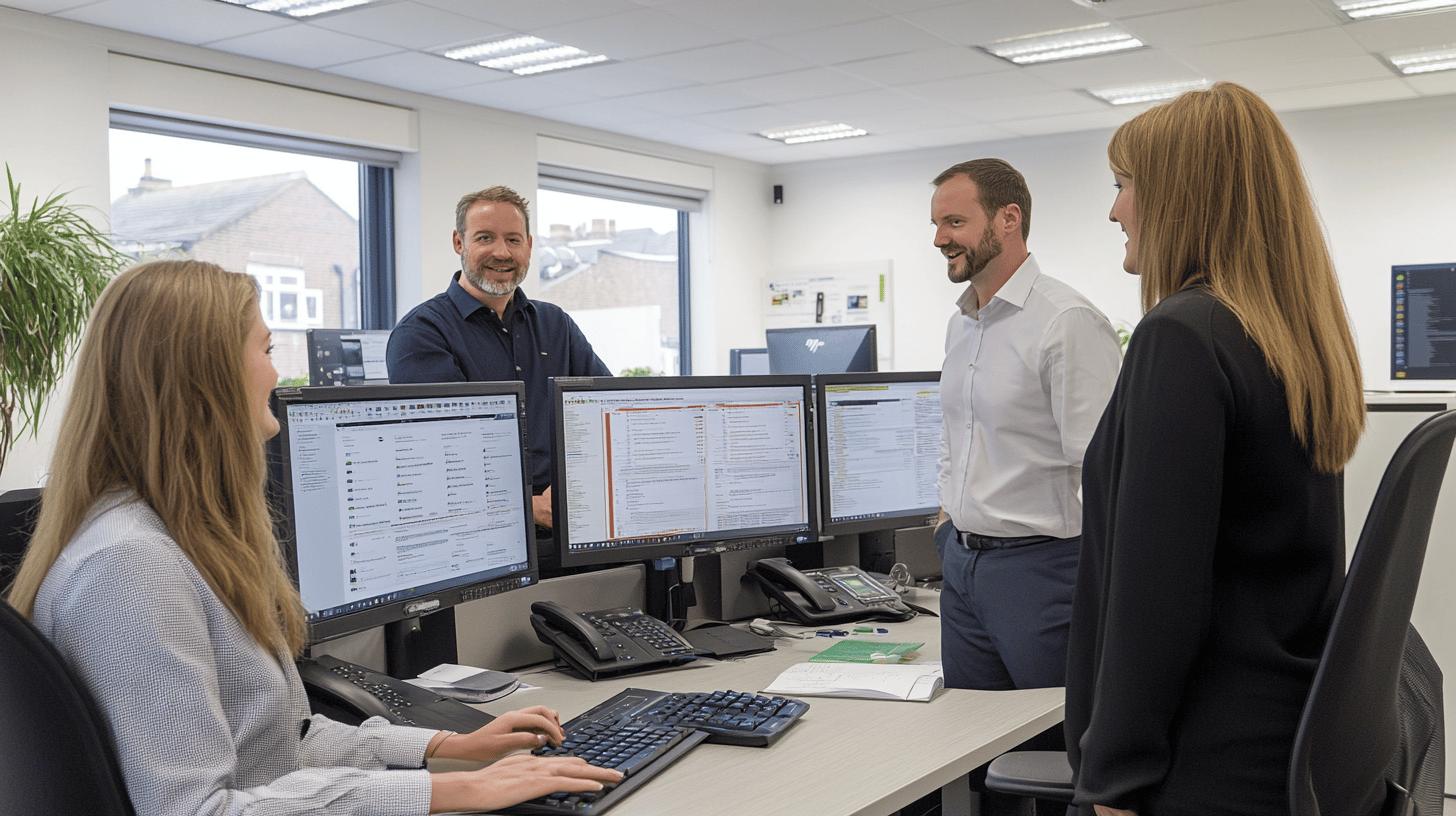
Integration with ERP Systems Boosts Oil and Gas Audits
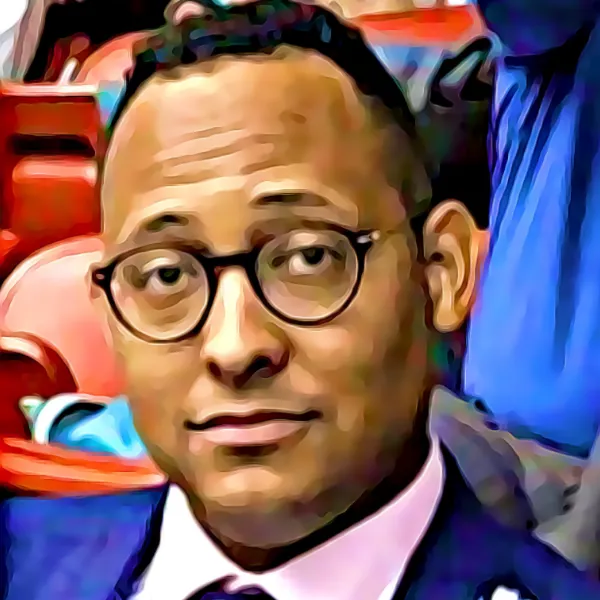
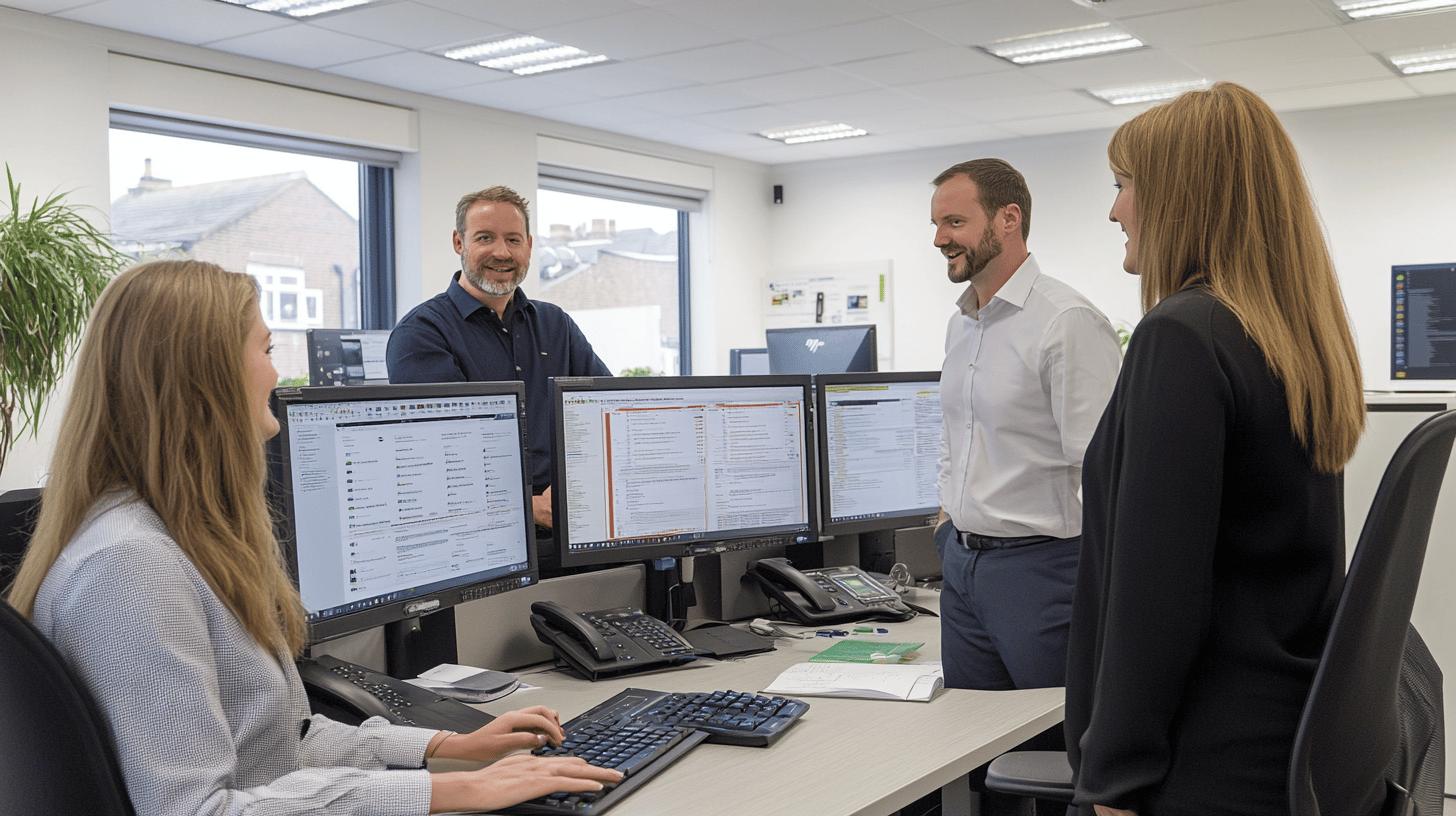
Integration with ERP Systems Boosts Oil and Gas Audits
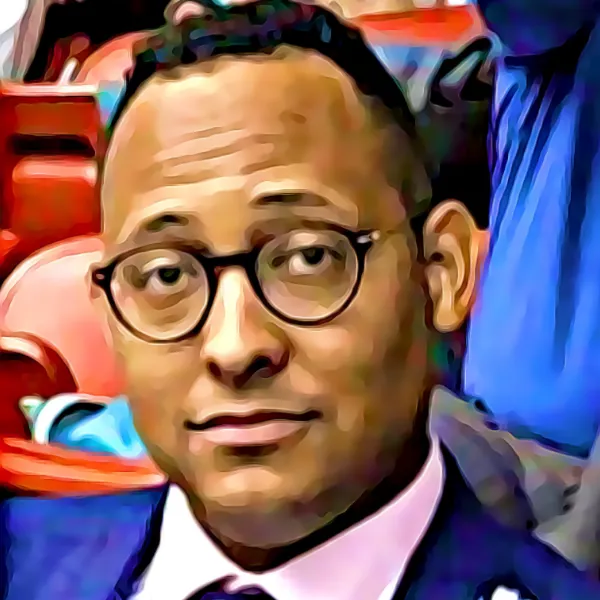
How ERP System Integration Enhances Audit and Inspection Workflows in Oil and Gas Supply Chains
Integrating ERP systems into oil and gas supply chains transforms fragmented audit and inspection processes into streamlined, cohesive operations. This digital unification centralises critical data, making compliance management significantly more efficient while reducing manual errors through automation. Q-Hub's specialised QHSE software solutions address these challenges by creating interconnected ecosystems that replace disjointed spreadsheets with intelligent, responsive systems.
