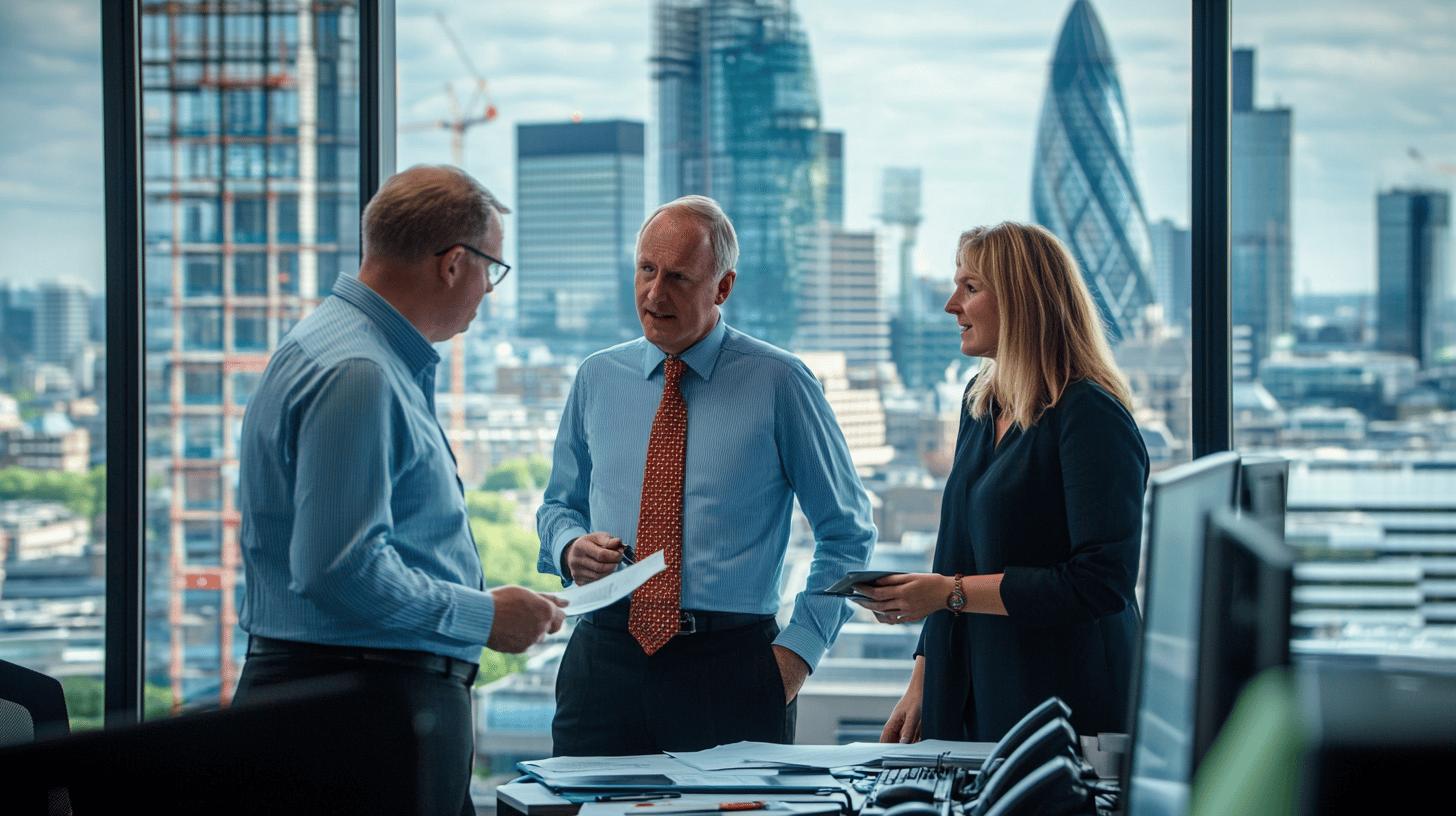
Continuous Improvement Programmes Boost Audit Procedures
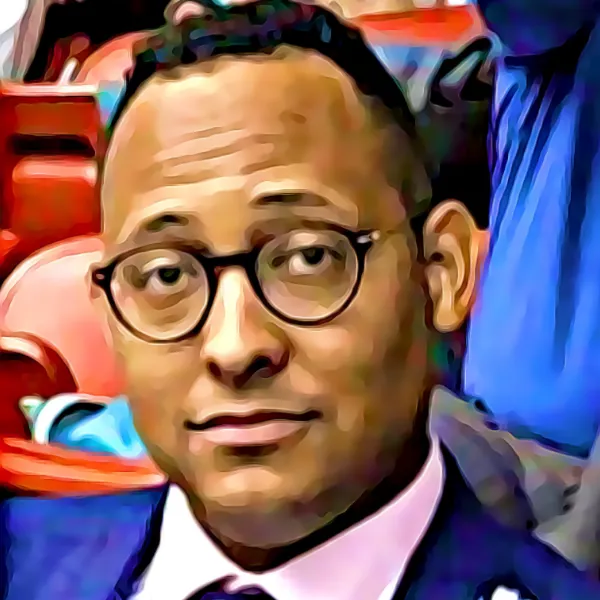
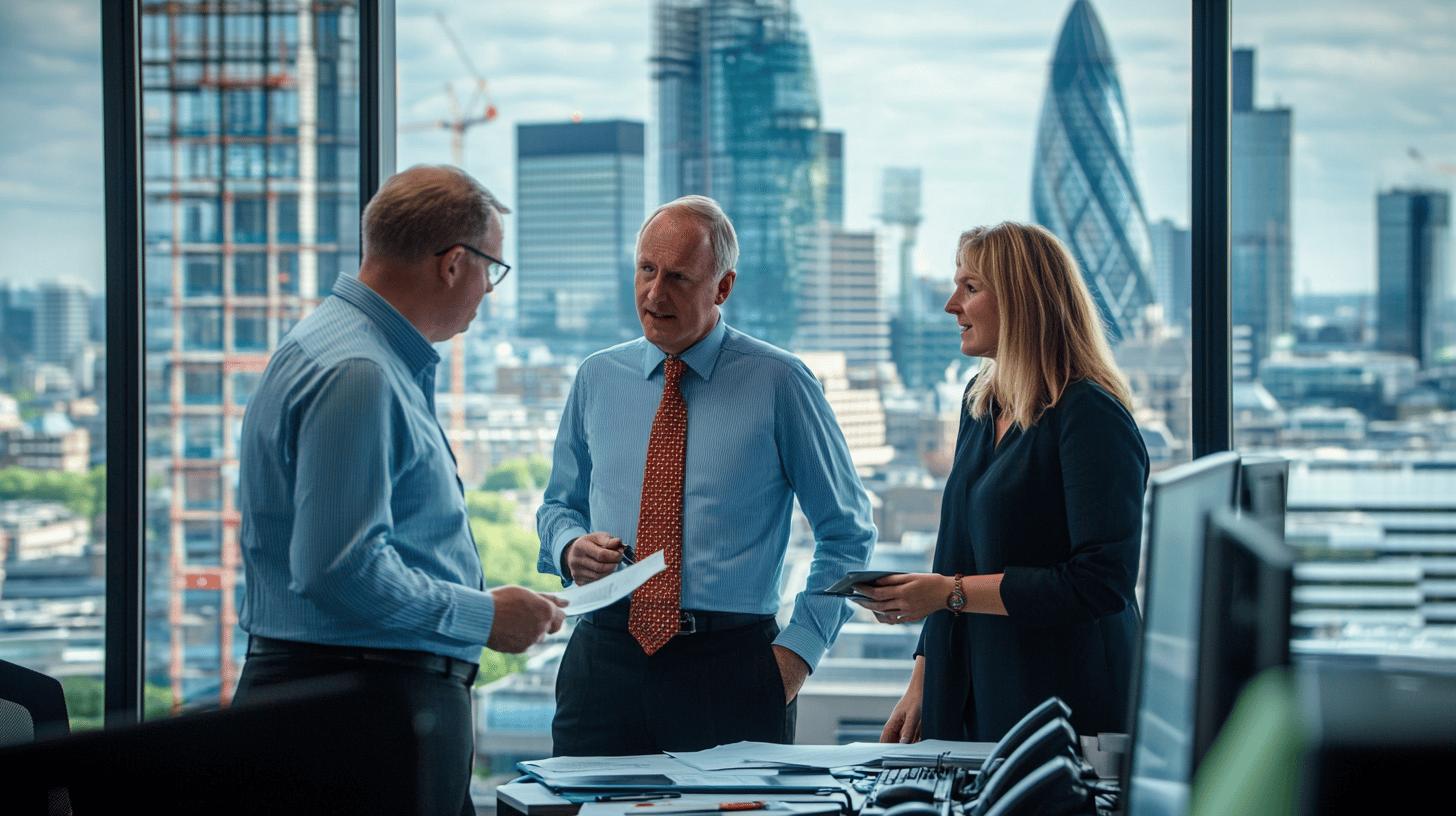
Continuous Improvement Programmes Boost Audit Procedures
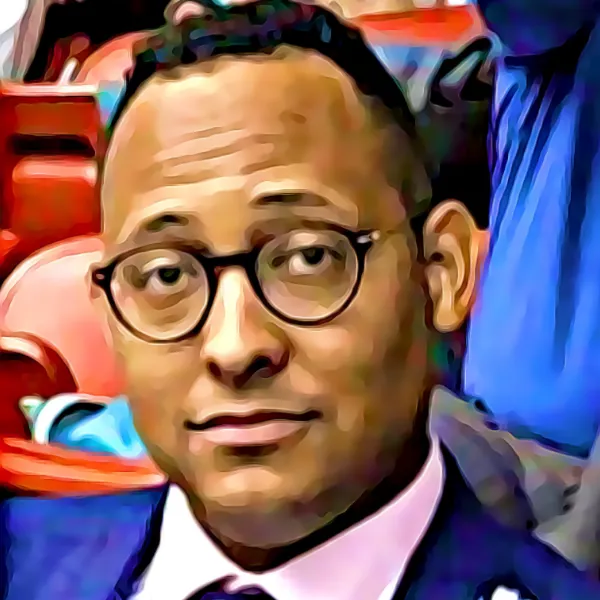
The Role of Continuous Improvement Programmes in Engineering Audit and Inspection Procedures
Continuous improvement programmes are revolutionising engineering audit and inspection procedures by systematically enhancing compliance, quality, and operational efficiency. In an industry where precision is non-negotiable, these initiatives identify inefficiencies and address root causes in structured ways. For engineering firms, such programmes aren't optional extras—they're essential for maintaining regulatory compliance while driving operational excellence.
