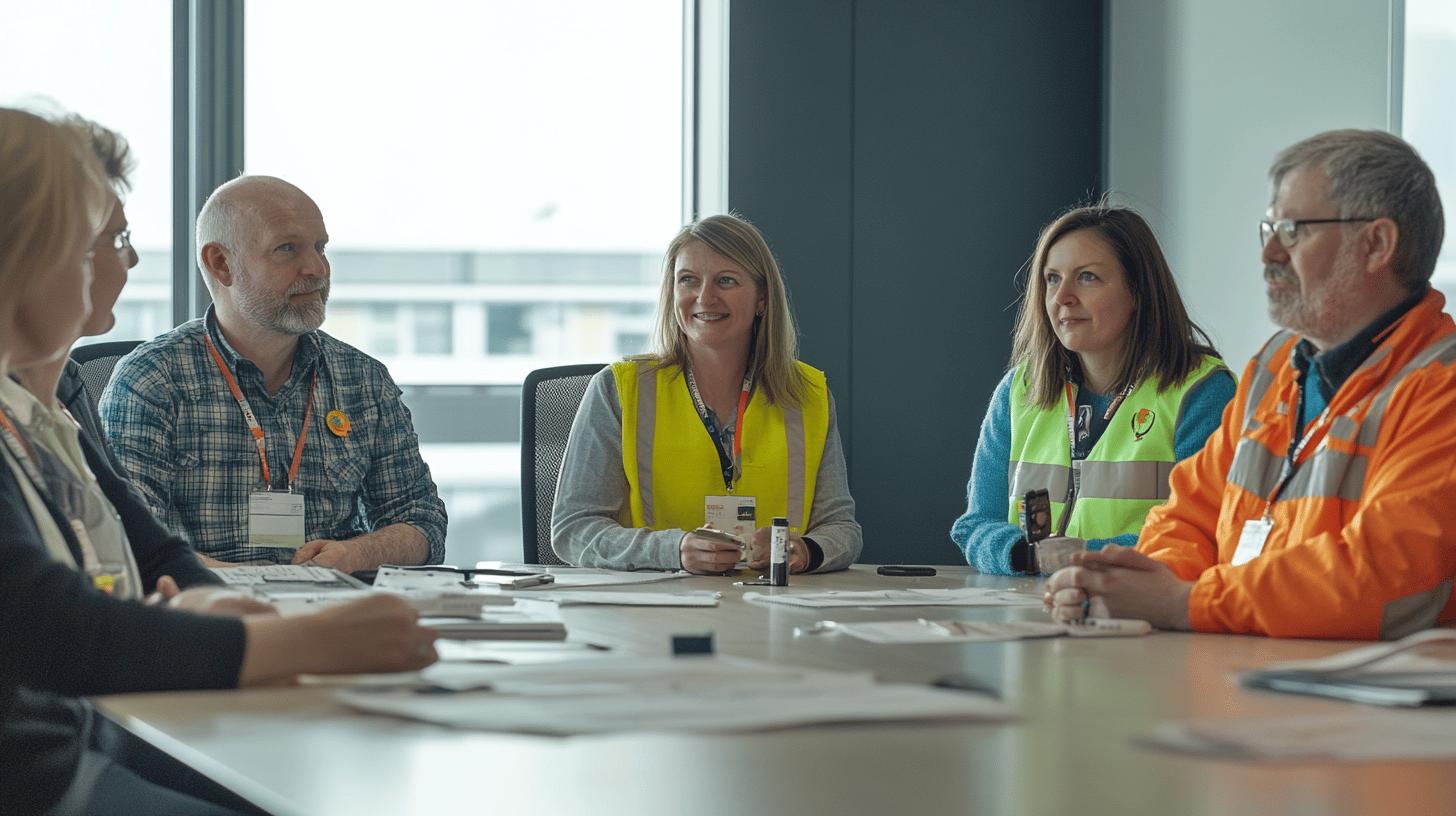
User Training Boosts Product Safety, Quality Assurance
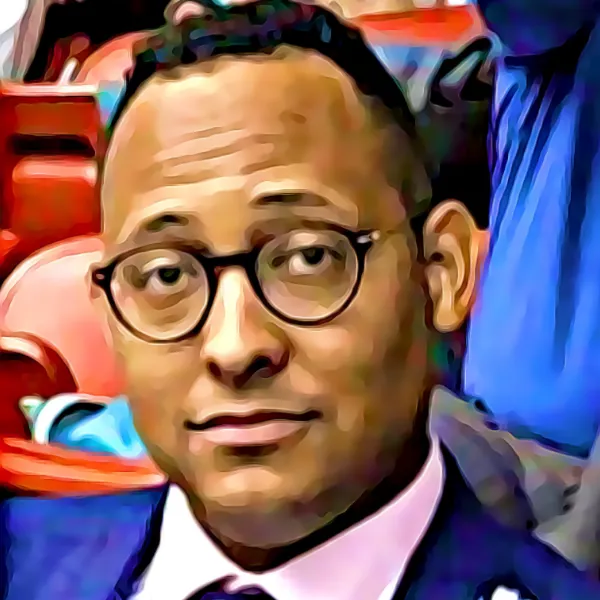
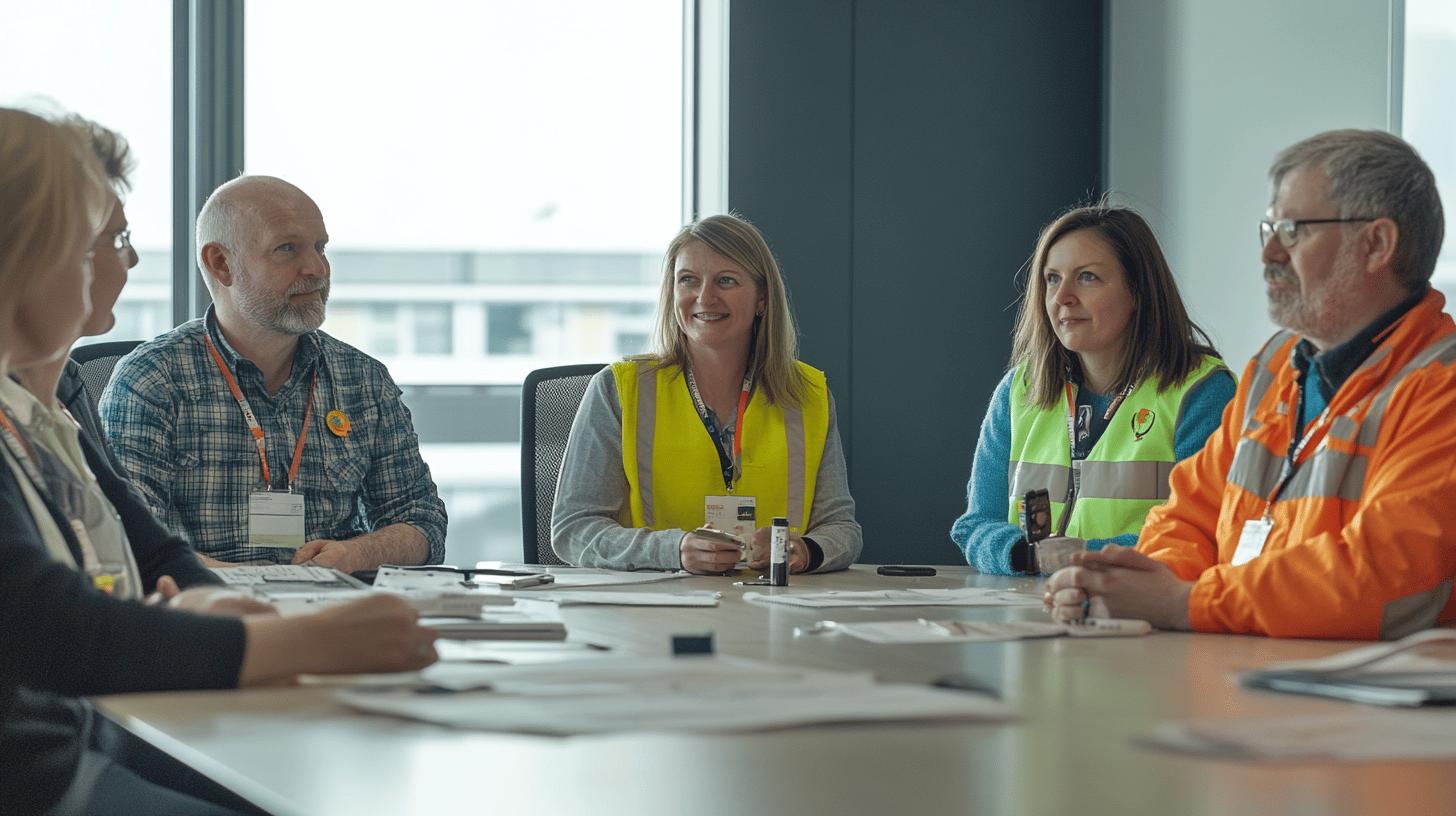
User Training Boosts Product Safety, Quality Assurance
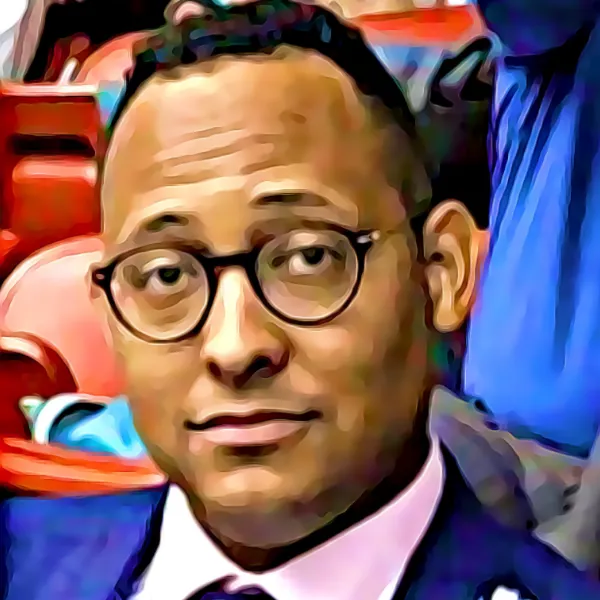
How User Training and Onboarding Enhance Engineering Staff's Capabilities in Product Safety and Quality Assurance
Effective user training and onboarding programs are vital for engineering teams to excel in product safety and quality assurance.
By integrating the user training and onboarding approach into their processes, teams can harness tailored training that resonates with both safety protocols and quality benchmarks. This leads to enhanced clarity and a culture where every team member not only understands, but also effectively implements critical safety measures. Q-Hub recognises that these structured initiatives transform engineers from merely understanding compliance standards to becoming proficient implementers of critical safety protocols. Well-designed programs demystify complex regulations