
Supplier and Contractor Management: Competence in Engineering
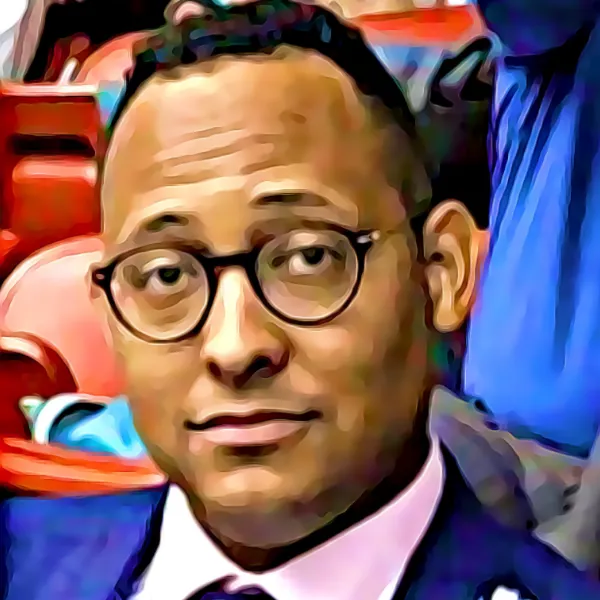

Supplier and Contractor Management: Competence in Engineering
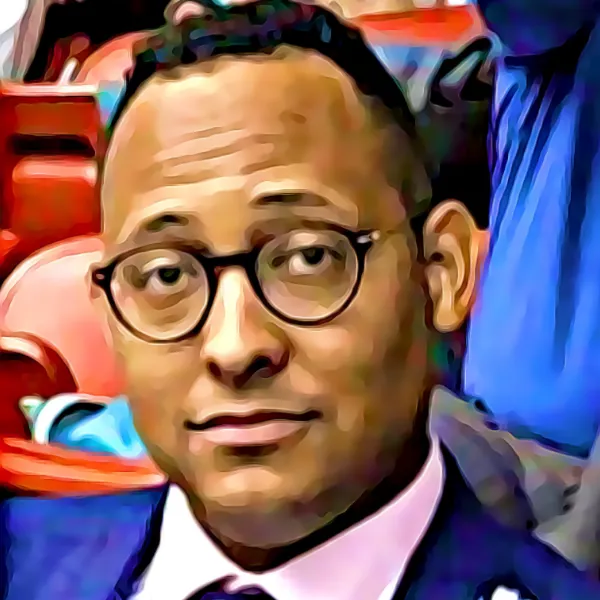
Supplier and Contractor Management: Key Challenges in Maintaining Competence Standards
Managing supplier and contractor competence standards in engineering sourcing presents significant challenges for organisations today.
Integrating a robust supplier and contractor management system is crucial to streamline processes and ensure that every contractor and supplier meets industry competence benchmarks. This digital integration mirrors the industry's shift from fragmented data systems to consolidated platforms, ensuring that operational excellence and regulatory compliance are continually achieved. Achieving consistency across fragmented supply chains remains the core difficulty, with competence standards being non-negotiable in high-stakes engineering projects.
Fragmented data systems lie at the heart of the problem. Many companies still rely on outdated, siloed approaches to track supplier capabilities and contractor qualifications. Imagine trying to verify a contractor's certifications when half their records exist in spreadsheets and the rest in disconnected software systems. This fragmentation creates inefficiencies and increases non-compliance risks with crucial standards like ISO 9001.
Without centralised competence management, organisations face increased regulatory risks, project delays, and potential safety incidents across their supply chains.
