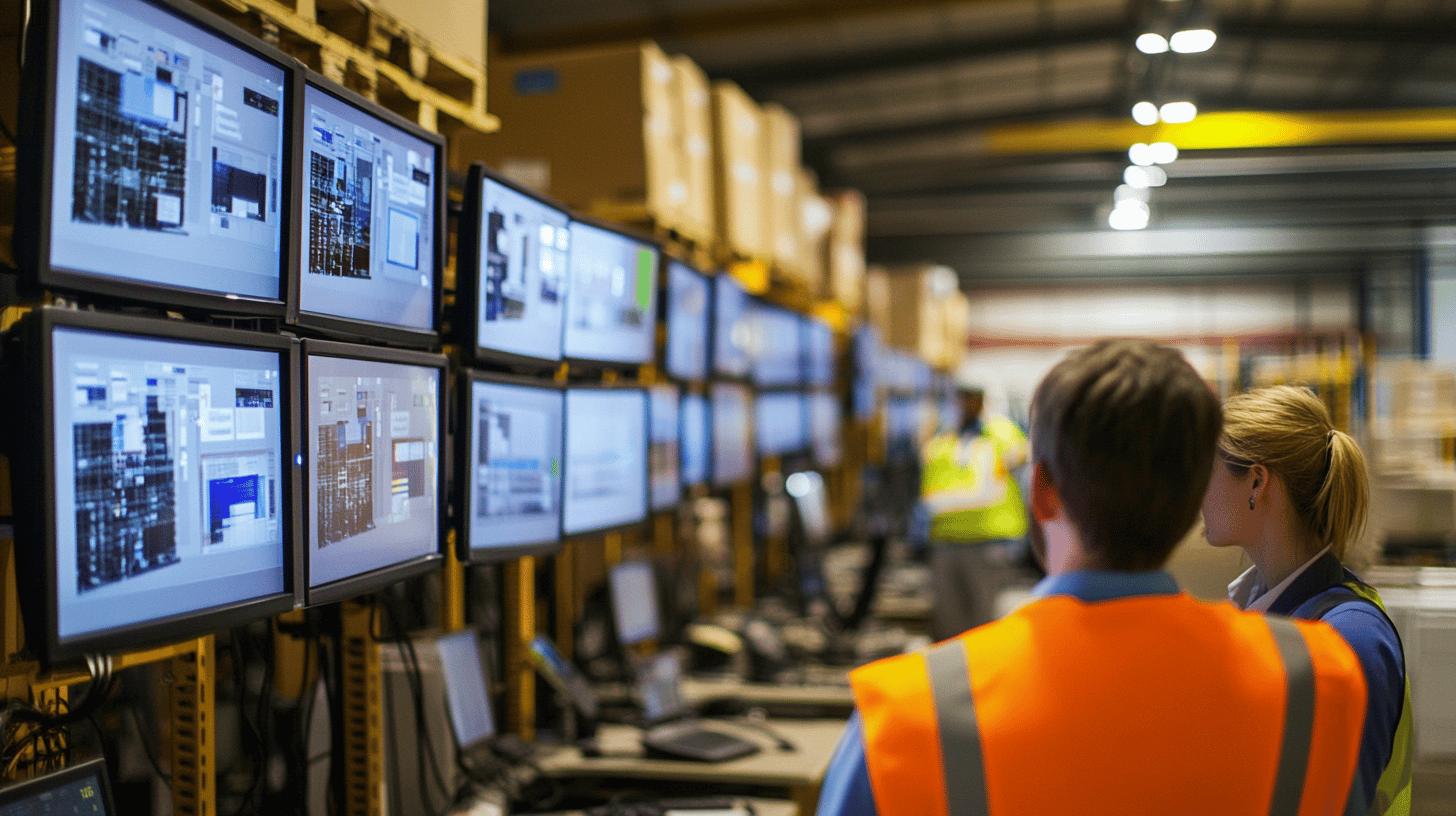
The power of ERP in food processing stems from its ability to create a single source of truth across operations. Think of it as your operation's central nervous system—collecting information, processing it, and directing appropriate responses. When a quality deviation occurs, the system doesn't just record it—it triggers immediate corrective actions and notifies the right people.
The implementation of Qhub resulted in transformative outcomes. Enhanced compliance management allowed our team to seamlessly manage multiple ISO standards within a single platform, significantly reducing audit preparation time and freeing resources for value-added activities.
