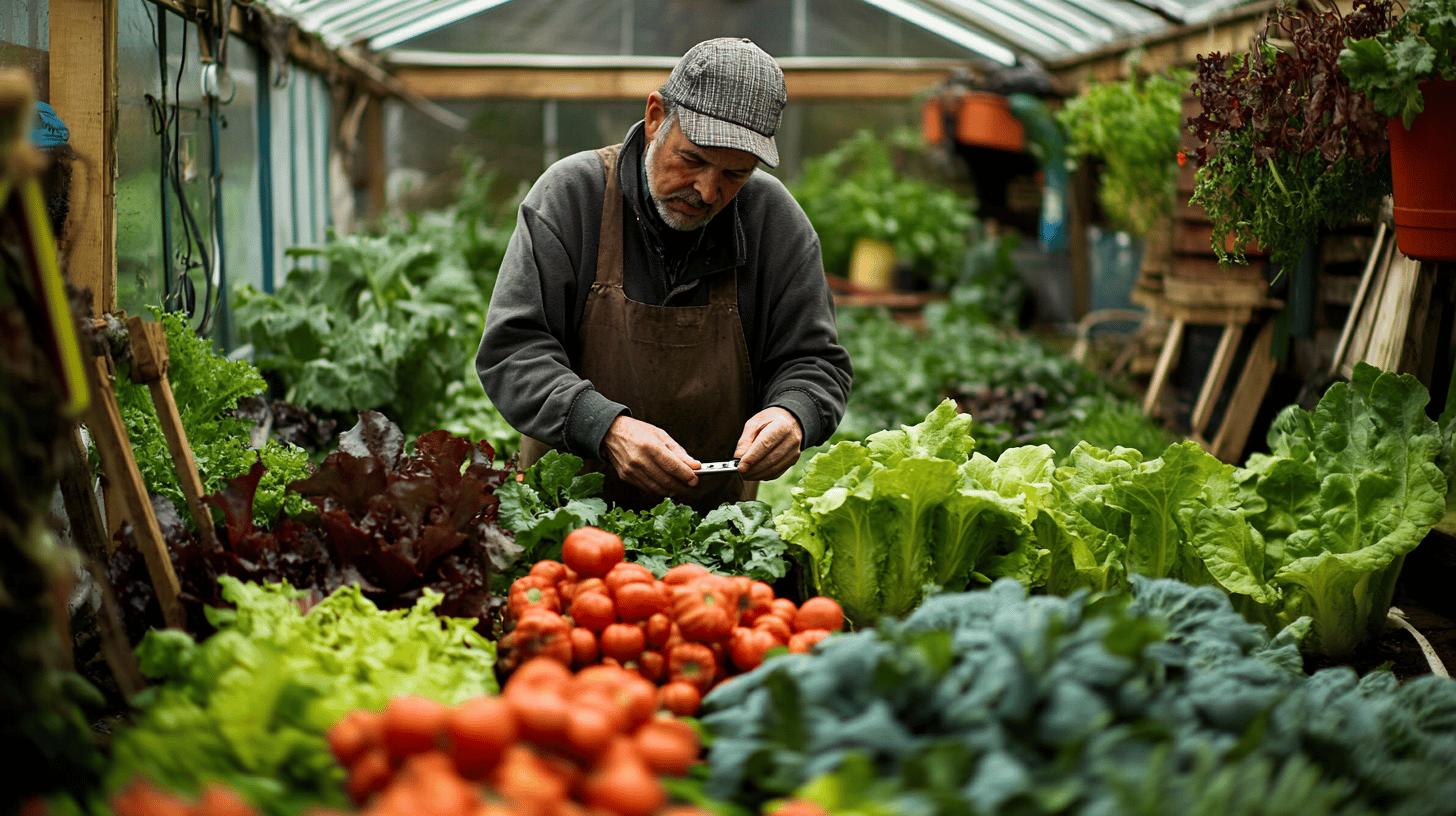
Data Management Solutions Boosting Food Safety and Quality
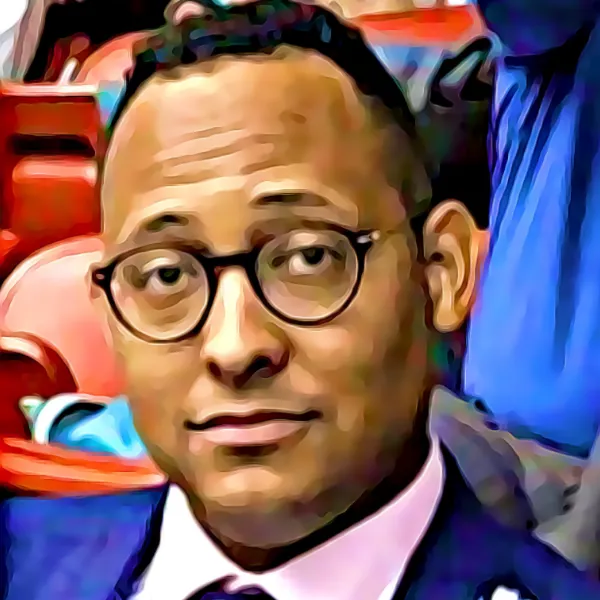
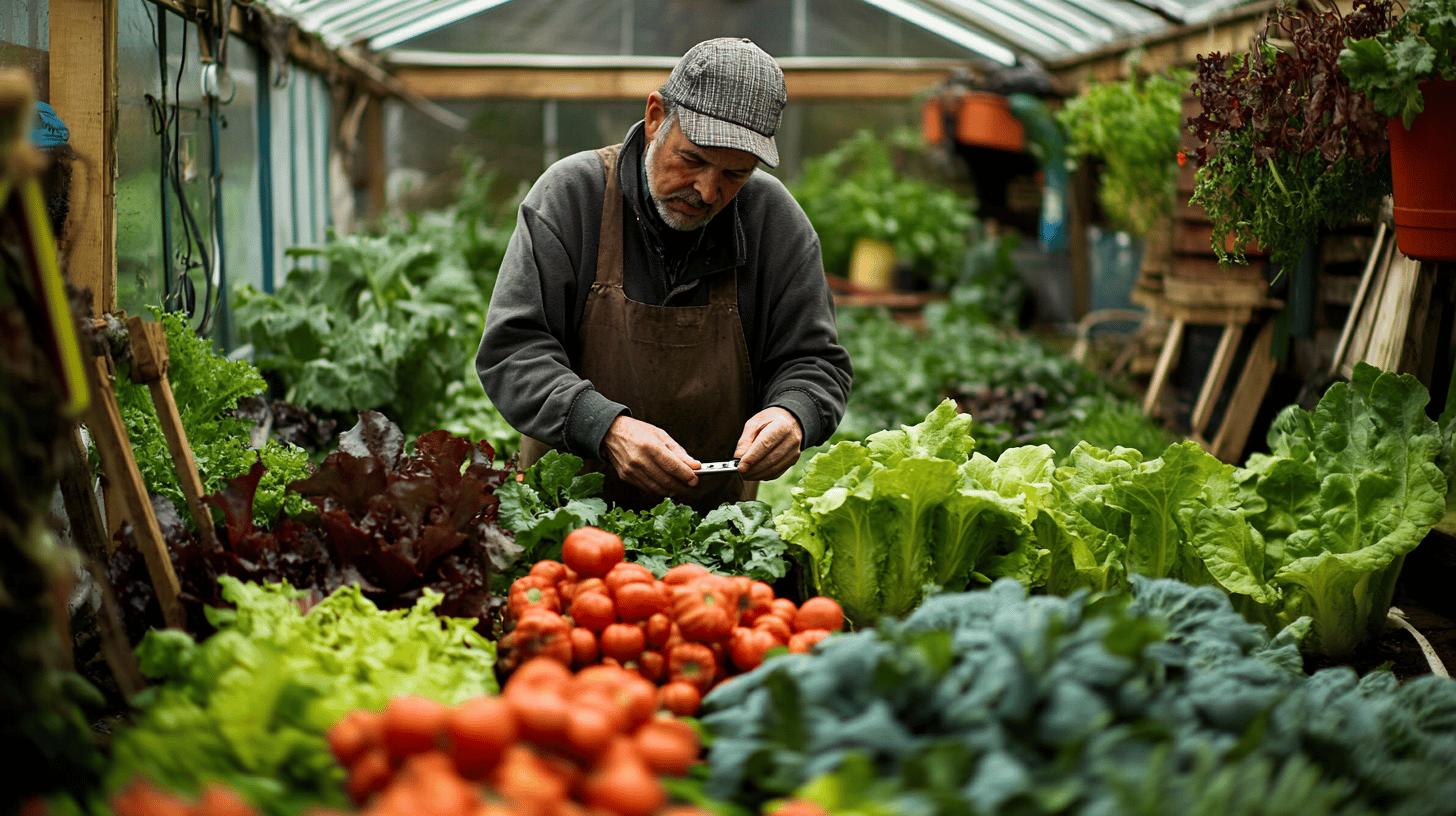
Data Management Solutions Boosting Food Safety and Quality
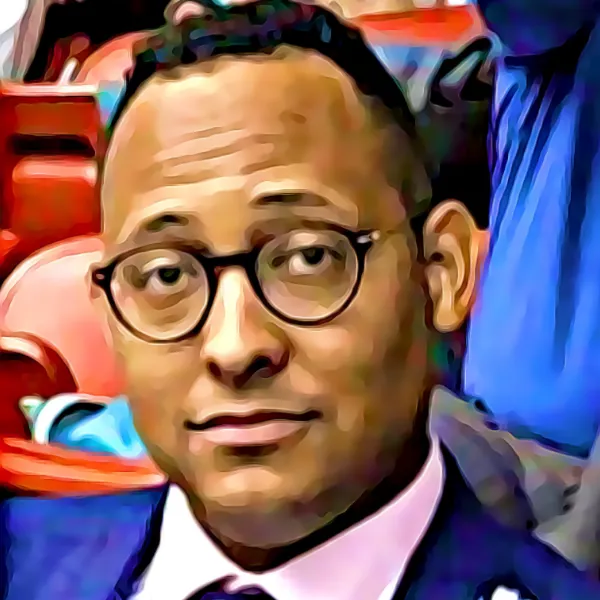
How Data Management Solutions Improve Product Safety for Food Producers
In today's fast-paced food industry, data management solutions strengthening product safety and quality assurance for food producers have become essential tools rather than optional extras. These systems help companies navigate complex regulatory requirements while eliminating the inefficiencies and errors inherent in manual processes. Q-Hub's specialised solutions address these challenges by digitising critical safety workflows, ensuring food producers can maintain compliance without sacrificing operational efficiency.
Manual processes in food production create significant vulnerabilities. Just imagine trying to track temperature variations across hundreds of batches by hand – mistakes are practically inevitable. These errors don't just compromise safety; they erode consumer trust and complicate regulatory inspections. Teams often waste valuable hours searching for scattered documentation during audits, further diminishing productivity.