Navigating the Complexity of Regional and Industry Standards
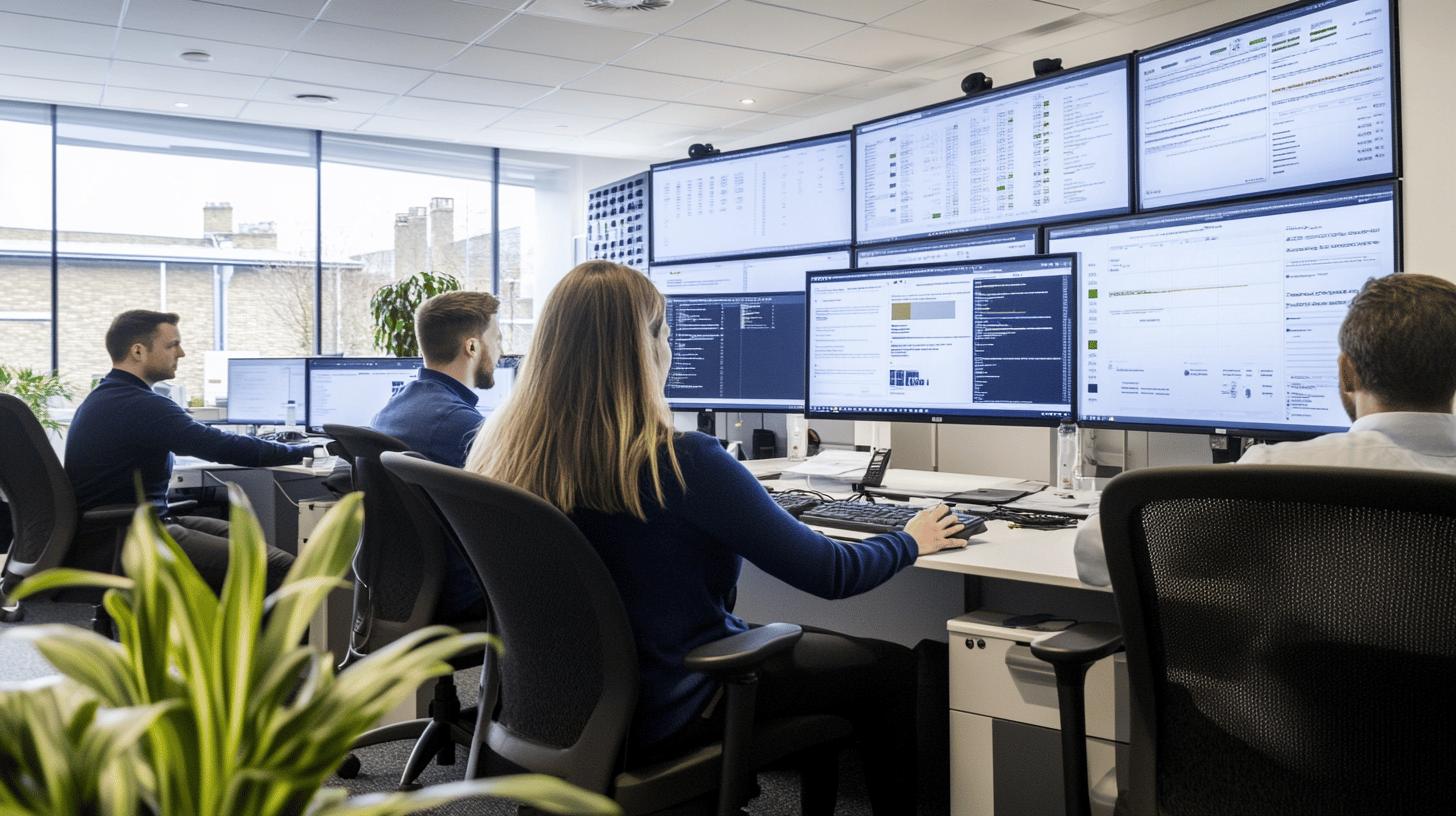
The diversity of regulations across industries and regions significantly complicates competence management. A supplier meeting aerospace standards might fail to satisfy automotive requirements, creating inconsistencies that lead to delays, cost overruns and safety concerns.
Training inconsistency further exacerbates these challenges. With contractors coming from varied operational backgrounds, standardisation becomes essential but difficult to implement. Companies like Weston Aerospace have addressed this by implementing digital platforms that standardise competence verification, resulting in significant efficiency improvements.
