Still juggling piles of safety paperwork while managing multiple job sites? You're not alone – UK Safety Officers are facing unprecedented compliance challenges in an increasingly complex regulatory landscape.
The daily grind of clipboard checks, paper forms, and scattered documentation isn't just frustrating – it's a serious liability. When critical safety records get lost in filing cabinets or email chains, the consequences can be devastating: compliance failures, preventable incidents, and even legal penalties. But there's good news on the horizon. The construction industry is embracing a digital revolution that promises to transform how safety officers manage quality and compliance.
Modern QMS Software is changing the game for UK construction safety professionals – replacing manual chaos with streamlined digital workflows that enhance visibility, strengthen compliance, and ultimately save lives.
Discover how Q-Hub’s QMS software is purpose-built to support construction safety officers in managing quality, health, safety, and environmental compliance from a single digital platform.
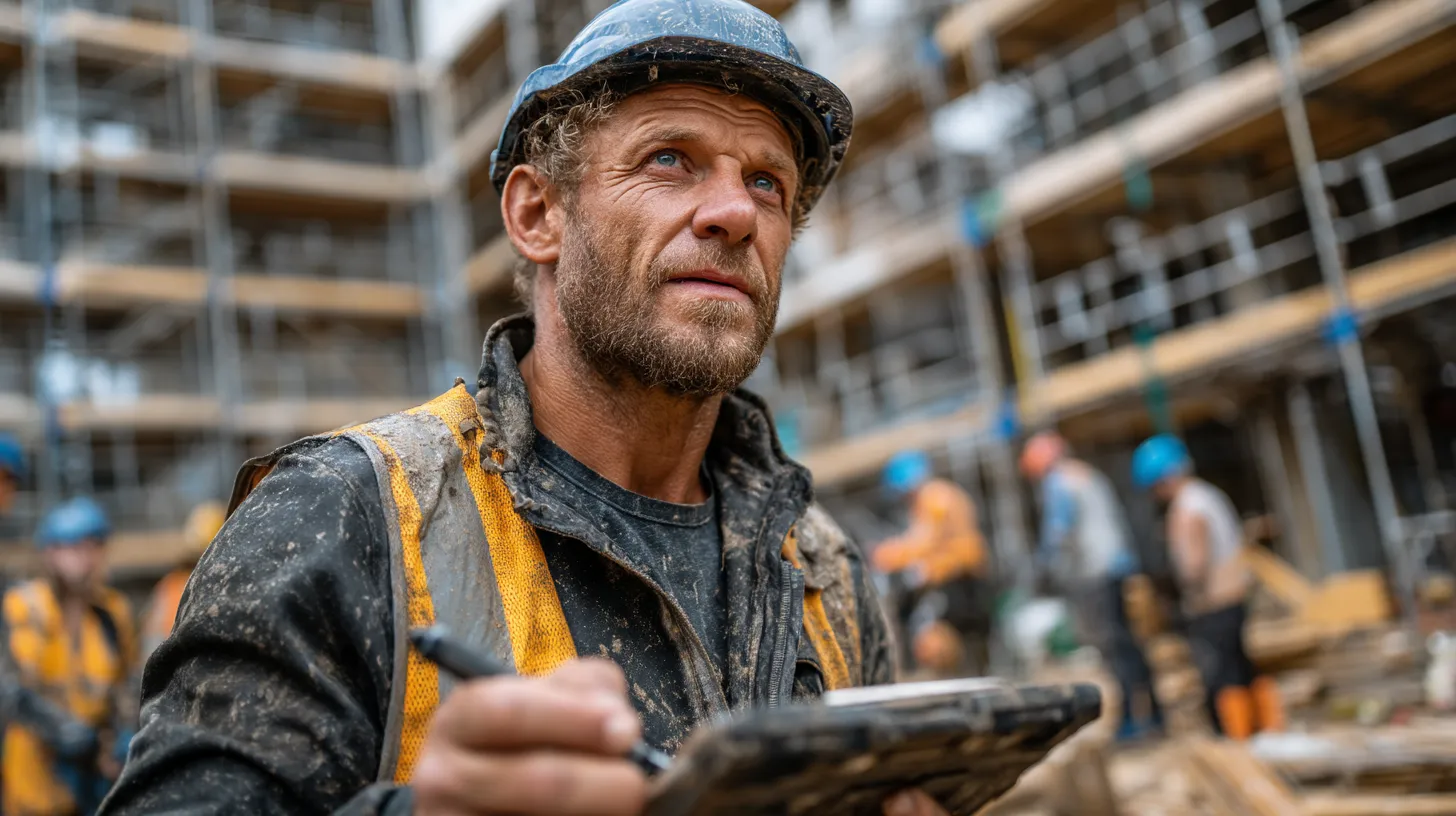
The Digital Revolution Reshaping Construction Quality Management
Are you still relying on manual systems that leave your construction sites vulnerable to safety gaps and compliance failures?
