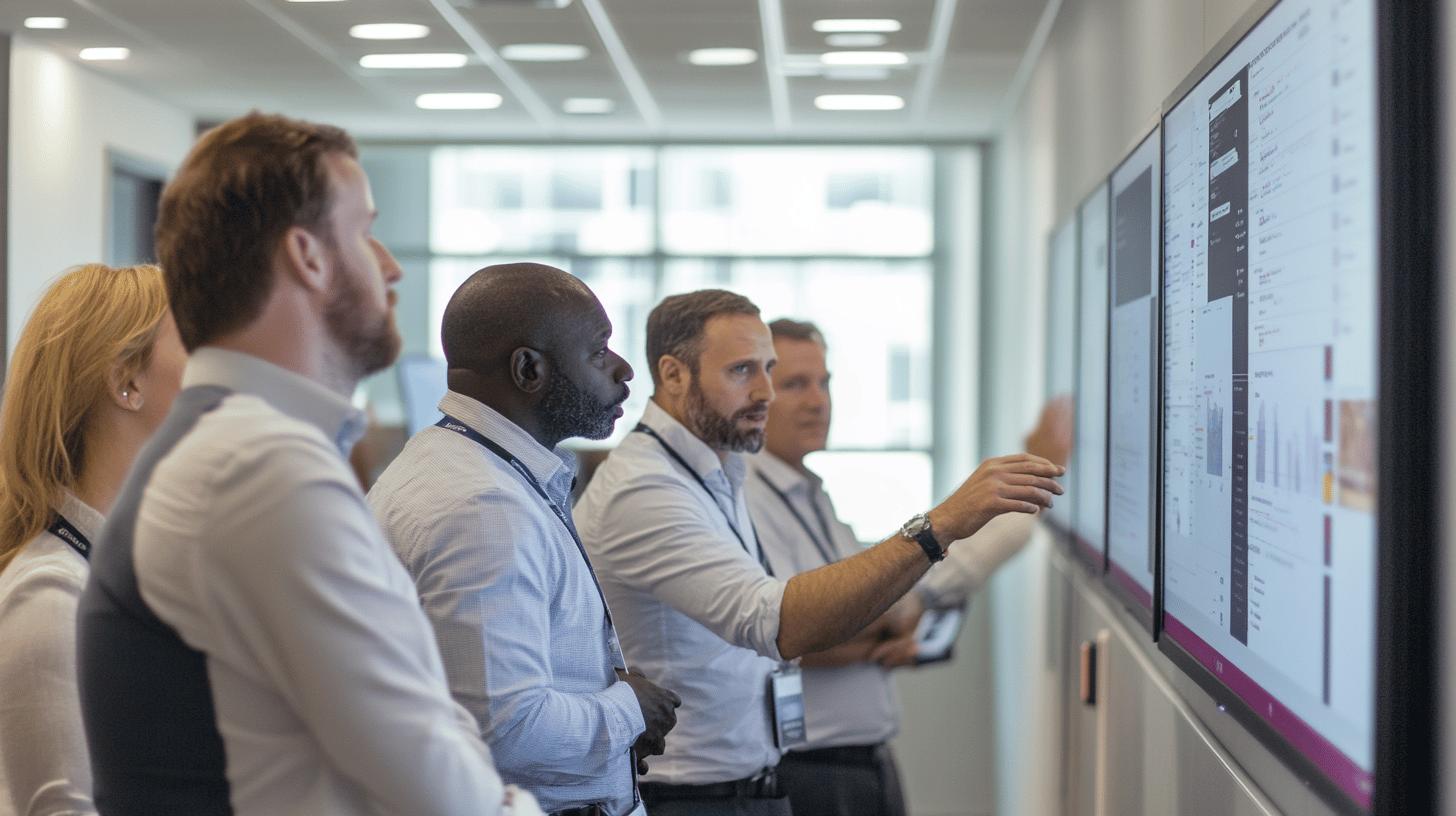
ERP Integration Boosts Training in Food Industry
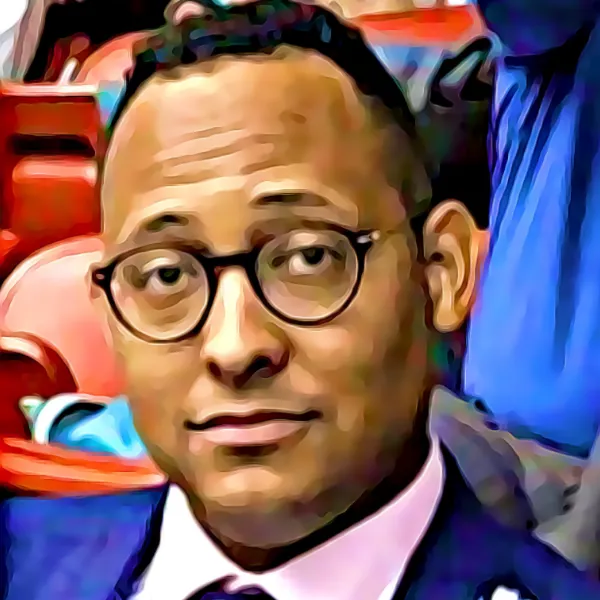
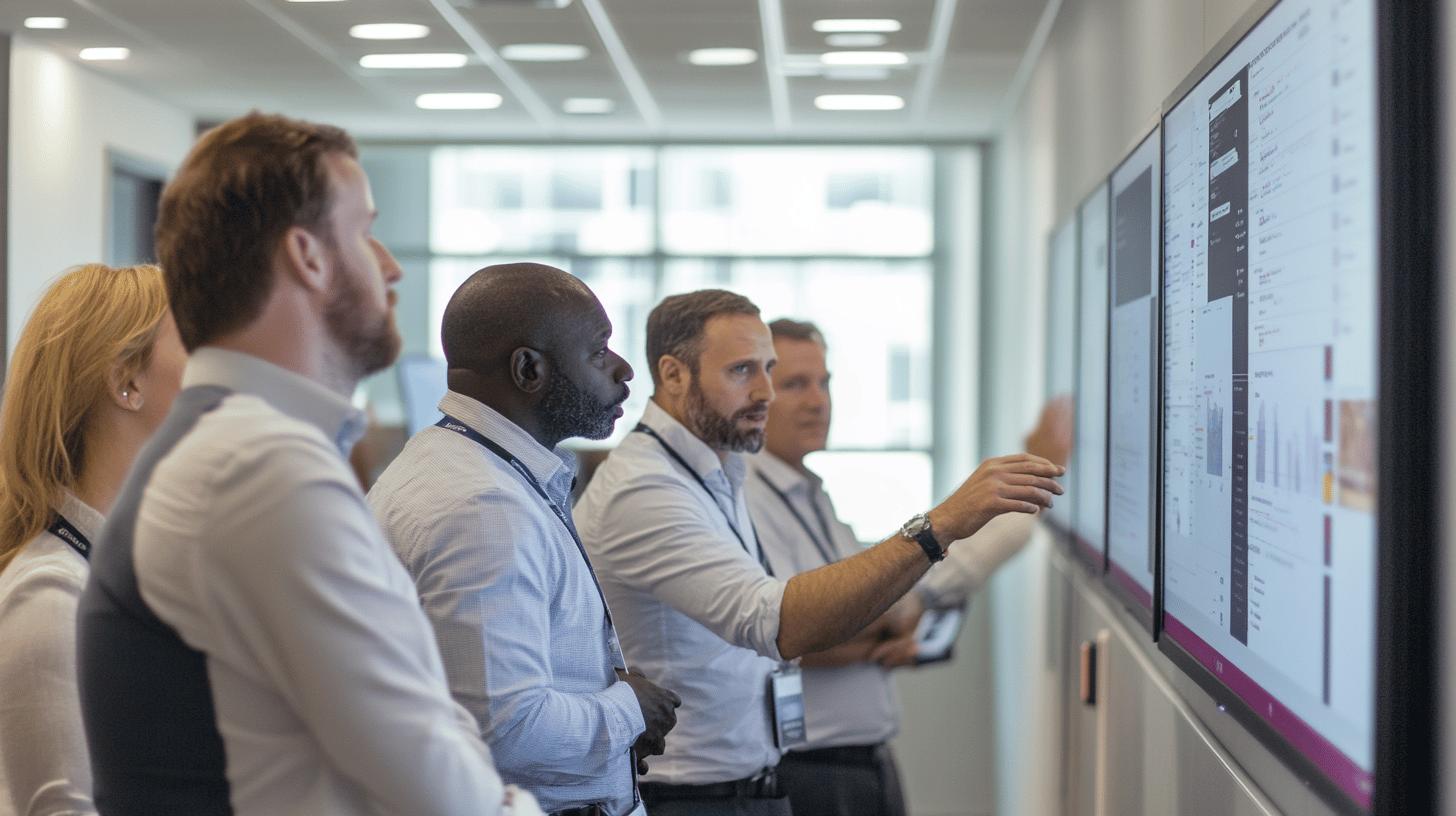
ERP Integration Boosts Training in Food Industry
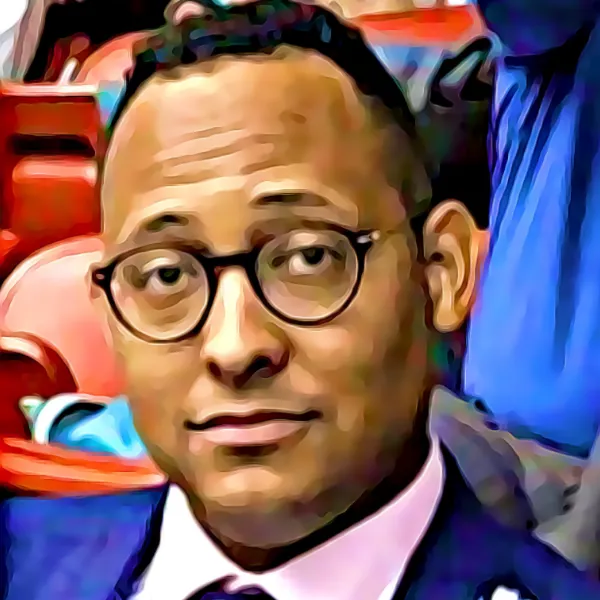
How ERP Integration Improves Training and Competence Management in the Food Industry
ERP integration enhancing training and competence management processes in the food industry is revolutionising workforce development and compliance tracking. Q-Hub's specialised software solutions centralise training data and automate key processes, eliminating the inefficiencies that plague traditional spreadsheet-based methods. For food manufacturers navigating complex regulations like FSMA and HACCP, integrated systems provide the structure needed to maintain consistent standards while developing employee skills.
With proper implementation, these systems transform scattered training records into actionable insights. Managers can instantly identify skill gaps, track certification statuses, and receive