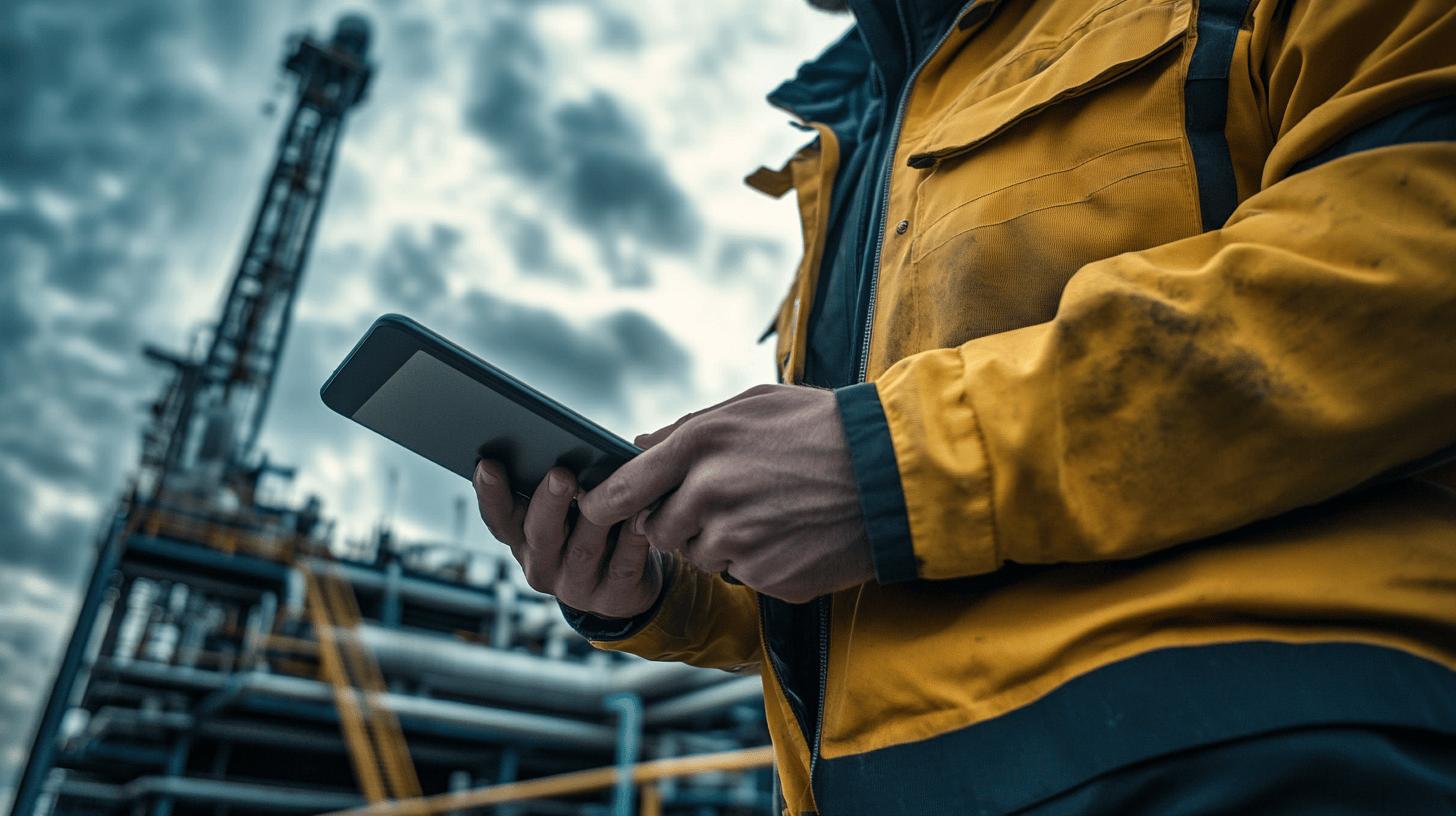
Integration with ERP Systems Boosts Oil and Gas Compliance
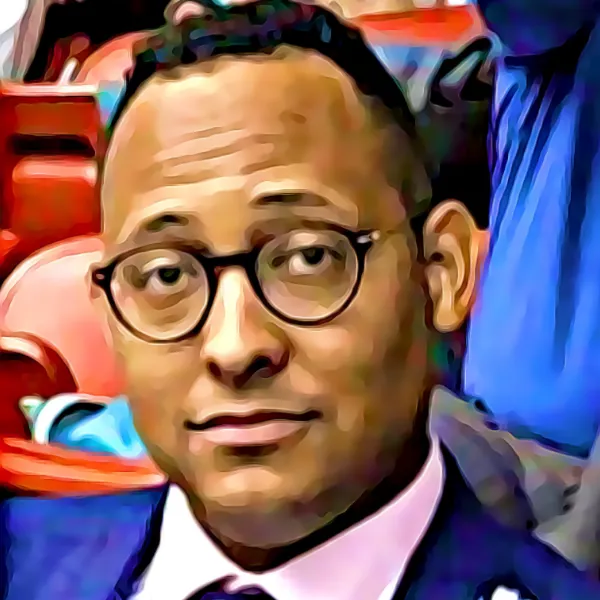
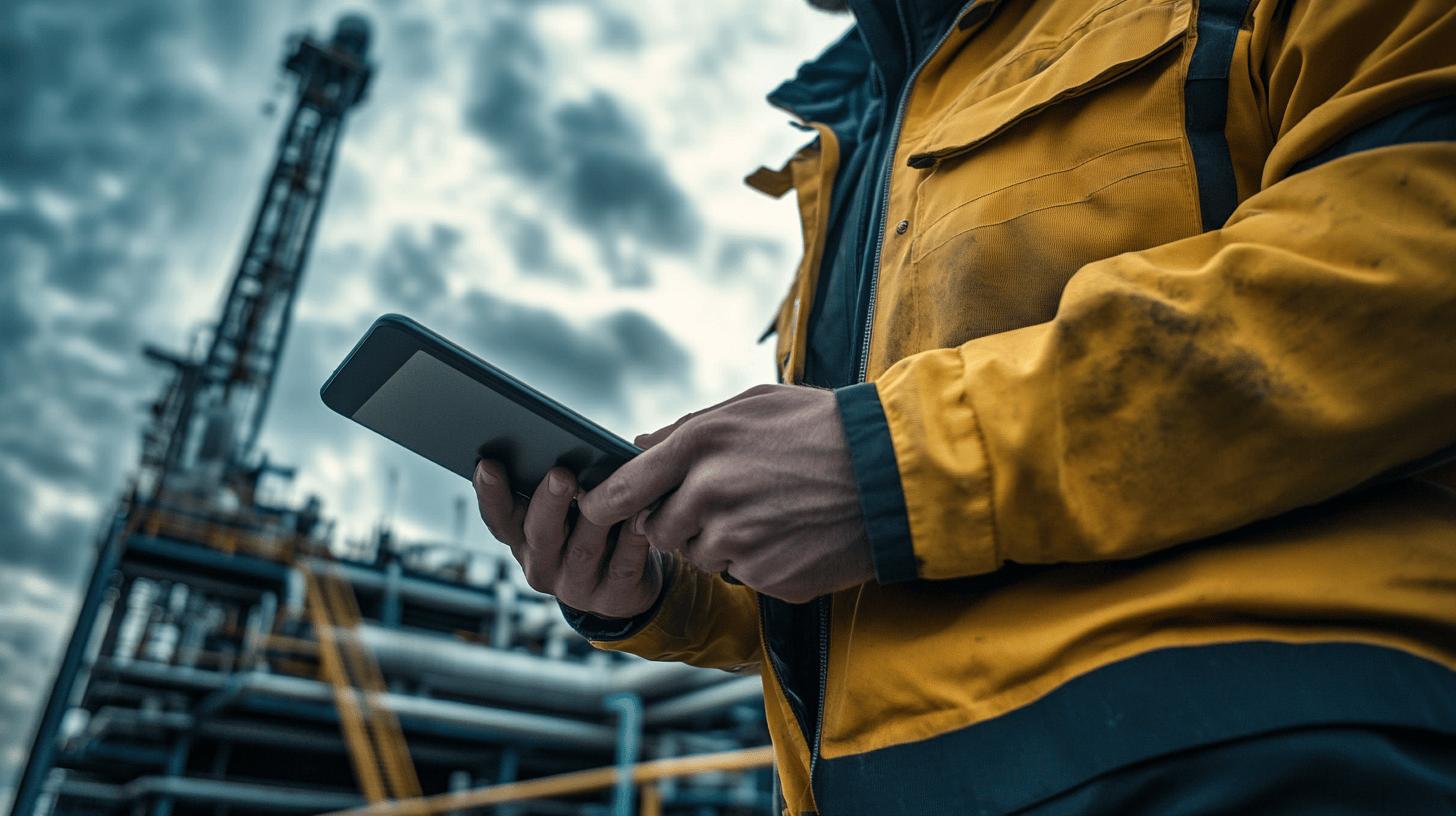
Integration with ERP Systems Boosts Oil and Gas Compliance
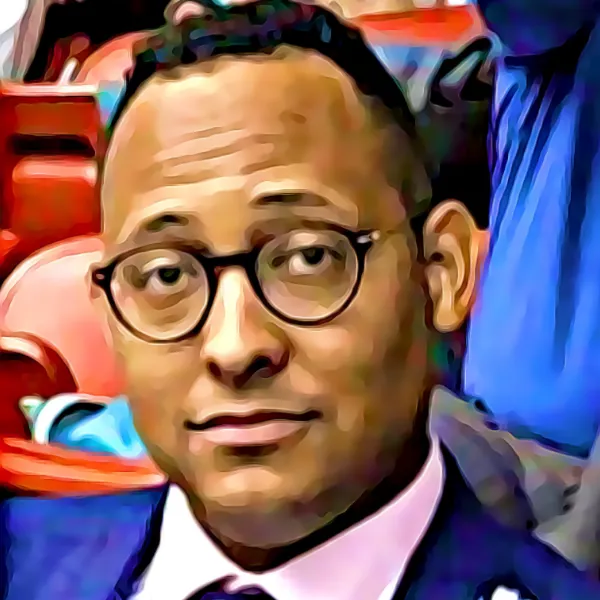
How ERP Integration Enhances Guest Management in Oil and Gas Supply Chains
In the high-stakes oil and gas industry, integrating ERP systems transforms how companies manage visitors and maintain compliance. Q-Hub's digital solutions centralise guest management processes, eliminating fragmented systems that often plague operational efficiency. By creating a unified platform, companies gain real-time visibility into visitor movements while automating safety protocols—critical in environments where risks are significant and compliance non-negotiable.
Guest management software embedded within ERP platforms replaces manual processes with streamlined digital workflows. This integration ensures only authorised personnel access sensitive areas, with real-time verification that reinforces site security. For oil and gas operations spanning multiple locations, this centralised approach provides consistent safety enforcement and comprehensive compliance monitoring.