like ISO 9001 and ISO 45001, making them actionable for everyday engineering tasks while fostering a culture where safety and quality become ingrained in every decision.
Companies implementing comprehensive training programs report significant improvements in operational metrics, with quality assurance audits revealing a 20-30% reduction in product defects. By tailoring these initiatives to specific roles and regulatory requirements, organisations build engineering teams that confidently navigate compliance challenges while maintaining the highest standards of safety and quality.
Transforming Paper-Based Systems into Digital Excellence
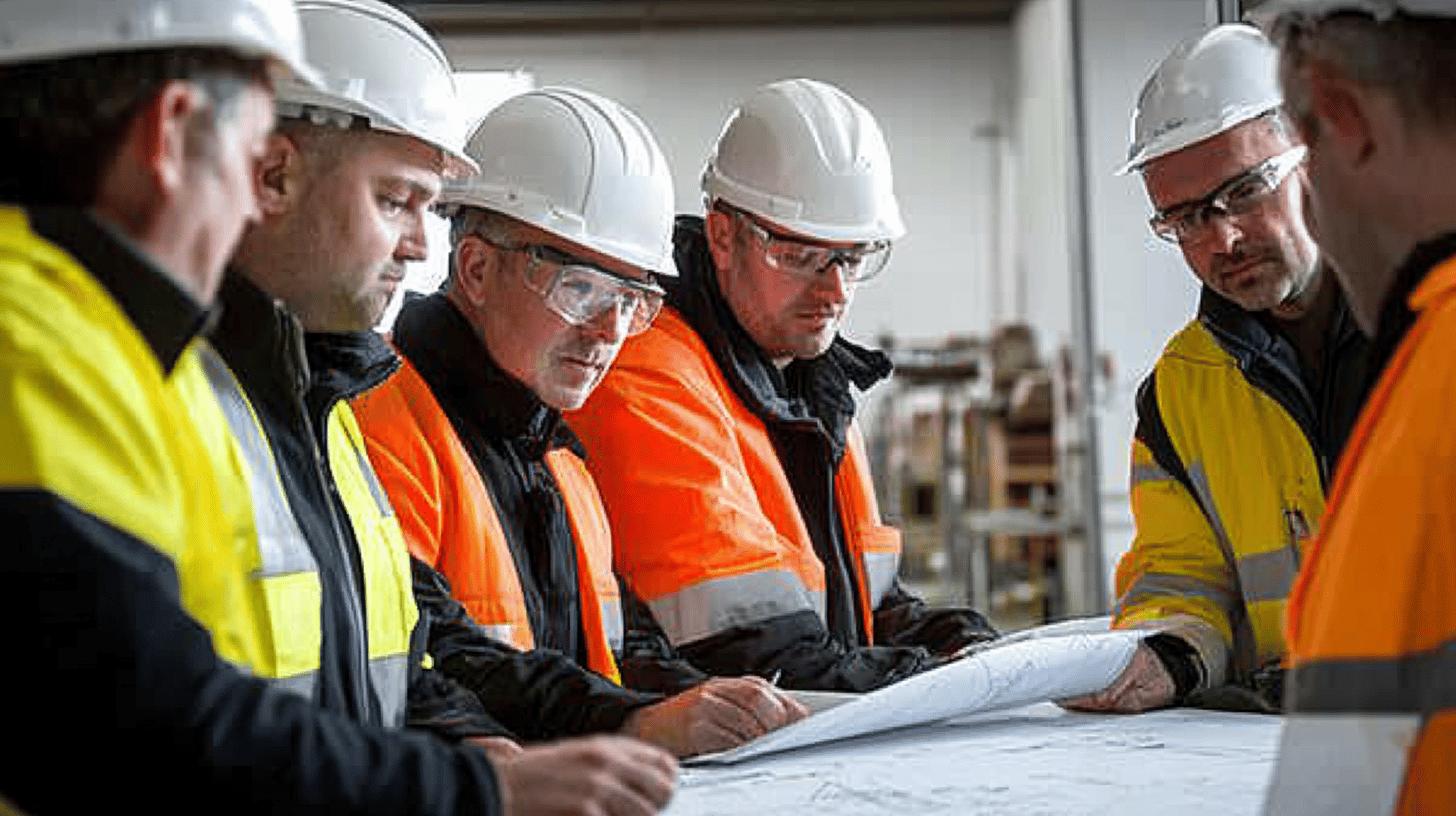
The shift from manual, paper-based training systems to digital solutions has revolutionised how engineering teams learn and apply safety standards. As demonstrated in Rocal Insulating Panels' experience with Q-Hub, digitising document control eliminated hours of wasted time searching through cluttered files and significantly improved compliance management.
