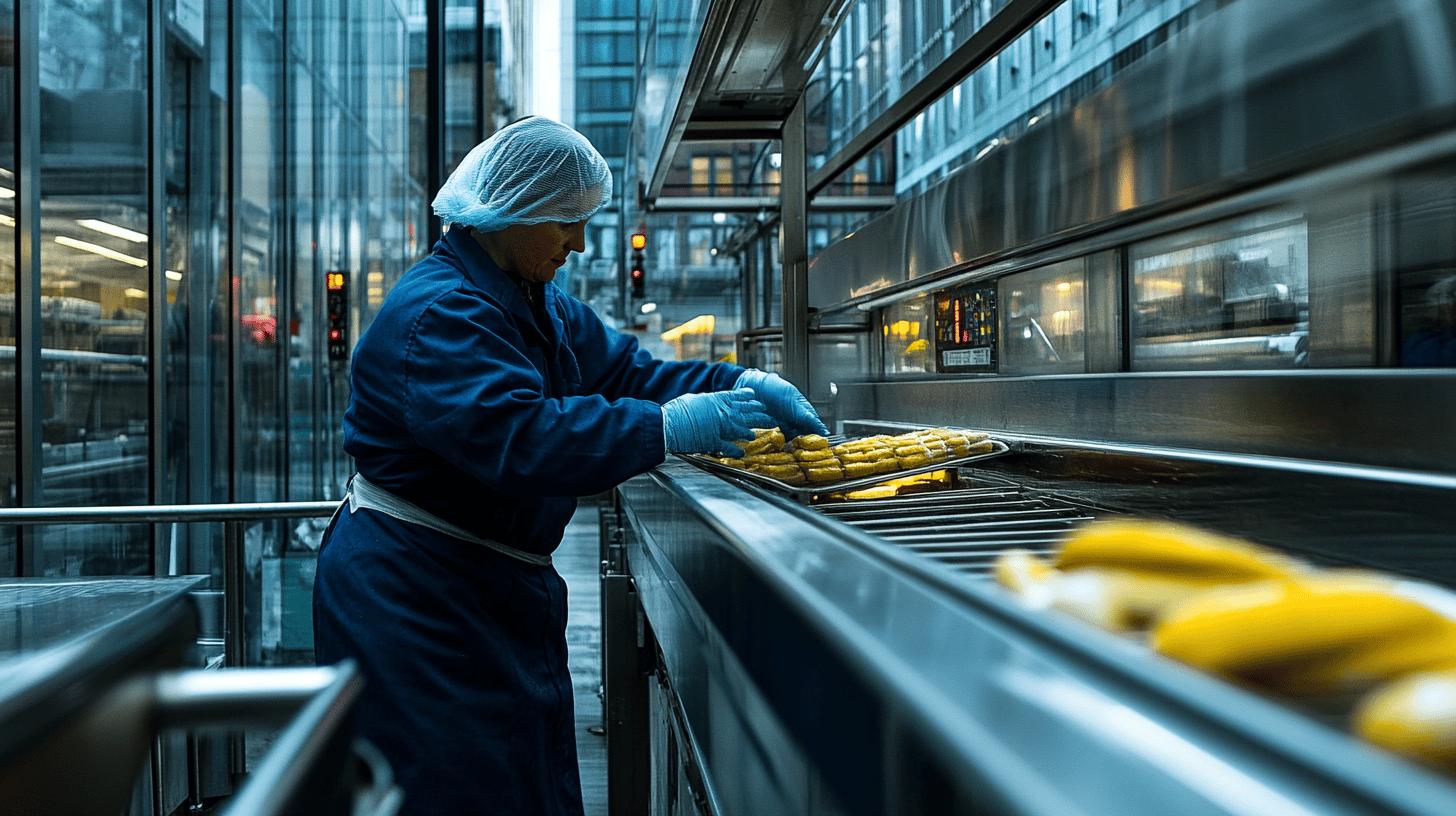
User Training Boosts Product Safety in Food Manufacturing
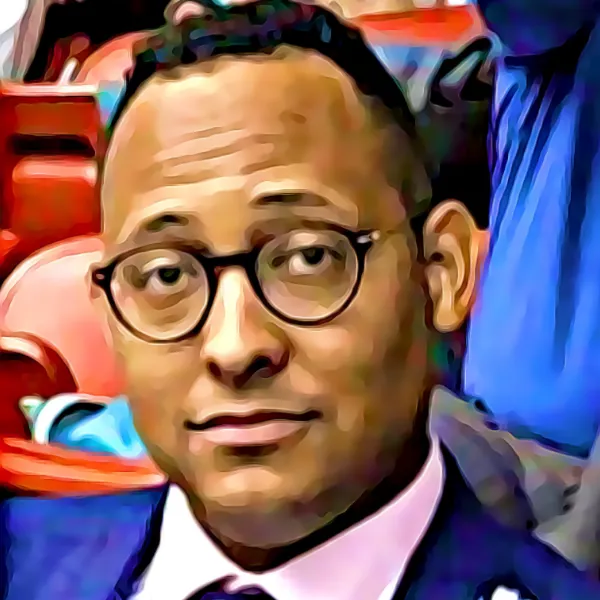
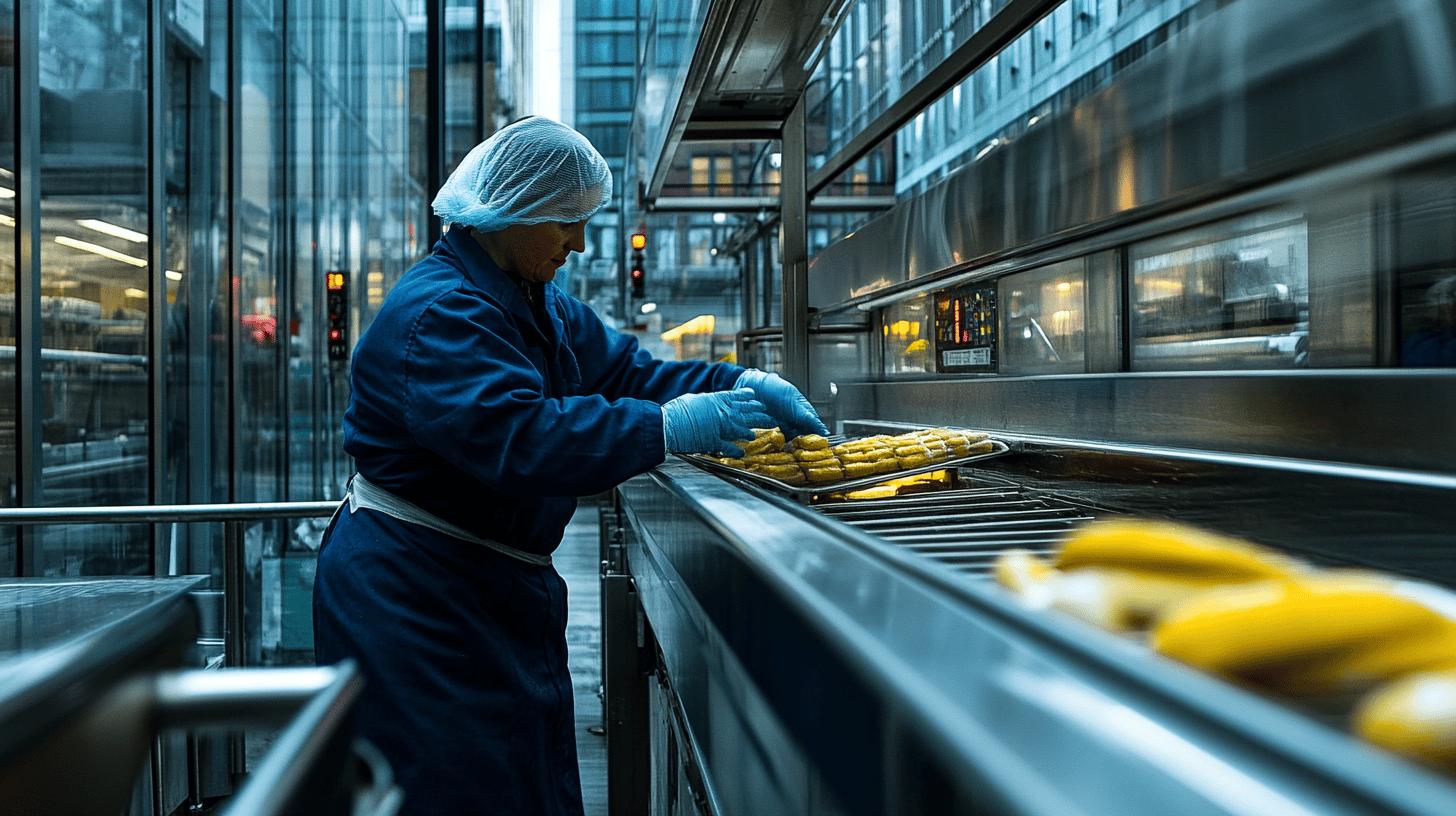
User Training Boosts Product Safety in Food Manufacturing
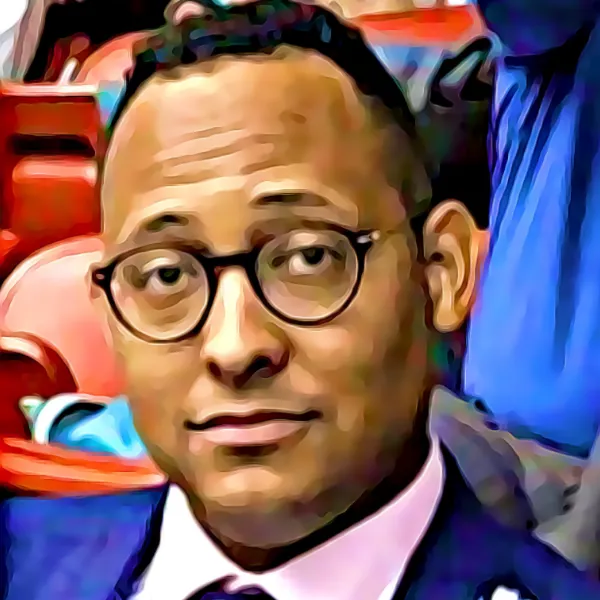
The Importance of User Training and Onboarding in Food Manufacturing for Safety and Quality Standards
User training and onboarding form the foundation of product safety and quality assurance in food manufacturing. Without robust employee education, businesses face increased contamination risks, regulatory non-compliance, and operational inefficiencies. Proper training ensures staff follow critical HACCP and GMP regulations – not just ticking boxes, but preventing lapses that could compromise consumer trust and product integrity.
Effective training bridges knowledge gaps, ensuring every team member understands food safety guidelines and quality control systems. From hygiene standards to cross-contamination prevention, these programmes equip employees with the tools to identify and address potential issues before they escalate, fostering a culture of accountability where everyone maintains high standards.
Q-Hub's digital transformation solutions can streamline these critical training processes, allowing food manufacturers to deliver consistent, traceable training that supports operational excellence and regulatory compliance. By digitising onboarding and training workflows, organisations can reduce errors and improve overall safety outcomes.
