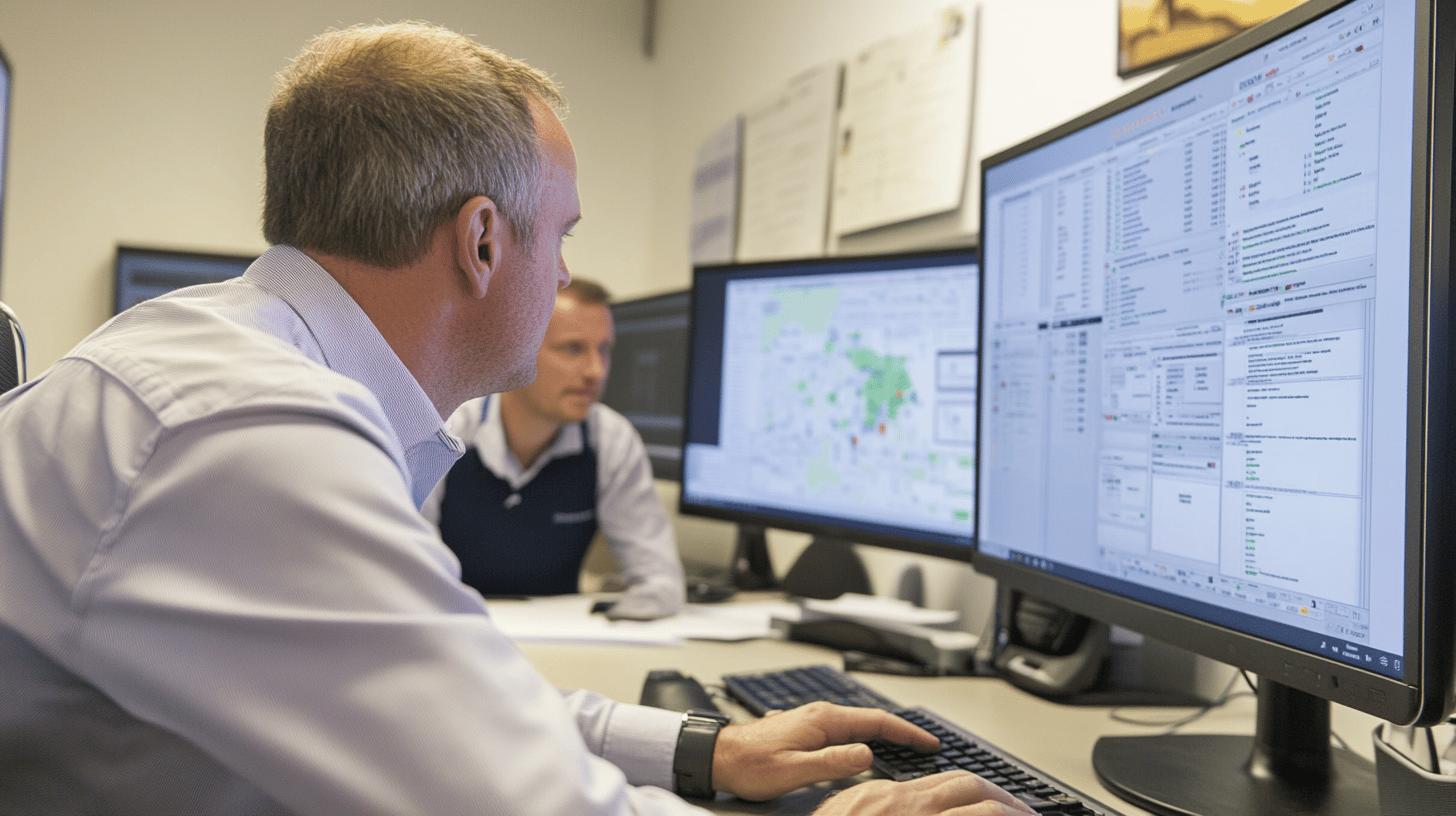
Integration with ERP Systems Boosts Engineering Training
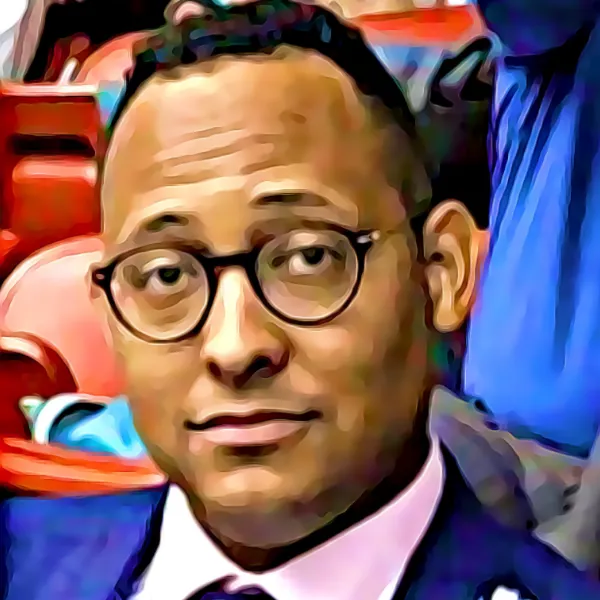
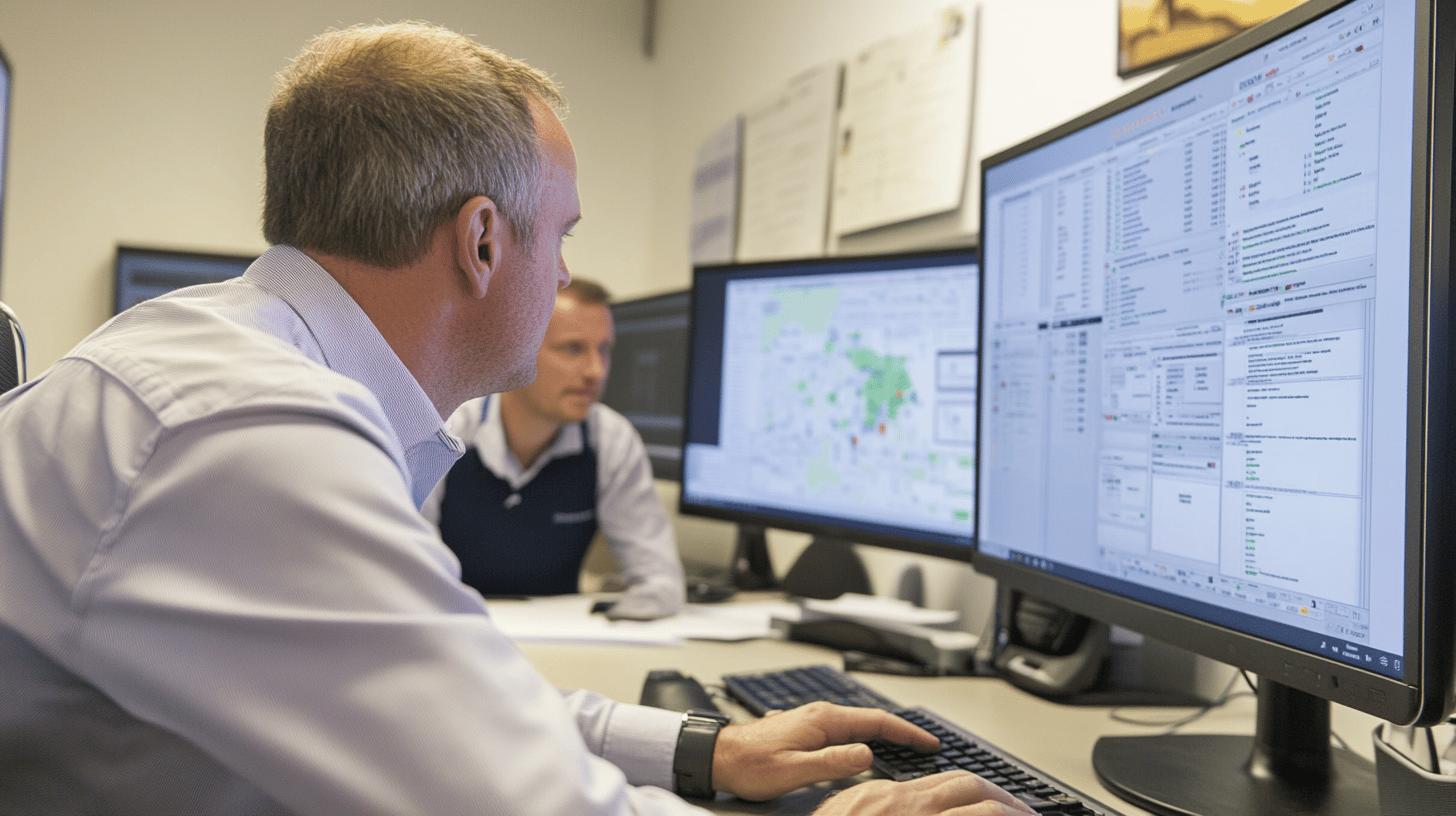
Integration with ERP Systems Boosts Engineering Training
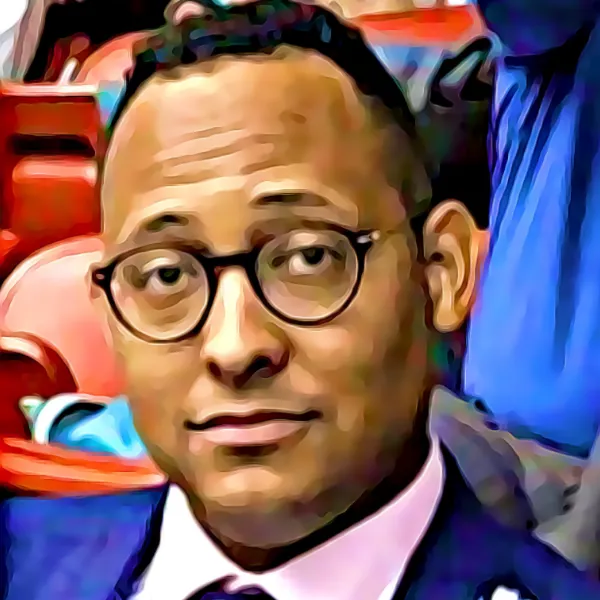
How ERP Integration Drives Training and Competence Management in Engineering Operations
Integration with ERP systems enhancing training and competence management workflows in engineering operations is revolutionising how engineering teams develop essential skills.
By integrating robust solutions such as integration with ERP systems, engineering firms can automate training workflows and track competencies with greater accuracy. This strategic integration not only simplifies the administrative burden but also ensures that teams stay updated with evolving technical standards, paving the way for continuous improvement and operational excellence. Using comprehensive ERP platforms to streamline workforce training has become fundamental to operational efficiency. The unification of these tools with training workflows delivers measurable results—creating faster, smarter, and more reliable workforce development.
ERP systems centralise all employee training data, from certifications to skill assessments, in one accessible location.
Leveraging efficient techniques like user training and onboarding further complements these systems by ensuring that every team member is seamlessly integrated into the digital workflow. This combined approach helps organisations not only manage compliance and competence more effectively but also fosters a culture where continuous learning transforms operational challenges into opportunities for growth. This eliminates the need to juggle multiple spreadsheets or standalone software. When an aerospace engineer's certification is about to expire, the system automatically flags it, prompting immediate action without manual intervention.
Beyond tracking, these systems automate training workflows, reducing administrative burden significantly. Tasks like scheduling sessions and generating reports become seamless processes. A UK automotive firm reported 25% reduction in training setup time after implementing ERP training modules.