From Fragmented Systems to Unified Control
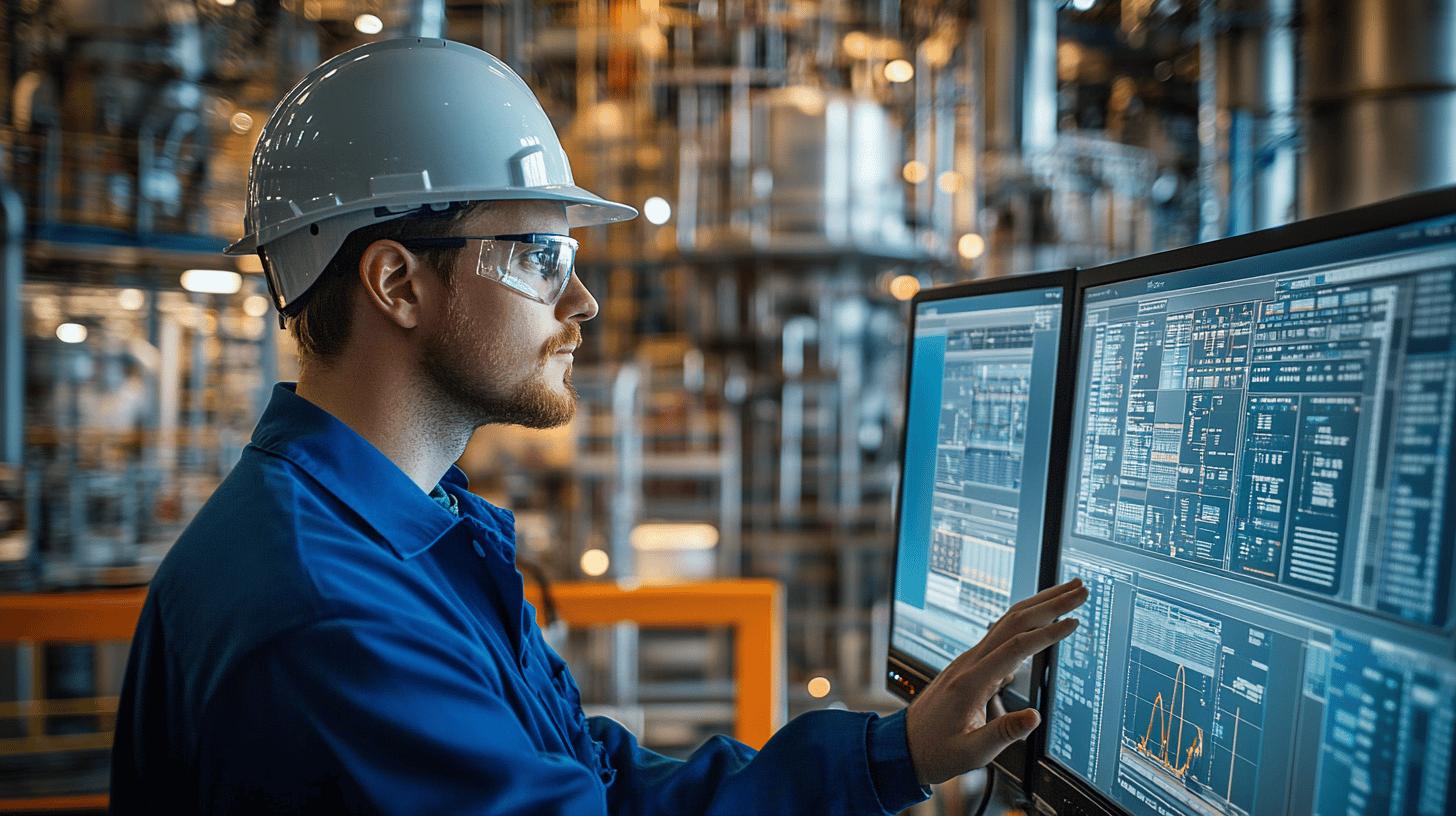
The traditional approach to guest management in oil and gas facilities often involves disconnected systems—paper logbooks at one site, standalone digital registration at another. This fragmentation creates significant compliance risks and operational blind spots.
When Scottish Leather Group implemented Q-Hub's integrated platform, they transformed their visitor management process across multiple sites. The system created a centralised hub for tracking contractors and visitors, eliminating the communication delays that previously plagued their operations.