Q-Hub's digital solutions play a critical role in this transformation, helping organisations move beyond traditional paper-based systems to integrated, data-driven approaches. Without robust improvement frameworks, companies risk compliance breaches, inconsistent quality, and inefficient resource allocation—costly problems in today's competitive landscape.
Engineering audits are no longer about ticking boxes. They're about creating sustainable systems that consistently deliver value while maintaining compliance with standards like ISO 9001 and ISO 45001.
Effective continuous improvement streamlines workflows while enhancing data accuracy. For example, automated tools can flag discrepancies in real-time, substantially reducing human error in inspection processes. These programmes ultimately foster a culture of constant evaluation and controlled iteration—essential qualities in an engineering sector facing ever-increasing regulatory and competitive pressures.
<table border="0"> <tr><th>Improvement Area</th><th>Before Digital Transformation</th><th>After Implementation</th></tr> <tr><td>Audit Preparation</td><td>Days of manual collection</td><td>Hours with automated systems</td></tr> <tr><td>Document Control</td><td>Fragmented storage systems</td><td>Centralised digital libraries</td></tr> <tr><td>Non-Conformance Resolution</td><td>Weeks with manual tracking</td><td>Days with automated workflows</td></tr> </table>Unlocking Engineering Excellence Through Methodological Approaches

Continuous improvement programmes employ several key methodologies to transform engineering audit and inspection procedures. These structured approaches help organisations systematically address inefficiencies while maintaining rigorous compliance standards.
