
Integration with ERP Systems: Refining Facility Workflows
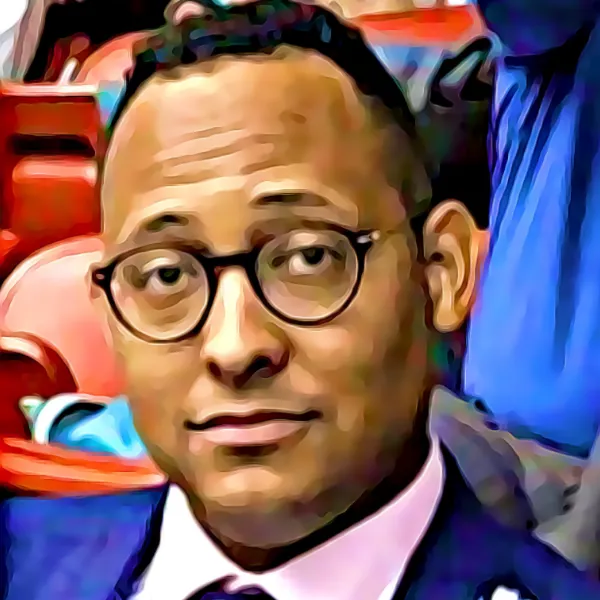

Integration with ERP Systems: Refining Facility Workflows
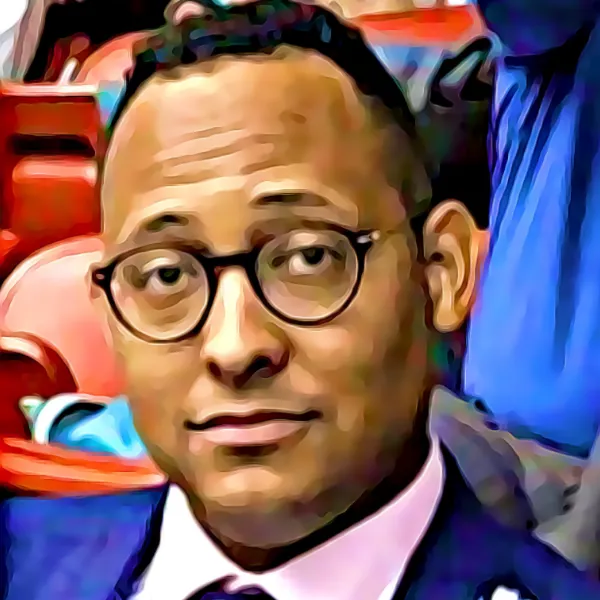
How Integration with ERP Systems Enhances Audit and Inspection Workflows in Facilities Management Supply Chains
Integrating ERP systems into facilities management supply chains is transforming audit and inspection workflows through centralised data management and enhanced efficiency. By eliminating fragmented systems prone to manual errors, organisations create seamless coordination across operations. Q-Hub's specialised software solutions bridge these operational gaps, enabling facilities management teams to achieve greater compliance and operational excellence through digital transformation.
Real-time data updates ensure inspection teams work with current information, automatically incorporating up-to-date compliance requirements when scheduling audits. Centralised storage creates robust audit trails while improving transparency.
By integrating data management solutions within your ERP framework, teams can enhance the visibility and reliability of critical operational data. This integration acts like a digital backbone that not only supports efficient audit workflows but also paves the way for innovative analytics, ensuring that every audit is supported by trusted data streams.
Meanwhile, automation handles routine administrative tasks like compiling reports and scheduling follow-ups, allowing teams to focus on strategic priorities.The Transformative Impact of Unified Data Systems

When facilities management teams implement integrated ERP solutions, the impact extends beyond simple efficiency gains. The centralisation of data creates a single source of truth that transforms decision-making processes. Rather than piecing together information from disparate sources, managers can access comprehensive insights instantly.
This unified approach means that audit findings can be immediately connected to corrective actions, with automatic notifications ensuring nothing falls through the cracks. For facilities managing multiple sites or complex supply chains, this visibility becomes a crucial competitive advantage.
When we implemented Qhub's digital platform, document control transformed from a administrative burden to a strategic asset. We eliminated hours of wasted time and improved overall compliance.
Companies embracing these innovations typically experience the following benefits:
- Documentation accuracy improvements through centralised management
- 25-30% reduction in compliance-related administrative work
- Enhanced inspection scheduling with automated workflows
- Stronger audit trails for regulatory compliance