automated alerts for upcoming renewals—all from a unified dashboard. This level of visibility ensures that food safety training isn't just a box-ticking exercise but a genuine competency builder.
The implementation of role-specific ERP training modules reduced food safety incidents by 60% across surveyed food manufacturers, while significantly improving audit readiness. Source: 2022 Global Food Safety Training Survey
- Centralised training management reduces administrative burden and paperwork by up to 70%
- Role-based access ensures employees receive only relevant training for their specific functions
- Real-time certification tracking eliminates compliance gaps and regulatory risks
- Automated renewal alerts prevent critical qualification lapses
Transforming Fragmented Systems into Unified Learning Platforms
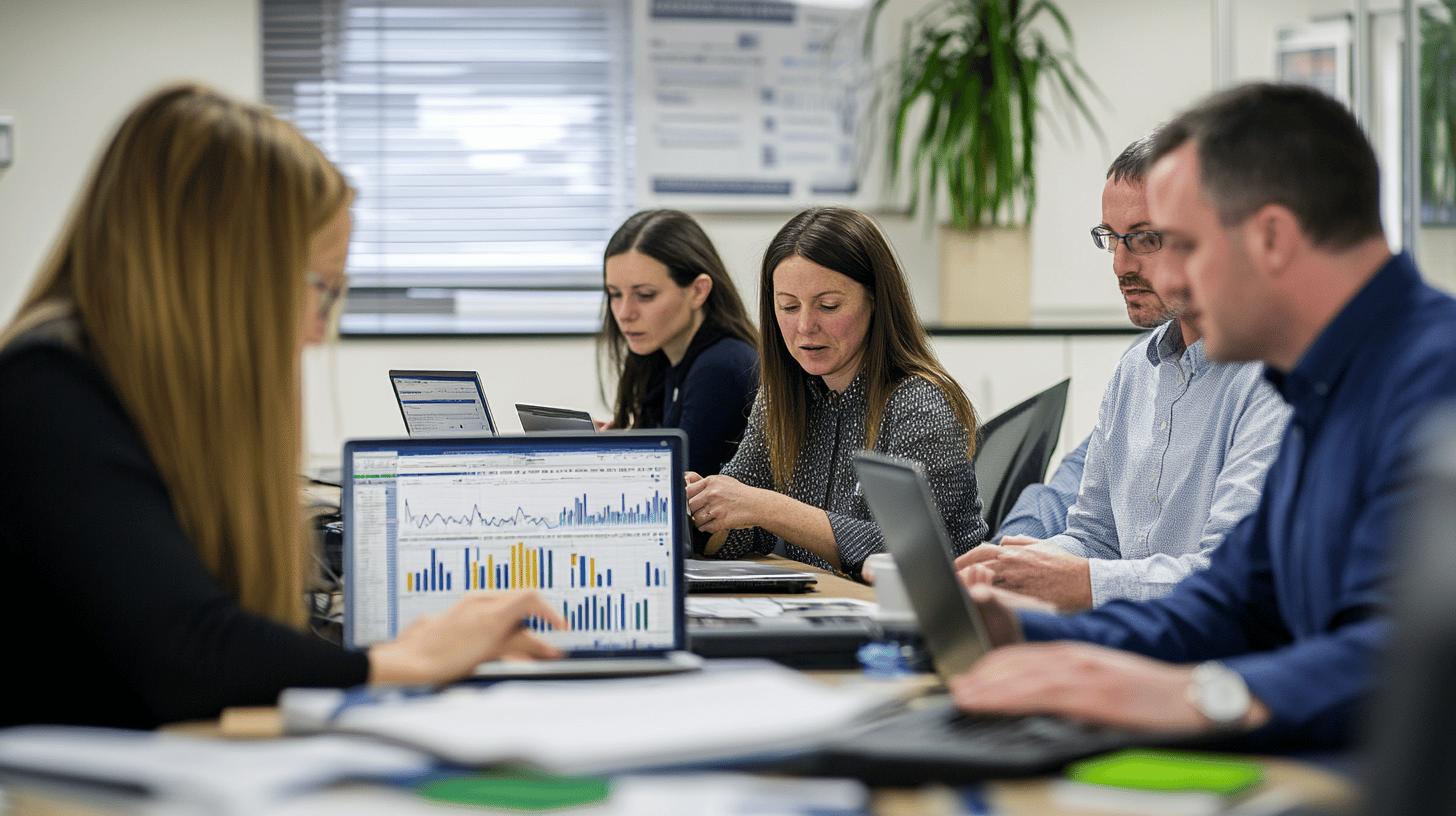
The shift from disconnected training records to integrated ERP solutions marks a significant evolution in food industry workforce development. Traditional approaches—typically relying on