When Scottish Leather Group implemented Q-Hub's digital platform, they transformed their approach to training across multiple ISO standards. Their once fragmented, resource-intensive training processes became streamlined, with real-time reporting capabilities that freed staff to focus on value-added activities rather than administrative tasks.
The implementation of digital training tools resulted in transformative outcomes for SLG: enhanced compliance management, streamlined communication, increased operational efficiency, and widespread adoption across all levels of the organisation.
These digital transformations don't just save time—they fundamentally change how engineering teams engage with safety and quality protocols:
- Reduced product defects by up to 30% through accessible, consistent training
- Improved workplace safety through better protocol adherence
- Enhanced risk assessment capabilities that catch issues before they escalate
- Greater compliance consistency across engineering teams
Building Effective Training Frameworks That Drive Results
The foundation of any successful engineering training program begins with thorough needs assessment. This critical first step identifies skill gaps and maps them against organisational objectives and compliance requirements. Q-Hub's experience with engineering firms shows that when training aligns precisely with both regulatory standards and specific operational challenges, the impact on safety and quality metrics is substantial.
Customised modules addressing role-specific requirements ensure engineers receive relevant training that they can immediately apply. For example, BMC Analysis partnered with Q-Hub to create targeted digital training programs that transformed their approach to non-conformance reporting and quality management, resulting in faster resolution times and improved compliance.
Technology integration plays a decisive role in modern training effectiveness. Learning management systems centralise training delivery while ensuring consistency across engineering teams of all sizes. These platforms offer automated tracking and reporting, giving managers immediate visibility into training progress and compliance status.
