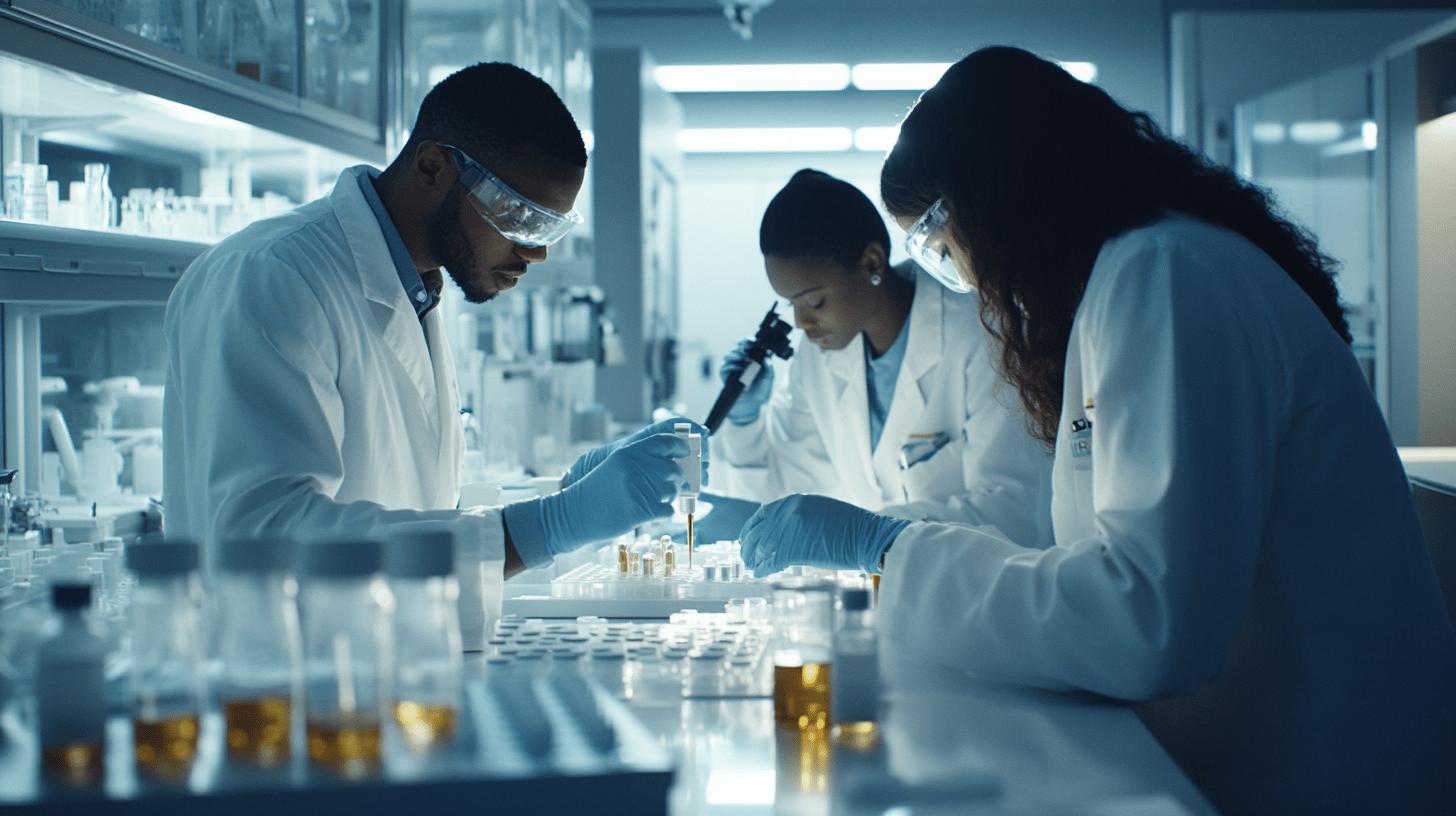
Enterprise Quality Control Solutions Elevate Pharma Standards
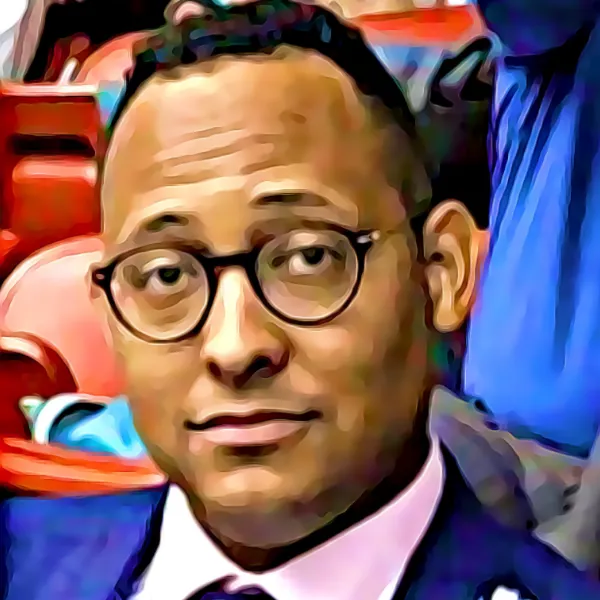
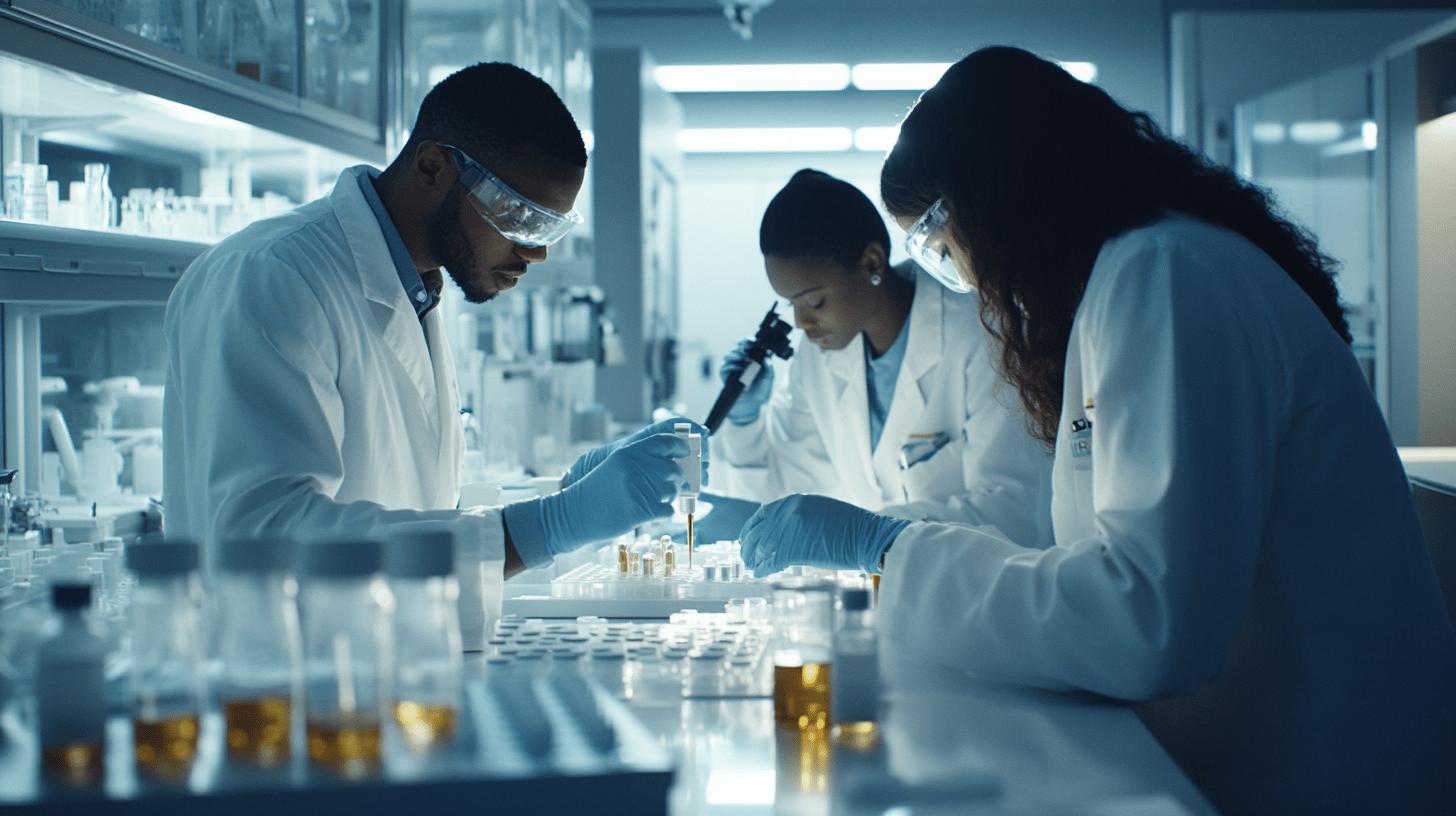
Enterprise Quality Control Solutions Elevate Pharma Standards
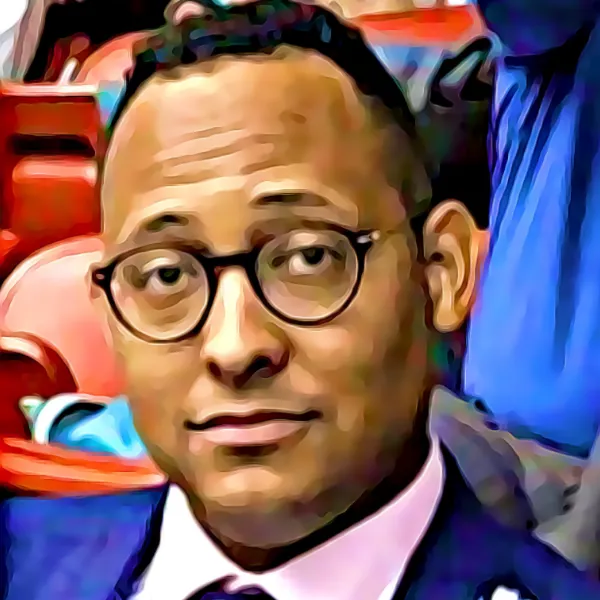
The Role of Enterprise Quality Control Solutions in Pharma Manufacturing
Enterprise quality control solutions play a crucial role in pharmaceutical manufacturing, where precision and consistency are non-negotiable. These advanced compliance platforms help manufacturers meet stringent regulatory requirements while maintaining product integrity. Without robust quality management systems, pharmaceutical companies risk costly compliance failures and product quality issues.
The pharmaceutical industry operates under intense regulatory scrutiny from bodies like the FDA and EMA. These authorities enforce strict standards such as FDA 21 CFR Part 11 and EU GMP Annex 11, which govern everything from electronic records to digital signatures. Enterprise solutions streamline compliance by automating document control and providing real-time monitoring capabilities.
When we implemented Qhub's digital quality management system, audit preparation time decreased by 70%, allowing our compliance team to focus on proactive improvements rather than reactive documentation.