Six Sigma provides a data-driven framework that minimises variability in auditing processes. Using the DMAIC model (Define, Measure, Analyse, Improve, Control), organisations can identify recurring errors in inspection data and implement preventative controls. This methodical approach ensures consistency across all quality checkpoints.
Lean principles complement Six Sigma by eliminating waste in audit workflows. By mapping inspection processes step-by-step, teams can identify and remove unnecessary procedures that consume resources without adding value. For example, Scottish Leather Group eliminated redundant documentation steps when they implemented Q-Hub's digital solution, significantly reducing audit preparation time.
Meanwhile, Kaizen fosters small, incremental improvements that collectively transform audit quality. Rather than overhauling systems entirely, this approach encourages teams to continuously refine processes through minor adjustments—perhaps adding verification steps or streamlining reporting workflows.
Root cause analysis digs deeper than surface-level fixes. When Weston Aerospace faced delayed inspection results, they used this technique to identify that outdated software was causing bottlenecks. By addressing the fundamental issue rather than adding more staff, they achieved sustainable improvements in inspection efficiency.
Complementing these approaches, process mapping provides visual clarity by documenting every step in audit workflows. This technique helps identify redundancies and error-prone areas, creating opportunities for targeted improvements.
- Six Sigma: Reduces variability and standardises audit processes
- Lean Principles: Eliminates non-value-adding steps in inspection workflows
- Kaizen: Encourages continuous, incremental refinements to procedures
- Root Cause Analysis: Addresses underlying issues rather than symptoms
- Process Mapping: Visualises workflows to identify improvement opportunities
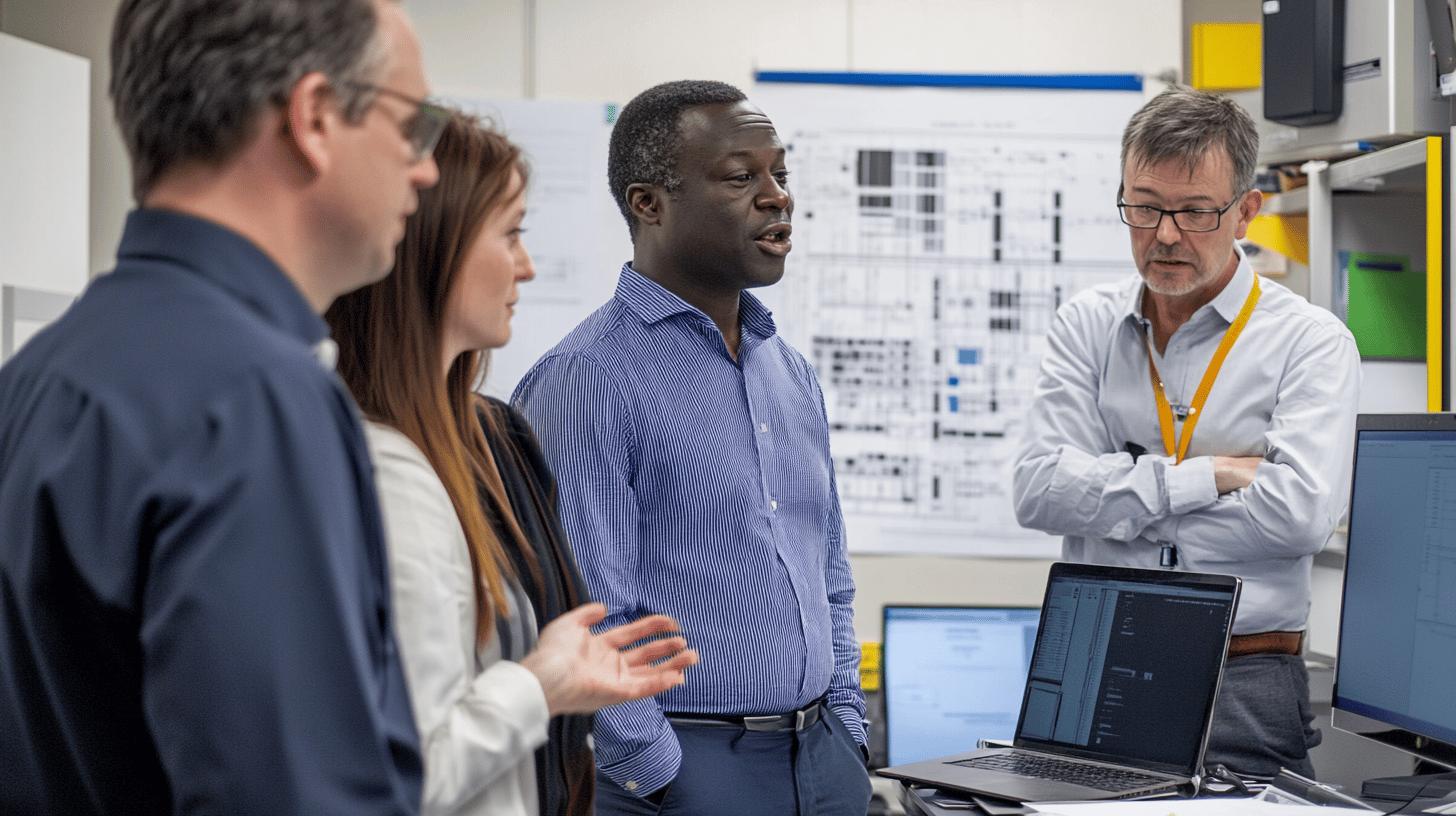
How Digital Transformation Drives Measurable Benefits
The integration of continuous improvement programmes into engineering audit procedures delivers tangible advantages across multiple business dimensions. When properly implemented, these initiatives transform compliance from a checkbox exercise into a strategic advantage.
Enhanced regulatory compliance stands out as a primary benefit. By aligning processes with standards like ISO 9001 and ISO 45001, organisations reduce non-conformities and avoid potentially costly penalties. Fowlers of Bristol experienced this firsthand when implementing Q-Hub's quality management tools, which streamlined their documentation controls and significantly improved compliance outcomes.