The integration eliminated hours of administrative work while improving compliance visibility across all our facilities.
With centralised ERP integration, companies gain comprehensive oversight of all personnel on-site—whether employees, contractors, or visitors—ensuring safety protocols are consistently applied and documented.
The benefits of integrated guest management extend beyond basic tracking:
- Automated pre-arrival safety briefings for visitors
- Real-time visibility of all personnel across multiple sites
- Integrated emergency response capabilities
- Streamlined compliance documentation
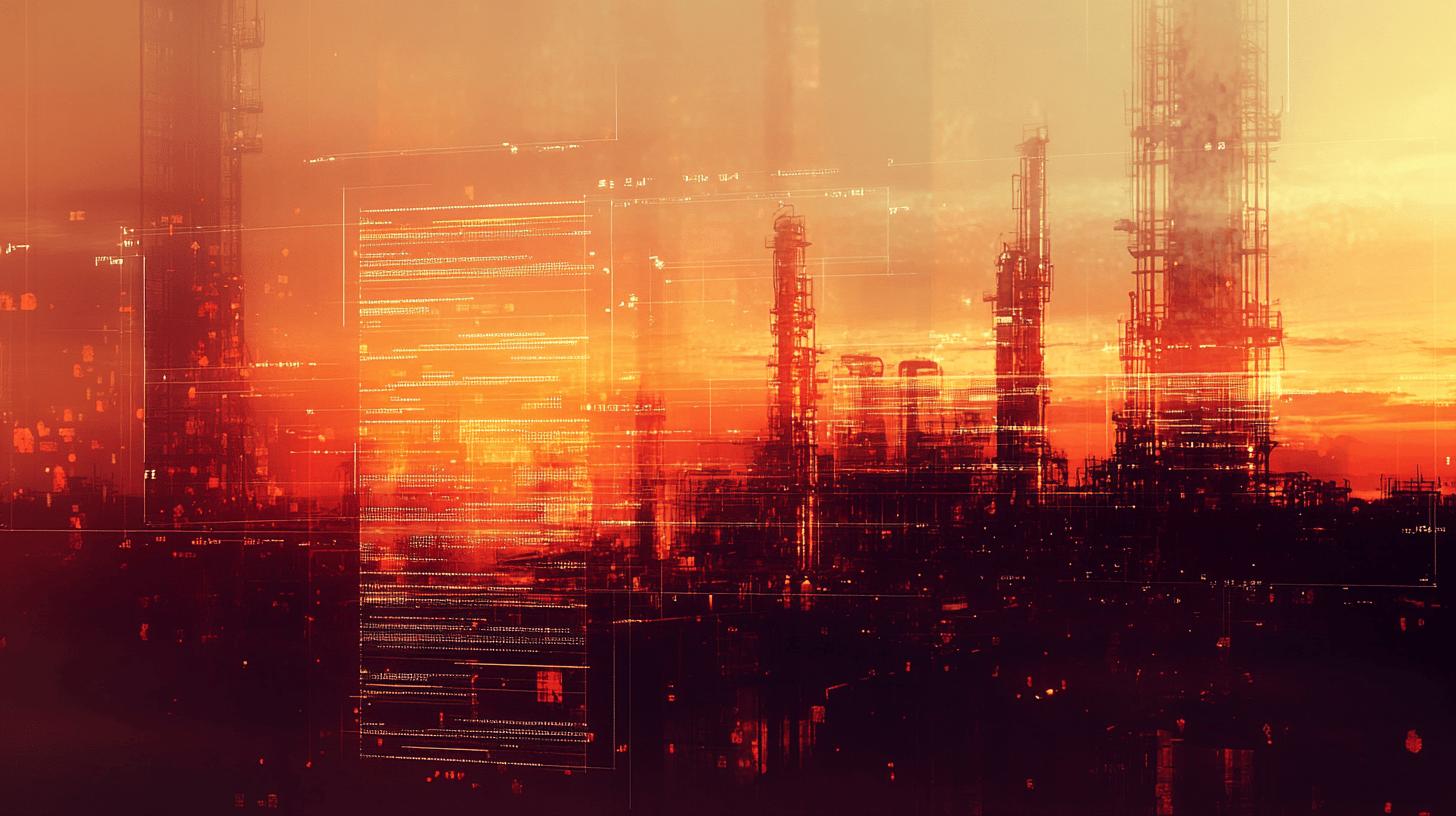
Streamlining Compliance Workflows Through ERP Integration
In oil and gas operations, compliance isn't optional—it's essential for operational continuity and safety. ERP integration revolutionises how companies manage regulatory requirements by replacing manual processes with automated workflows. This shift significantly reduces compliance risks whilst improving accuracy and consistency across operations.