Revolutionising Document Control in Regulated Environments
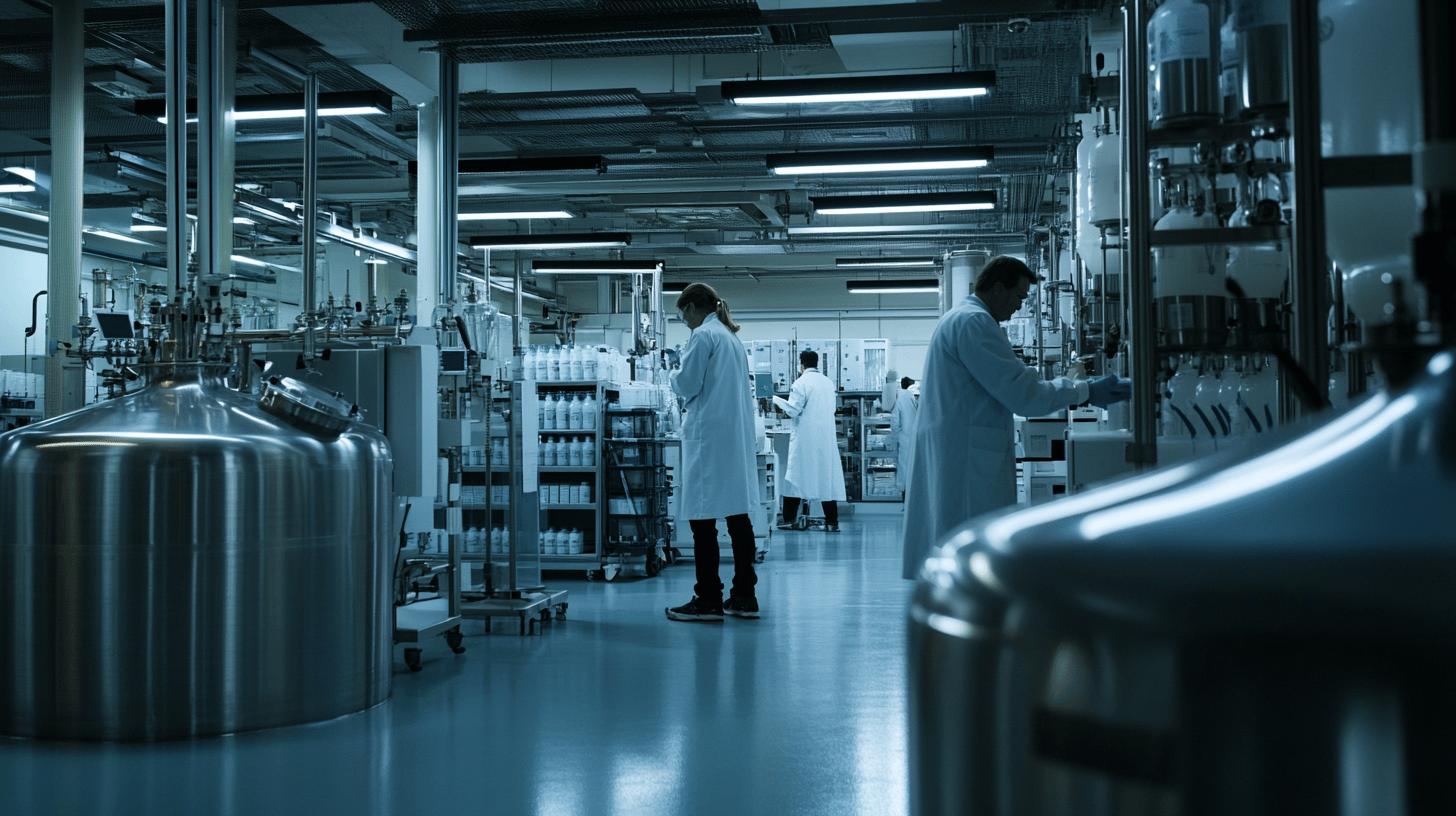
Manual document management in pharmaceutical manufacturing isn't just inefficient—it's risky. Traditional paper-based systems for handling SOPs create opportunities for human error and compliance gaps. Modern enterprise platforms automate version control, accessibility, and review reminders, significantly reducing these risks.
At Weston Aerospace, document control was a major bottleneck before implementing a digital solution. Staff struggled with outdated paper systems that couldn't keep pace with evolving regulations. After adopting Qhub's Doc Library, the company transformed its approach to document management, enabling real-time access and automated version control.
Beyond basic compliance, these systems enhance product quality by integrating seamlessly with quality assurance workflows. They track deviations and anomalies in real-time, enabling manufacturers to address issues before they escalate into serious problems that could trigger recalls or regulatory penalties.
From Reactive to Proactive: The Compliance Transformation
Traditional quality control relies on identifying and correcting problems after they occur. Modern enterprise solutions shift this paradigm by enabling preventative measures. By implementing automated monitoring and alert systems, pharmaceutical manufacturers can detect potential issues before they affect product quality.
Q-Hub's quality management software enables this transformation through intelligent workflow design. When Scottish Leather Group needed to manage compliance across multiple ISO standards, they turned to Q-Hub's Audit Hub to streamline their processes. The result was a significant reduction in administrative burden and improved audit readiness.