Critical ERP Features Solving Longstanding Audit Challenges
Modern ERP platforms provide several game-changing capabilities that address persistent challenges in facilities management. Real-time monitoring and analytics allow discrepancies to be spotted and addressed almost immediately. For example, when an inspection reveals regulatory non-compliance, the system flags it and suggests corrective actions based on historical data.
Customised reporting tools further streamline compliance across diverse regulatory landscapes. Rather than creating separate reports for different standards, these systems can automatically format and deliver documentation that meets specific requirements like ISO 9001 or environmental regulations.
Automated scheduling represents another crucial advancement, eliminating overlaps and ensuring timely audits.
Implementing custom automation tools further refines these processes by streamlining repetitive tasks and reducing manual errors. Much like a well-tuned engine, these tools synchronize various moving parts of ERP systems to deliver consistent and error-free operations, ensuring that the automated workflow consistently supports superior operational performance in facilities management.
Combined with centralised data storage, these features create a comprehensive solution for traceability and compliance management. <table border="0"> <tr><th>ERP Feature</th><th>Challenge Addressed</th><th>Business Impact</th></tr> <tr><td>Real-time analytics</td><td>Delayed identification of issues</td><td>60% faster problem resolution</td></tr> <tr><td>Automated scheduling</td><td>Missed or overlapping audits</td><td>Near-perfect compliance rates</td></tr> <tr><td>Centralised storage</td><td>Fragmented documentation</td><td>75% reduction in document retrieval time</td></tr> </table>Practical Implementation: From Legacy Systems to Digital Excellence
Successfully integrating ERP systems requires a structured approach. Start by defining clear business requirements based on your specific operational goals—whether reducing downtime, improving compliance, or enhancing resource allocation. Working closely with IT teams ensures effective data mapping and workflow design that aligns with strategic needs.
Selecting the right software is crucial, as not all ERP tools offer the same capabilities. Q-Hub's customisable QHSE solutions provide tailored approaches that address specific industry challenges while ensuring scalability. Comprehensive staff training follows, ensuring everyone understands how to use the new system effectively.
Regular performance monitoring through KPIs helps identify gaps and opportunities for improvement. Metrics like inspection accuracy and audit completion rates provide valuable insights into system effectiveness. Finally, continuous optimisation ensures the system evolves with your organisation's changing needs.
Real-World Transformation: Case Studies in Excellence
Anglia Cathodic Protection Services demonstrates how effective ERP integration transforms operations. Before implementing Q-Hub, they relied on paper and spreadsheet-based systems that couldn't keep pace with their growing workload. The fragmented approach hindered effective compliance management across multiple sites.
After digitising these processes with Q-Hub, they eliminated bottlenecks and enhanced operational visibility. The centralised platform streamlined non-conformance tracking and audit management, saving hours of administrative work while improving compliance oversight. This transformation fostered greater accountability across teams and ensured everyone had access to the information needed to perform effectively.
Similarly, Weston Aerospace faced challenges managing quality and compliance across departments using outdated systems. Legacy processes failed to deliver actionable data when needed, creating significant operational bottlenecks. After implementing Q-Hub, they streamlined compliance management through automated audit scheduling and reporting. The Process Hub digitised critical workflows like NCR management, while comprehensive dashboards provided instant visibility into resolution progress.
Navigating Integration Challenges for Long-Term Success
Despite clear benefits, ERP integration comes with challenges. Data migration issues, resistance to change, and mismatched software capabilities can create significant barriers. During migration, organisations may encounter compatibility problems between legacy systems and modern platforms, potentially leading to data loss or duplication.
Addressing these challenges requires a strategic approach. Phased implementation breaks the process into manageable stages, allowing teams to test and refine the integration before scaling up. Comprehensive training programmes help overcome resistance by ensuring employees understand the benefits and feel confident using the new system.
Regular process reviews ensure continuing alignment with operational needs, while stakeholder involvement at every stage increases buy-in and reduces the risk of critical oversights. Q-Hub's approach to implementation emphasizes collaboration, ensuring systems are practical, functional, and aligned with organisational goals.
What's Next? The Evolution of Integrated Audit Solutions
The future of ERP integration in facilities management is being shaped by transformative technologies. Predictive analytics, IoT, and AI-driven insights are redefining what's possible in audit and inspection workflows. Predictive maintenance capabilities enable real-time monitoring of equipment and infrastructure, shifting from reactive to proactive management approaches.
AI represents another significant advancement, with machine learning algorithms analysing historical data to identify patterns, flag potential risks, and suggest optimisations. For audit workflows, this means predicting compliance issues before they escalate, allowing proactive intervention.
Q-Hub continues to innovate in this space, developing solutions that incorporate these advanced capabilities while maintaining intuitive interfaces and seamless scalability. This ensures that as organisations grow or regulations change, their systems can adapt without requiring extensive overhauls.
Ready to transform your audit and inspection workflows with Q-Hub's innovative digital solutions? Discover how our tailored software can streamline your compliance processes, reduce operational costs, and support long-term business growth through strategic digital transformation.
Start using Q-Hub today
- Manage compliance in one place
- Streamline your teams and tasks
- Use Q-Hub free for 30 days