Building the Foundations of Food Safety Excellence
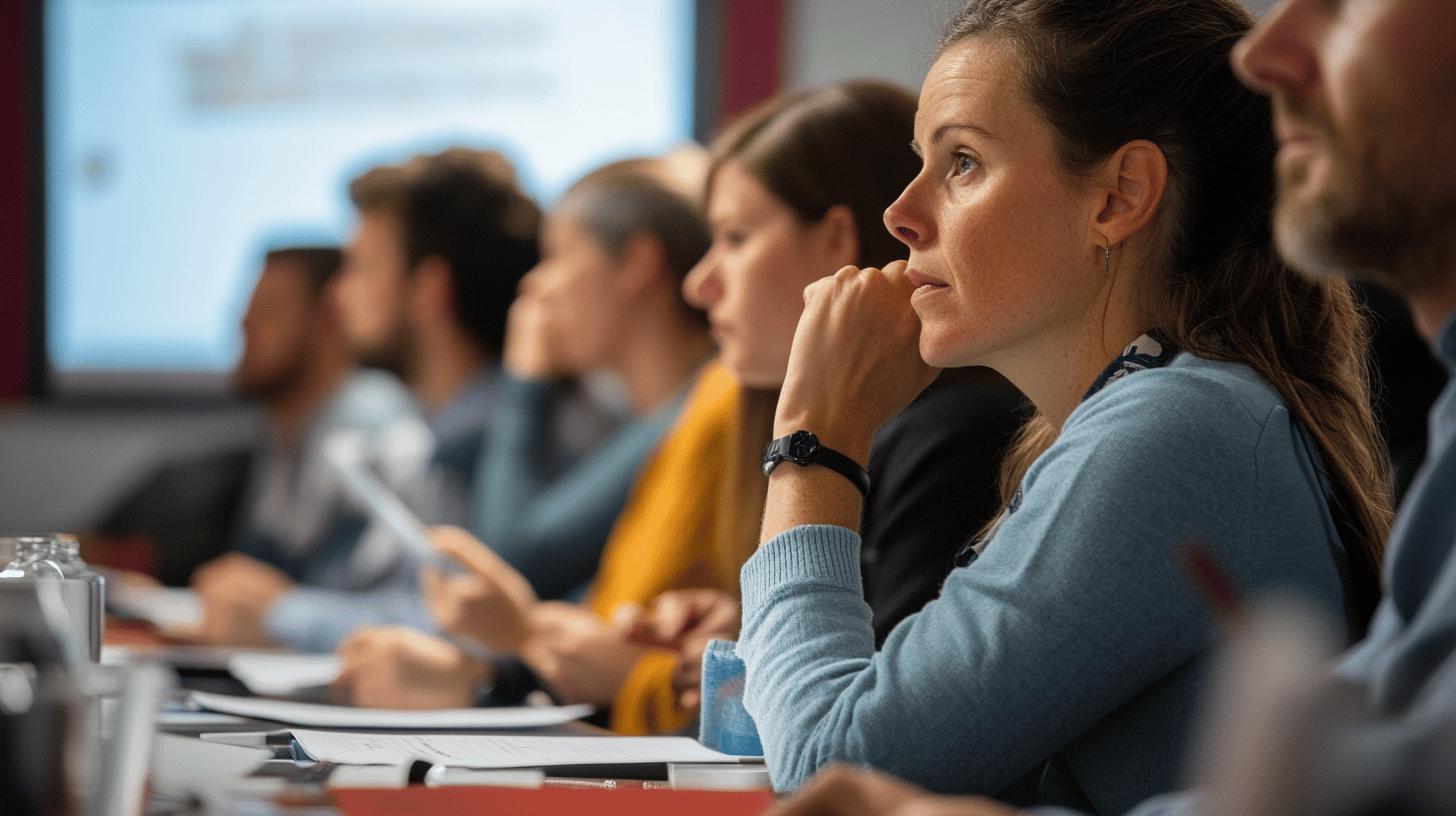
Creating structured safety training is essential for maintaining robust food safety protocols. Without comprehensive onboarding, knowledge gaps lead to contamination risks and regulatory breaches. Effective training evolves continuously with new safety standards and operational challenges.
Key safety topics that must be covered include personal hygiene practices, cross-contamination prevention strategies, safe food storage procedures, allergen management protocols, cleaning practices, and emergency response procedures. These fundamentals establish a strong safety foundation.
When we implemented Q-Hub's digital training tracking system, we saw a 47% improvement in training completion rates and significantly faster onboarding for new staff. This directly translated to fewer quality incidents in production.Source: Scottish Leather Group case study.
Interactive training materials such as quizzes, videos, and simulations foster employee engagement and improve knowledge retention. Continual learning programmes providing regular updates on food safety protocols ensure compliance over time, building a culture of accountability across the workforce.
Overcoming Onboarding Hurdles for Enhanced Quality Assurance
Structured onboarding embeds new employees into systems where they can perform safely and in compliance with Standard Operating Procedures (SOPs). Common challenges include time constraints, knowledge retention issues, unclear expectations, resource limitations, and resistance to change.