Oil and gas audits must comply with stringent regulations like ISO 45001 for safety and ISO 14001 for environmental standards. Modern ERP systems excel at automating repetitive tasks such as inspection scheduling and maintaining digital audit trails. Instead of manually cross-referencing maintenance logs, these systems instantly consolidate data, saving valuable time and virtually eliminating oversight risks.
Breaking Down Inspection Workflow Bottlenecks
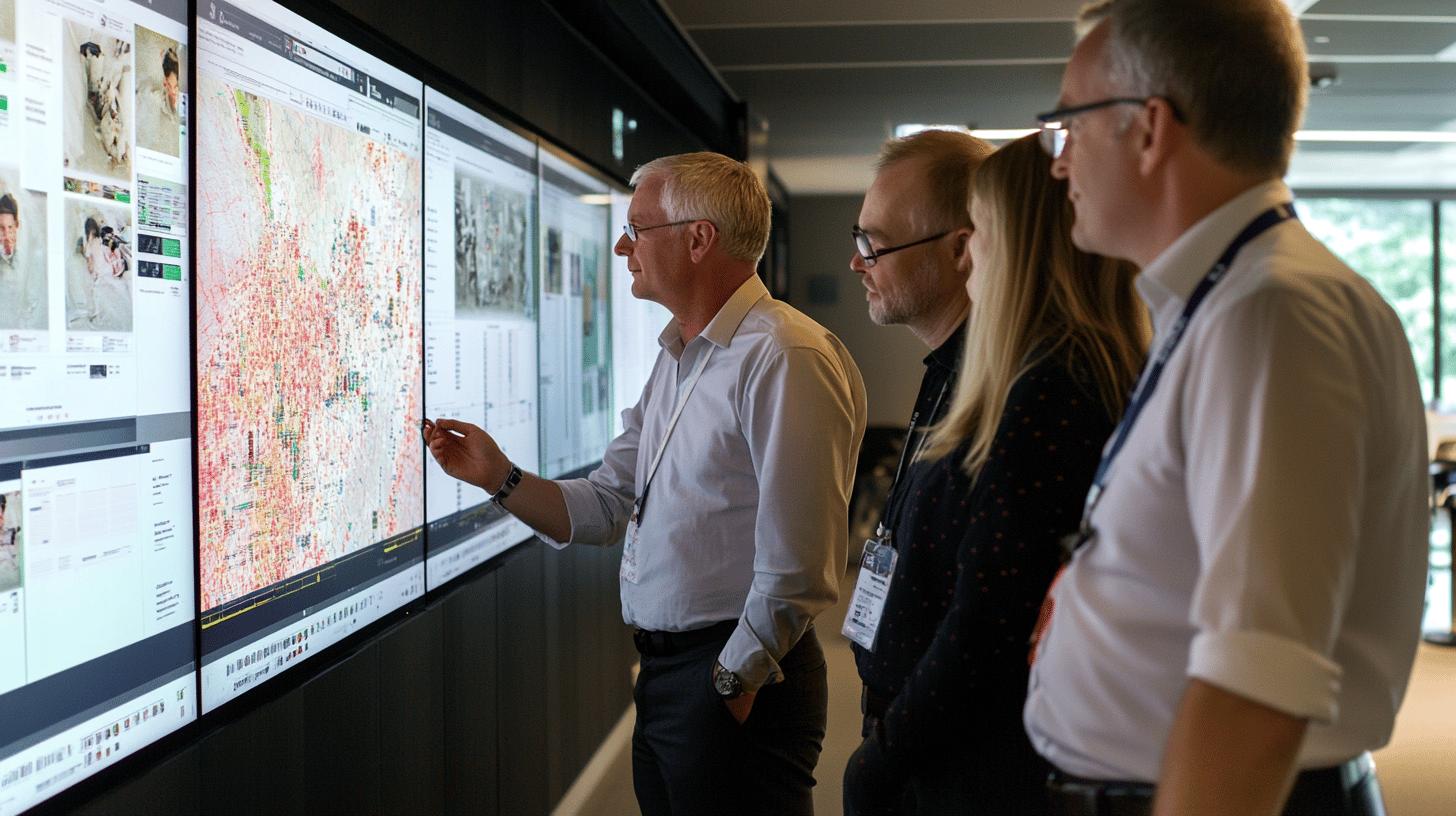
Traditional inspection workflows often suffer from incomplete data and communication gaps between departments. ERP integration eliminates these problems by enabling seamless information flow throughout the organisation. When a pipeline inspection identifies a potential hazard, the system immediately flags the issue and notifies relevant teams, ensuring swift corrective action that prevents costly downtime.
Beyond compliance and efficiency, ERP systems dramatically enhance operational visibility. With procurement, maintenance and production linked in one platform, decision-makers can analyse performance metrics in real-time, supporting proactive management and helping address issues before they escalate.
The digital transformation of our inspection processes reduced our audit preparation time by 40% and helped us achieve a near-perfect compliance rate with safety standards.Source: Operations Director, UK offshore drilling company.
Key Benefits That Transform Operations
The integration of ERP systems with audit and inspection workflows delivers tangible advantages that directly impact the bottom line. Automating audit trails—a critical component in regulatory compliance—eliminates the need to manually compile documents and logs. This provides instant access to historical data, saving significant time whilst reducing oversight risks.
Process standardisation represents another major benefit. In an industry governed by strict regulations, ensuring uniformity across inspections is non-negotiable. ERP systems enforce these standards through predefined checklists, automated alerts, and corrective action protocols. When an inspector identifies a potential safety hazard, the system immediately flags the issue, assigns responsibility, and tracks resolution—all while maintaining a digital log for future audits.
Cost reduction often follows ERP implementation as these systems minimise errors and improve data accuracy. Real-time analysis helps identify inefficiencies in supply chain operations, enabling proactive issue resolution before problems escalate.