This real-time capability represents a fundamental shift from reactive to proactive quality management. Rather than discovering issues during scheduled quality checks or—worse—after products reach consumers, ERP systems flag anomalies instantly. For instance, if temperature controls fall outside acceptable ranges during processing, alerts trigger immediate intervention, preventing potentially unsafe products from proceeding further in production.
Companies embracing these integrated solutions typically experience:
- 60-80% reduction in recall response times through precise batch identification
- Enhanced regulatory compliance with automated documentation and audit trails
- Significant waste reduction through improved inventory management
- Greater consumer trust through demonstrated commitment to transparency
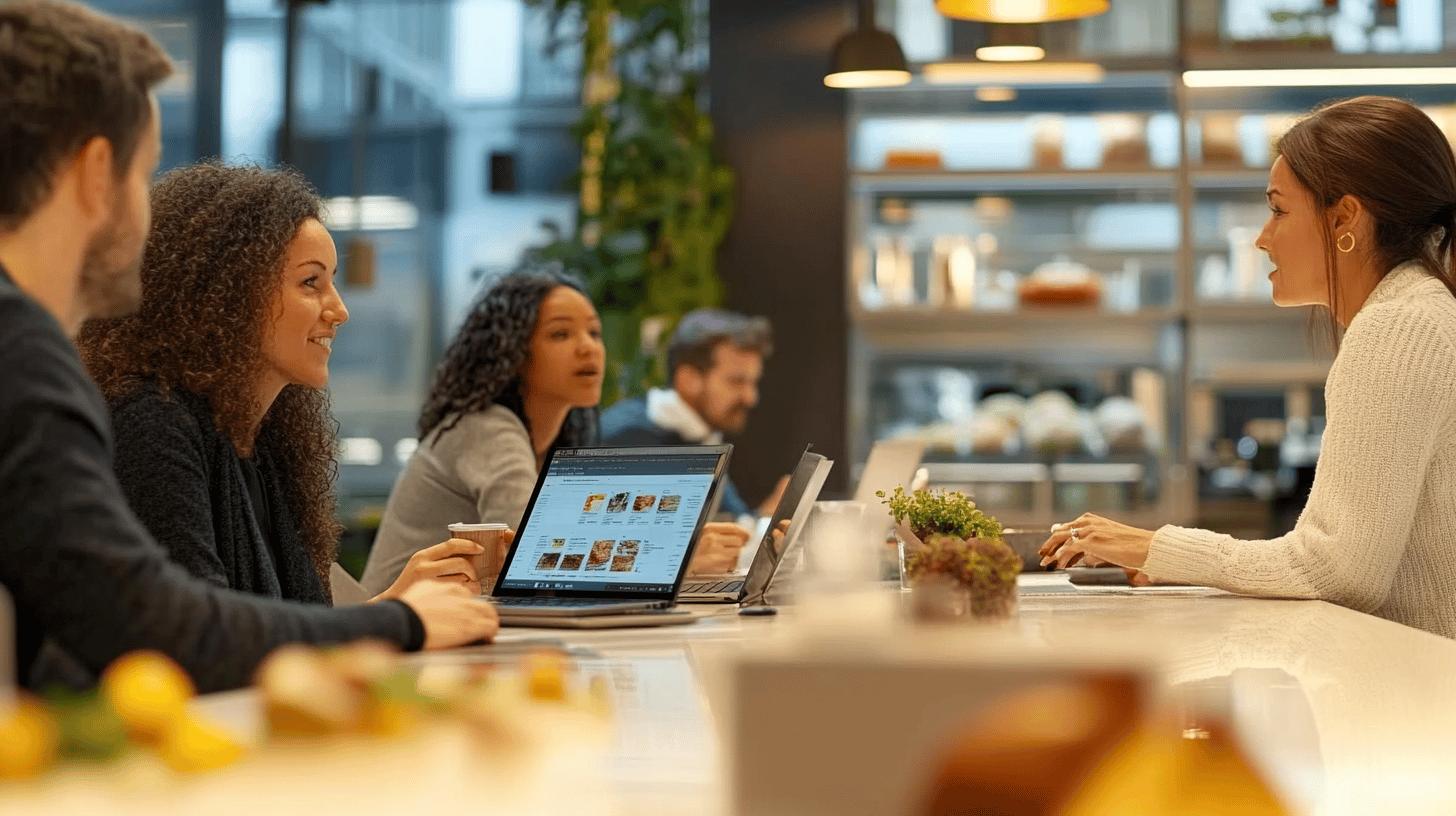
Breaking Down Silos for Enhanced Compliance
Food safety regulations continue to grow more complex globally, with standards like FSMA and ISO 22000 requiring unprecedented levels of documentation and verification. Here, ERP systems prove invaluable by automating compliance processes that would otherwise consume countless hours of manual effort. Q-Hub's compliance solutions integrate these requirements into daily workflows rather than treating them as separate administrative burdens.