Defect reduction represents another critical advantage. Continuous improvement methodologies help identify and address quality issues earlier in processes. When one automotive manufacturer applied these principles, they achieved a remarkable 20% reduction in defects by systematically refining their inspection procedures.
Cost efficiency improves naturally as processes become more streamlined. Anglia Cathodic Protection Services reported substantial operational savings after digitising their previously fragmented systems with Q-Hub. By eliminating redundant steps and automating routine tasks, they reduced resource requirements while improving outcomes.
Customer satisfaction ultimately benefits from these improvements. When audits and inspections consistently identify and address issues before products reach customers, reliability improves and reputation strengthens. This creates a virtuous cycle of trust and continued business.
Game-Changing Technologies Powering Modern Audit Approaches
The technological backbone of effective continuous improvement in engineering audits comprises several interconnected systems. These digital tools transform how organisations gather, analyse, and act upon inspection data.
Advanced audit software represents the cornerstone of modern improvement programmes. Platforms like Q-Hub automate document reviews and standardise data collection, reducing human error while increasing consistency. BMC Analysis demonstrated the impact of such tools when they digitised their NCR management processes, transforming what was once a fragmented email-based system into a structured, accountable workflow.
IoT devices extend these capabilities by enabling real-time condition monitoring. Rather than waiting for scheduled inspections, sensors can continuously track equipment performance and automatically trigger alerts when parameters deviate from acceptable ranges. This predictive approach helps organisations address potential issues before they escalate into major problems.
AI-powered analytics further enhance these capabilities by identifying patterns invisible to human reviewers. By analysing historical inspection data, these systems can predict future failure points and recommend preventative measures—shifting the entire audit philosophy from reactive to proactive.
Digital dashboards tie these elements together, providing at-a-glance visibility into compliance metrics and inspection outcomes. Rocal Insulating Panels leveraged such tools to centralise their safety operations, making it easier to track near misses, manage daily inspections, and identify emerging trends.
