The Growing Documentation Burden in Metal Fabrication: Why Spreadsheets No Longer Cut It
Does your team spend more time managing paperwork than focusing on precision metalwork and innovation?
Small metal fabricators face unique challenges in balancing hands-on production excellence with increasingly demanding quality documentation requirements.The whir of cutting machines, the precise dance of welding equipment, the meticulous measuring and fitting—your small metal fabrication workshop produces quality components, but is the paperwork and process management keeping pace with your craftsmanship?
For many small metal fabricators across the UK, excellence in metalwork often contrasts sharply with behind-the-scenes operational chaos. Spreadsheets multiply like weeds, traceability becomes a paper chase, and quality documentation struggles to keep pace with production demands. This administrative burden doesn't just create headaches—it directly impacts your bottom line through errors, rework, and delayed deliveries. The good news? UK fabricators implementing digital management systems are seeing remarkable transformations: process errors down by up to 25%, delivery times accelerated by 20%, and regulatory audit readiness improved by as much as 30%. This article unpacks how you can achieve similar results without disrupting your production or breaking the bank.
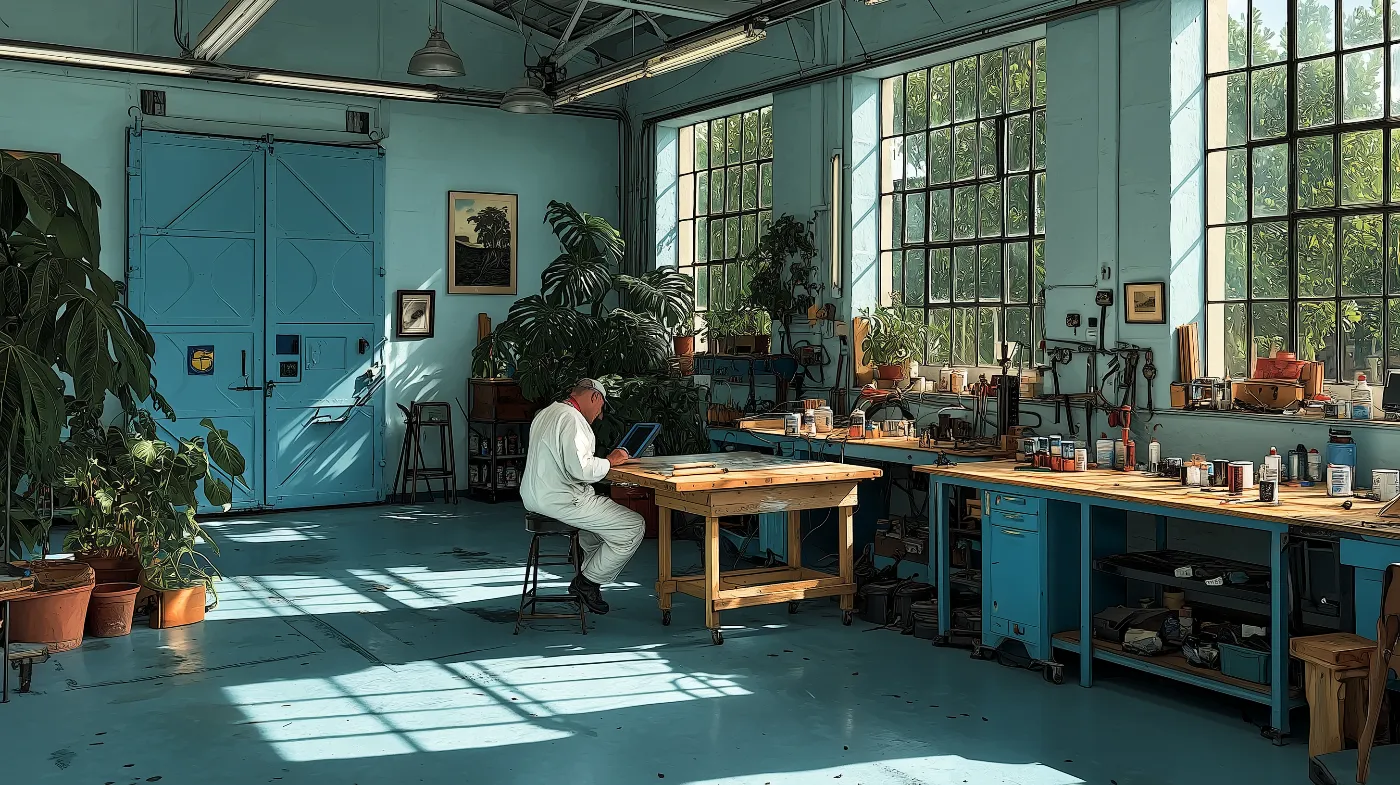
31% of UK metal businesses identified price volatility and supply disruptions as key motivators in adopting more sustainable, resource-efficient management practices.