Automated documentation ensures every production step is recorded, time-stamped, and linked to specific batches or lots. When auditors arrive—whether internal or from regulatory bodies—all required information is instantly accessible. This alone transforms compliance from a stressful scramble to a routine demonstration of operational excellence.
<table border="0"> <tr><th>Compliance Activity</th><th>Before ERP Integration</th><th>After ERP Integration</th></tr> <tr><td>Audit Preparation</td><td>3-5 days</td><td>4-6 hours</td></tr> <tr><td>Trace-Back Exercise</td><td>24+ hours</td><td>Minutes</td></tr> <tr><td>Recall Management</td><td>Days</td><td>Hours</td></tr> <tr><td>Compliance Reporting</td><td>Weekly manual effort</td><td>Automated real-time</td></tr> </table>Transforming Supply Chain Visibility from Aspiration to Reality
Perhaps the most significant advantage of ERP integration is the unprecedented supply chain visibility it provides. Similar to how Scottish Leather Group revolutionised their operations with Q-Hub's solution, food processors can gain end-to-end transparency across complex supply networks. This visibility enables manufacturers to track ingredients from their source, monitor processing conditions, and verify distribution paths—all within a single system.
This level of transparency doesn't just satisfy regulatory requirements; it fundamentally changes how businesses operate. Imagine spotting a potential ingredient shortage weeks before it affects production, or identifying quality trends that might indicate emerging problems with a particular supplier. With integrated ERP systems, these insights become routine rather than exceptional.
For food processors working with numerous suppliers and ingredients, this capability transforms risk management. Rather than reacting to problems after they occur, businesses can proactively identify and address potential issues before they impact operations or consumer safety.
The ROI Equation: Why Investment in Traceability Pays Dividends
The business case for ERP-enhanced traceability extends far beyond compliance. While avoiding regulatory penalties provides immediate financial justification, the long-term return on investment comes from operational efficiencies and risk reduction. With recalls potentially costing millions in direct expenses and immeasurable damage to brand reputation, systems that minimize these risks deliver substantial ROI.
Inventory optimization represents another significant cost benefit. ERP systems provide precise visibility into ingredient usage, helping processors maintain optimal stock levels while reducing waste from expired or unused materials. For businesses working with perishable ingredients, these savings alone can justify the investment in integrated systems.
Labor efficiency gains further strengthen the ROI case. As Weston Aerospace discovered after implementing Q-Hub's solutions, automating routine compliance tasks frees staff to focus on higher-value activities. Rather than spending hours compiling documentation or reconciling records, quality teams can concentrate on process improvements and proactive quality initiatives.
Navigating Implementation Challenges with Strategic Partnerships
Despite the clear benefits, implementing ERP systems for traceability isn't without challenges. Many food processors struggle with legacy systems, data migration issues, and resistance to change. Q-Hub's approach addresses these obstacles through phased implementation and comprehensive support, similar to their work with BMC Analysis.
When legacy systems contain years of valuable production data, careful migration strategies preserve this information while enabling the enhanced capabilities of modern platforms. Similarly, when staff accustomed to paper-based processes express concerns about digital transitions, targeted training and change management support smooth the transition.
The most successful implementations typically share common elements: clear objectives, phased rollouts, cross-functional teams, and ongoing support. By addressing both technical and human factors, these approaches ensure ERP systems deliver their full potential for enhancing traceability.
Ready to transform your food processing operations with enhanced traceability? Q-Hub's customised software solutions combine industry expertise with cutting-edge technology to streamline compliance, improve visibility, and optimize performance across your entire operation. Discover how our tailored approach can help you achieve operational excellence while ensuring the highest standards of food safety and regulatory compliance.
Start using Q-Hub today
- Manage compliance in one place
- Streamline your teams and tasks
- Use Q-Hub free for 30 days