When Weston Aerospace implemented Q-Hub's compliance solutions, they transformed fragmented processes into a cohesive system. The platform's Audit Hub became central to their regulatory strategy, offering automated scheduling, reporting, and real-time dashboards that dramatically reduced preparation time for audits.
Turning Data into Compliance Intelligence
ERP systems deliver critical compliance tools that address the complex regulatory demands of the oil and gas sector. Automated audit trails document every action, creating verifiable records that withstand regulatory scrutiny. Meanwhile, real-time monitoring identifies potential compliance issues before they escalate into major violations.
For companies managing safety KPIs across multiple sites, ERP integration eliminates the common problem of fragmented reporting. By consolidating compliance data, systems like Q-Hub ensure timely submissions to regulators while minimising operational risks.
Anglia Cathodic Protection Services experienced this transformation firsthand. Before implementing Q-Hub, tracking non-conformances was challenging, with resolutions often delayed due to their paper-based system. Q-Hub's Process Hub provided a centralised platform for managing NCRs, linking them to audits, and ensuring accountability at every step.
<table border="0"> <tr><th>Compliance Process</th><th>Before Integration</th><th>After Integration</th></tr> <tr><td>Audit Preparation</td><td>Days of manual work</td><td>Hours with automated tools</td></tr> <tr><td>NCR Resolution</td><td>Weeks with paper tracking</td><td>Days with digital workflows</td></tr> <tr><td>Compliance Reporting</td><td>Manual compilation</td><td>Automated generation</td></tr> </table>Key Benefits of ERP Integration in Oil and Gas Supply Chains
Integration with ERP systems has revolutionised oil and gas operations by creating unprecedented visibility and control. Q-Hub's solutions consolidate fragmented data into unified platforms, eliminating information silos that hinder effective decision-making. This interconnectedness enables teams to collaborate seamlessly, with critical information flowing across departments in real-time.
Breaking Down Operational Silos
When Rocal Insulating Panels implemented Q-Hub's solutions, they eliminated their cluttered document management system that previously caused significant delays. The centralised digital library provided version tracking and instant access to critical records, saving countless hours previously spent searching for information.
Workflow automation represents another crucial advantage of ERP integration. Tasks that once consumed hours of manual effort—from visitor processing to compliance reporting—now occur automatically, freeing resources for strategic activities. For example, automated alerts can notify teams of potential compliance issues, allowing them to address problems before they escalate.
The benefits translate directly to measurable cost savings. Companies implementing integrated ERP solutions typically report operational cost reductions of up to 30%. These savings come from improved resource allocation, fewer delays, and more streamlined processes that eliminate redundancy.
- Enhanced visibility across all operational areas
- Significant reduction in administrative overhead
- Faster response to potential compliance issues
- Improved collaboration across departments
Overcoming Integration Challenges in Oil and Gas ERP Systems
Implementing ERP systems in oil and gas operations presents unique challenges. Many companies struggle with fragmented data silos, outdated legacy systems, and insufficient integration expertise. These barriers are particularly significant in an industry with fluctuating market conditions and complex regulatory requirements.