Market Size & Growth: A Booming Digital Transformation
The UK construction software market is projected to reach USD 682.5 million by 2035, growing at an impressive CAGR of 8.525% from 2025-2035. Within this landscape, quality management solutions are experiencing particularly robust growth, with the UK quality management software market expected to reach USD 798.6 million by 2030, growing at a CAGR of 8.4% from 2025.
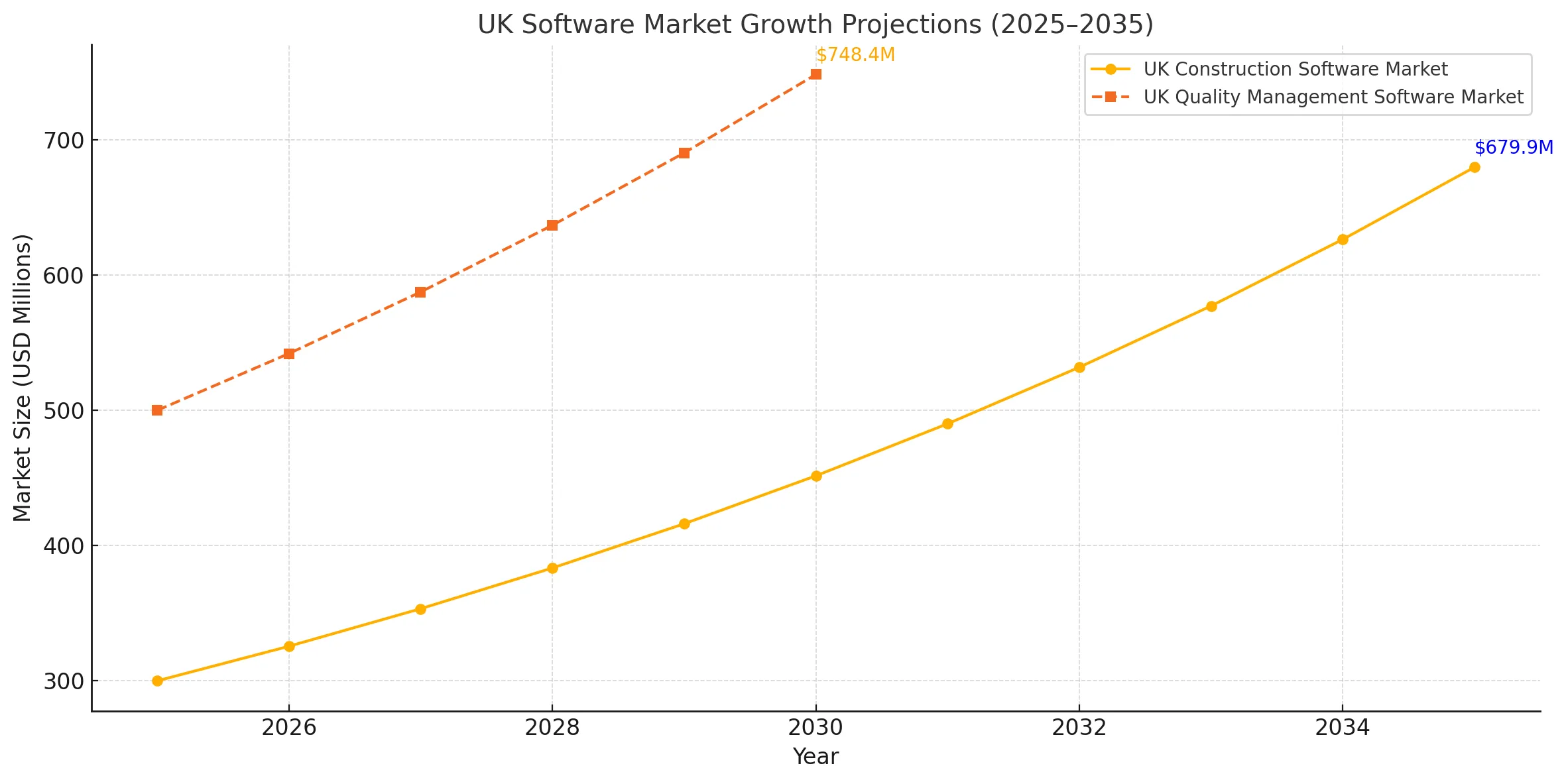
Drivers of Change: Why Construction is Embracing Digital Quality Management
The shift toward digital quality management isn't happening by chance. Several powerful forces are compelling UK construction firms to rethink how they manage safety and quality processes:
- Regulatory Complexity: The UK construction industry faces increasingly stringent regulatory requirements, making manual compliance tracking nearly impossible to maintain effectively.
- Mobile Technology Integration: The proliferation of smart devices and Internet of Things (IoT) technology on construction sites demands more sophisticated digital management tools.
- Cost Pressures: In a sector with tight margins, the efficiency gains from automating routine quality and safety processes represent significant competitive advantages.
Key Benefits & Business Case
Efficiency Gains: Transforming Safety Officer Workloads
Construction firms implementing QMS software report an average 37% reduction in time spent on administrative safety documentation, freeing Safety Officers to focus on actual hazard prevention rather than paperwork.
- Replace hours of manual form completion with digital smart forms that can be completed in minutes – even offline on remote construction sites.
- Eliminate duplicate data entry with seamless integration between incident reporting, corrective actions, and regulatory documentation.
- Gain instant visibility across multiple construction sites with centralised dashboards that highlight safety trends and emerging risks.
Cost & Compliance Impact: The Financial Case for Digital Quality Management
Impact Area | Measured Benefit |
---|---|
Safety Incident Reduction | 28% average decrease within 12 months |