As Scottish Leather Group discovered, managing multiple ISO standards (including ISO 9001 for quality and ISO 45001 for health and safety) across sites requires a unified approach rather than fragmented systems. Their transition to a centralised platform delivered measurable improvements in compliance management.
Modern Solutions to Age-Old Challenges
So how are leading organisations addressing these challenges? Q-Hub works with companies to implement digital solutions that centralise competence management. For example, Anglia Cathodic Protection transformed their paper-based systems into a unified digital platform, significantly improving compliance visibility and operational oversight.
The most successful approaches to competence management include:
- Establishing clear, industry-specific competence frameworks tailored to each role
- Implementing centralised systems for real-time monitoring of qualifications and certifications
- Creating standardised assessment protocols that ensure consistent evaluation
- Setting up automated alerts for certification renewals and compliance gaps
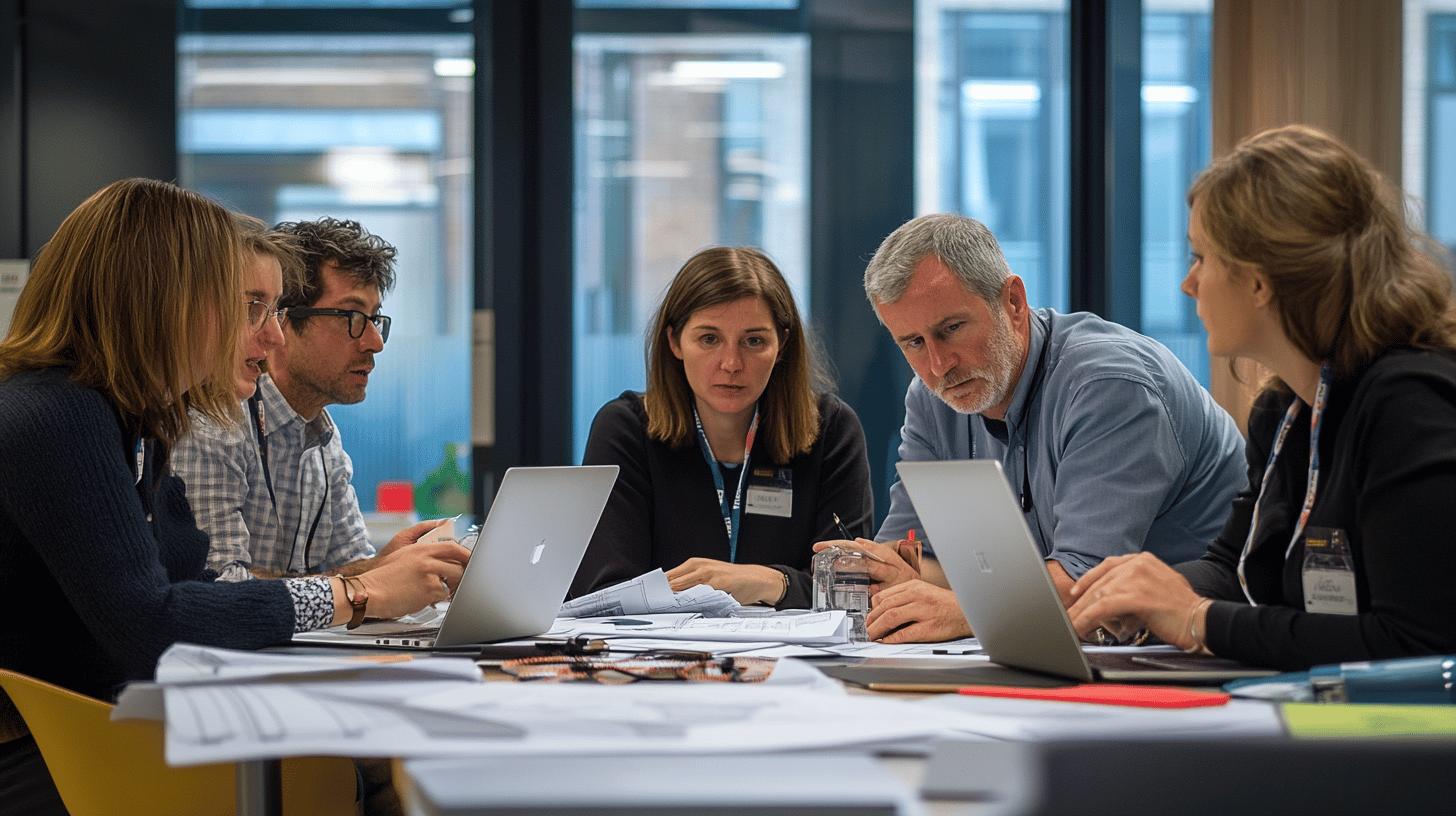
Rocal Insulating Panels experienced how shifting from fragmented paper processes to digital workflows improved visibility and accountability across departments. Their safety management system now provides consistent tracking of competencies, inspections, and incidents through a single platform.