Building Bridges Between Systems and Teams
Successful integration requires tailoring ERP systems to the specific operational demands of oil and gas enterprises. When BMC Analysis implemented Q-Hub's digital platform, they transformed their manual NCR management process from Word documents and fragmented email communications into a centralised, automated workflow.
A strategic approach to implementation is essential. This includes customising platforms to address industry-specific requirements like safety compliance and real-time asset management. Fowlers of Bristol experienced this transformation when they implemented Q-Hub to revolutionise their document control processes, ensuring every team had access to the latest information.
Companies addressing these challenges should focus on:
- Conducting thorough operational needs assessments
- Selecting platforms with industry-specific capabilities
- Providing comprehensive training for all system users
- Partnering with integration specialists familiar with oil and gas operations
Best Practices for Integrating Guest Management and Compliance Workflows
Successful ERP implementation for guest management and compliance requires strategic alignment with operational objectives. Q-Hub's approach focuses on synchronising data flows across departments while automating critical workflows. This alignment ensures that systems deliver both operational efficiency and regulatory compliance, particularly important in high-risk environments like oil and gas facilities.
Creating Seamless Digital Workflows
Effective integration requires mapping how guest management intersects with compliance requirements. For example, when a visitor enters a facility, their credentials and safety training must be verified against current regulatory standards. Scottish Leather Group achieved this seamless integration using Q-Hub's platform, which connected their visitor management, compliance documentation, and safety training verification into a unified system.
Implementation is only the beginning—ongoing evaluation ensures systems continue to deliver value. Regular assessment helps identify inefficiencies and adaptation opportunities as operational needs evolve. This continuous improvement approach creates a feedback loop between operational teams and IT support, driving incremental enhancements that maintain system effectiveness.
- Aligning technology implementation with compliance objectives
- Creating automated workflows that connect visitor management with safety protocols
- Establishing cross-functional teams to oversee integration
- Conducting regular system audits and performance reviews
- Implementing continuous improvement processes
Future Trends in ERP Integration for Oil and Gas
The oil and gas industry is rapidly embracing digital transformation to enhance compliance and visitor management. Advanced ERP solutions like those from Q-Hub now integrate with cutting-edge technologies including IoT sensors and artificial intelligence, enabling real-time data collection from across operations. This technological convergence delivers immediate insights for faster, more accurate decision-making—whether tracking visitor movements or ensuring compliance with complex safety protocols.
The Rise of Predictive Compliance
Predictive analytics represents a significant advancement in ERP functionality. Rather than simply tracking compliance, next-generation systems forecast potential issues before they become problems. This shift from reactive to proactive management fundamentally changes how oil and gas companies approach operational safety and regulatory adherence.
Scalability and adaptability have become essential design principles for modern ERP systems. As regulatory requirements evolve and operational demands shift, platforms must adjust seamlessly. Automation in compliance workflows has transitioned from optional to essential, streamlining processes like visitor onboarding and compliance reporting while significantly reducing error risks.
Emerging Technology | Compliance Impact |
---|---|
AI-Powered Analytics | Identifies compliance patterns and predicts potential issues |
IoT Integration | Provides real-time safety monitoring across facilities |
Mobile Compliance Tools | Enables field-based verification and reporting |
As the oil and gas industry continues to evolve, integrated ERP systems will play an increasingly vital role in balancing operational efficiency with regulatory compliance. Q-Hub's comprehensive digital solutions help companies navigate this complex landscape, transforming fragmented processes into cohesive systems that support safety, compliance, and operational excellence. Ready to transform your guest management and compliance workflows? Q-Hub offers tailored solutions that drive measurable improvements across your entire operation.
Start using Q-Hub today
- Manage compliance in one place
- Streamline your teams and tasks
- Use Q-Hub free for 30 days