Audit Preparation Time | 62% reduction in hours spent |
Compliance Documentation | 89% improvement in accuracy and completeness |
Staff Training Compliance | 94% of certifications kept current vs. 67% with manual systems |
While the upfront investment in QMS software may seem significant, the financial risk of non-adoption is far greater. McKinsey research supports this with industry-wide data on digital transformation ROI in construction.
Implementation Strategies
Planning & Assessment: Building Your Digital Quality Foundation
- Conduct a thorough audit of your current safety processes, documenting pain points, compliance gaps, and administrative bottlenecks. Aligning with ISO 45001 helps formalise these efforts.
- Identify your non-negotiable features based on specific construction safety requirements. These typically include mobile incident reporting, document control for safety procedures, equipment inspection checklists, and automated compliance notifications.
- Evaluate cloud-based vs on-premise QMS solutions based on your specific construction site security requirements and internet connectivity challenges. Most UK construction firms now prefer cloud solutions for their accessibility across multiple sites.
- Develop a phased implementation plan that prioritises high-impact modules first. Many safety officers start with incident reporting and corrective actions before expanding to comprehensive audit and training management.
Deployment & Training: Ensuring Adoption Across Construction Teams
Technology Selection: Finding the Right Fit for Construction
When evaluating QMS software options, construction safety officers should prioritise solutions designed with the unique challenges of construction environments in mind. Q-Hub's Safety Management Tools offer construction-specific features that address the mobile nature of site work, the need for offline capability, and the robust documentation requirements of the sector.
- Prioritise mobile-enabled platforms with offline capabilities that support real-time incident reporting from construction sites with potentially limited connectivity.
