
Enterprise Risk Management Solutions Optimising Food Safety
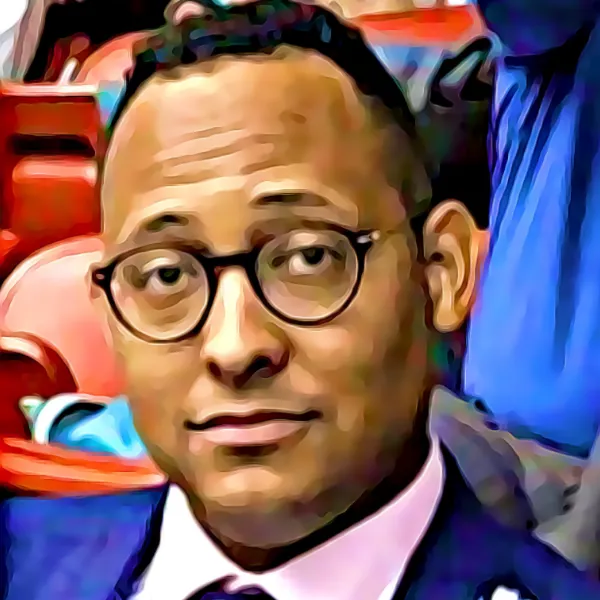

Enterprise Risk Management Solutions Optimising Food Safety
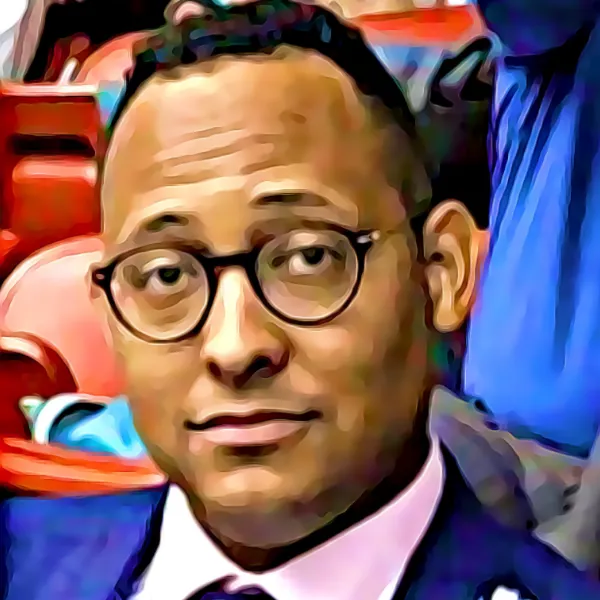
Why Enterprise Risk Management is Crucial for the Food Processing Industry
Enterprise risk management solutions for the food processing industry are essential safeguards in today's complex food production landscape. Q-Hub's specialised risk control frameworks help food manufacturers navigate the myriad of hazards that threaten product safety and business continuity. In an industry where a single contamination incident can trigger widespread illness and devastating brand damage, having robust systems to identify and mitigate risks isn't optional—it's critical for survival.
Food processors face unique challenges that make comprehensive risk management particularly vital. From biological hazards like Salmonella to chemical contaminants and physical fragments, the threat landscape is diverse and ever-changing. Add to this the complexity of global supply chains and stringent regulatory requirements, and it's clear why systematic approaches to risk management have become a cornerstone of successful operations.
The food industry has seen a 36% increase in recall events over the past five years, with the average cost of a significant recall exceeding £7.5 million in direct costs alone.
Let's explore the key challenges that effective ERM solutions address in food processing:
- Prevention of foodborne illness outbreaks through systematic hazard control
- Reduction of contamination risks throughout production stages
- Streamlined compliance with complex food safety regulations
- Effective management of supply chain vulnerabilities
- Optimisation of production processes to maintain quality and efficiency

Beyond Compliance: Creating a Culture of Food Safety Excellence
Modern ERM systems do far more than tick regulatory boxes. They fundamentally transform how food processors approach risk by shifting from reactive to proactive mindsets. Q-Hub's digital transformation expertise enables food businesses to embed risk prevention into their operational DNA, creating comprehensive safety frameworks that protect consumers while strengthening business resilience.
The most effective systems blend intelligent technologies with practical workflows. AI-powered predictive analytics can identify potential contamination points before they become problems, while IoT sensors provide real-time monitoring across production lines. When integrated with robust compliance frameworks, these technologies create a seamless safety ecosystem that adapts to evolving threats.
