
Supplier and Contractor Management Boosts Food Compliance
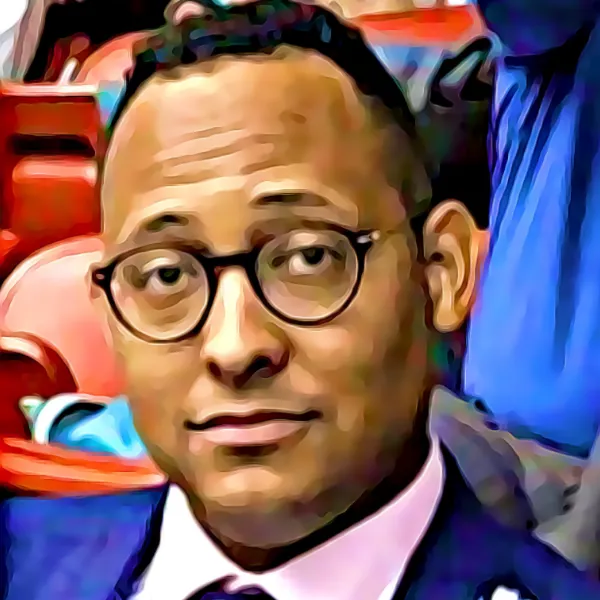

Supplier and Contractor Management Boosts Food Compliance
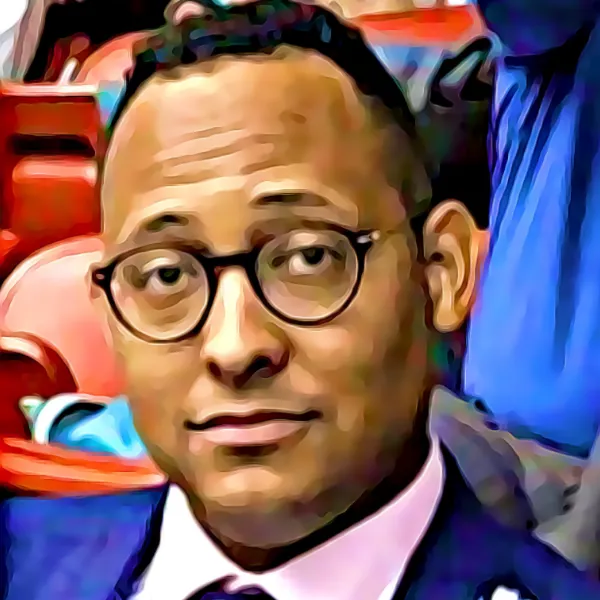
The Role of Supplier and Contractor Management in Guest Compliance for Food Operations
Effective supplier and contractor management is essential for ensuring guest compliance in food operations. supplier and contractor management plays a critical role in aligning suppliers with rigorous food safety standards, ensuring that every link in the supply chain is robust and reliable. This approach not only minimizes risks but also fosters collaboration and accountability across the board. By strategically overseeing external partners, businesses align their supply chain with food safety regulations, protecting both customer satisfaction and operational standards. This vendor oversight minimises non-compliance risks while upholding brand reputation. When external partners consistently meet required standards, the entire operation benefits through enhanced guest trust and streamlined workflows.
Q-Hub's digital solutions support this critical function by providing automated tools that enhance transparency and accountability throughout the supply chain. With structured strategies for managing external partnerships, food operations can ensure consistent quality delivery while creating a foundation for sustainable business relationships.
- Reduces food safety compliance risks
- Strengthens guest trust through consistent quality
- Streamlines operational workflows
- Promotes accountability across the supply chain
Essential Steps in Vetting Suppliers and Contractors for Food Operations
Thorough supplier and contractor vetting forms the cornerstone of compliance in food operations. This systematic assessment safeguards food quality, mitigates risks, and maintains operational integrity beyond merely ticking regulatory boxes. When done properly, it builds a robust foundation for long-term success in the competitive food industry.
Building a Digital Foundation for Partner Evaluation