Measuring the Impact of Streamlined Competence Management
The business benefits of addressing fragmentation in competence management are substantial and quantifiable:
<table border="0"> <tr><th>Metric</th><th>Before Digital Integration</th><th>After Digital Integration</th></tr> <tr><td>Compliance Verification Time</td><td>Days to Weeks</td><td>Minutes to Hours</td></tr> <tr><td>Contractor Certification Gaps</td><td>15-25%</td><td>Under 5%</td></tr> <tr><td>Audit Preparation Time</td><td>Weeks</td><td>Hours</td></tr> <tr><td>Non-Compliance Incidents</td><td>Frequent</td><td>Reduced by 25%+</td></tr> </table>Building a Foundation for Continuous Improvement
Effective competence management isn't just about meeting today's standards—it's about creating systems that evolve with changing industry requirements. BMC Analysis discovered this when they digitised their NCR management and asset calibration processes, establishing a foundation for ongoing improvement rather than just solving immediate problems.
Regular performance reviews coupled with structured feedback systems create the continuous improvement cycle that keeps competence standards relevant and robust.
Leveraging continuous improvement programmes enables organisations to refine their supplier and contractor processes, ensuring that even as industry standards evolve, competence and safety remain at the forefront. This approach not only strengthens operational oversight but also fosters an environment where proactive enhancements become part of the organisational culture. Fowlers of Bristol, for instance, implemented dashboards tracking "Right First Time" performance metrics, linking actions directly to forms and registers for improved quality management.
Key Components of an Effective Competence Management System
An effective system includes centralised documentation, automated compliance alerts, standardised assessment protocols, and real-time visibility across the supply chain. The ability to track "read and understood" acknowledgments, as implemented by Anglia Cathodic Protection, ensures that critical information reaches all relevant personnel.
The Technology Advantage in Competence Verification
Modern competence management platforms provide organisations with tools that transcend traditional approaches. These systems enable real-time monitoring of supplier and contractor qualifications, automated alerts for non-compliance issues, and integrated training modules to address competency gaps immediately.
What makes these platforms particularly valuable is their ability to create a single source of truth for all competence-related data. Rather than searching through disconnected systems, managers can instantly access comprehensive qualification records, certification status, and compliance history—all from one interface.
The Path Forward: Strategic Integration
The most effective approach to supplier and contractor management integrates competence standards directly into core business processes. This means moving beyond standalone systems to create an ecosystem where competence verification becomes part of procurement, project planning, and operational delivery.
Q-Hub specialises in creating these integrated environments where competence management flows seamlessly across business functions. By connecting previously disconnected processes, organisations gain comprehensive visibility into their supply chain competence landscape while significantly reducing administrative burden.
As we've seen with companies like Weston Aerospace and Scottish Leather Group, the transformation from fragmented to integrated competence management creates ripple effects across the organisation—improving safety, enhancing quality, and ultimately delivering better project outcomes.
Ready to transform your approach to supplier and contractor competence management? Q-Hub offers tailored digital solutions that centralise your systems, standardise your processes, and ultimately drive operational excellence across your supply chain.
Start using Q-Hub today
- Manage compliance in one place
- Streamline your teams and tasks
- Use Q-Hub free for 30 days