Key Features of Enterprise Risk Management Solutions for Food Processing
Enterprise risk management platforms designed for food processors must deliver specific capabilities to address the unique challenges of food safety and production. Q-Hub's risk management software combines powerful analysis tools with user-friendly interfaces to create comprehensive protection systems. These solutions help businesses not only prevent hazards but also streamline operations and maintain regulatory compliance.
The value of these features becomes apparent when considering the consequences of inadequate risk management. A single missed hazard could trigger a catastrophic recall, while documentation gaps might lead to significant regulatory penalties. In an industry where consumer trust is paramount, the right systems create both a safety net and a competitive advantage.
Smart Monitoring: The Eyes and Ears of Food Safety
Modern ERM solutions leverage advanced monitoring capabilities to maintain constant vigilance over critical control points. Temperature fluctuations, equipment performance, and production parameters are continuously tracked to identify anomalies before they become serious problems. This real-time visibility enables immediate intervention, significantly reducing the likelihood of contamination events or quality issues.
The impact is particularly valuable for large-scale operations where manual monitoring is impractical. By automating surveillance across multiple production lines and facilities, food processors can maintain consistent standards while freeing quality personnel to focus on higher-value activities.
Feature | Benefit |
---|---|
Predictive Analytics | Anticipates risks before they materialise by analysing patterns and trends |
HACCP Integration | Embeds critical control point monitoring into digital workflows |
Real-Time Alerts | Provides immediate notification when parameters exceed safe limits |
Centralized Documentation | Creates a single source of truth for all compliance records |
Automated Reporting | Generates compliance documentation with minimal manual input |
The Digital Command Centre: Centralising Compliance Control
Fragmented documentation systems represent one of the greatest vulnerabilities in food safety management. Q-Hub's solutions address this by creating a centralised repository for all safety-related documents, procedures, and records. This digital command centre ensures every team member has access to the most current protocols and that audit trails are automatically maintained.
This consolidation dramatically improves audit readiness while reducing administrative burden. When regulatory inspectors request documentation, staff can retrieve it instantly rather than scrambling through disparate paper files or disconnected systems. This capability alone delivers significant return on investment through reduced compliance costs and improved inspection outcomes.
Managing Food Safety Risks with ERM in the Food Processing Sector
Food processors face multiple hazard categories that require comprehensive management approaches. Enterprise risk management systems provide the structure and tools needed to systematically address these challenges. Q-Hub's solutions help manufacturers tackle biological, chemical, physical, and allergen risks through integrated digital workflows that enhance visibility and control.
Invisible Threats: Conquering Biological Hazards
Microbiological contaminants represent some of the most significant threats to food safety. Pathogens like E. coli, Listeria, and Salmonella can enter production through numerous vectors, from raw materials to equipment surfaces. These invisible hazards demand sophisticated detection and prevention systems.
Modern ERM platforms incorporate pathogen testing schedules, environmental monitoring programs, and sanitation verification processes into cohesive digital workflows. By centralising these activities, manufacturers gain comprehensive visibility into their biological control measures and can quickly identify patterns that might indicate emerging problems.
Chemical Control: Ensuring Product Purity
From cleaning agents to pesticide residues, chemical hazards require rigorous management protocols. Effective ERM systems maintain detailed inventories of all chemicals used in production environments and establish strict controls for their application, storage, and disposal.
Digital management tools allow food processors to verify chemical testing programs, monitor concentration levels, and enforce proper handling procedures. When integrated with supplier management systems, these tools also help verify the chemical safety of incoming materials, providing multi-layered protection against contamination.
Physical Protection: Eliminating Foreign Materials
Metal fragments, plastic pieces, glass shards—physical contaminants pose direct threats to consumer safety and brand reputation. Comprehensive risk management solutions coordinate detection technologies (like metal detectors and X-ray systems) with preventive maintenance programs to minimise the likelihood of physical contamination.
Q-Hub's digital workflows ensure that equipment inspection schedules are maintained, detection systems are regularly calibrated, and any incidents are thoroughly investigated. The resulting data creates valuable insights for continuous improvement, helping manufacturers address root causes rather than just symptoms.
Allergen Safeguards: Protecting Sensitive Consumers
With food allergies affecting millions of consumers, allergen control has become a critical aspect of food safety management. Effective ERM systems establish comprehensive protocols for ingredient segregation, production scheduling, equipment cleaning, and labelling verification to prevent cross-contact.