Transforming Workforce Capabilities Through Digital Integration
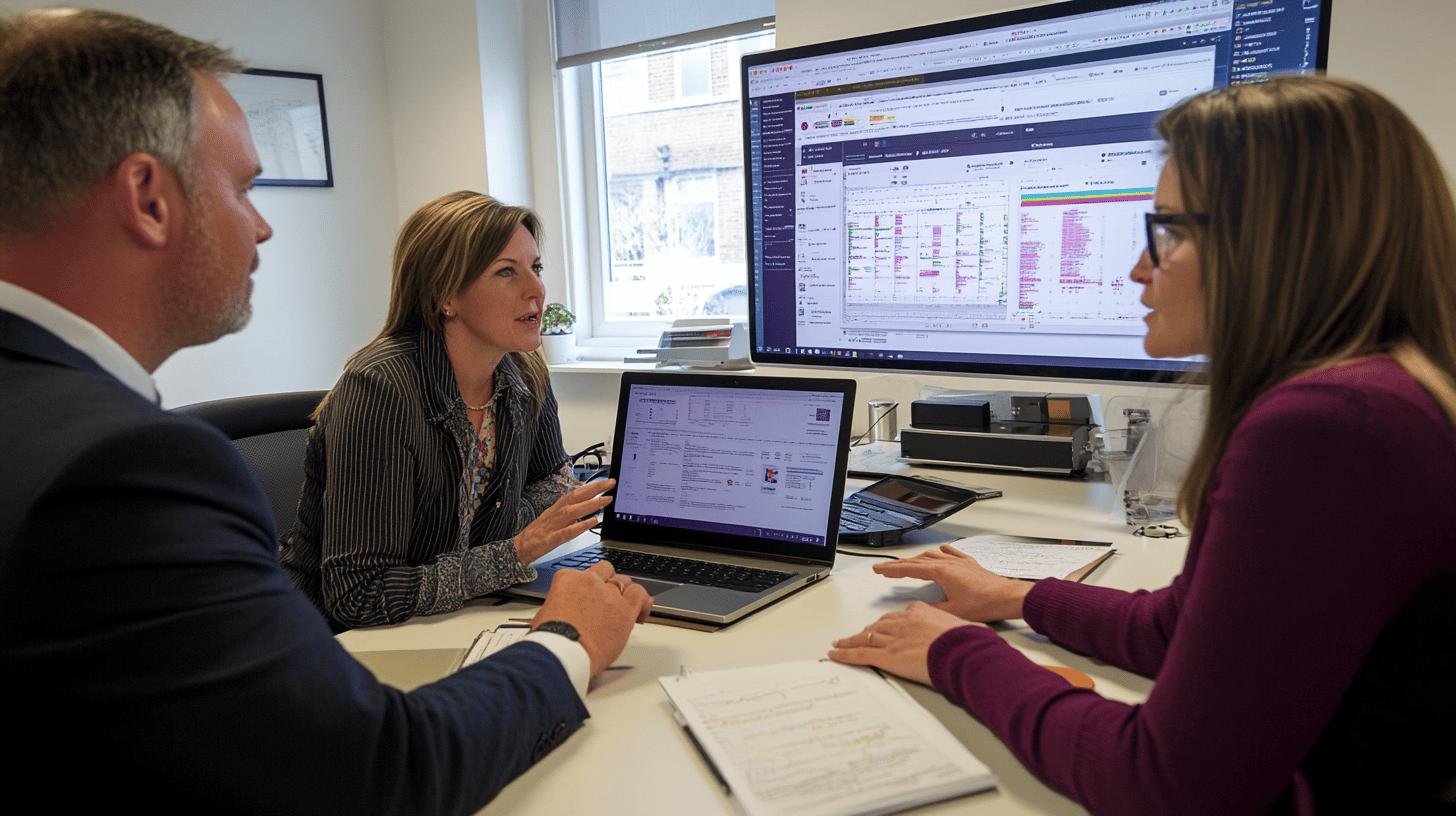
One of the most powerful aspects of ERP integration is competency-based training alignment. These systems map training programs directly to role-specific skills, ensuring relevance and measurable outcomes. When an engineering firm needs to upskill staff on new machinery, the ERP system identifies employees requiring training, assigns appropriate courses, and tracks progress automatically.
Q-Hub's comprehensive software solutions specialise in exactly this kind of digital transformation, helping engineering operations streamline their competency management through integrated systems that connect training with operational requirements.