spreadsheets, paper records, and manual tracking—create dangerous blind spots in compliance management. With Q-Hub's specialised software, these fragmented pieces transform into a coherent system where training, competence verification, and regulatory requirements seamlessly connect.
This transformation isn't merely technological—it's operational. Food manufacturers using integrated systems report significant reductions in compliance violations and better preparation for unannounced audits. The ability to instantly verify that all employees have completed required allergen management training or that production supervisors maintain up-to-date HACCP qualifications delivers both peace of mind and tangible business benefits.
<table border="0"> <tr><th>Training Management Metric</th><th>Before ERP Integration</th><th>After ERP Integration</th></tr> <tr><td>Certification Tracking Time</td><td>4-8 hours weekly</td><td><1 hour weekly</td></tr> <tr><td>Training Compliance Rate</td><td>75-85%</td><td>95-99%</td></tr> <tr><td>Audit Preparation Time</td><td>3-5 days</td><td><1 day</td></tr> <tr><td>Expired Certification Incidents</td><td>8-12 annually</td><td>0-2 annually</td></tr> </table>Unlocking Personalised Learning Paths and Role-Based Access
One of the most powerful features in modern ERP training modules is role-based access control. This functionality ensures that each employee receives precisely the training content relevant to their specific responsibilities—no more, no less. A production line worker accesses different training modules than a quality assurance manager, creating targeted development paths that enhance role competence without overwhelming staff with irrelevant content.
This personalisation extends beyond content delivery to include verification and assessment. Scottish Leather Group, after implementing Q-Hub's solutions, discovered that role-specific training significantly improved knowledge retention and practical application. Their employees weren't just completing training—they were applying it effectively in daily operations, leading to measurable quality improvements.
