
Web Portal Creation Enhancing Engineering Incident Oversight
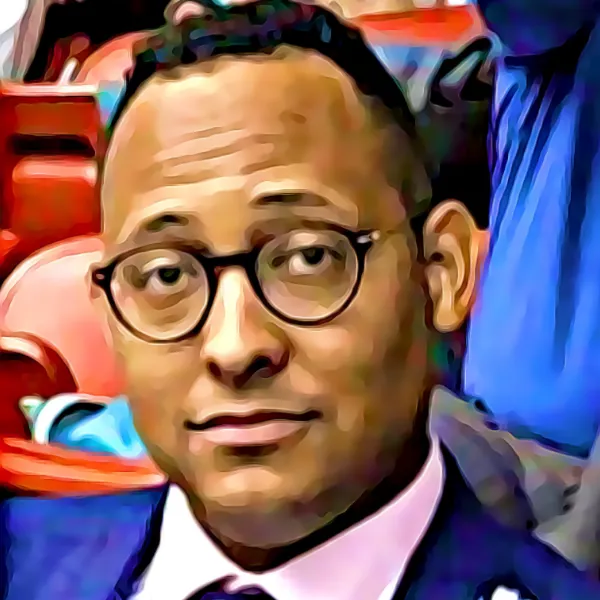

Web Portal Creation Enhancing Engineering Incident Oversight
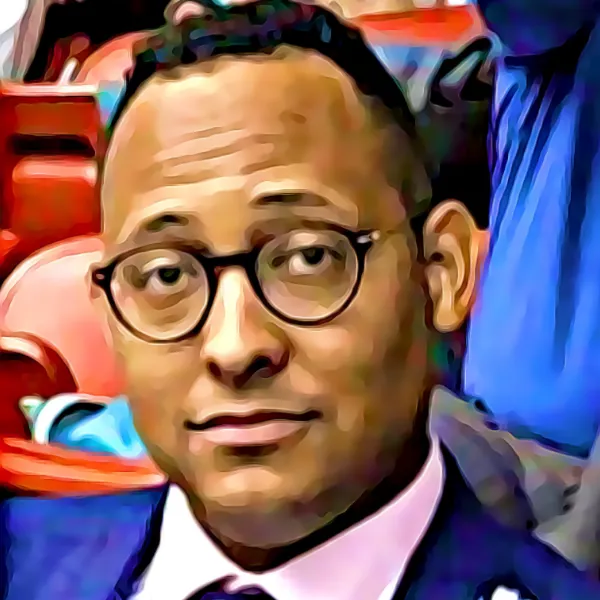
The Importance of Web Portals in Transparent Incident Reporting for Engineering Organisations
Effective web portal creation supporting transparent incident reporting oversight for engineering organisations web portal creation. This vital approach transforms how incident data is captured and managed, ensuring that engineering operations benefit from centralized, real-time insights. By integrating this digital platform, teams can streamline communication, enhance data security, and maintain unparalleled oversight of incident trends, thereby reinforcing a culture of accountability and safety. is no longer optional in today's high-risk industries. With UK engineering organisations reporting over 60,645 non-fatal workplace injuries in 2022-2023 alone, the need for centralised incident management systems has never been more critical. Q-Hub specialises in developing these essential digital reporting platforms that transform fragmented processes into streamlined, compliant workflows.
These web portals consolidate safety reporting tools into a single, accessible platform, making it easier to document, monitor and address incidents in real-time while ensuring compliance with frameworks like RIDDOR 2013 and ISO standards. By offering a unified source of truth, these systems bridge critical transparency gaps in engineering operations.
Implementing a well-designed incident reporting portal can reduce response times by up to 25% while simultaneously improving interdepartmental communication and regulatory compliance.
Here's why engineering organisations are rapidly adopting these solutions:
- Elimination of scattered spreadsheets and paper trails through centralised data management
- Automated documentation and reporting for streamlined regulatory compliance
- Real-time information sharing across teams, preventing miscommunication
- Significant reduction in administrative burdens through optimised workflows
- Decreased human error through automated processes and instant updates
Core Features of Effective Incident Reporting Web Portals
The most impactful web portals for engineering organisations do more than just collect data—they transform how teams respond to critical incidents while maintaining rigorous compliance standards. These digital platforms bridge the gap between raw incident data and actionable insights continuous improvement programmes in engineering. Just as continuous improvement programmes in engineering drive gradual yet impactful change on the shop floor, integrating incident reporting systems can foster an environment of perpetual enhancement. This alignment not only ensures prompt responses to incidents but also promotes ongoing enhancements in operational workflow and safety protocols, much like the iterative progress witnessed in world-class engineering practices., offering monitoring tools that empower swift, effective responses.
The Power of Real-Time Visibility and Alerts