Here are the most significant benefits ERP systems bring to audit and inspection workflows:
- Automated audit trails with digital verification
- Real-time data analysis across multiple sites
- Reduced operational costs through process optimisation
- Enhanced supply chain transparency
- Improved compliance with industry standards
- Streamlined inspection workflows with mobile capabilities
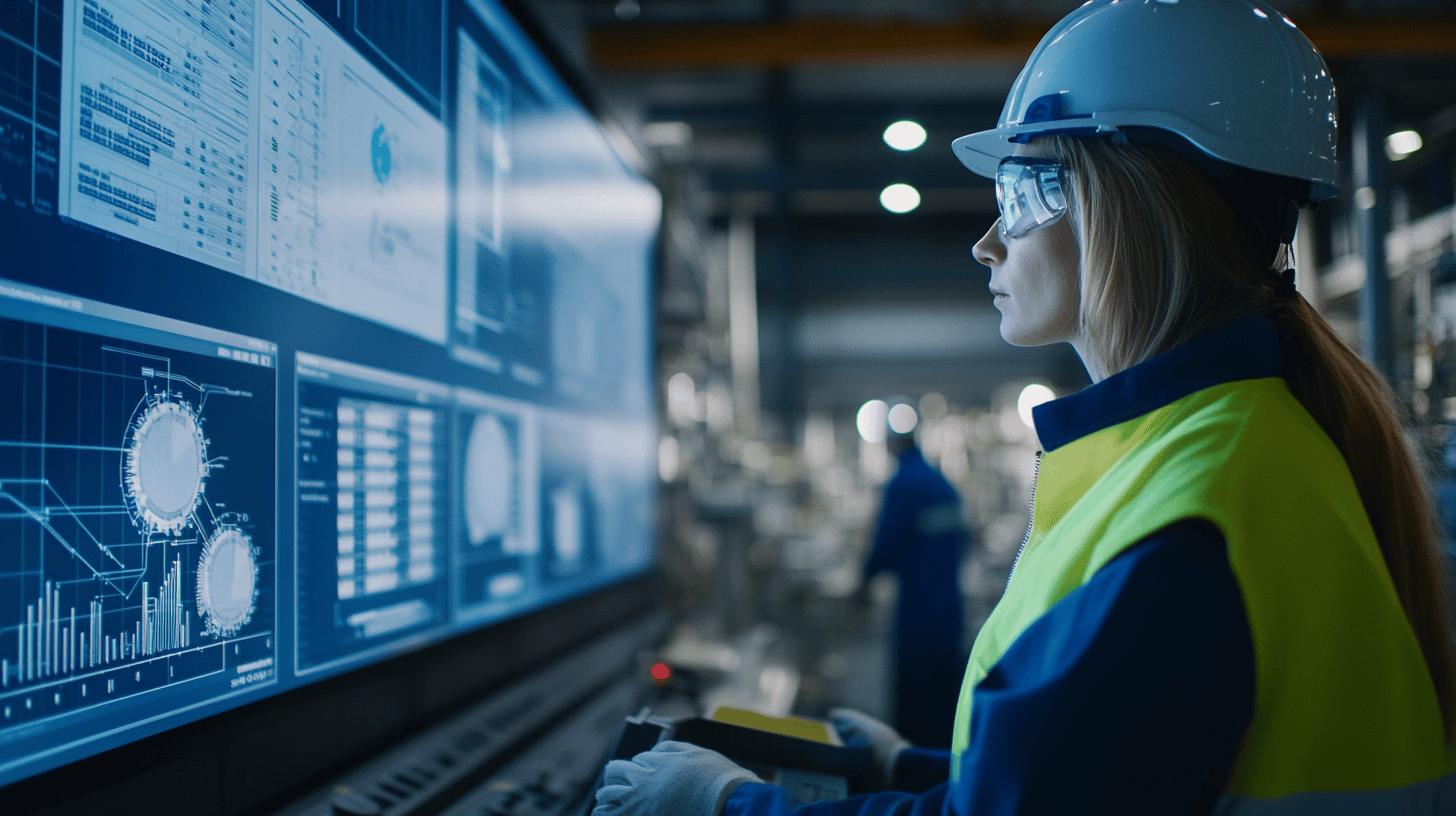
Implementation Best Practices for Success
Implementing ERP systems for audit and inspection workflows requires careful planning. Start with a thorough feasibility study to assess existing processes and identify inefficiencies. Every gap identified at this stage prevents complications during later phases—for example, recognising that inspection data is trapped in spreadsheets highlights the need for a robust migration strategy.
Stakeholder involvement is crucial. IT teams, compliance officers, auditors, and field inspectors all interact with the system differently, making their input invaluable. Early collaboration ensures the ERP system meets operational needs while minimising resistance due to lack of buy-in.
Data integration presents significant challenges, particularly when legacy systems don't integrate easily with modern ERP platforms. The solution lies in choosing solutions that support APIs or middleware to bridge gaps between old and new systems. This approach allows for seamless data flow without duplication errors.
Effective change management is equally important. Implementation is as much about cultural adaptation as technology. Providing comprehensive training and introducing functionalities through phased rollouts minimises disruption while allowing teams to adapt gradually.
