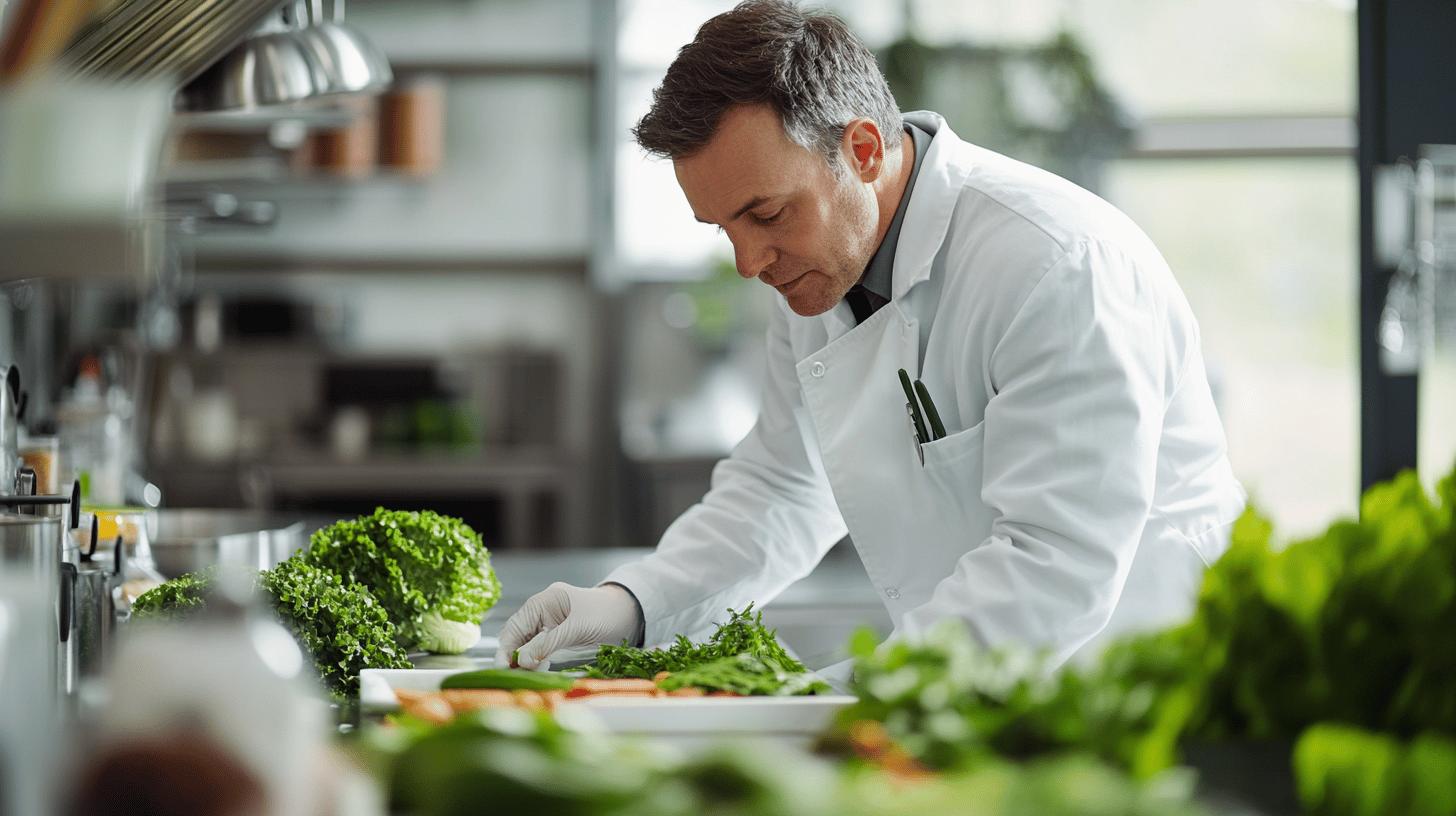
Web Portal Creation Boosts Safety in Food Production
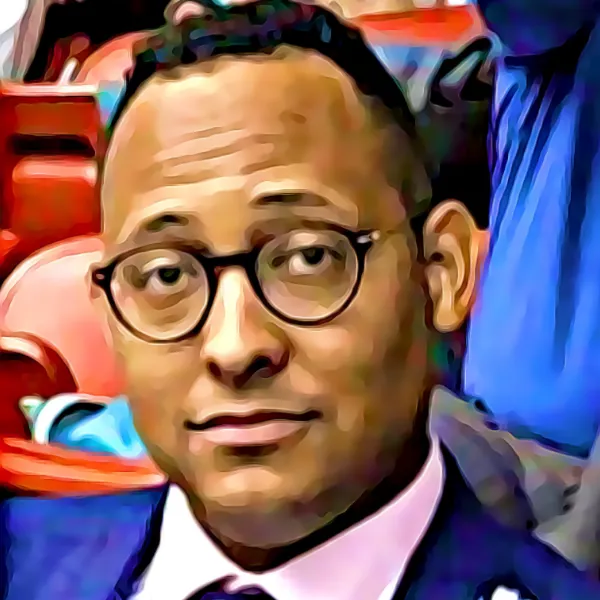
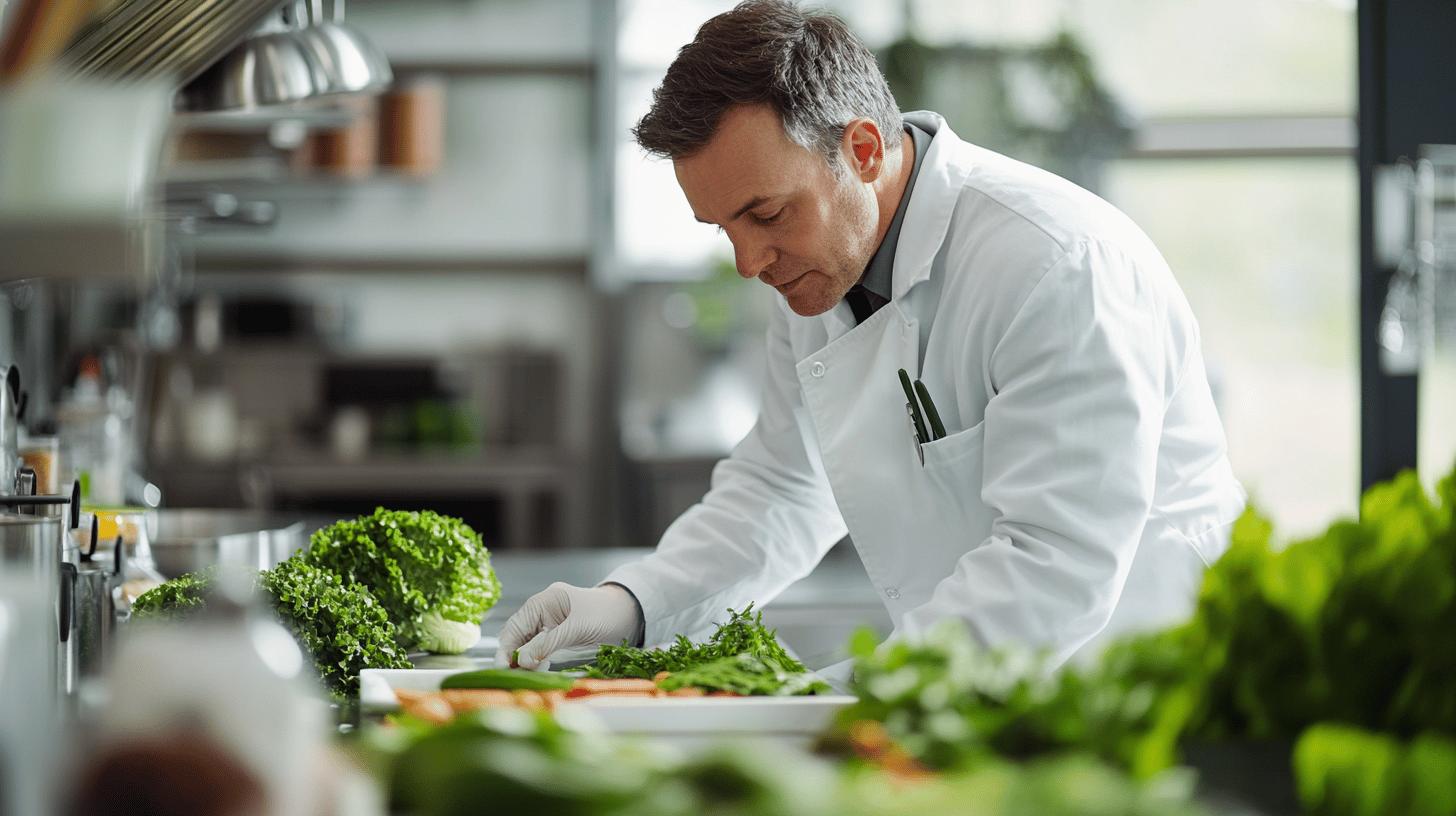
Web Portal Creation Boosts Safety in Food Production
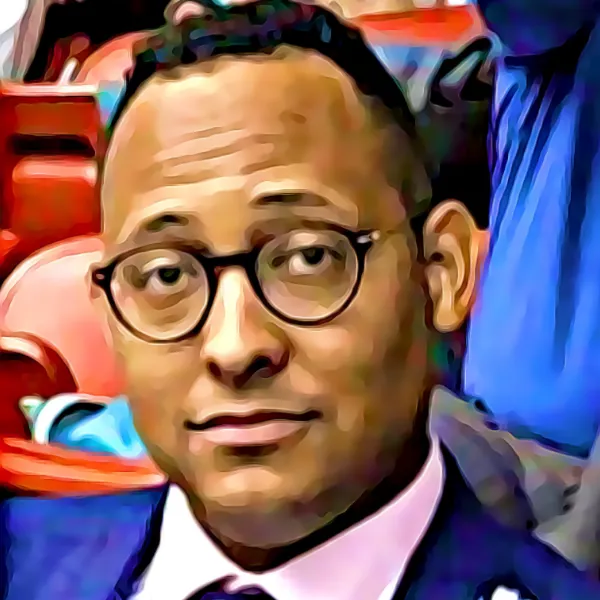
How Web Portal Creation Enhances Safety Management in Food Production
Web portal creation is revolutionising safety management in food production by centralising critical data and streamlining compliance processes. These digital platforms allow manufacturers to gather, organise, and access safety information in one unified environment, eliminating fragmented spreadsheets and error-prone manual processes. Q-Hub's tailored software solutions for the food industry bring transparency and organisational clarity, ensuring consistent safety protocols across all production sites. By embracing this digital transformation, food manufacturers can better address regulatory demands, improve interdepartmental communication, and significantly reduce safety risks.
