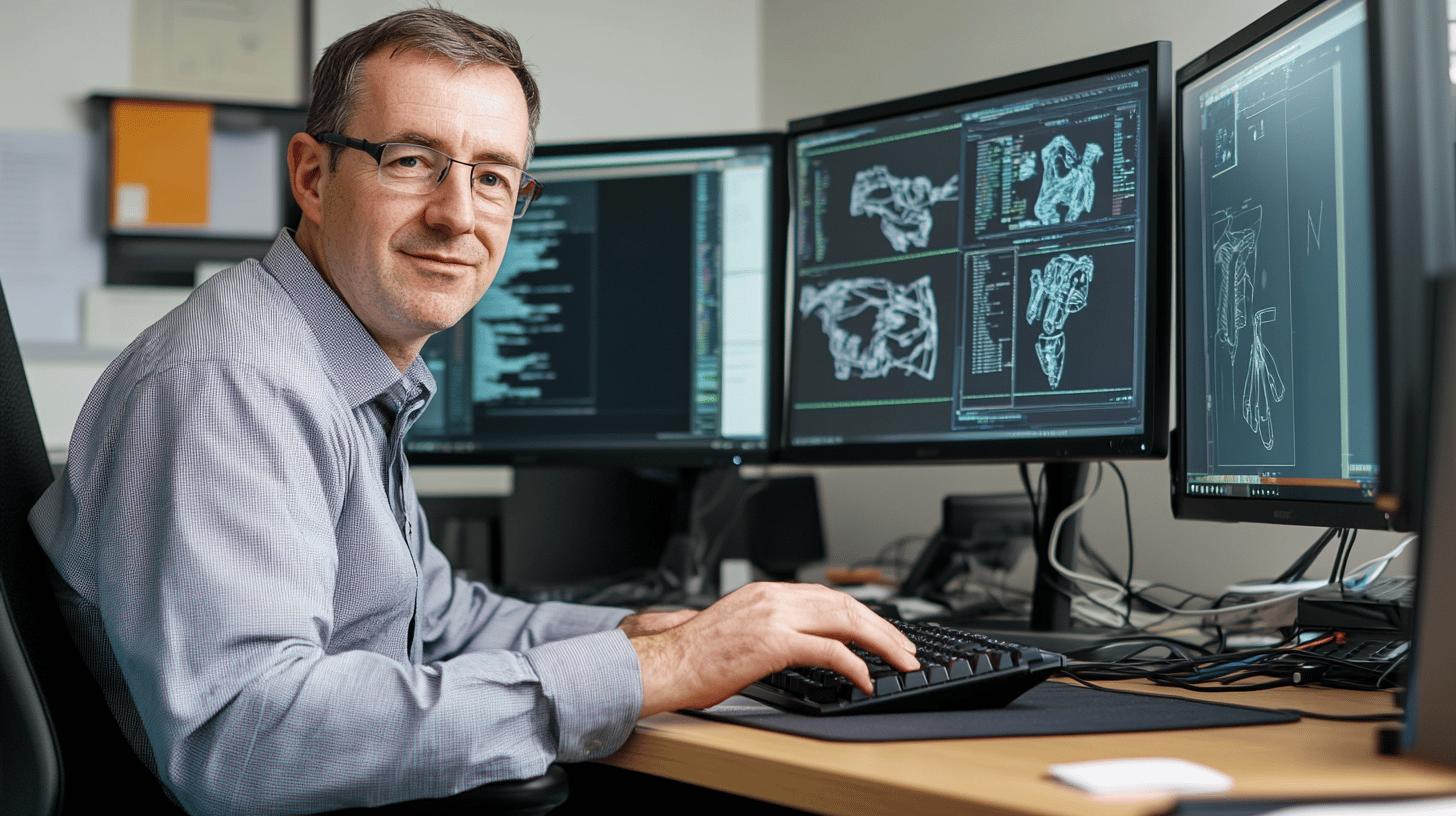
Custom Automation Tools Streamlining Engineering Training Tasks
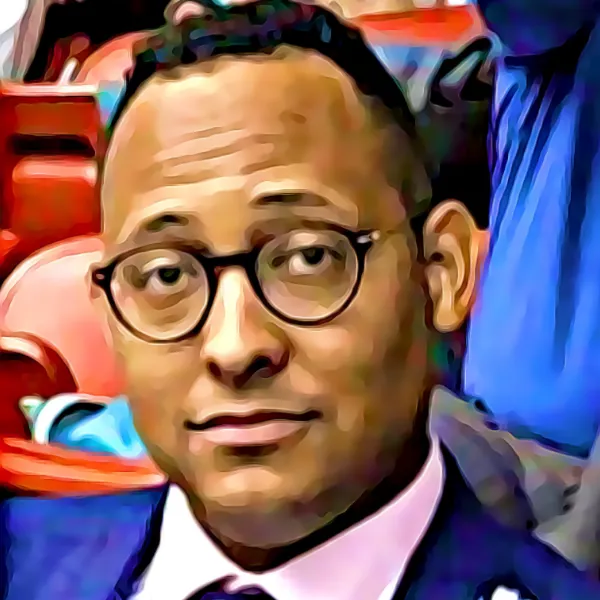
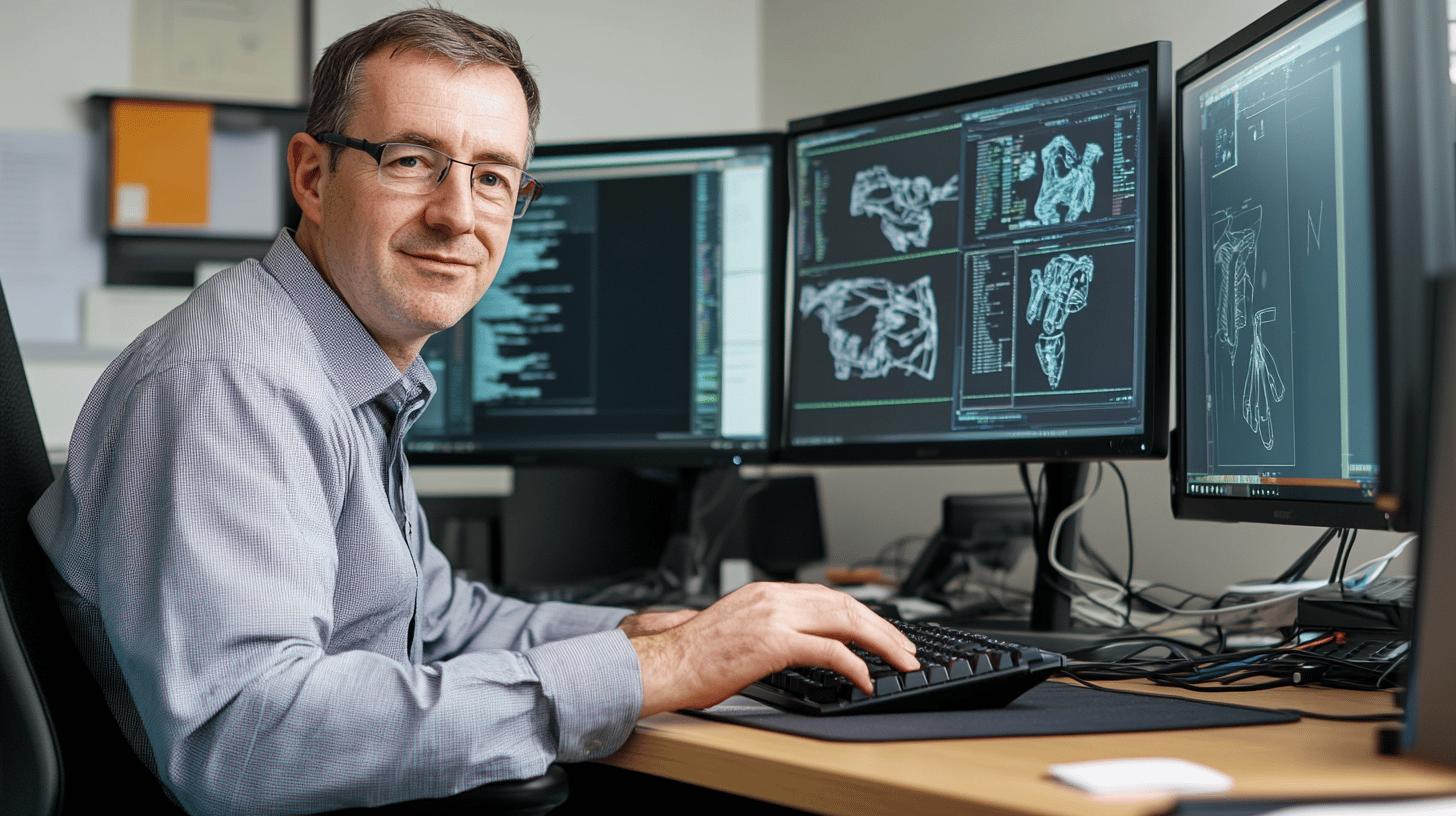
Custom Automation Tools Streamlining Engineering Training Tasks
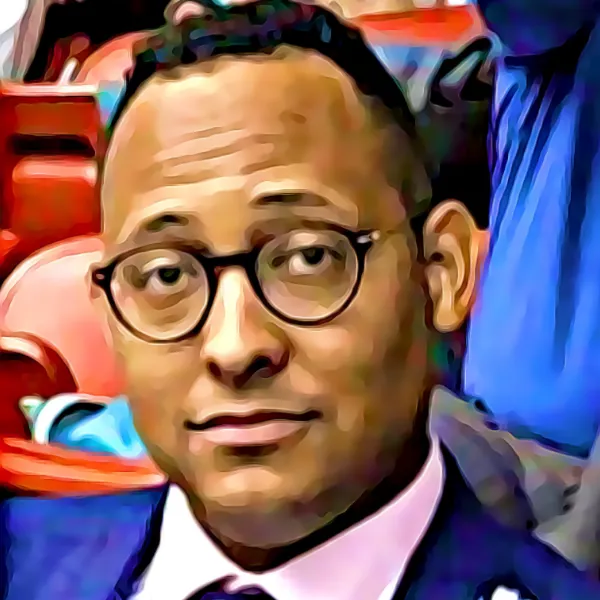
How Custom Automation Tools Enhance Training and Competence Management in Engineering
Custom automation tools for training and competence management in engineering have become essential for modern businesses seeking operational excellence. Q-Hub's specialised solutions transform how organisations handle workforce development by eliminating inefficiencies in traditional manual methods. These tailored platforms seamlessly integrate with existing engineering workflows, enabling businesses to maintain compliance, optimise processes, and significantly reduce administrative burden.
Engineering firms implementing custom automation tools report an average 40% improvement in training completion rates and 30% reduction in competency assessment time, demonstrating clear return on investment.
At their core, these tools feature customisable training modules aligned with industry standards like ISO 9001 and ISO 45001. This flexibility allows aerospace companies to focus on safety-critical operations while automotive firms might prioritise advanced manufacturing techniques—making them vastly more effective than generic solutions.
The real-time analytics capabilities provide instant visibility into training progress and competency gaps. This level of insight enables managers to make informed decisions quickly and allocate resources efficiently, particularly valuable before compliance audits or when onboarding new team members.
Moreover, effective user training and onboarding initiatives are central to maximising the benefits of automated systems, ensuring every new employee quickly understands how to leverage these sophisticated tools. This comprehensive approach not only reinforces compliance standards but also builds a more resilient, knowledgeable workforce ready to tackle complex engineering challenges.