- Look for strong document control and corrective action features with automated notification workflows to ensure nothing falls through the cracks.
- Ensure the system can generate regulatory reports in formats required by UK construction authorities, saving hours of manual formatting.
Myth vs Reality: Overcoming QMS Software Misconceptions
- "QMS software is too complicated for our construction site workers to use effectively."
- Modern quality management solutions like Q-Hub are designed with construction workflows in mind, featuring intuitive mobile interfaces that require minimal training. The CITB’s Digital Competence Framework shows how construction workers are becoming increasingly tech-ready.
- "We're too small a construction firm to justify the investment in QMS software."
- Smaller construction firms often see the fastest ROI from QMS implementation precisely because they have fewer resources to dedicate to manual quality and safety processes. Modern cloud-based solutions offer flexible pricing models that scale with your business, making them accessible even for small and medium-sized contractors.
Case Studies & Success Stories
BMC Analysis: From Manual Struggles to Streamlined Efficiency
https://www.q-hub.app/case-studies/bmc-analysisBMC Analysis achieved significant improvements in NCR root cause tracking and overall process efficiency through their QMS software implementation.
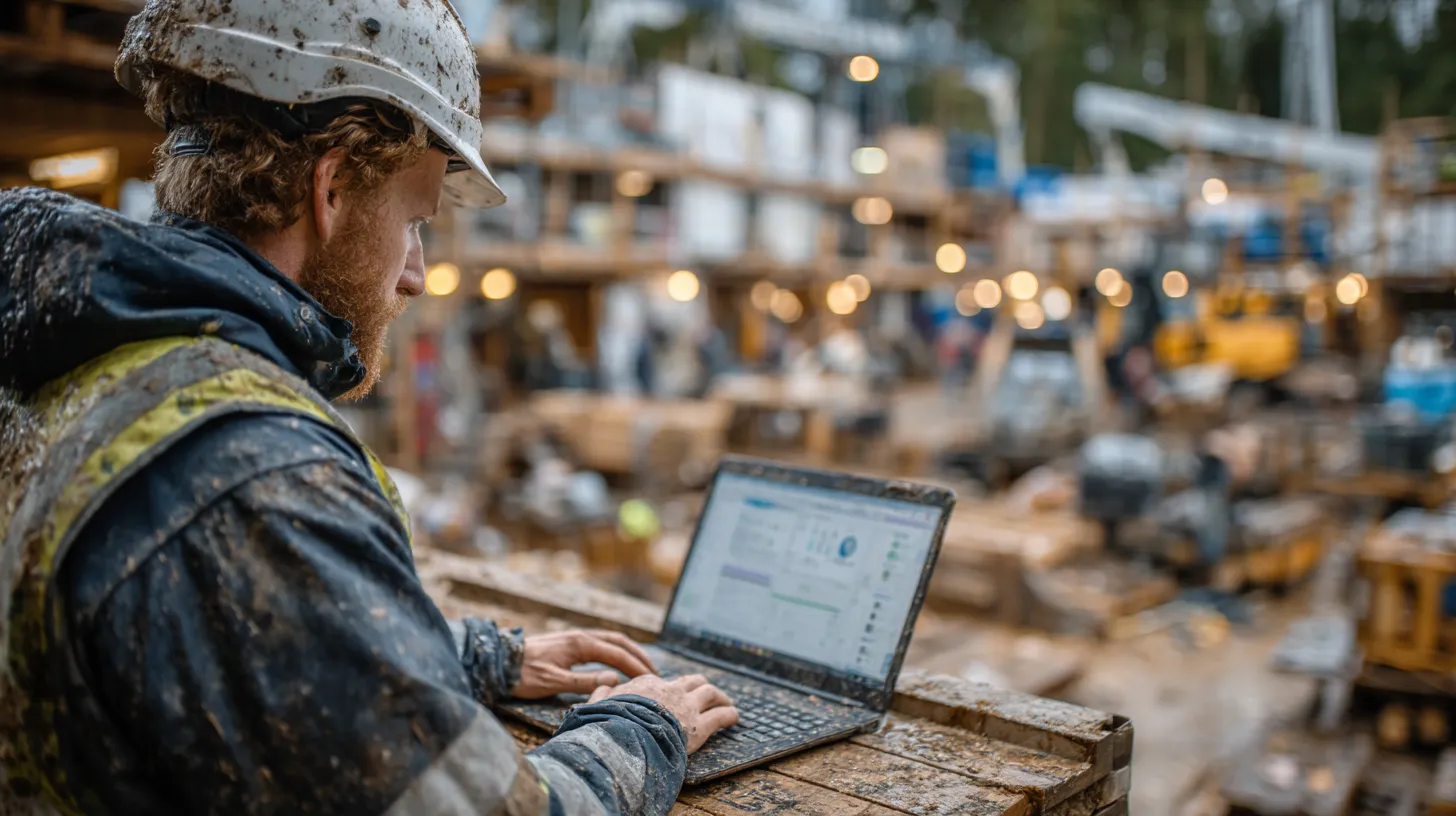
The Challenge: Manual Quality Management Bottlenecks
Before implementing QMS software, BMC Analysis faced several critical challenges that will sound familiar to many construction safety officers:
- Manual NCR tracking led to fragmented investigations and inefficient issue resolution processes.
- Time-consuming document control with physical signing sheets that were easily lost or forgotten.