The Digital Revolution in Food Safety Management
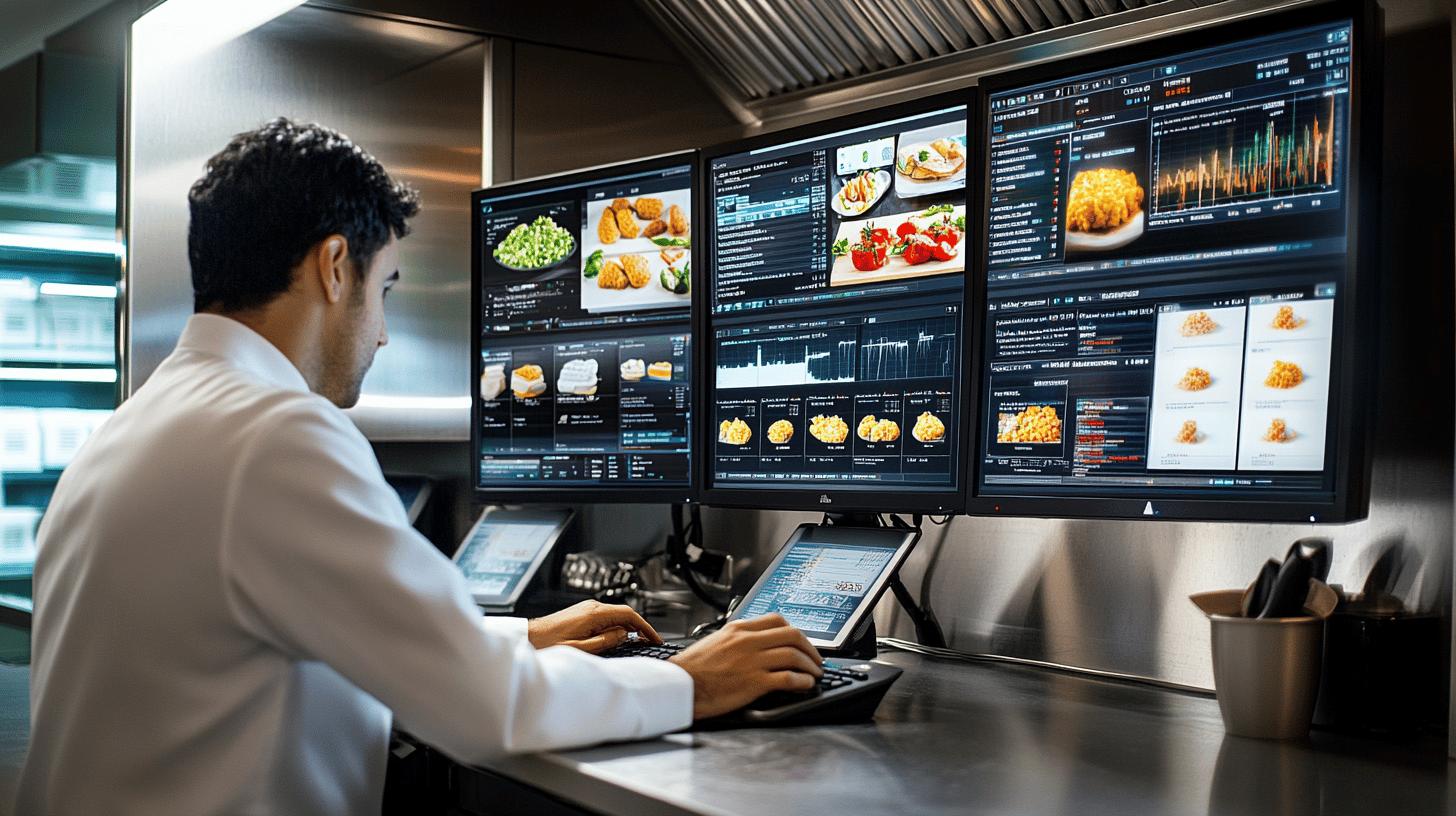
Automated data management solutions transform food safety operations through intelligent digitisation. By converting routine quality checks and inspections into streamlined digital workflows, these systems dramatically reduce human error while saving valuable time. Temperature monitoring becomes precise and real-time, eliminating guesswork and delays that plague manual approaches.
Centralised data collection creates audit-ready documentation at the touch of a button. This streamlined approach not only reduces compliance penalties but significantly enhances operational efficiency. The results speak for themselves – safer products, smoother inspections, and healthier bottom lines.
By implementing Q-Hub's digital data management solution, we've seen a 40% reduction in quality-related incidents and cut our audit preparation time in half. The system pays for itself through improved efficiency alone.
Beyond basic safety tracking, these solutions enhance operational visibility through intuitive dashboards and analytics. Real-time insights help identify trends and anomalies before they become serious problems, enabling proactive quality management rather than reactive damage control.
Traceability: The Backbone of Modern Food Safety
Effective traceability systems are non-negotiable in contemporary food production. Without them, identifying contamination sources becomes virtually impossible, placing both consumers and business reputation at risk. Robust traceability provides end-to-end accountability, dramatically reducing recall risks while strengthening quality assurance efforts.