Breaking Free from Manual Compliance Nightmares
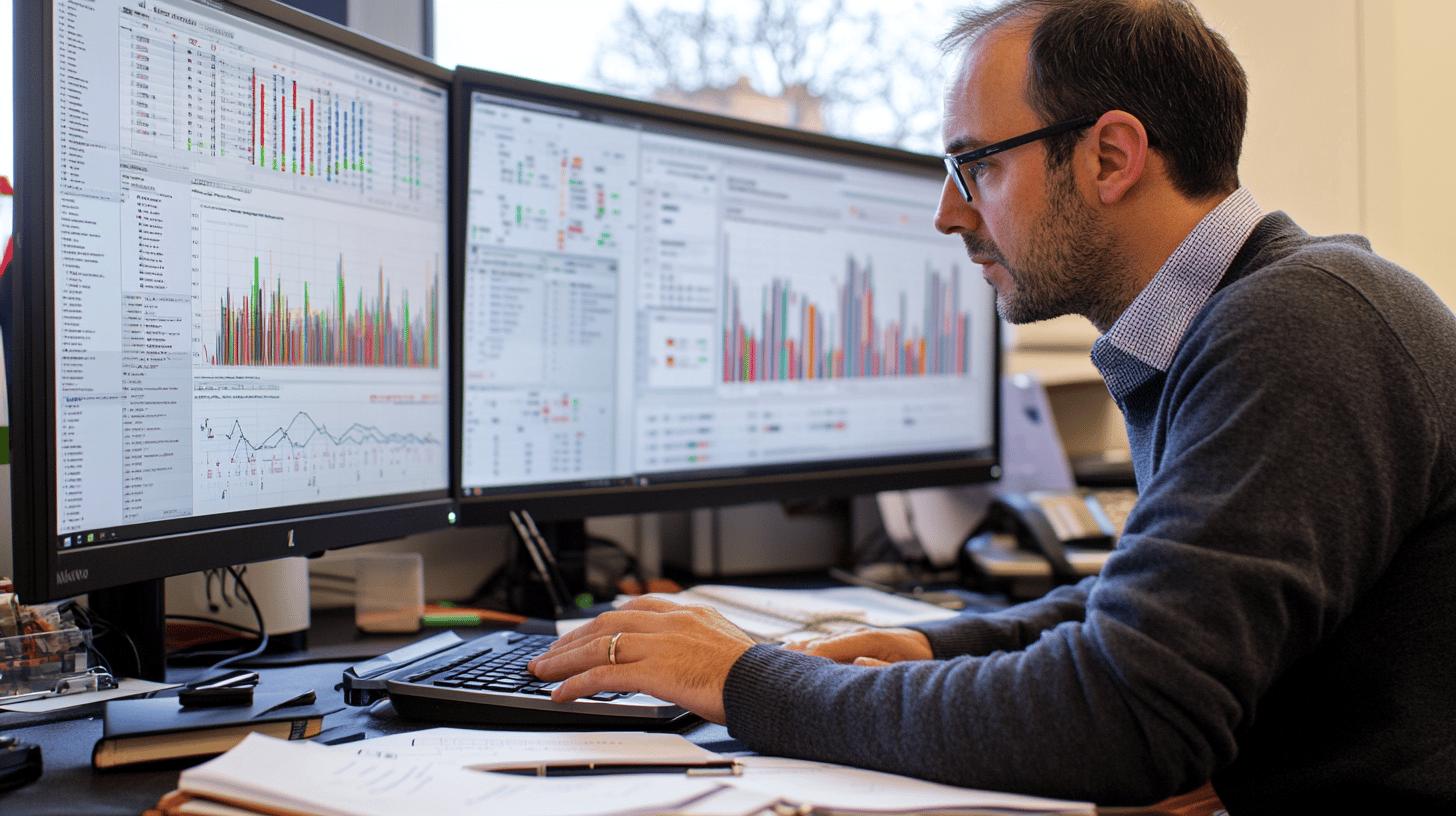
Engineering organisations face unique challenges that generic training solutions simply can't address. Multi-disciplinary teams with diverse skill requirements create complexity that quickly overwhelms manual tracking systems.
Consider the typical engineering compliance scenario: spreadsheets scattered across departments, paper certificates filed in multiple locations, and no single source of truth for training records. This fragmentation creates significant risk—outdated records might lead to untrained personnel operating critical machinery or missed compliance deadlines resulting in costly penalties.
Real-world impact is measurable. Weston Aerospace, before implementing a digital solution, struggled with legacy systems that failed to deliver actionable data when needed. Their quality and compliance teams were bogged down by repetitive manual tasks instead of focusing on strategic improvements.