The vetting process begins with certification reviews to confirm compliance with Food Standards Agency regulations. Regular supplier audits provide insights into adherence to agreed standards, while evaluation of past performance indicates reliability and consistency in meeting expectations.
Digital tools have transformed this evaluation process by enabling real-time updates and simplifying record-keeping. As demonstrated in the Scottish Leather Group case study, Q-Hub's centralised platform provides comprehensive visibility across multiple standards, significantly reducing audit preparation time while freeing resources for value-added activities.
We've transformed fragmented paper-based processes into streamlined digital workflows, giving our teams the tools and information needed to perform their roles effectively and maintain compliance standards. Source: Anglia Cathodic Protection Services
For food operations managing complex supplier networks, this level of transparency is invaluable, ensuring nothing falls through the cracks while maintaining consistent quality standards.
<table border="0"> <tr><th>Vetting Step</th><th>Traditional Process</th><th>Q-Hub Digital Process</th></tr> <tr><td>Certification Review</td><td>Manual verification and filing</td><td>Automated tracking with expiry alerts</td></tr> <tr><td>Supplier Audits</td><td>Paper-based checklists, delayed reporting</td><td>Digital forms with real-time reporting</td></tr> <tr><td>Performance Tracking</td><td>Spreadsheets with limited visibility</td><td>Centralised dashboards with KPI tracking</td></tr> </table>Strategies for Ongoing Compliance Monitoring in Supplier Management
Maintaining operational compliance hinges on effective ongoing monitoring of suppliers and contractors. This performance oversight is crucial to ensuring consistent adherence to food safety standards and guest service expectations. Without this vigilance, compliance risks can quickly escalate, jeopardising both guest trust and business reputation.
Transforming Manual Processes into Digital Workflows
Digital tools have revolutionised compliance monitoring by offering food operations real-time tracking and automated reporting capabilities. Similar to how Rocal Insulating Panels transformed their safety management system with Q-Hub, food businesses can implement automated alerts for upcoming audit deadlines and certification renewals.
Accountability frameworks assign clear responsibilities to external partners, compelling them to uphold food safety standards consistently. By digitising these processes, businesses can address non-compliance issues proactively, before they impact guest experience.
- Establish clear compliance standards and communicate them to all partners
- Conduct regular digital audits to identify and resolve potential risks
- Leverage Q-Hub's real-time tracking for automated compliance reporting
- Create accountability frameworks that ensure adherence to standards
Leveraging Technology for Supplier and Contractor Management
The integration of technology significantly enhances supplier and contractor management in food operations. By adopting digital transformation solutions like Q-Hub's contractor management platform, businesses ensure compliance across their supply chain through real-time updates, streamlined onboarding, and enhanced transparency.
Automation: The Key to Error-Free Compliance
Automation reduces human error by standardising workflows across supplier relationships. Real-time data enables managers to identify compliance gaps immediately, whether it's an expired certification or a delayed audit. For example, restaurant chains can centralise all supplier records, track deadlines, and automate alerts for upcoming renewals.
Weston Aerospace experienced similar benefits when implementing Q-Hub's platform, transforming their supplier management from a paper-based system to a comprehensive digital solution. Their compliance and quality teams were freed from resource-intensive tasks to focus on strategic initiatives.
- Automated alerts for critical certification deadlines
- Real-time performance reporting and tracking
- Centralised dashboards for comprehensive record management
- Traceability systems integration for complete supply chain visibility
- Customisable compliance metrics tailored to operational needs

Building Strong Relationships with Suppliers for Long-Term Compliance
Trust and collaboration form the heart of effective supplier management that facilitates guest compliance in food operations. When suppliers and contractors feel valued and engaged, they're more likely to uphold food safety standards, significantly reducing non-compliance incidents.
Creating a Culture of Shared Responsibility
Joint training programmes and shared compliance goals strengthen external partnerships. By offering specialised training sessions, food businesses equip their partners with the knowledge to meet stringent food safety standards. For instance, workshops on updated Food Standards Agency regulations ensure alignment across the supply chain.
BMC Analysis found that implementing Q-Hub's digital platform created an environment of shared responsibility by making compliance processes transparent and accessible to all stakeholders. This collaborative approach transformed transactional supplier relationships into genuine partnerships focused on quality and safety.
Stakeholder engagement embeds external partners into the compliance process through regular meetings, feedback sessions, and joint audits. When suppliers participate in decision-making, they develop higher commitment to compliance objectives, creating a foundation for long-term partnerships that enhance operational efficiency.
Measuring Compliance Success in Food Operations
Metrics are the backbone of assessing supplier compliance success in food operations. Meaningful indicators like audit scores, guest feedback, and incident response times highlight how well external partners align with operational standards while contributing to guest satisfaction.
Turning Data into Actionable Insights
Digital dashboards have transformed compliance reporting for food businesses. These tools provide real-time insights into supplier performance, allowing operations to identify weaknesses before they become problems. For instance, a dashboard might highlight declining quality control measures from a key supplier, enabling swift corrective action.
Fowlers of Bristol experienced similar benefits when implementing Q-Hub's solution, gaining visibility into "Right First Time" performance metrics that empowered teams to take proactive steps in quality improvement. The centralised reporting eliminated manual tracking inefficiencies while making trends immediately apparent.
By combining these insights with actionable steps, food operations can drive continuous improvement in their supplier management processes. Q-Hub's customisable dashboards transform raw compliance data into clear roadmaps for achieving operational excellence and exceptional guest experiences.
Ready to transform your supplier and contractor management for enhanced guest compliance? supplier and contractor management is not just about adhering to regulatory norms—it is a strategic endeavor that empowers food operations to create seamless, transparent, and accountable supplier relationships. Imagine a scenario where every interaction with your suppliers is optimized with digital solutions, ensuring that quality and safety are never compromised, but rather continuously improved upon. Q-Hub offers tailored digital solutions that streamline your food operations while ensuring consistent quality and safety standards across your supply chain.
Start using Q-Hub today
- Manage compliance in one place
- Streamline your teams and tasks
- Use Q-Hub free for 30 days