<table border="0"> <tr><th>Training Component</th><th>Traditional Approach</th><th>Digital Transformation with Q-Hub</th></tr> <tr><td>Document Management</td><td>Manual file storage, difficult retrieval</td><td>Centralised digital library with version control</td></tr> <tr><td>Compliance Tracking</td><td>Spreadsheets and paper records</td><td>Automated monitoring with real-time dashboards</td></tr> <tr><td>Knowledge Assessment</td><td>Periodic written tests</td><td>Continuous digital verification with "read and understood" tracking</td></tr> <tr><td>Performance Analysis</td><td>Manual review of incident reports</td><td>Integrated KPI dashboards showing real-time metrics</td></tr> </table>Modern Tools Revolutionising Engineering Training
Digital transformation has dramatically enhanced how engineering teams learn and apply safety and quality standards. Q-Hub's software platform exemplifies how modern tools can streamline previously cumbersome training processes while improving outcomes. For Anglia Cathodic Protection, replacing fragmented spreadsheets and paper-based systems with Q-Hub's digital platform transformed their ability to manage compliance across multiple sites.
Learning management systems have revolutionised training delivery, enabling organisations to provide consistent, role-specific modules that can be accessed anytime, anywhere. When Weston Aerospace implemented Q-Hub's digital platform, they transformed their training approach from resource-intensive manual processes to streamlined, automated workflows that freed up staff time while improving compliance outcomes.
- Digital documentation systems provide instant access to up-to-date procedures and training materials
- Automated tracking ensures all team members complete required training
- Real-time performance dashboards highlight areas needing additional focus
- Centralized knowledge repositories maintain institutional expertise even as teams change
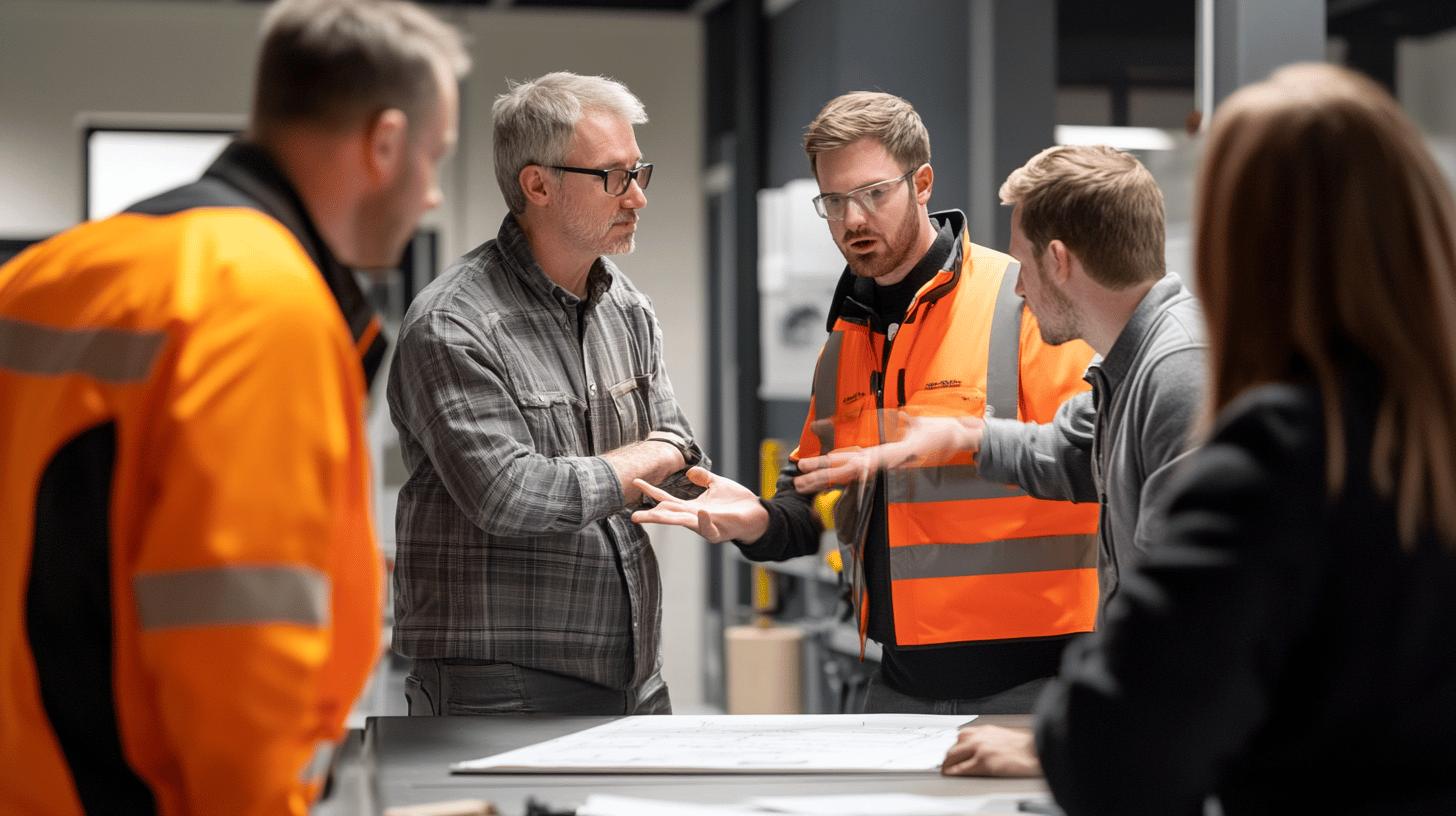
Measuring Success Through Quantifiable Outcomes
Effective training isn't just about completion rates—it's about measurable improvements in safety and quality outcomes.