Have you ever wondered what happens when a pharmaceutical company faces a surprise regulatory inspection? With proper enterprise quality control systems, the answer is simple: they're prepared. These solutions maintain ongoing compliance rather than scrambling to gather documentation when inspectors arrive.
<table border="0"> <tr><th>Quality Process</th><th>Before Digital Quality Control</th><th>After Implementation</th></tr> <tr><td>Audit Preparation</td><td>Days of manual work</td><td>Hours with automated reporting</td></tr> <tr><td>NCR Resolution</td><td>Weeks with paper tracking</td><td>Days with digital workflows</td></tr> <tr><td>Document Updates</td><td>Manual distribution</td><td>Automated notifications</td></tr> </table>Achieving GMP Compliance Without the Headache
GMP compliance requires robust processes for document management, risk assessment, and validation. Enterprise quality control platforms simplify these requirements by automating critical workflows and eliminating human error. They ensure every step is traceable and repeatable—essential qualities for regulatory compliance.
One standout example is how BMC Analysis transformed their non-conformance reporting (NCR) process. Before implementing Q-Hub's Process Hub, they struggled with Word documents and fragmented email communications. After digitalisation, NCRs were resolved efficiently through automated tracking, notifications, and real-time KPI monitoring.
Let's look at five essential features that make these systems indispensable:
- Automated document control with version tracking
- Risk-based validation tools aligned with GAMP®5
- Data integrity assurance using ALCOA+ principles
- Real-time deviation monitoring and alerting
- Comprehensive compliance reporting capabilities
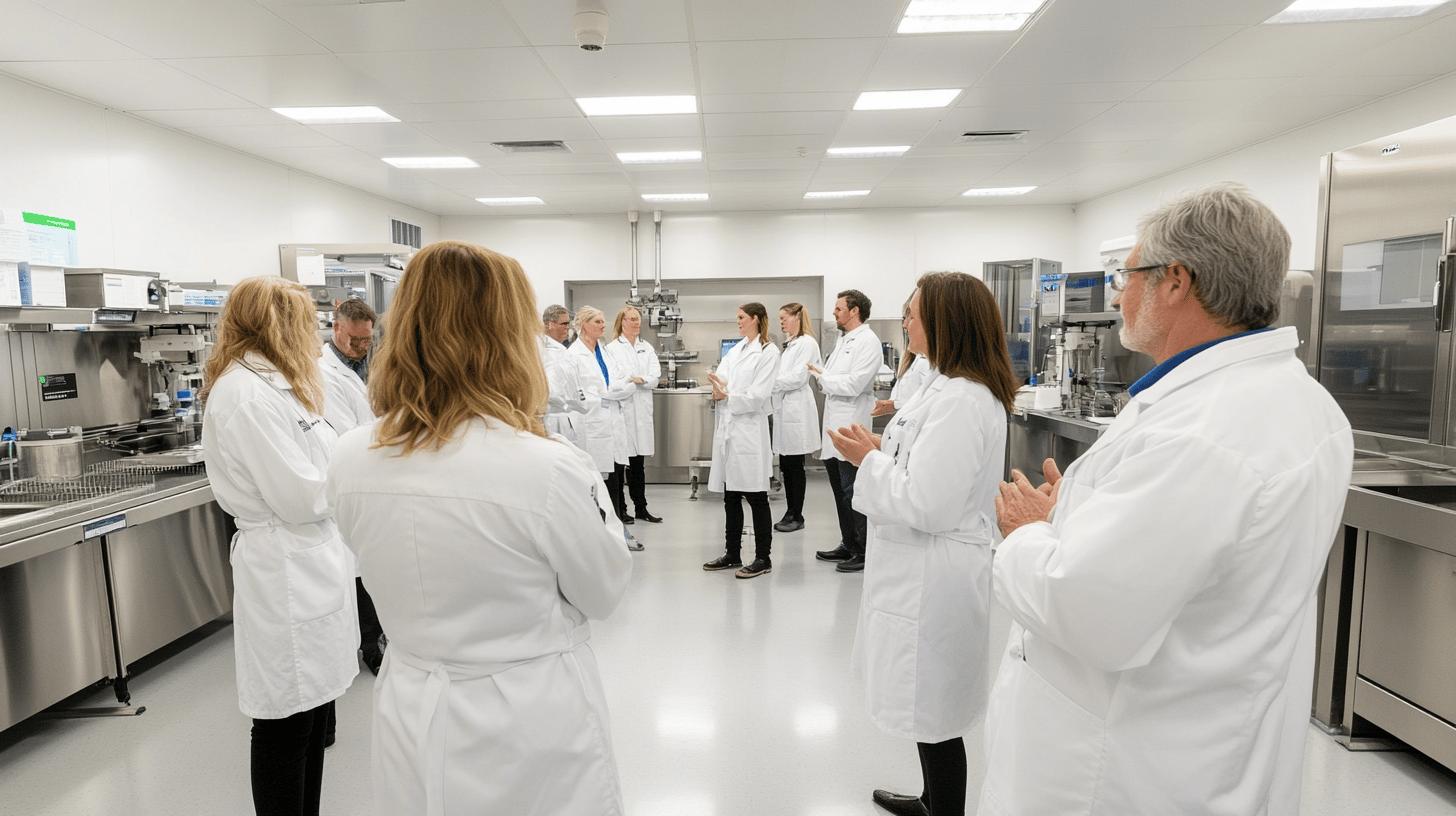
Building Quality Into Every Process
Quality by Design (QbD) represents a fundamental shift in pharmaceutical manufacturing. Instead of inspecting quality into products, QbD builds it into processes from the beginning. Enterprise quality management systems support this approach by enabling risk assessments and critical parameter monitoring throughout production.
For example, Fowlers of Bristol leveraged Q-Hub's quality management tools to drive their "Zero Defects" initiative. By implementing digital dashboards that tracked key performance indicators like "Right First Time" metrics, they transformed their quality culture from reactive to proactive.
Continuous improvement strategies also benefit from enterprise solutions. These platforms collect and analyse data to identify inefficiencies and recurring issues. When Rocal Insulating Panels needed to improve their safety management system, Q-Hub's centralised dashboards helped them track near misses, daily inspections, and accident trends—transforming data into actionable insights.