Digital allergen management tools provide visual representations of production schedules, clearly identifying allergen-containing processes and establishing appropriate separation measures. These systems also maintain detailed records of cleaning validation procedures, creating evidence of due diligence that protects both consumers and manufacturers.
Supply Chain Risk Management in Food Processing
Today's food supply chains span continents, creating complex networks with multiple vulnerability points. Enterprise risk management solutions help food processors maintain visibility and control throughout these extended networks. Q-Hub's supply chain monitoring systems provide real-time insights into supplier performance, material quality, and logistics operations, enabling proactive management of potential disruptions.
The complexity of modern food production makes comprehensive supply chain oversight essential for both safety and operational continuity. Without effective monitoring systems, disruptions can cascade through production networks, leading to product shortages, quality issues, or contamination events.
Connecting the Dots: Building End-to-End Visibility
Supply chain transparency begins with comprehensive mapping of all inputs, from raw materials to packaging components. Advanced ERM systems maintain detailed supplier profiles, including quality certifications, audit histories, and risk ratings. This information creates a foundation for proportional oversight, allowing processors to allocate resources according to risk levels.
Digital supplier management tools enable food processors to schedule and track supplier assessments, monitor corrective actions, and maintain current documentation. When integrated with production planning systems, this information helps manufacturers anticipate and mitigate potential disruptions before they impact operations.
The most common supply chain vulnerabilities that food processors must address include:
- Supplier reliability issues that can disrupt production schedules
- Transportation failures that compromise product integrity
- Documentation gaps that create compliance vulnerabilities
- Quality inconsistencies that affect finished products
- Fraud or adulteration risks that threaten brand reputation

When Things Go Wrong: Managing Supply Chain Incidents
Even the most robust prevention systems occasionally fail, making effective incident management capabilities essential. Q-Hub's solutions include comprehensive recall management tools that help food processors quickly identify affected products, notify relevant stakeholders, and coordinate recovery efforts when supply chain issues occur.
Digital incident management platforms maintain detailed traceability records, enabling manufacturers to precisely determine which production lots might be affected by supplier issues. This targeted approach minimises the scope and cost of withdrawals while demonstrating regulatory compliance and protecting consumer safety.
Implementing ERM Solutions in the Food Processing Industry
Successful implementation of enterprise risk management systems requires careful planning and execution. Q-Hub's experience with digital transformation in food processing environments has identified key success factors that help manufacturers maximise their return on investment. From initial assessment through ongoing optimisation, each implementation phase builds upon the previous steps to create comprehensive protection.
Blueprint for Success: The Implementation Roadmap
The implementation journey begins with thorough assessment of current processes, technologies, and risk profiles. This foundation enables development of tailored solutions that address specific operational challenges while aligning with industry best practices and regulatory requirements. By establishing clear objectives from the outset, food processors can ensure their ERM systems deliver meaningful value.
Effective implementation typically follows these key steps:
- Conduct comprehensive risk assessment to identify and prioritise hazards across operations
- Map current processes to understand workflow strengths and vulnerabilities
- Select appropriate technology solutions that address priority risks
- Integrate systems with existing technologies to ensure seamless operation
- Train personnel on new processes and tools to ensure adoption
- Establish metrics to measure performance and guide continuous improvement
Change Management: The Human Element of Implementation
Technology alone rarely delivers optimal results. Successful ERM implementation requires thoughtful change management that addresses the human factors in risk management. Q-Hub's implementation approach emphasises user engagement, clear communication, and practical training to ensure new systems are fully adopted and utilised.
Digital transformation inevitably changes how people work, making stakeholder buy-in essential for success. By involving key personnel in system design and clearly communicating the benefits of new approaches, food processors can overcome resistance and accelerate adoption of improved risk management practices.
Benefits of ERM Solutions for Food Processing Businesses
Implementing comprehensive enterprise risk management solutions delivers multiple benefits for food processors. Beyond improving safety outcomes, these systems enhance operational efficiency, reduce compliance costs, and strengthen market positioning. Q-Hub's clients typically experience significant improvements in key performance indicators after deploying integrated risk management platforms.
Beyond Prevention: The Business Case for ERM
While risk prevention remains the primary goal of ERM systems, the business benefits extend far beyond avoiding problems. Digital transformation of risk management processes creates operational advantages that directly impact profitability and market position. From reduced waste to improved production throughput,
Start using Q-Hub today
- Manage compliance in one place
- Streamline your teams and tasks
- Use Q-Hub free for 30 days