The landscape for small metal fabricators has transformed dramatically over the past five years. Customers increasingly demand comprehensive quality documentation, material traceability, and evidence of process consistency. Meanwhile, volatile material costs mean that production errors and rework directly impact already-tight margins. Traditional paper-based systems and fragmented spreadsheets—often developed ad hoc as businesses grew—simply cannot deliver the operational visibility needed in today's market.
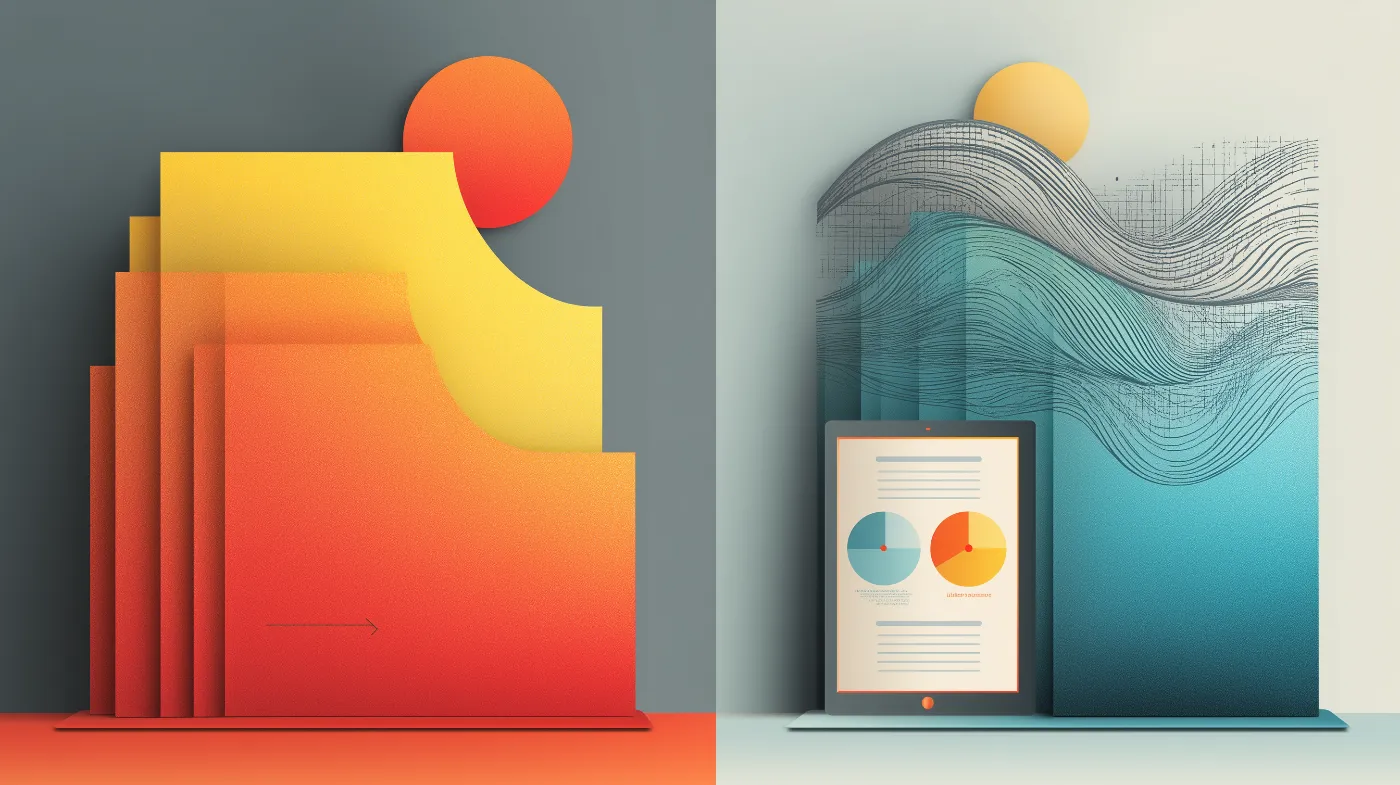
- Manual tracking systems typically result in 4-7 hours of administrative overhead per week for small fabrication shops, time that could be spent on production or business development.