The transparency provided by comprehensive traceability solutions delivers immediate practical benefits. When quality issues arise, producers can pinpoint exactly where problems originated – down to specific suppliers, batches, or even production lines. This precision enables targeted interventions rather than costly blanket recalls, saving both money and reputation.
Here are the key benefits traceability systems provide:
- Rapid identification of affected batches during contamination events
- Enhanced consumer confidence through supply chain transparency
- Reduced legal and financial exposure from non-compliance
- Data-driven decision-making capabilities
- Streamlined audit processes with centralised documentation
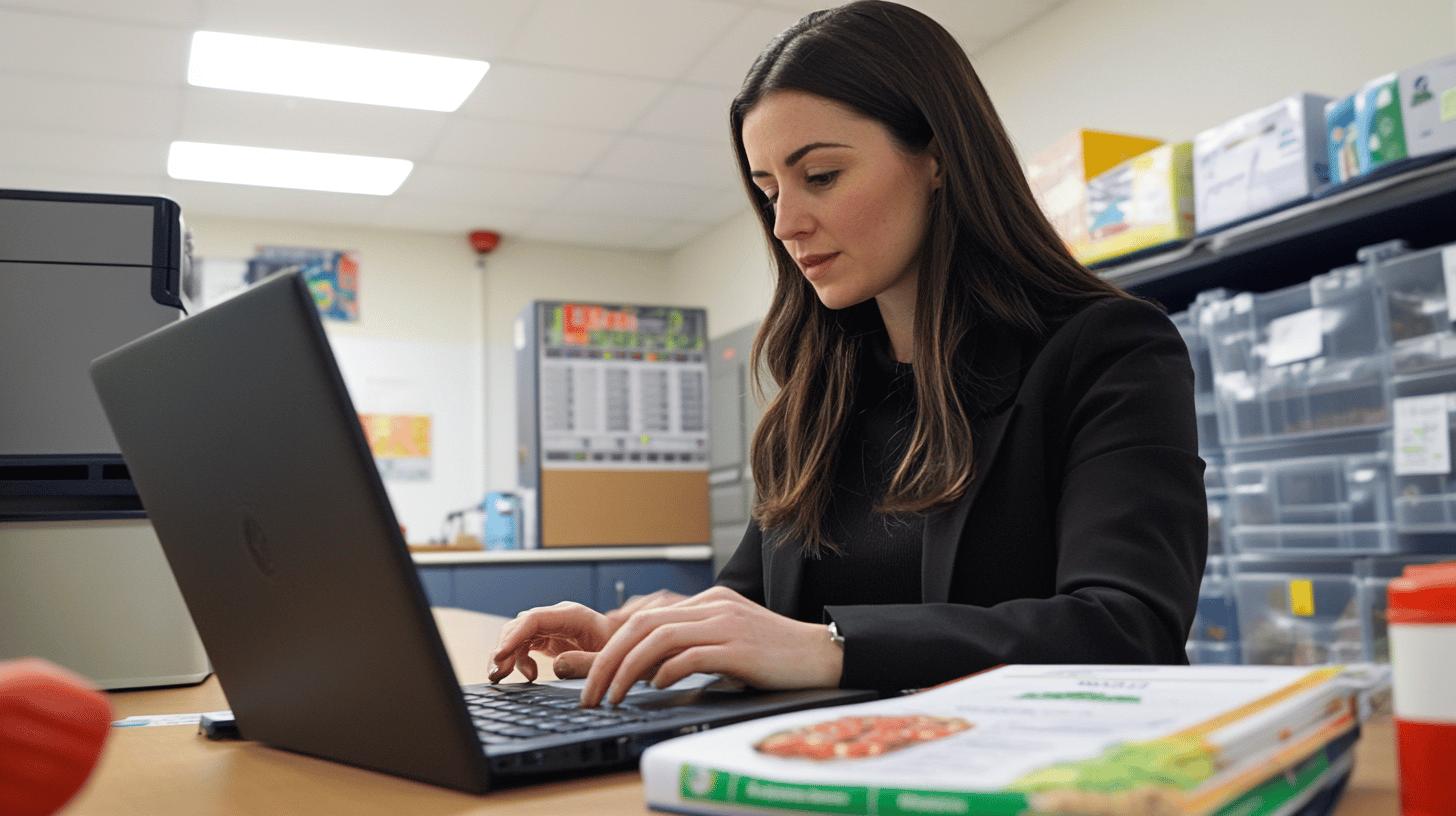
Integration with existing systems like ERP and QMS platforms further amplifies these benefits. Q-Hub's solutions excel at creating these seamless connections, providing a unified platform for monitoring, reporting, and data management that ensures both regulatory compliance and operational excellence.