Companies implementing Q-Hub's solutions have transformed these challenges into opportunities. Digital platforms enable modular learning programmes that allow employees to progress in manageable stages. Tracking capabilities ensure critical information isn't overlooked, while digital workflows clarify expectations from day one.
The benefits extend far beyond initial training. Improved onboarding efficiency leads to better safety compliance, enhanced team cohesion, and reduced employee turnover. In food manufacturing, where precision is paramount, these improvements directly impact product quality and safety.
Digital Revolution in Food Safety Training
Technology is reshaping how food safety training is delivered, replacing static compliance programmes with dynamic, interactive methods. Q-Hub's digital solutions offer innovative tools that enhance engagement and improve outcomes in ways traditional training cannot match.
The following technologies are transforming training effectiveness in food manufacturing:
- Mobile-accessible platforms: Allow employees to access training modules anytime, improving flexibility and completion rates
- Real-time monitoring dashboards: Enable supervisors to track compliance instantly, ensuring critical steps aren't missed
- Digital workflow systems: Connect training directly to operational procedures, ensuring practical application
- Automated reminder systems: Prevent training and certification lapses before they impact compliance
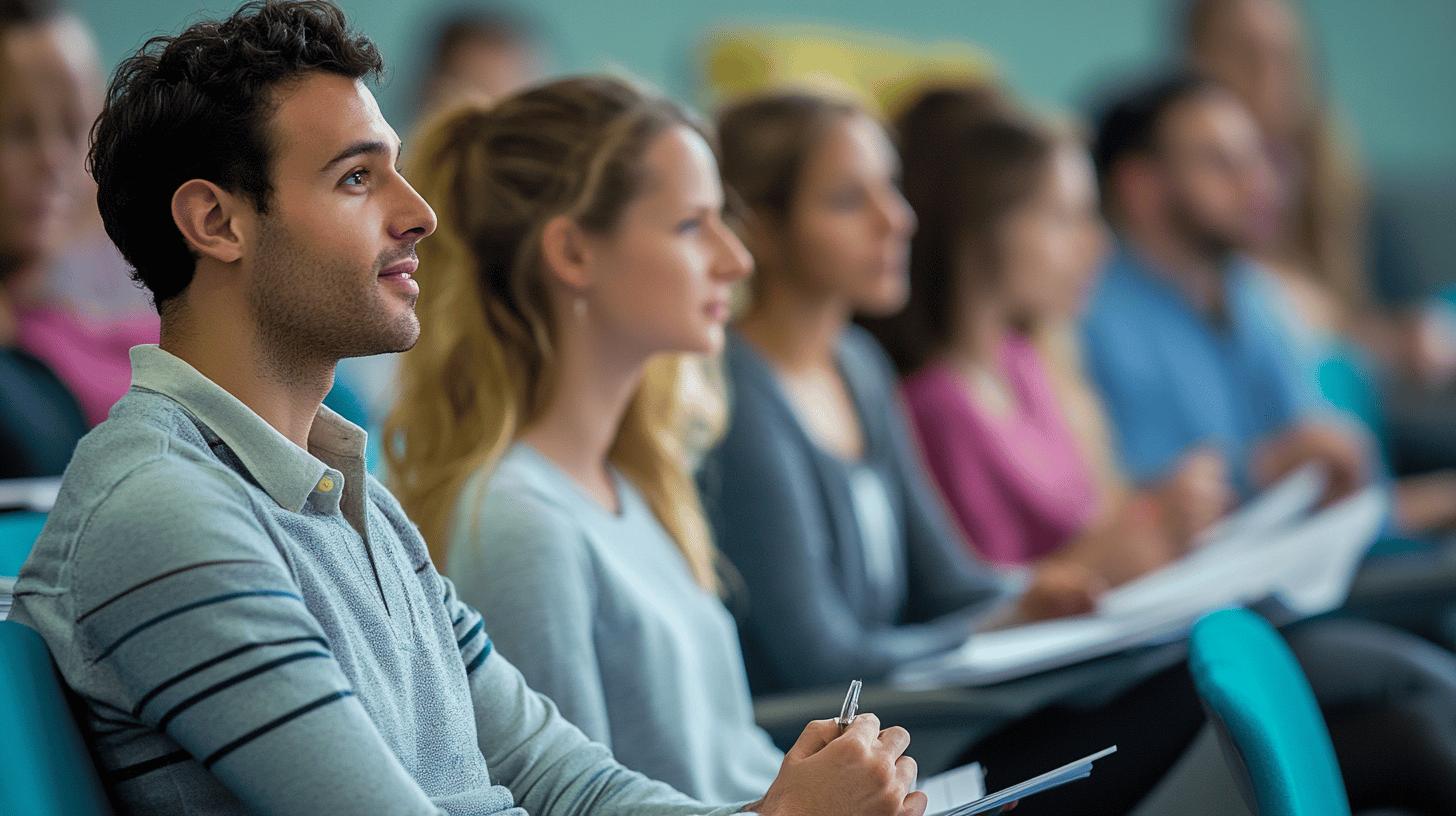
Companies like Fowlers of Bristol have experienced significant improvements after implementing Q-Hub's digital training solutions. By centralizing critical workflows, documentation, and training records, they've created a more cohesive approach to safety management that directly supports quality assurance goals.