- According to industry benchmarks, quality-related paperwork often increases by 35% when bidding for larger contracts or serving regulated industries like aerospace or energy.
- Metal fabricators using spreadsheet-based quality tracking report spending an average of 12-15 hours monthly reconciling records for customer audits—time that digital systems can reduce by up to 70%.
The Measurable Impact: How Digital Quality Management Transforms Metal Fabrication Operations
Small metal fabricators implementing integrated quality management systems report an average 15-25% reduction in process errors and rework, translating to approximately £14,000-£22,000 in annual savings for a typical 10-person operation.
- Up to 20% faster order turnaround and customer delivery times through streamlined workflow management, better document control, and integrated operations platforms.
- Enhanced traceability and batch control, enabling small fabricators to track materials from supplier to finished product with up to 30% improvement in regulatory audit readiness.
- Material waste reduction of 12-18% through better process standardisation and quality control measures, directly improving profit margins in an era of volatile material costs.
Performance Metric | Typical Improvement |
---|---|
Process Error Rate | 15-25% reduction |
Order Delivery Time | 20% reduction |
Material Waste | 12-18% reduction |
Audit Preparation Time | 60-70% reduction |
Customer Satisfaction | 22% improvement |
While implementing digital systems requires initial investment of time and resources, the cost of inaction is far greater. Metal fabricators continuing with manual or spreadsheet-based quality management face increasing competitive disadvantages, including lost contracts to more agile competitors, growing administrative overhead, and vulnerability to costly quality incidents that could have been prevented with better visibility and control.
Practical Steps: Transforming Your Metal Fabrication Operations Without Disrupting Production
- Map and Document All Core Manufacturing Processes: Begin by clearly mapping out all manufacturing workflows, from material intake to final product delivery. Create diagrams and written documentation for each process step, including responsibilities and decision points. This mapping should cover job scheduling, inventory movements, bills of material, and order tracking—critical functions for small metal fabricators. Use process mapping tools (digital flowchart software or whiteboards) and shop management platforms with process visualisation modules. The expected outcome is improved process visibility, identification of inefficiencies, and creation of a clear baseline for improvement initiatives.
- Set Measurable Quality Objectives and Track Key Metrics: Formulate concise, data-driven quality objectives aligned to business goals, such as reducing material waste, minimising rework, or decreasing customer complaints. Define a set of key metrics for ongoing tracking within your software platform (e.g., first-pass yield, order delivery times, scrap rates). Regularly review performance and share progress with your team. Use manufacturing management software with integrated reporting/analytics, shop floor data collection terminals, and regular team meetings. The expected outcome is greater focus on achievable improvements, ongoing measurement of performance, and a culture of continuous improvement.
- Implement Standard Operating Procedures and Continuous Feedback Loops: Develop detailed standard operating procedures (SOPs) for each mapped process. Train staff on these standards and create mechanisms for capturing feedback and corrective actions (such as deviation logs or nonconformance reports). Utilise regular reviews to update procedures and reinforce best practices, ensuring adaptations as business needs evolve. The expected outcome is consistent process adherence, faster identification and resolution of issues, and improved overall product quality.
- Select and implement a manufacturing-focused QMS software solution, ensuring it covers core needs such as document control, job costing, materials traceability, and flexible workflow management. Prioritise systems that offer integration capabilities with your existing shop floor equipment and business software, and that provide mobile access for shop floor data collection. Train all staff thoroughly and designate system champions who can support ongoing adoption.
Common Myths About Digital Quality Management Systems
- Digital quality management systems are only necessary for large metal fabricators serving highly regulated industries.
- While larger fabricators may face more extensive documentation requirements, small shops actually see proportionally greater benefits from digitisation. According to UK Metals Council data, small fabricators (5-25 employees) implementing QMS software report an average 23% reduction in administrative overhead, compared to 17% for larger operations. This efficiency gain allows smaller teams to focus more resources on value-added activities and competitive differentiation.