Essential Features for Effective Food Safety Software
When evaluating data management solutions for food safety, certain capabilities stand out as essential. Real-time monitoring tops this list, providing immediate visibility into critical production parameters. User-friendly interfaces ensure broad adoption across teams, while comprehensive traceability features support both compliance and quality management goals.
Advanced analytics capabilities transform raw data into actionable insights. Predictive tools can identify potential issues before they impact production, while automated reporting simplifies regulatory compliance and internal oversight. Together, these features create a proactive safety culture that prevents problems rather than simply responding to them.
<table border="0"> <tr><th>Capability</th><th>Impact on Safety</th><th>Operational Benefit</th></tr> <tr><td>Real-time monitoring</td><td>Immediate detection of safety issues</td><td>40% reduction in quality incidents</td></tr> <tr><td>Integrated traceability</td><td>Precise identification of affected products</td><td>60% faster response to quality issues</td></tr> <tr><td>Automated reporting</td><td>Consistent compliance documentation</td><td>50% reduction in audit preparation time</td></tr> </table>Transforming Operations Through Case Studies
Real-world implementations demonstrate the transformative impact of comprehensive data management solutions. For example, when Scottish Leather Group implemented Q-Hub's digital solutions, they dramatically improved audit management across multiple ISO standards. The system eliminated paper-based processes, enhanced communication between sites, and created significant operational efficiencies.
Similarly, Fowlers of Bristol revolutionised their document control processes by implementing Q-Hub's platform. Their previous system relied heavily on email and in-person follow-ups, creating delays and inefficiencies. With Q-Hub's intuitive portal, they brought all critical workflows and communications into a single digital environment, enabling instant access to real-time data.
In both cases, implementing comprehensive data management solutions delivered measurable improvements:
Key Implementation Results
• 40-50% reduction in audit preparation time
• 25-30% decrease in quality control costs
• 15-20% improvement in compliance rates
• Significant reductions in manual data entry errors
• Enhanced visibility across departments and locations
Selecting the Perfect Solution for Your Requirements
Choosing the right data management solution requires careful consideration of several key factors. Essential functionalities like real-time monitoring, automated reporting, and comprehensive traceability should top your requirements list. Equally important is a user-friendly interface that supports rapid adoption across your organisation – complicated systems often face resistance that undermines their effectiveness.
Scalability deserves special attention when evaluating potential solutions. Your business will evolve, and your safety management system must grow alongside it. Q-Hub's platforms are designed with scalability at their core, ensuring they can adapt to changing requirements without disruptive replacements.
Integration capabilities determine how seamlessly a new solution will fit into your existing technology ecosystem. The best systems offer robust API functionality and pre-built connectors for common enterprise systems, creating a unified operational environment rather than another isolated data silo.
Implementation support and ongoing customer service significantly impact long-term success. Look for providers that offer comprehensive training, responsive support, and a track record of successful implementations in your industry. This ensures you'll maximise value from your investment while minimising implementation challenges.
As food safety regulations continue to evolve and consumer expectations rise, implementing robust data management solutions becomes increasingly critical. Q-Hub's customised QHSE software provides the comprehensive capabilities food producers need to ensure compliance, streamline processes, and support sustainable growth through digital transformation. By choosing the right solution, you're not just protecting your products – you're strengthening your entire operation.
Start using Q-Hub today
- Manage compliance in one place
- Streamline your teams and tasks
- Use Q-Hub free for 30 days