The integration of training management with ERP platforms isn't just an upgrade—it's a complete reimagining of how engineering teams develop and maintain their skills in an increasingly complex technical landscape.
Companies implementing these integrated systems have reported up to 30% reduction in operational costs through streamlined processes and elimination of inefficiencies.
Key Benefits of ERP Training Modules for Engineering Operations
Integrating ERP systems with training and competence management transforms engineering workforce development. This synchronisation eliminates inefficiencies, streamlines assessments, and ensures staff development aligns perfectly with operational goals.
ERP training modules excel at creating customised learning paths tailored to specific roles within engineering operations. Rather than generic programs, these pathways focus precisely on relevant skills. An aerospace company might design paths for advanced materials engineering, while automotive manufacturers might focus on robotics integration.
Competency mapping tools enable organisations to identify skill gaps with remarkable precision. For example, when a civil engineering team prepares for infrastructure projects but lacks geotechnical expertise, the ERP system highlights this gap, assigns relevant training, and tracks progress until the team is fully prepared.
Achieving Measurable Performance Improvements
Automated assessments represent another significant advancement. When a mechanical engineer completes a safety training module, they receive immediate data-driven feedback on strengths and improvement areas, ensuring consistent evaluation across the organisation.
These comprehensive capabilities transform engineering staff development into a strategic asset. Companies using Q-Hub's digital transformation solutions report significant improvements in training effectiveness and compliance management across their engineering operations.
<table border="0"> <tr><th>Training Management Metric</th><th>Before ERP Integration</th><th>After ERP Integration</th></tr> <tr><td>Training Record Access Time</td><td>Hours to Days</td><td>Seconds</td></tr> <tr><td>Certification Tracking Accuracy</td><td>~70%</td><td>~99%</td></tr> <tr><td>Compliance Reporting Time</td><td>Days</td><td>Minutes</td></tr> <tr><td>Training Resource Utilisation</td><td>60-70%</td><td>85-95%</td></tr> </table>Best Practices for Enhancing Competence Management Workflows through ERP Integration
<<Integration with ERP systems enhancing training and competence management workflows in engineering operations offers a transformative approach to workforce planning. This fusion provides a clear path to streamline workflows, identify competency gaps, and automate training programs. The question is: how do you implement this effectively?
Identifying Skill Gaps Through Data-Driven Analysis
Competency gap analysis is the essential first step. Evaluate your current workforce capabilities against operational demands. For teams transitioning to new technologies like robotics, ERP systems can flag gaps in specialised skills such as programming or maintenance.
Once identified, these systems assign tailored training programs with real-time progress tracking, ensuring employees develop the right skills at the right time—eliminating inefficiencies and guesswork.
Stakeholder engagement is equally crucial. ERP integration requires collaboration across departments. Engineers, supervisors, HR teams, and IT professionals must contribute to the planning process to ensure the system aligns with practical workflows rather than disrupting them.
Building Automated Excellence Into Everyday Operations
The real power comes from training program automation. Tasks like assigning courses, scheduling sessions, and generating performance reports become automated processes. An aerospace firm using such workflows reduced administrative overhead by 30% while improving compliance reporting accuracy.
Companies looking to optimise their engineering operations with Q-Hub's software solutions find that this automation creates significant operational cost savings while enhancing compliance management.
Finally, implement continuous system evaluation. Regular audits of system performance, user adoption rates, and training outcomes ensure the integration remains aligned with your strategic workforce planning, allowing you to adapt to evolving industry standards.
Case Studies: Successful ERP Integration in Engineering Training Management
Integration with ERP systems enhancing training and competence management workflows in engineering operations has delivered measurable results across various industries. Companies leveraging these integrated solutions have transformed their engineering workflow strategies, achieving streamlined processes and optimised training resource allocation.
Real-World Transformation Through Digital Integration
Weston Aerospace, faced with managing quality and compliance across departments using paper-based systems, implemented Q-Hub's comprehensive platform. The transformation included an Audit Hub for efficient compliance management across multiple standards and Process Hub for digitising NCR management and CAPA processes.
The results were striking—Weston Aerospace reported dramatic improvements in efficiency through real-time dashboards and automated workflows, saving hours each week on repetitive tasks and simplifying processes like calibration and safety inspections.