- Implementing digital systems will disrupt our production and require significant IT expertise.
- Modern quality management platforms are designed for phased implementation, allowing operations to continue without disruption. Most systems now offer cloud-based deployment options that require minimal IT infrastructure and provide mobile-friendly interfaces suited to shop floor environments. The key success factor is selecting a system designed specifically for manufacturing environments rather than generic business software.
Real Results: How UK Metal Fabricators Are Transforming Operations
https://www.q-hub.app/clients/case-study/bmc-analysisBMC Analysis, a specialised metal fabrication business, transformed their operations by implementing a comprehensive digital quality management system. Before implementation, they struggled with manual NCR tracking that created fragmented investigations and reports, time-consuming document acknowledgment processes that risked compliance failures, and inefficient asset management with no automated tracking for calibration and maintenance tasks.
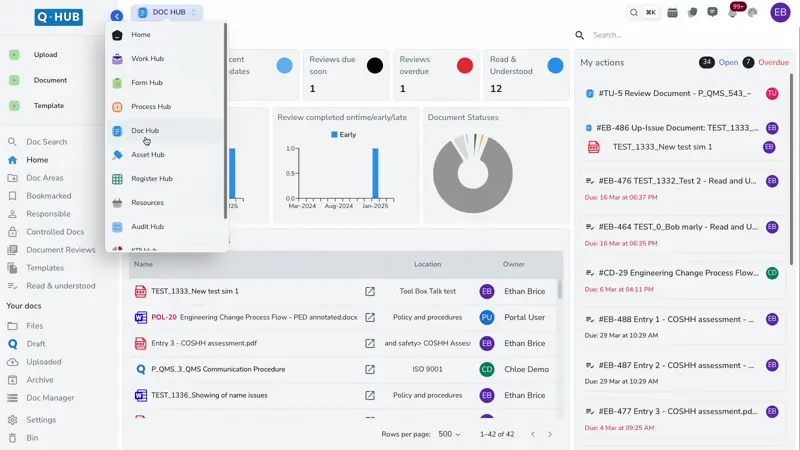
"The automation and centralisation that Qhub offers have completely transformed our quality management operations. NCR reporting is streamlined, document control is effortless, and audit preparation is faster than ever. These changes have saved us countless hours across multiple teams, and we're excited to expand Qhub's use into other business areas in the future."
- Manual NCR tracking creating fragmented investigations and reports
- Time-consuming document acknowledgment processes risking compliance failures
- Inefficient asset management with no automated tracking for calibration
- Streamlined NCR management with centralised digital platform
- Digitized document control with automated acknowledgments
- Improved asset management with automated calibration schedules
- Enhanced audit readiness with centralized documentation
The Road Ahead: Future Trends Reshaping Small Metal Fabrication
The adoption of collaborative robots (cobots) in metal fabrication is accelerating, with over 40% of surveyed UK manufacturers investing in robotics between 2022 and 2024. For small metal fabricators, these technologies offer the potential to boost productivity, lower labour costs, and enhance workplace safety—making it feasible to remain competitive despite workforce and pricing pressures.
- Surge in Additive Manufacturing (3D Printing): Adoption of 3D printing technologies among UK metal fabricators grew by 27% between 2020 and 2024. Small fabricators can use additive manufacturing to deliver bespoke components, lower material waste, and accelerate product development, giving them a competitive edge in niche markets.
- Focus on Supply Chain Resilience and Diversification: 24% of UK metals businesses have adjusted supply strategies, and 17% have diversified their business activities since 2021. Small metal fabricators must monitor supply risks, diversify material sources, and manage lead times more effectively to ensure continuity and profitability.
- Sustained Market Growth Driven by Infrastructure and Renewable Energy: UK metal fabrication market is projected to grow at a CAGR of 5.1% from 2025 onward, reaching USD 1.2 billion market size. Opportunities are emerging for small metal fabricators able to supply to infrastructure and offshore wind energy projects, especially those who can deliver high-quality, customised components.
- Increasing Emphasis on Sustainability and Environmental Performance: 31% of UK metal businesses identified price volatility and supply disruptions as key motivators in adopting more sustainable, resource-efficient practices. Small fabricators that can demonstrate sustainable practices and reduce their environmental impact will be better placed to win contracts and appeal to environmentally conscious clients.