Transforming Food Safety Through Digital Innovation
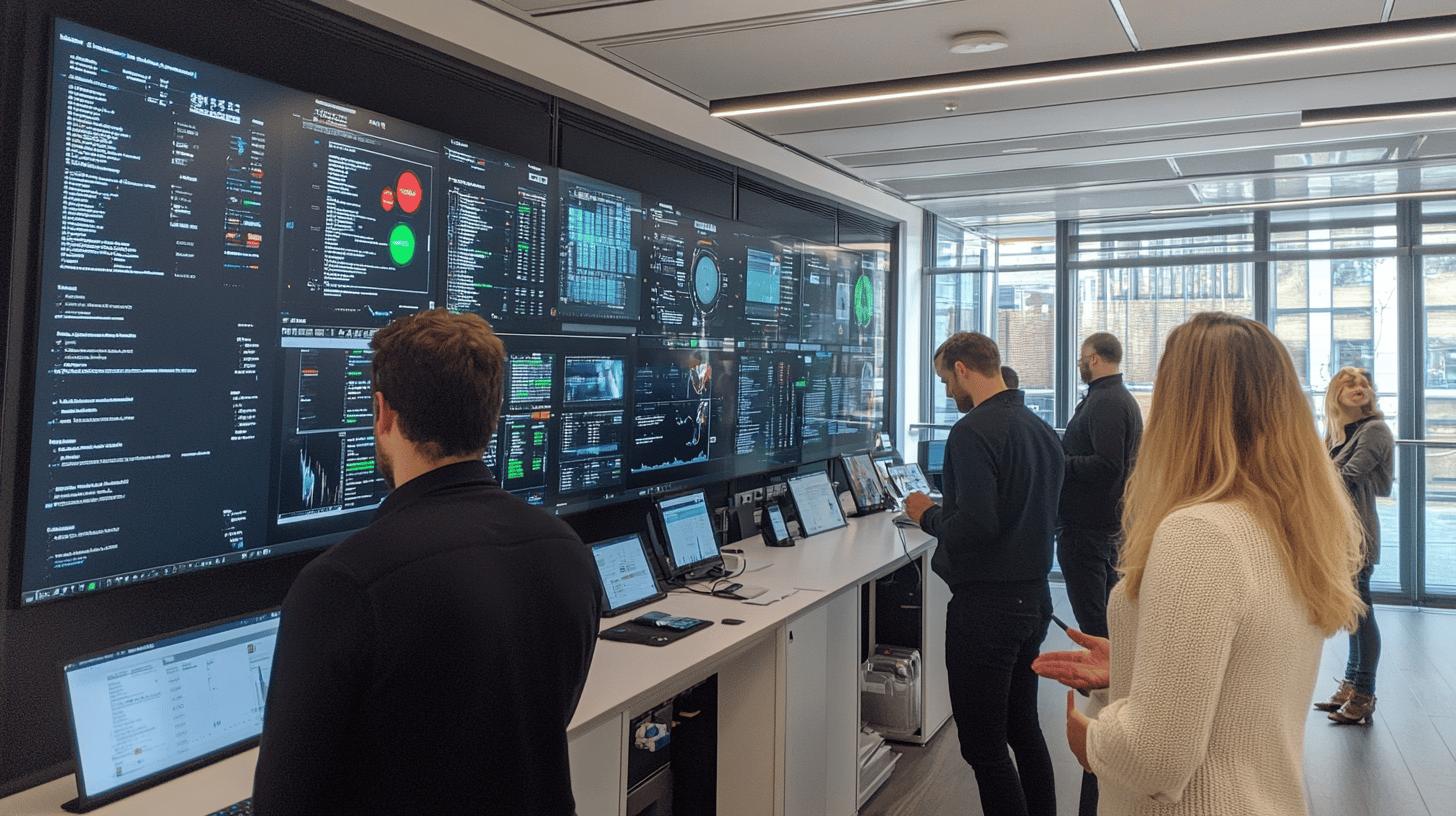
The standout benefit of these platforms is their ability to leverage automated reporting and real-time monitoring to identify and address safety hazards. Real-time alerts notify teams immediately when potential safety breaches occur, enabling swift response before issues escalate. Meanwhile, automated reporting ensures incidents are documented accurately and consistently, reducing human error while providing comprehensive visibility of safety performance.
A leading food manufacturer implemented Q-Hub's web portal and reported a 25% increase in safety audit efficiency within just one year. The platform's real-time dashboards delivered actionable insights, while compliance tracking tools ensured adherence to food safety standards like HACCP and ISO 22000.
Digital transformation in food safety isn't just about technology—it's about creating a culture where safety becomes integrated into every aspect of production.
Measurable Benefits That Drive Safety Excellence
Centralising safety data through web portals eliminates the need for scattered spreadsheets or siloed systems. This consolidation dramatically improves traceability and ensures consistency across production sites. Imagine tracking everything from inspection logs to incident reports in one accessible location—this simplified oversight provides a clear audit trail that meets even the strictest regulatory requirements.
The automation capabilities of these platforms reduce time spent on manual processes by up to 30%. By flagging non-compliance risks in real time, these systems ensure adherence to critical standards while enabling efficient online audits without the logistical challenges of paper trails.