- No automated system existed to track calibration and maintenance of critical safety equipment.
- Audit preparation required significant manual intervention, creating bottlenecks and risks of incomplete documentation.
The Solution: Digital Transformation of Quality Processes
BMC Analysis implemented Q-Hub's Quality Management System, focusing on three key areas:
- Streamlining NCR management through centralised digital tracking and automated notifications
- Digitising document control to ensure proper version management and acknowledgment
- Implementing structured asset calibration and maintenance schedules
Results & Metrics: Quantifiable Improvements
"The automation and centralisation that Q-Hub offers have completely transformed our quality management operations. NCR reporting is streamlined, document control is effortless, and audit preparation is faster than ever. These changes have saved us countless hours across multiple teams."
Future Outlook & Trends
Digital Transformation Acceleration in UK Construction
UK construction firms are steadily accelerating their uptake of advanced software solutions to digitise and automate core processes. The construction and design software market in the UK is projected to reach a volume of £641.08 million by 2030, growing at a CAGR of 1.82% between 2025-2030.
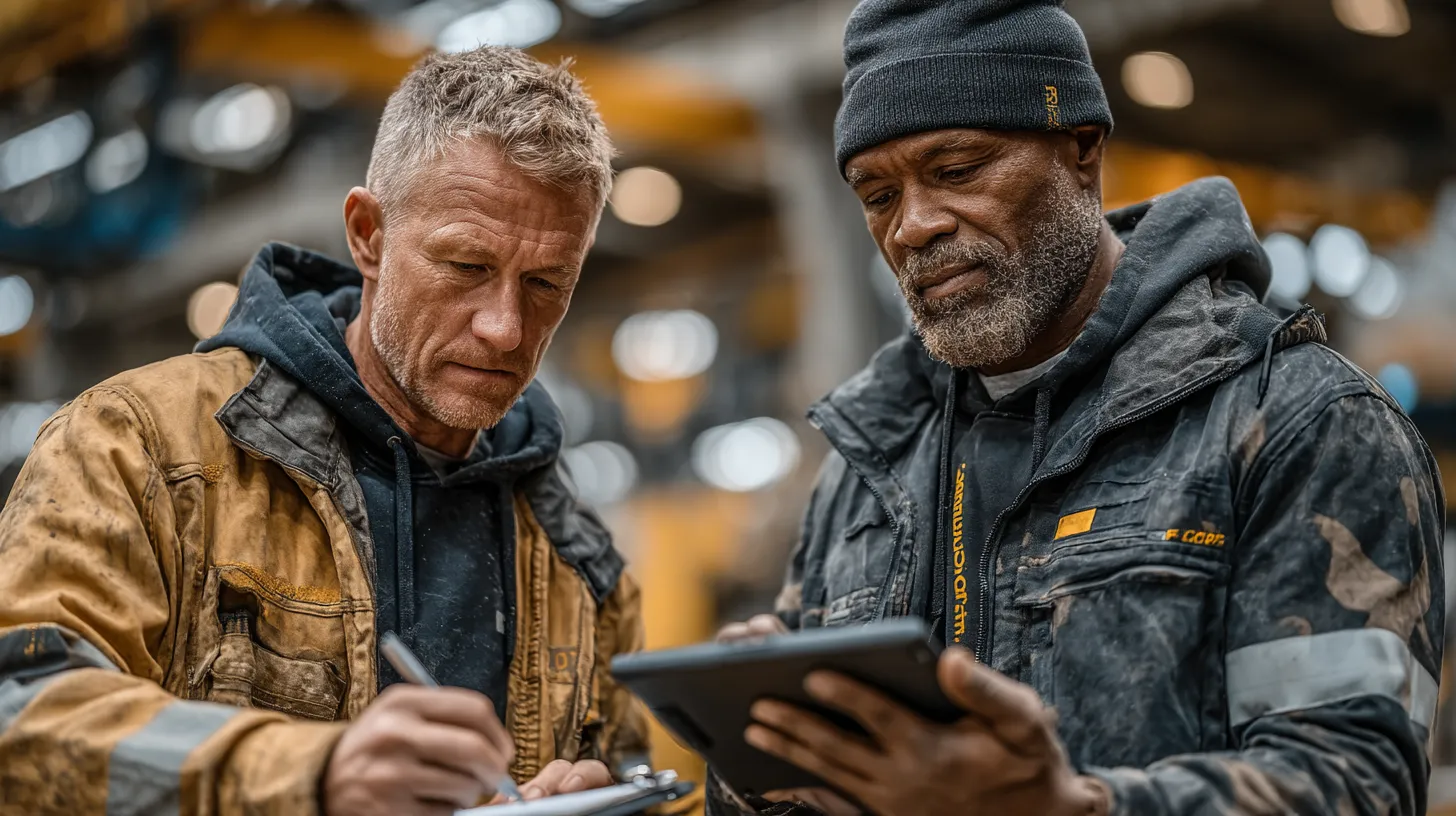
Emerging Technologies Reshaping Quality Management
Q-Hub is at the forefront of integrating these emerging technologies into practical solutions for construction safety officers:
- AI and machine learning capabilities are increasingly incorporated into QMS solutions, enhancing the software's ability to analyse safety data, identify patterns, and make data-driven recommendations.
- Mobile capabilities continue to advance, allowing for more sophisticated on-site safety management through augmented reality inspections and voice-activated reporting.