Embracing a strategy akin to continuous improvement programmes helps engineering teams evolve and fine-tune their practices over time. This dynamic process ensures that training remains relevant, adaptive, and consistently aligned with the evolving challenges in product safety and quality assurance. Organisations partnering with Q-Hub consistently report significant performance improvements after implementing structured digital training programs. Tracking metrics allows companies to identify what's working and where additional focus may be needed.
Fowlers of Bristol transformed their quality management approach with Q-Hub's platform, implementing robust tracking systems that monitored both training completion and subsequent performance metrics. Their "Zero Defects" goal became measurable through dashboard-driven KPIs like "Right First Time" performance, creating direct visibility between training initiatives and quality outcomes.
The most effective measurement approaches combine quantitative metrics with qualitative feedback mechanisms:
Metric | Purpose | Example |
---|---|---|
Training Completion Rates | Ensure regulatory compliance coverage | 90% of engineers completing ISO 9001 training within first month |
Knowledge Retention | Verify understanding of critical concepts | 85% average score on safety protocol assessments |
Performance Improvement | Measure real-world application | 25% reduction in quality defects post-training implementation |
Feedback Scores | Gauge program effectiveness | 4.2/5 average rating for training relevance and application |
Real-World Transformation Through Digital Training
The impact of well-structured digital training programs becomes clear through real-world success stories. When Scottish Leather Group implemented Q-Hub's platform, they transformed their ability to manage compliance across multiple ISO standards, including ISO 9001 for quality management and ISO 45001 for health and safety. Their digital transformation eliminated silos between departments and created a unified approach to training that engaged employees at all levels.
Weston Aerospace faced growing inefficiencies with legacy systems that failed to deliver actionable data when needed. After implementing Q-Hub's digital platform, they centralised compliance management through the Audit Hub, Process Hub, and Registers, dramatically improving their ability to track training completion and measure subsequent performance improvements.
These transformations deliver consistent benefits across different engineering sectors:
- Accelerated onboarding that gets engineers productive faster
- Reduced administrative burden through automated tracking and reporting
- Improved compliance consistency across multiple sites and departments
- Enhanced visibility into training effectiveness through integrated dashboards
Building a Culture of Continuous Improvement
Effective training isn't a one-time event but an ongoing commitment to excellence. Q-Hub's digital platform supports this approach by enabling engineering teams to build continuous improvement into their everyday operations. Regular training updates ensure engineers stay current with evolving standards, while digital documentation keeps critical knowledge accessible across the organisation.
Organisations implementing robust digital training programs report 10-15% annual improvements in quality performance metrics. This continuous upward trajectory happens because these systems make learning part of the engineering culture rather than a periodic requirement. When BMC Analysis digitised their document control and asset management with Q-Hub, they created a framework where improvement became systematic rather than occasional.
The most successful engineering organisations make training an integral part of their operational strategy, with:
- Quarterly refreshers on changing safety and quality protocols
- Digital certification tracking ensuring compliance credentials remain current
- Integrated feedback mechanisms to refine training based on real-world application
- Performance dashboards highlighting the connection between training and outcomes
As engineering teams face increasingly complex regulatory requirements and quality standards, effective training becomes a competitive advantage. Q-Hub's digital transformation platform provides the tools organisations need to build comprehensive, measurable training programs that drive real improvements in safety and quality outcomes while creating a culture of continuous improvement.
Start using Q-Hub today
- Manage compliance in one place
- Streamline your teams and tasks
- Use Q-Hub free for 30 days