The system's ability to track role-specific competencies also simplifies cross-training and succession planning, allowing manufacturers to identify multi-skilled employees who could step into critical roles during absences or staff changes.
Real-Time Dashboards: The Compliance Command Centre
Modern ERP systems transform training oversight with intuitive visual dashboards that highlight progress, gaps, and upcoming requirements at a glance. These command centres give management teams real-time visibility into the organisation's training status without time-consuming report generation.
Food safety managers can instantly identify departments with outstanding training requirements or individuals needing recertification. This capability is particularly valuable during supplier audits or regulatory inspections, when being able to demonstrate complete training compliance can make the difference between passing and failing.
- Colour-coded visualisations highlight areas requiring immediate attention
- Drill-down capabilities allow managers to investigate specific departments or individuals
- Progress tracking shows completion percentages across different training initiatives
- Customisable filters enable focused views based on department, certification type, or expiration date
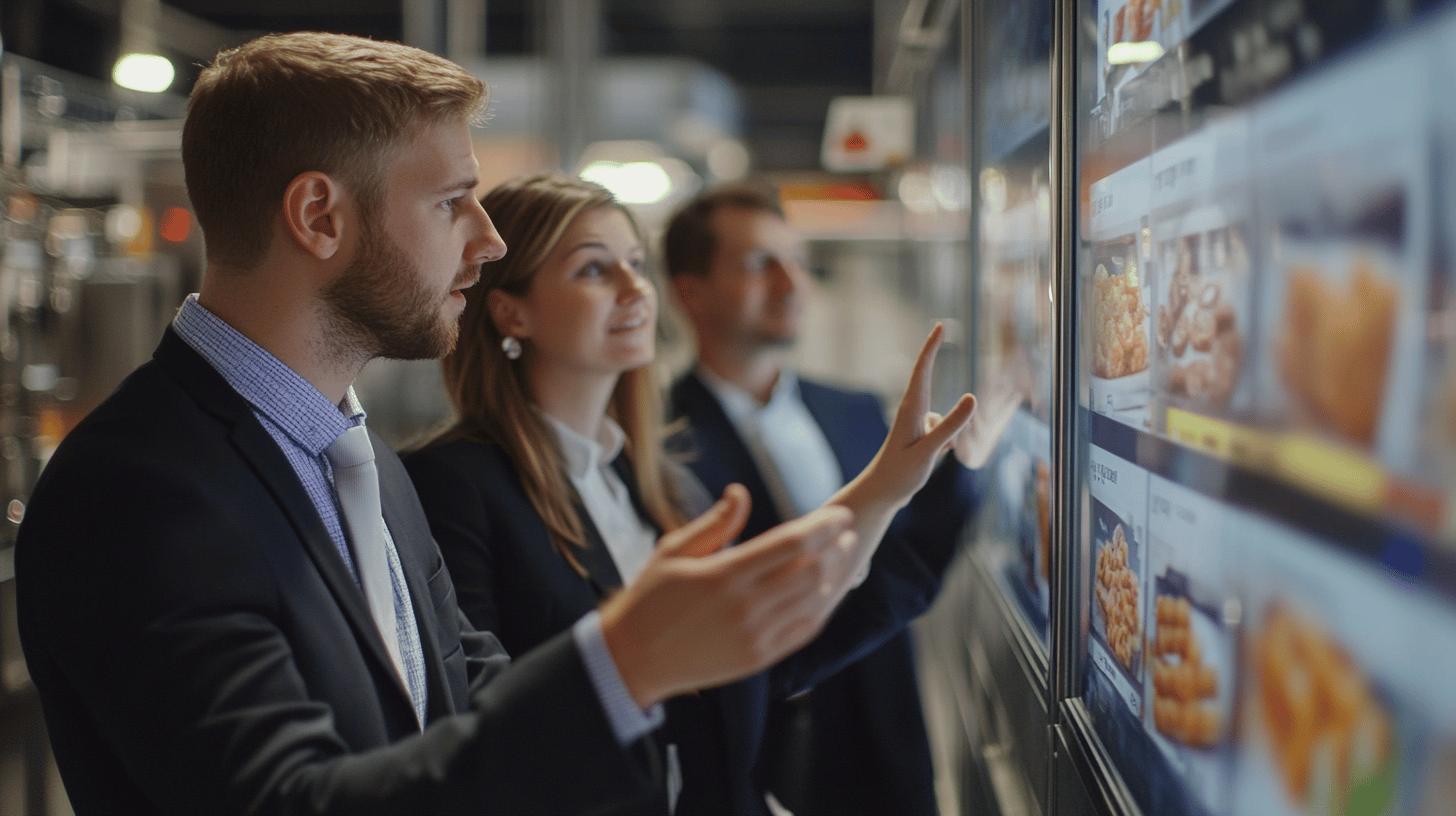
Bridging Theory and Practice Through Integrated Competence Verification
ERP integration enhancing training and competence management does more than track course completion—it bridges the gap between theoretical knowledge and practical application. Q-Hub's systems incorporate competence verification tools that document not just that an employee attended training, but that they can demonstrate the required skills in practice.