Similar success was seen at the Scottish Leather Group, which struggled with paper-based systems for ISO compliance. After implementing Q-Hub's solutions, they achieved enhanced compliance management across multiple ISO standards, streamlined communication between departments, and increased operational efficiency through automation of routine tasks.
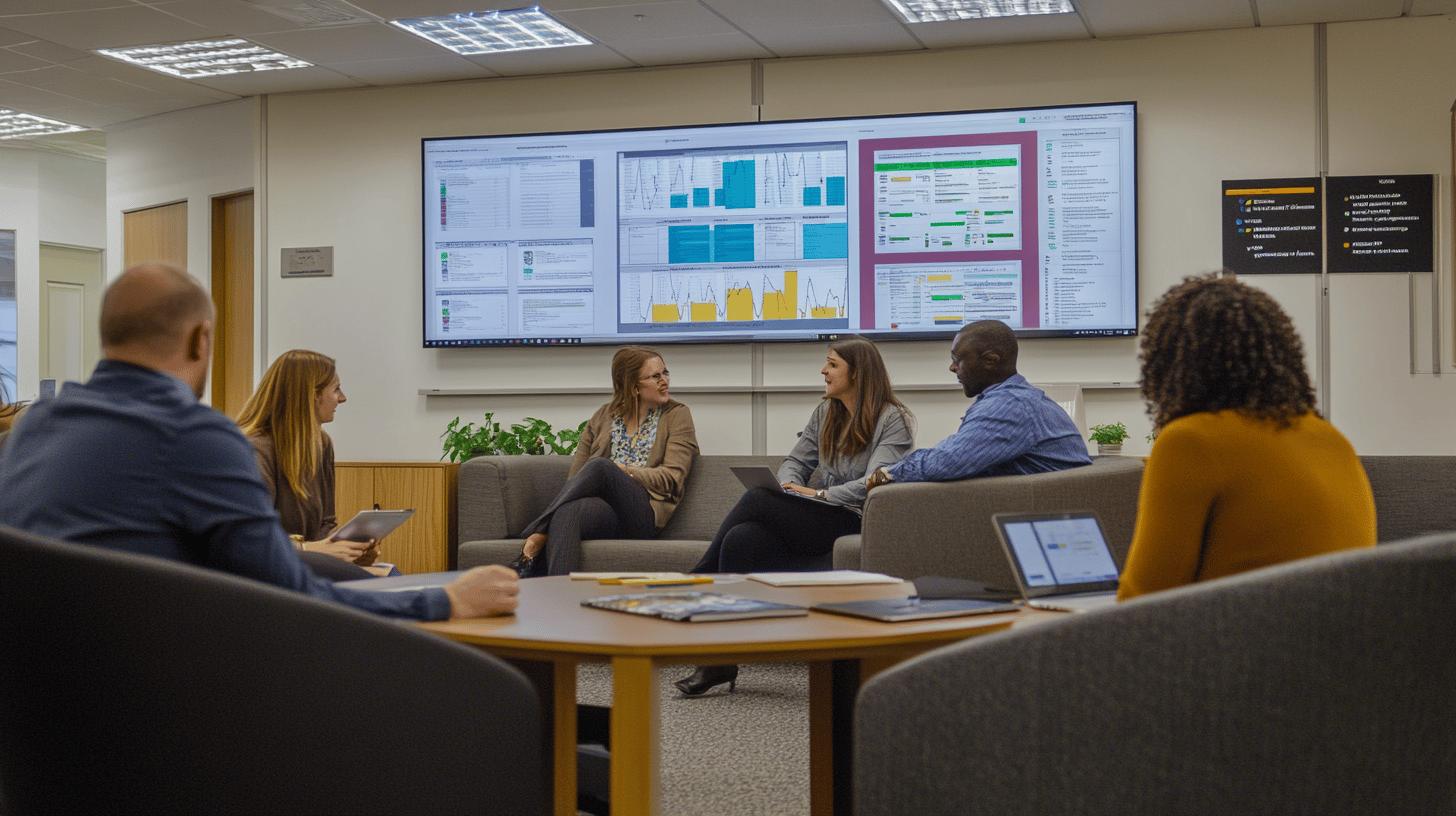
In another case, an automotive manufacturer transitioning to robotics-driven assembly lines implemented a comprehensive ERP solution for competency management. The system mapped training modules directly to skills required for operating new machinery, cutting unnecessary training costs by 23% while ensuring employees were fully prepared before new equipment went operational.