<table border="0"> <tr><th>Implementation Phase</th><th>Common Challenges</th><th>Best Practices</th></tr> <tr><td>Planning</td><td>Inadequate process mapping</td><td>Conduct thorough workflow analysis</td></tr> <tr><td>Data Migration</td><td>Information silos and format incompatibility</td><td>Use middleware and staged migration</td></tr> <tr><td>Training</td><td>Resistance to new systems</td><td>Tailor training to different user roles</td></tr> <tr><td>Deployment</td><td>Operational disruption</td><td>Implement phased rollout approach</td></tr> </table>Real-World Success Stories
The impact of ERP integration on audit and inspection workflows is best illustrated through real examples. Scottish Leather Group faced significant challenges managing compliance across multiple sites with paper-based systems. After implementing Q-Hub's digital solution, they streamlined audits across various ISO standards, significantly reducing preparation time and improving interdepartmental communication.
Similarly, Weston Aerospace struggled with legacy systems that created bottlenecks in compliance processes. Their adoption of Q-Hub's Audit Hub and Process Hub transformed NCR management and ISO compliance, freeing staff from administrative tasks to focus on innovation and strategic goals.
Anglia Cathodic Protection Services encountered rapid growth that stretched their manual systems beyond capacity. Q-Hub's platform digitised their fragmented processes, streamlining non-conformance tracking and scheduling audits in real-time. This not only saved hours of administrative work but also improved compliance visibility across operations.
Overcoming Integration Challenges
Despite their benefits, ERP integrations face several obstacles. Data silos represent one of the most significant hurdles, as legacy systems often store information in formats incompatible with modern platforms. Adaptive frameworks using APIs or middleware offer solutions by automating data transfer without duplication errors.
Resistance to change presents another challenge. Employees may feel uneasy about new systems that disrupt familiar workflows. Effective change management strategies include early stakeholder involvement, transparent communication about benefits, and ongoing training. For instance, demonstrations showing how automated audit trails reduce workload can transform scepticism into adoption.
Implementation costs often concern decision-makers. While ERP integration requires investment, phased rollouts help manage expenses while minimising operational disruption. Prioritising high-impact areas like compliance workflows before expanding to other processes allows organisations to realise early benefits that justify further investment.
Future Trends Reshaping Audit and Inspection
The future of ERP systems in oil and gas workflows is increasingly tied to advanced technologies. AI-driven predictive analytics can analyse vast datasets to identify patterns that might otherwise go unnoticed, enabling proactive maintenance by predicting equipment failures before they occur. This prevents costly downtime and improves safety outcomes.
Cloud-based solutions offer unprecedented accessibility and scalability. Teams can access critical data from anywhere, whether monitoring offshore rigs or reviewing audit trails from headquarters. This accessibility improves decision-making speed and quality, particularly valuable in remote operations.
Internet of Things (IoT) integration connects equipment, pipelines, and environmental sensors directly to ERP systems. When a sensor detects an anomaly, the system automatically triggers alerts, assigns tasks, and generates compliance records—creating a continuous feedback loop that revolutionises both operations and auditing approaches.
These technologies are shifting audit philosophy from reactive to proactive, focusing on continuous improvement rather than just corrective measures. This approach aligns perfectly with increasingly stringent regulatory demands while reducing administrative burdens.
Measuring Integration Success
To evaluate ERP integration effectiveness, organisations should track specific Key Performance Indicators. Regulatory compliance rates measure adherence to standards like ISO 45001 and ISO 14001. ERP systems typically improve these metrics by reducing human error through automation.
Inspection error reduction quantifies how effectively the system eliminates inconsistencies from manual processes. Companies migrating from spreadsheet-based pipeline checks often report error reductions exceeding 30% after adopting integrated solutions.
Mean Time to Repair (MTTR) measures how quickly issues identified during inspections are resolved. Real-time data sharing enables faster prioritisation and problem-solving, with some operators reporting 50% MTTR reductions through ERP-integrated workflows.
These KPIs highlight continuous improvement opportunities while demonstrating return on investment. By tracking these metrics, organisations can refine workflows and stay ahead in a demanding industry.
Q-Hub's specialised QHSE software solutions address these challenges through custom digital transformation that seamlessly integrates with existing operations. By unifying audit and inspection processes, Q-Hub helps oil and gas companies achieve operational excellence while maintaining rigorous compliance standards. Ready to transform your audit and inspection workflows? Discover how Q-Hub's tailored solutions can drive operational excellence while ensuring regulatory compliance.
Start using Q-Hub today
- Manage compliance in one place
- Streamline your teams and tasks
- Use Q-Hub free for 30 days