The absence of automation means valuable engineering talent spends hours on administrative tasks:
- Manually updating training matrices
- Chasing training attendance records
- Preparing compliance documentation for audits
- Identifying and addressing competency gaps without reliable data
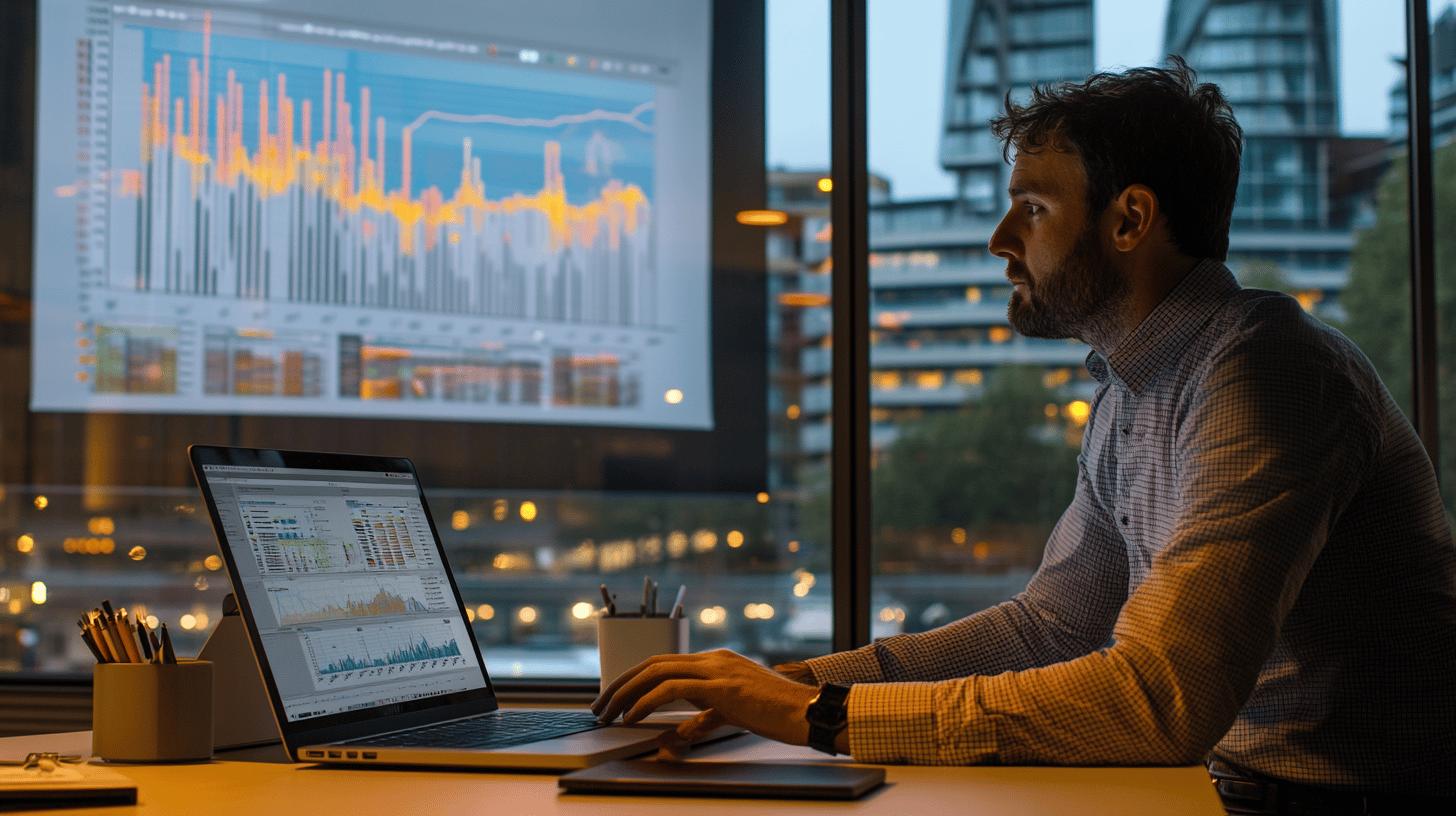
Transformative Features That Drive Real Results
Effective automation tools share key capabilities that address engineering-specific challenges. Q-Hub's solutions stand out by delivering comprehensive functionality designed specifically for complex operational environments.
Customisation is paramount—engineering firms require flexibility to align with their unique regulatory obligations and operational workflows. For instance, Scottish Leather Group implemented Q-Hub's Audit Hub to efficiently manage compliance across multiple ISO standards, including ISO 9001 for quality management and ISO 45001 for health and safety.
Integration capabilities ensure these tools work seamlessly with existing engineering systems.
By integrating with established ERP systems, engineering organisations can not only streamline their training processes but also centralise data management, making compliance tracking and corrective actions more efficient. This integration with ERP systems serves as a linchpin for connecting disparate datasets and operational workflows, ultimately enhancing the overall effectiveness of digital transformation in engineering. Fowlers of Bristol transformed their operations by bringing critical workflows, datasets and communications into a single digital space through Q-Hub's intuitive portal, enabling instant access to real-time data across engineering teams and compliance managers.