Measuring Training Impact with Key Performance Indicators
Evaluating training effectiveness is essential for maintaining regulatory compliance and operational efficiency. Without clear measurement, food manufacturers risk safety breaches and quality inconsistencies. Digital solutions from Q-Hub provide real-time tracking of critical metrics, enabling continuous improvement.
Key performance indicators for training effectiveness include:
<table border="0"> <tr><th>Metric</th><th>Before Digital Training</th><th>After Q-Hub Implementation</th></tr> <tr><td>Training Completion Rate</td><td>72%</td><td>98%</td></tr> <tr><td>Compliance Documentation</td><td>Manual, paper-based</td><td>Automated, digital</td></tr> <tr><td>Audit Preparation Time</td><td>Days</td><td>Hours</td></tr> </table>Regular feedback and updates to training programmes are critical as food safety regulations evolve constantly. Q-Hub's digital platforms enable real-time adjustments to training content, ensuring employees remain aligned with the latest safety requirements. This continuous improvement cycle safeguards compliance while fostering a culture of proactive learning.
Navigating Complex Regulatory Requirements
Regulatory compliance forms the backbone of food manufacturing safety. User training and onboarding are fundamental in achieving this, as proper education prevents regulatory breaches that could lead to fines or production shutdowns. Key certifications like HACCP, GMP, ISO 22000, and BRC Global Standards require thorough staff training to maintain compliance.
Digital compliance solutions from Q-Hub provide food manufacturers with tools to track training completion, certification status, and regulatory updates in real-time. This visibility ensures no compliance gaps develop and provides auditable evidence of training completion – critical during regulatory inspections.
Regular updates to compliance training are non-negotiable in this highly regulated industry. Q-Hub's platforms ensure that whenever regulations from agencies like the FDA, USDA, or EFSA change, training can be quickly updated and distributed, with verification that all staff have reviewed and understood the new requirements.
Creating a Culture of Safety Excellence
Effective onboarding builds a safety culture that prioritises product integrity and operational excellence. This doesn't happen accidentally—it requires consistent training, clear communication, and shared commitment to reducing risks. When safety becomes embedded in company culture, quality improvements follow naturally.
Weston Aerospace demonstrated this principle by digitising their training and compliance processes with Q-Hub. Their approach to integrating safety protocols into onboarding created a workforce where safety awareness became second nature, resulting in measurable improvements in product quality and consistency.
Over time, systematic onboarding creates ripple effects throughout operations. Well-trained employees stay engaged and proactive, reducing turnover and improving compliance with safety protocols. This safety-first mindset protects the business and builds a workplace where every team member contributes to quality assurance and operational success.
Ready to transform your food safety training and compliance processes? Q-Hub offers comprehensive digital solutions that streamline onboarding, improve training effectiveness, and enhance regulatory compliance. Discover how our tailored software can help your organisation build a culture of safety excellence while reducing administrative burden.
Start using Q-Hub today
- Manage compliance in one place
- Streamline your teams and tasks
- Use Q-Hub free for 30 days