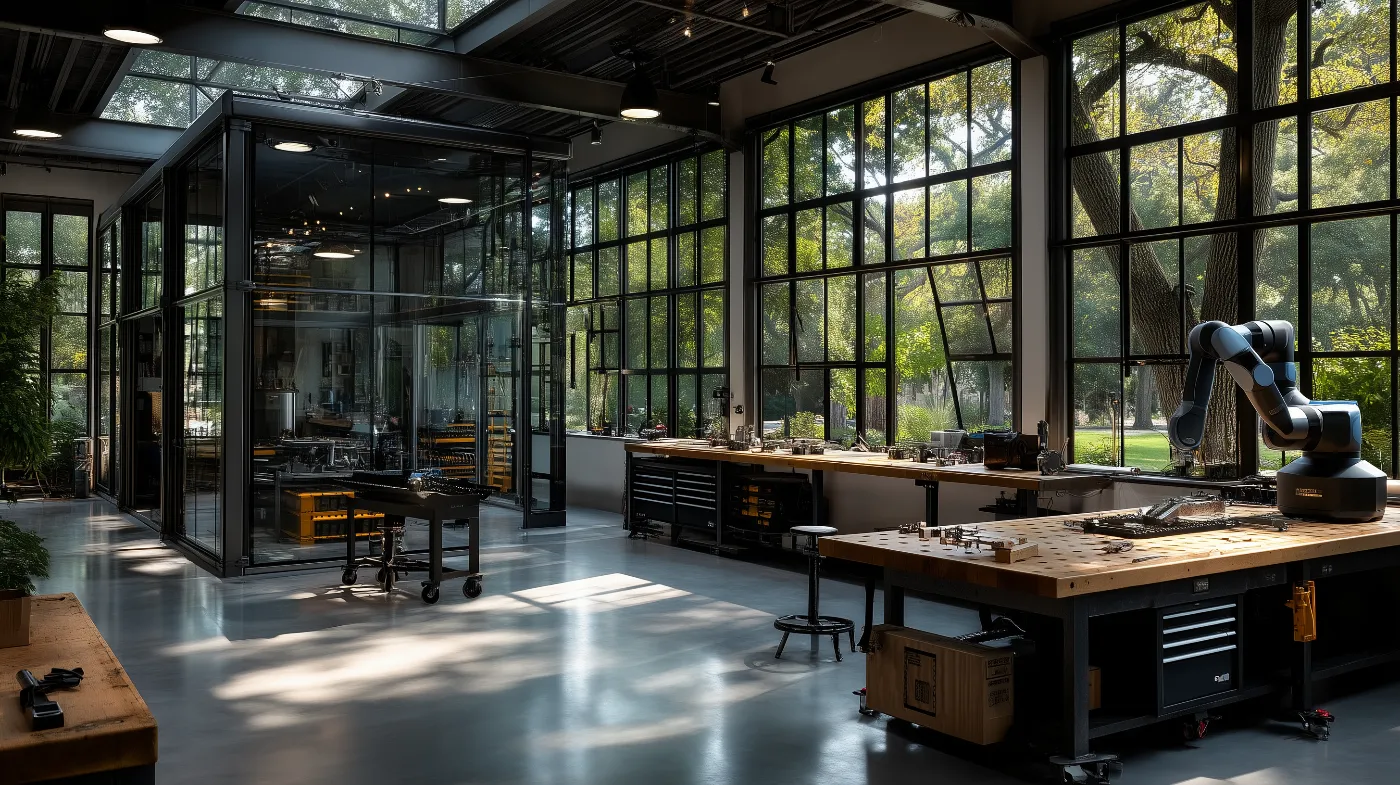
The transformation from spreadsheet chaos to digital control represents more than just operational efficiency for small metal fabricators — it's increasingly becoming a competitive necessity. As we've seen, the benefits are substantial and measurable: reduced errors, faster delivery times, enhanced traceability, and improved margins. The path forward doesn't require massive disruption or excessive investment, but rather a strategic, step-by-step approach to streamlining your quality management processes.
- Map your current processes to identify inefficiencies and improvement opportunities
- Set measurable quality objectives aligned with your business goals
- Implement standardized procedures with feedback mechanisms
- Select and deploy a manufacturing-focused QMS solution