Why does real-time data matter so much in engineering incident reporting? Simply put, delays in communication can escalate minor issues into major safety hazards. A robust portal with instant updates ensures incident details are accessible the moment they're logged, while automated notifications immediately alert relevant stakeholders about new incidents or status changes.
Take a manufacturing scenario where equipment begins to malfunction. Without real-time alerts, this issue might go undetected until it causes significant disruption. With automated notifications, maintenance teams receive immediate alerts, drastically reducing both downtime and safety risks.
This immediacy transforms traditionally reactive processes into proactive solutions while ensuring everyone—from shop floor engineers to compliance officers—accesses identical, up-to-date information.
Building Trust Through Secure Data and Complete Traceability
Engineering organisations handle sensitive, proprietary designs and safety-critical data daily. Robust web portals deploy multiple security layers to protect this information, including encryption that renders sensitive incident data unreadable to unauthorised parties and role-based access controls that limit who can view or modify specific reports.
Equally crucial are comprehensive audit trails that maintain detailed records of every action—from initial incident logging to final resolution. These records create a transparent chain of responsibility while satisfying regulatory requirements like RIDDOR 2013, which demands accurate, complete incident documentation during audits.
The Scottish Leather Group found that implementing Q-Hub's audit capabilities dramatically simplified compliance with multiple ISO standards while creating transparent accountability across their organisation.
<table border="0"> <tr><th>Portal Feature</th><th>Business Impact</th><th>Implementation Priority</th></tr> <tr><td>Real-Time Notifications</td><td>25% faster incident response</td><td>High</td></tr> <tr><td>Integrated Audit Trails</td><td>Simplified regulatory compliance</td><td>High</td></tr> <tr><td>Custom Dashboards</td><td>15% reduction in reporting errors</td><td>Medium</td></tr> <tr><td>Role-Based Access Controls</td><td>Enhanced data security</td><td>High</td></tr> </table>Seamless Integration with Existing Engineering Systems
The true power of incident reporting portals emerges when they connect with existing engineering tools and workflows. For engineering organisations balancing project management systems, ERP software, and compliance platforms, integration eliminates frustrating data silos.
Consider Fowlers of Bristol, who previously struggled with siloed data processes and cumbersome document control. After implementing Q-Hub's solution, they centralised all communications, datasets and workflows into a single digital space, enabling instant access to real-time data across engineering teams, shop floor workers and compliance managers.
Most engineering organisations benefit from integrating their incident portals with:
- ERP systems to centralise operational data
- Project management tools to align incident reporting with timelines and tasks
- Compliance monitoring software to ensure adherence to ISO and other standards
- Data visualisation platforms for generating actionable insights

Transforming Raw Data into Actionable Intelligence
Web portal creation supporting transparent incident reporting oversight for engineering organisations goes beyond simple data collection. The most effective solutions transform complex information into clear, actionable insights through interactive dashboards and visualisation tools.
Unlocking Patterns Through Visual Analytics
Complex incident data becomes immediately meaningful when presented visually. Engineering teams at Weston Aerospace, for example, leveraged Q-Hub's dashboard capabilities to identify recurring quality issues that weren't apparent in traditional reports. These visual tools highlighted patterns that enabled preventative measures rather than reactive fixes.
Effective visualisation tools provide several critical advantages:
- Trend graphs that reveal incident frequency patterns over time
- Heat maps identifying high-risk areas within facilities or processes
- Comparative charts breaking down incident categories for better analysis
- Performance analytics measuring response times and corrective action effectiveness
By making these insights accessible to everyone from floor engineers to senior compliance officers, these tools democratise data and foster organisation-wide accountability.
Case Studies: Measurable Transformation in Action
The impact of implementing robust incident reporting web portals is best illustrated through real-world examples:
Manufacturing Excellence: Rocal Insulating Panels
Rocal Insulating Panels struggled with paper-based safety management systems that made accident reporting and non-conformances tracking inefficient. After implementing Q-Hub's digital portal, they transformed their approach to safety management. Document control was streamlined through a centralised digital library with version tracking, while automated workflows for accident reporting enabled faster resolution and better involvement from department managers. The results included dramatically improved visibility across departments and enhanced accountability at all organisational levels.
Aerospace Precision: Weston Aerospace
Weston Aerospace faced growing inefficiencies due to outdated systems that failed to deliver actionable data. Their legacy approach to NCR tracking and ISO standard adherence was resource-intensive and often delayed. After implementing Q-Hub's platform, they achieved streamlined compliance management and dramatically improved inter-departmental communication. The Audit Hub became central to their compliance strategy, offering automated scheduling, reporting, and real-time dashboards. This transformation freed teams to focus on innovation rather than administrative tasks.
Cultivating a Culture of Transparency and Accountability
Perhaps the most valuable outcome of implementing effective incident reporting portals is the cultural shift they facilitate. When BMC Analysis implemented Q-Hub's solution, they discovered that beyond efficiency gains, the system fostered open communication that encouraged employees to report incidents without hesitation or fear of retaliation.
This approach directly aligns with core engineering ethics principles, where safety prioritisation is non-negotiable. Employees who trust that their concerns will be addressed fairly are more likely to participate in proactive safety measures, ultimately reducing organisational risk.
A strong reporting culture isn't just about compliance—it's about engagement. When incidents are openly addressed and employees are involved in the reporting process, it creates shared responsibility and ownership of safety protocols. This engagement strengthens organisational trust and transforms incident reporting from a reactive task into a cornerstone of continuous improvement.
For engineering organisations seeking to transform their approach to incident management, Q-Hub offers tailored digital solutions that not only streamline compliance but cultivate transparent, accountability-driven cultures. By providing the tools to centralise, secure, and visualise critical incident data, Q-Hub empowers engineering teams to move beyond mere reporting toward true operational excellence and safety leadership.
Start using Q-Hub today
- Manage compliance in one place
- Streamline your teams and tasks
- Use Q-Hub free for 30 days