Trends and Future Developments in ERP-Enabled Training for Engineering Operations
Integration with ERP systems enhancing training and competence management workflows in engineering operations continues to drive innovation. As organisations embrace this digital transformation, the emphasis on scalability, efficiency, and precision through advanced ERP-enabled learning platforms grows steadily.
Navigating the Future of Workforce Development
The shift towards cloud-based ERP solutions is particularly significant for engineering operations that face changing project demands. These platforms enable organisations to scale training programs efficiently, ensuring resources align with current project requirements.
An automotive engineering firm using cloud ERP can rapidly deploy new robotics training modules to hundreds of employees without infrastructure overhauls, creating flexibility that reduces downtime and supports technological advancement.
Another key development is AI-driven predictive analytics that analyse employee performance data to forecast future training needs. Imagine an aerospace operation where the system identifies technicians needing safety protocol refreshers months in advance, proactively recommending targeted courses before skills gaps become problematic.
Personalising Learning for Maximum Impact
The focus on adaptive learning methodologies continues to grow, personalising content based on individual progress. For engineering environments where technologies evolve rapidly, this ensures training remains relevant and impactful.
Q-Hub's digital transformation solutions embrace these trends, offering engineering operations the tools to implement adaptive, data-driven methodologies that keep pace with industry demands while ensuring compliance and operational excellence.
As these technologies mature, engineering operations that embrace ERP-enabled training will maintain a significant competitive advantage through more skilled, efficient, and adaptable workforces.
Overcoming Challenges in ERP Integration for Training and Competence Management
<<Integration with ERP systems enhancing training and competence management workflows in engineering operations can be transformative, but the process comes with challenges. From complex system functionalities to resistance to change, successful implementation requires addressing several key barriers.
Building User Confidence Through Strategic Implementation
Resistance to change often presents the first hurdle, particularly in engineering sectors where traditional workflows are deeply entrenched. When employees hesitate to adopt new systems, the entire implementation can falter. The solution lies in targeted training programs that demystify ERP functionalities through role-specific guidance.
Breaking training into manageable phases—beginning with introductory workshops followed by hands-on sessions—significantly improves user adoption and confidence. Companies partnering with Q-Hub find that this approach helps overcome initial resistance and builds enthusiasm for the new capabilities.
Technical complexities present another challenge. ERP systems integrate various organisational functions into a unified platform, which can overwhelm teams without careful implementation planning. A phased rollout allows gradual adaptation rather than overwhelming staff with a complete system overhaul.
Ensuring Data Integrity for Compliance Excellence
Data accuracy is perhaps the most critical concern. ERP systems rely on centralised data, and inaccuracies can cascade through training and reporting workflows. This is particularly crucial in aerospace or automotive engineering, where regulatory compliance is non-negotiable.
Centralised reporting features within Q-Hub's platforms provide essential safeguards, enabling real-time data validation and comprehensive audit trails. When an employee's certification data needs updating, the system automatically flags it, ensuring compliance with standards like ISO 9001 or ISO 45001.
Success ultimately depends on combining targeted training, iterative integration processes, and leveraging appropriate tools for compliance management. With these measures in place, engineering operations can successfully navigate the complexities of ERP integration while enhancing their training and competence management workflows, creating a workforce that's not just compliant but equipped to excel in a rapidly evolving industry.
Ready to transform your engineering operations with integrated training and competence management? Discover how Q-Hub's tailored digital solutions can streamline your workforce development while ensuring compliance and operational excellence.
Start using Q-Hub today
- Manage compliance in one place
- Streamline your teams and tasks
- Use Q-Hub free for 30 days