Companies embracing these innovations typically experience the following benefits:
- Automated compliance reporting that drastically reduces audit preparation time
- Centralised documentation with version control and digital approval workflows
- Real-time visibility into competency gaps through intuitive dashboards
- Streamlined processes for tracking incidents, non-conformances and corrective actions
From Paperwork Nightmare to Digital Excellence: Real Success Stories
The transformation achieved through custom automation tools is best illustrated through real engineering case studies. BMC Analysis, like many engineering firms, struggled with tracking non-conformances, managing document acknowledgment, and overseeing asset calibration through manual methods.
After implementing Q-Hub's Process Hub, they revolutionised their NCR management with automated tracking and reporting. Tasks that previously required extensive manual effort were automated with built-in alerts and due dates ensuring timely action. This reduced the administrative burden significantly while improving operational accuracy.
Similarly, Anglia Cathodic Protection Services faced challenges with paper and spreadsheet-based systems as their workload increased. By digitising their fragmented processes with Q-Hub, they eliminated bottlenecks and enhanced operational oversight. The platform's audit capabilities enabled real-time scheduling and reporting, saving hours of administrative work while improving compliance visibility.
The measurable results speak for themselves:
<table border="0"> <tr><th>Process</th><th>Before Automation</th><th>After Automation</th></tr> <tr><td>Training completion rates</td><td>60%</td><td>85-95%</td></tr> <tr><td>Audit preparation time</td><td>Days</td><td>Hours</td></tr> <tr><td>Compliance documentation access</td><td>Hours/days</td><td>Seconds</td></tr> </table>Smart Implementation: Setting Your Organisation Up for Success
Implementing custom automation tools effectively requires strategic planning and a clear roadmap. The first critical step is conducting a thorough needs assessment to identify your organisation's specific pain points and requirements.
Rocal Insulating Panels illustrates this approach perfectly. Their previous system for document management relied on a cluttered drive lacking structure, causing frequent delays in finding critical files. By first identifying this as a priority issue, they could focus their implementation on Q-Hub's document control capabilities, creating a centralised digital library with version tracking and instant access.
Customisation should reflect your organisation's unique workflows and terminology. When Scottish Leather Group implemented Q-Hub, they tailored the platform to address specific challenges across multiple ISO standards. This customisation extended to creating pre-built templates and automated schedules that aligned perfectly with their compliance requirements.
User adoption remains critical to success. The most sophisticated system will fail if employees don't embrace it. Start with comprehensive training sessions tailored to different user roles. Weston Aerospace's experience demonstrates that when properly introduced, these tools foster wide adoption and engagement across all organisational levels, from shop floor workers to management.
The Long-Term Value Proposition: Beyond Initial ROI
The financial case for custom automation tools is compelling when considering both immediate and long-term benefits. On average, engineering organisations report a 20% reduction in training-related expenses after implementation, primarily through decreased administrative burdens and fewer compliance-related errors.
However, the value extends far beyond direct cost savings. These tools enable significant productivity improvements by allowing engineers to focus on core duties rather than paperwork. As Fowlers of Bristol discovered, having centralised communication and data management fostered collaboration between teams and empowered them to focus on their "Zero Defects" quality initiative rather than administrative tasks.
Scalability represents another crucial advantage. As your organisation grows, these systems expand accordingly without proportional increases in administrative overhead. This adaptability ensures continued return on investment even as business needs evolve.
Most importantly, these tools significantly reduce compliance risks that could otherwise result in costly penalties, project delays, or reputation damage. By maintaining accurate, accessible records and automating compliance tracking, organisations gain both peace of mind and tangible protection against regulatory challenges.
As engineering organisations continue to navigate increasingly complex regulatory landscapes and competition for skilled talent, investing in custom automation tools from experts like Q-Hub represents not just an operational improvement but a strategic advantage for long-term success. By transforming training and competence management from administrative burdens into strategic assets, these solutions help engineering firms build more capable, compliant and competitive organisations.
Start using Q-Hub today
- Manage compliance in one place
- Streamline your teams and tasks
- Use Q-Hub free for 30 days