- Predictive analytics for risk management will enable the forecasting of potential safety issues before they occur, allowing for truly proactive safety management.
- Regulatory Complexity: The UK construction industry faces increasingly stringent regulatory requirements, making manual compliance tracking nearly impossible to maintain effectively. View official guidance from the Health and Safety Executive.
While these innovations are already making a significant impact on day-to-day site safety and compliance, the next wave of technological advancements promises to take quality management even further. Here’s what’s on the horizon:
- Greater integration between QMS software and other construction technologies such as Building Information Modelling (BIM) will create more comprehensive safety management ecosystems.
- User experience will continue to evolve with more intuitive interfaces designed specifically for construction professionals, making it easier for Safety Officers to implement and maintain safety protocols.
Key Takeaways: The Path Forward for Construction Safety Officers
The transition from clipboard chaos to cloud control isn't just about keeping up with technology—it's about fundamentally transforming how construction safety officers protect workers, ensure compliance, and demonstrate value to their organisations. By implementing robust QMS software solutions, you can enhance quality assurance, streamline quality processes, and create a continuous improvement tool that elevates safety standards across all your construction sites.
The evidence is clear: firms that embrace digital quality management see fewer incidents, higher compliance rates, and significant time savings. See HSE’s latest sector report for supporting statistics.
Is your construction firm ready to leave manual quality management behind and embrace the digital future of safety compliance?