This verification component is crucial in food manufacturing, where proper handling procedures directly impact product safety. For example, after implementing an integrated ERP system, Fowlers of Bristol was able to reduce quality deviations by tracking both training completion and on-the-job skill demonstration, creating a more comprehensive approach to competence management.
The ability to link theoretical training with practical verification creates a more robust food safety culture, where employees understand both the "why" and "how" of critical procedures. This comprehensive approach significantly reduces the risk of costly errors and contamination incidents.
Furthermore, the implementation of esg-focused training plays a critical role in aligning workforce skills with industry best practices in food safety and sustainability. It creates a training environment where compliance and responsible practices are intertwined, much like a well-coordinated team that mirrors the precision and care necessary in food manufacturing.
Implementing ERP Training Integration: A Strategic Roadmap
Successfully integrating ERP systems for training management requires careful planning and execution. Food companies typically achieve the best results through a phased implementation approach, starting with core training functionality before expanding to more complex applications.
The critical first step involves mapping current training processes and identifying pain points—exactly where manual systems create bottlenecks or compliance risks. This discovery phase helps prioritise which ERP features will deliver the most immediate value. For many food manufacturers, beginning with certification tracking and compliance reporting provides quick wins that build momentum for broader adoption.
Change management represents perhaps the most challenging aspect of implementation. Employees accustomed to traditional training methods may initially resist new digital systems. Successful companies address this by providing comprehensive system training, clearly communicating benefits, and involving key stakeholders early in the process.
- Conduct a training process audit to identify current inefficiencies and compliance risks
- Define specific objectives for your ERP training management implementation
- Select appropriate ERP modules that align with your identified needs
- Develop a phased rollout plan starting with high-priority functionality
- Create a robust change management strategy to ensure user adoption
Companies like BMC Analysis found that starting with clear, measurable goals helped focus their implementation efforts and demonstrate ROI to senior leadership. Their staged approach to rolling out Q-Hub's solutions allowed teams to adapt gradually while steadily improving compliance performance.
Overcoming Integration Challenges in Food Manufacturing
While the benefits of ERP integration for training management are substantial, food manufacturers often face challenges during implementation. Resistance to change typically tops the list, as employees comfortable with established processes may question the value of new systems. Additionally, concerns about implementation costs and potential disruptions to daily operations can delay adoption decisions.
To overcome these hurdles, successful companies employ several proven strategies. First, they demonstrate clear ROI by calculating the costs of compliance failures, training inefficiencies, and administrative overhead. This financial perspective helps justify the investment to stakeholders. Second, they implement in phases, minimising disruption while allowing teams to adjust gradually to new processes.
Perhaps most importantly, they partner with experienced providers like Q-Hub who understand the unique requirements of food manufacturing environments. This industry-specific expertise ensures that training management systems align perfectly with food safety regulations and operational needs.
Weston Aerospace overcame initial resistance by creating a cross-functional implementation team that included representatives from production, quality, and training departments. This collaborative approach ensured the system addressed real operational needs while building broad organisational support.
The food industry's complex regulatory environment demands sophisticated training management solutions. By implementing Q-Hub's digital transformation tools, manufacturers can transform compliance from a burden into a competitive advantage. Ready to revolutionise your training management approach? Discover how Q-Hub's tailored software solutions can help you build a more skilled, compliant workforce while reducing administrative overhead.
Start using Q-Hub today
- Manage compliance in one place
- Streamline your teams and tasks
- Use Q-Hub free for 30 days