Companies implementing Q-Hub's solutions have reported a 20% reduction in safety-related incidents within their first year. This improvement stems from enhanced communication, better data accuracy, and proactive hazard management through real-time dashboards and automated alerts.
- Reduced errors through automated safety processes
- Enhanced traceability across multiple production sites
- Streamlined interdepartmental communication
- Improved regulatory compliance tracking
- Significant reduction in safety-related incidents
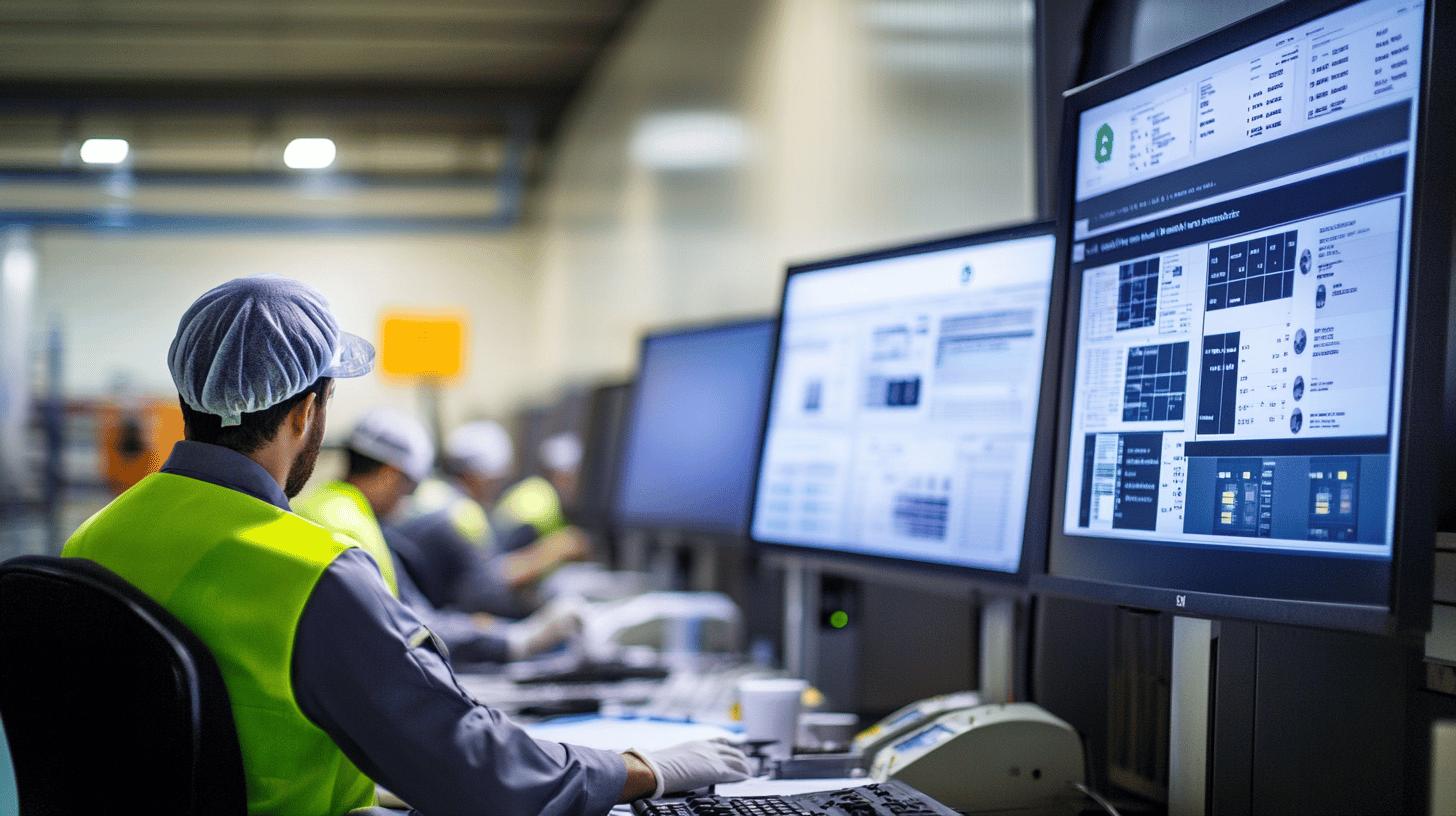
Essential Features That Power Effective Safety Management
A well-designed safety management portal offers customisable dashboards that provide real-time visibility into critical performance metrics. This enables teams to pinpoint issues quickly and make data-driven decisions. Unlike paper-based methods, these centralised systems ensure every safety breach is addressed promptly through automated workflows and instant notifications.