The Technology Revolution in Pharmaceutical Quality
AI and machine learning are transforming pharmaceutical quality control. These technologies analyse historical and real-time data to predict potential issues before they occur. When subtle process variations emerge, AI systems can flag anomalies before they affect product quality, preventing costly recalls and ensuring batch-to-batch consistency.
Automation reduces human error while streamlining workflows. Document control systems ensure every revision is tracked and verified, maintaining the data integrity required by regulatory standards. Real-time monitoring systems detect deviations instantly, enabling immediate corrective actions that prevent batch failures.
Anglia Cathodic Protection Services experienced this transformation firsthand. Their paper and spreadsheet-based systems couldn't keep pace with growing client demands. After implementing Q-Hub, they digitalised their compliance processes, making them more accessible and actionable while eliminating bottlenecks in audit management and non-conformance tracking.
Cultivating a Culture of Quality Excellence
Technology alone can't ensure quality—it requires a culture where every employee takes ownership of excellence. This means developing not just procedures but mindsets where quality is everyone's responsibility. Enterprise tools support this cultural transformation by making quality processes transparent and accessible to all.
Training management systems automate scheduling and tracking, ensuring employees receive timely updates on critical procedures. When Scottish Leather Group needed to improve engagement across departments, Q-Hub's ability to share documents and track "read and understood" acknowledgments fostered accountability at all levels of the organisation.
Effective deviation management is another crucial element. Root cause analysis tools help identify patterns and systemic issues, converting incidents into opportunities for improvement. These systems turn quality assurance from a department responsibility into an organisation-wide commitment.
Enterprise quality control solutions are transforming pharmaceutical manufacturing by making compliance simpler, more efficient, and more reliable. Q-Hub's comprehensive platform offers pharmaceutical manufacturers the tools they need to meet regulatory requirements while optimising processes and fostering a culture of quality excellence. Ready to elevate your quality management approach? Discover how Q-Hub's tailored solutions can transform compliance challenges into operational advantages.
Start using Q-Hub today
- Manage compliance in one place
- Streamline your teams and tasks
- Use Q-Hub free for 30 days