Key Technology Integration Points for Engineering Audits
Effective implementation typically integrates:
- Document management systems that maintain version control and approval workflows
- Mobile data collection tools for field inspections
- Automated notification systems for non-conformances
- Integrated calibration management for test equipment
- Real-time reporting dashboards for management visibility
Real-World Success: Transformation Stories That Inspire
Continuous improvement programmes have delivered remarkable results across various engineering sectors. These case studies demonstrate how systematic approaches to refining audit and inspection procedures translate into measurable business benefits.
In the aerospace sector, Weston Aerospace faced significant challenges with their paper-based quality systems. By implementing Q-Hub's digital platform, they transformed their audit processes through automated workflows and centralised documentation. The results were striking: audit preparation time reduced by days, while compliance visibility dramatically improved across all departments.
Similarly, Anglia Cathodic Protection Services struggled with fragmented processes spanning multiple sites. Their implementation of a continuous improvement programme centred around digital transformation helped unify systems and enhance productivity. The Process Hub feature proved particularly valuable for tracking non-conformances, linking them directly to audits and ensuring accountability at each resolution step.
For Rocal Insulating Panels, safety management posed significant challenges. Their previous system relied on cluttered file storage and paper-based accident reporting, creating delays and inconsistencies. Q-Hub's platform revolutionised their approach by centralising safety operations through intuitive dashboards. This improved visibility across departments and streamlined accident investigations, resulting in faster resolution times and better compliance.
Scottish Leather Group's experience demonstrates how continuous improvement can work at scale. Managing multiple ISO standards across different sites presented considerable complexity, but their systematic approach using Q-Hub's modular platform created a unified, efficient workforce. Audit preparation time decreased significantly, while communication between departments improved through centralised digital systems.
Blueprint for Implementation: Making Continuous Improvement Work
Implementing continuous improvement for engineering audits requires a structured approach that balances technical capabilities with human factors. Even the most sophisticated systems will fail without proper change management and stakeholder buy-in.
Begin with comprehensive employee training. This ensures that staff can effectively use new tools and understand the principles behind process changes. When BMC Analysis implemented their digital transformation with Q-Hub, they prioritised training across all levels, from shop floor workers to senior management, ensuring everyone could participate in the improvement journey.
Effective change management proves equally crucial. Engineering organisations often have established procedures and cultural resistance to new approaches. Creating a phased implementation plan with clear communication helps overcome this natural resistance. Fowlers of Bristol succeeded by introducing continuous improvement gradually, allowing teams to adapt while maintaining operational continuity.
Stakeholder engagement represents another critical success factor. When Scottish Leather Group implemented their improvement programme, they involved representatives from each department in the planning process. This collaborative approach ensured the solution addressed specific needs across the organisation while building ownership and commitment.
Strategic alignment provides the final cornerstone. Continuous improvement initiatives must connect directly to broader organisational objectives—whether that's achieving certification, reducing operational costs, or enhancing product quality. This alignment ensures sustained support and resources for the programme.
Companies embracing these implementation principles typically experience smoother transitions and more sustainable results:
- Conduct thorough needs assessment before selecting improvement methodologies
- Start with pilot projects that demonstrate quick wins and build momentum
- Establish clear metrics to measure progress and demonstrate value
- Create feedback mechanisms to capture insights from all levels of the organisation
- Review and refine programmes regularly based on performance data
Q-Hub's engineering clients have consistently found that these implementation practices help transform theoretical improvement models into practical, sustainable operational excellence.
The journey toward optimised engineering audits and inspections continues to evolve with advancing technology and changing regulatory landscapes. By embracing continuous improvement principles and leveraging digital tools like Q-Hub's integrated platform, organisations can not only maintain compliance but transform their quality processes into strategic advantages that drive long-term success.
Ready to transform your engineering audit and inspection procedures? Discover how Q-Hub's customised QHSE software solutions can help your organisation streamline processes, ensure compliance, and support sustainable growth through digital transformation.
Start using Q-Hub today
- Manage compliance in one place
- Streamline your teams and tasks
- Use Q-Hub free for 30 days