Integration with IoT devices represents another breakthrough feature. Sensors monitor equipment and environmental conditions, offering predictive maintenance capabilities that prevent failures before they occur. Equally important is user-friendly design that ensures accessibility for everyone from managers to front-line workers, fostering a collaborative safety culture throughout the organisation.
<table border="0"> <tr><th>Feature</th><th>Function</th><th>Impact</th></tr> <tr><td>Custom Dashboards</td><td>Visualise safety metrics</td><td>Enhanced decision-making</td></tr> <tr><td>Real-Time Alerts</td><td>Immediate hazard notification</td><td>40% faster response times</td></tr> <tr><td>Automated Reporting</td><td>Streamline documentation</td><td>Reduced administrative burden</td></tr> <tr><td>IoT Integration</td><td>Sensor-based monitoring</td><td>Predictive hazard prevention</td></tr> </table>Seamless Integration: The Key to Implementation Success
Successful web portal implementation hinges on effective integration with existing systems. Q-Hub specialises in ensuring smooth data flow between legacy software and new digital platforms, preventing information silos that hinder operational efficiency. By connecting traditional systems with advanced digital tools, food producers can maintain consistency across all departments while enhancing compliance tracking.
Integration challenges like data migration and software compatibility require careful planning. Q-Hub's approach includes phased rollouts, thorough compatibility testing, and comprehensive training to ensure adoption across all levels. Scottish Leather Group successfully implemented Q-Hub's platform across multiple sites, significantly improving their compliance management while streamlining communication between departments.
Proactive Safety Management Through Real-Time Monitoring
Real-time monitoring systems are transforming how food producers identify and address safety breaches. These systems reduce response times by up to 40% by replacing manual processes with instant detection and notification. When safety issues arise, automated alerts ensure swift action, limiting potential escalation while reinforcing accountability across teams.
Robust incident reporting software standardises documentation processes, ensuring every incident is logged consistently. This enables teams to identify patterns and address systemic issues rather than just symptoms. Fowlers of Bristol experienced this transformation first-hand after implementing Q-Hub's solution, centralising their critical workflows and communications into a single digital space.
How predictive analytics prevents safety incidents
Predictive analytics analyses historical data and current conditions to identify potential hazards before they occur. Sensors integrated with monitoring systems detect equipment anomalies, flagging them as risks before failures happen. This proactive approach not only prevents incidents but enhances overall operational efficiency, moving the industry toward a data-driven safety culture.
Real Results: A Multinational Success Story
One multinational food manufacturer struggled with disparate safety processes across multiple sites. Manual tracking and inconsistent audit preparation led to frequent delays and compliance risks, while the absence of real-time monitoring meant hazards were often identified too late.
After implementing Q-Hub's web portal solution, the transformation was remarkable. Safety audit times decreased by 35%, while compliance tracking features ensured 100% adherence to food safety standards. Real-time dashboards provided actionable insights that contributed to a 15% improvement in safety performance metrics.
Similar results were achieved by BMC Analysis, who struggled with tracking non-conformances and managing document acknowledgement. Q-Hub's Process Hub revolutionised their workflow with automated tracking and reporting, while digital document control eliminated inefficiencies in their compliance processes.
Ready to transform your food safety management with Q-Hub's innovative digital solutions? Discover how our tailored web portals can streamline your compliance processes, reduce safety incidents, and drive operational excellence throughout your food production operations.
Start using Q-Hub today
- Manage compliance in one place
- Streamline your teams and tasks
- Use Q-Hub free for 30 days