
Custom Development for Food Sector Incident Reporting
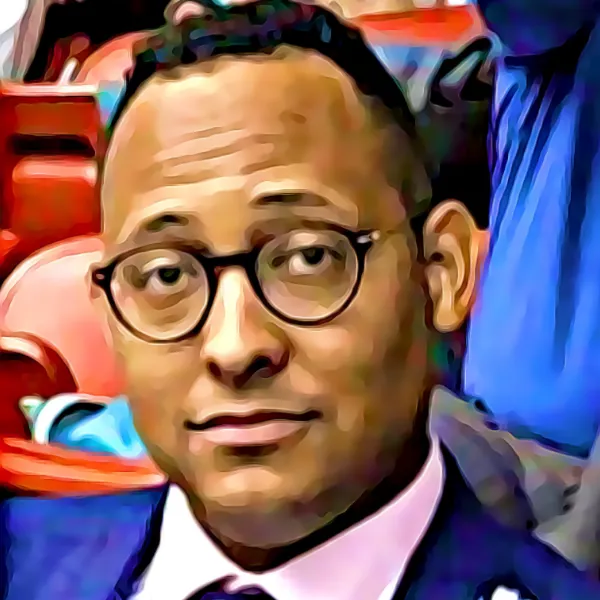

Custom Development for Food Sector Incident Reporting
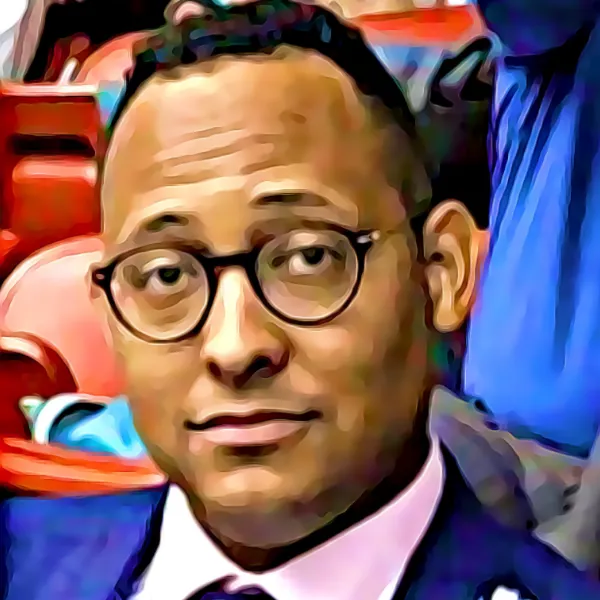
The Importance of Custom Development Projects for Incident Reporting in the Food Sector
Custom development projects for food sector incident reporting have shifted from optional investments to essential operational tools. In this highly regulated industry, bespoke software solutions address unique challenges that generic systems simply can't handle. Q-Hub specialises in creating these tailored digital solutions that help food businesses navigate complex compliance requirements while streamlining their reporting processes.
The food industry faces particularly strict regulatory demands, with standards like HACCP, ISO 22000, FDA FSMA and EU Food Law requiring meticulous documentation and real-time monitoring. Non-compliance risks are substantial – with UK fines averaging £100,000 per breach – not to mention the potential reputational damage and operational disruptions.
Traditional systems force food businesses to adapt their processes to fit the software, rather than the other way around. Custom solutions flip this relationship, creating systems that mirror your actual workflows.
Custom development delivers precision and adaptability that off-the-shelf solutions can't match. When incident reporting systems are tailored to your specific processes, they transform compliance from a burden into a competitive advantage.
Why Generic Solutions Fall Short in Food Safety

The food sector operates under unique constraints that make standard software inadequate for incident reporting. Multi-site operations, complex supply chains, and ever-evolving regulations create a perfect storm that generic systems simply weren't designed to handle.
Off-the-shelf solutions typically offer broad functionality that satisfies basic needs across multiple industries. However, they rarely provide the depth required for food-specific compliance demands. This forces businesses to create workarounds or maintain separate systems, creating inefficiencies and increasing error risks.
Companies using custom development report significant improvements in several critical areas:
- Precise regulatory compliance with food-specific standards and reporting requirements
- Streamlined audit preparation with automated documentation and centralised record-keeping
- Improved incident response times through real-time alerts and designated workflows
- Enhanced data security with role-based access controls tailored to your organisation
- Reduced operational downtime by identifying and addressing patterns before they escalate

These benefits compound over time. As Q-Hub's clients have discovered, the initial investment in custom development typically pays dividends through reduced compliance costs, fewer incidents, and more efficient operations.
Crucial Features That Transform Food Safety Compliance
When designing custom incident reporting systems for food businesses, certain features prove consistently valuable. These capabilities directly address the unique challenges of maintaining food safety while supporting operational efficiency.
Real-time incident tracking stands out as particularly critical in food environments, where contamination or safety issues can escalate rapidly. Custom solutions can monitor and report incidents as they happen, enabling immediate response to potential risks before they affect consumers or production.
The most effective custom solutions also include:
- Automated alerts that notify relevant personnel about critical events instantly
- Role-specific dashboards providing exactly the information each user needs
- Seamless integration with existing ERP or quality management systems
- Industry-specific templates aligned with HACCP, ISO 22000 and other frameworks
These features directly address the challenges food businesses face in maintaining compliance while operating efficiently. The difference between generic and custom solutions becomes particularly evident when comparing key capabilities:
<table border="0"> <tr><th>Capability</th><th>Generic Solutions</th><th>Custom Development</th></tr> <tr><td>Audit Preparation</td><td>Manual collection from multiple sources</td><td>Automated with one-click reporting</td></tr> <tr><td>Compliance Updates</td><td>Periodic with manual implementation</td><td>Real-time with automated workflows</td></tr> <tr><td>Multi-site Management</td><td>Limited with separate instances</td><td>Comprehensive with unified oversight</td></tr> </table>Real-World Success: How Custom Solutions Transform Operations
The proof of custom development's value lies in the transformative results achieved by food businesses who've implemented tailored solutions. These case studies highlight the practical benefits of bespoke incident reporting systems.
Scottish Leather Group provides an excellent example of transformative digital implementation. Before partnering with Q-Hub, they struggled with paper-based systems that made compliance with multiple ISO standards inefficient and resource-intensive. Their custom solution unified processes across multiple sites and digitised critical workflows.
The results were remarkable: audit preparation time dropped dramatically, compliance management became seamless, and interdepartmental communication improved significantly. By implementing Q-Hub's Audit Hub, they gained efficient management of audits across multiple standards with pre-built templates and automated schedules.
Another instructive example comes from Rocal Insulating Panels, whose paper-based accident reporting system created significant operational bottlenecks. Managers struggled with incomplete records and lengthy delays in closing investigations. After implementing a custom solution, reporting became faster and more detailed, with real-time access to all relevant data.
As Rocal discovered, digital transformation delivered measurable improvements:
- Reduced time spent on document retrieval from hours to seconds
- Decreased accident investigation completion time by over 60%
- Improved visibility of safety metrics across all departments
- Enhanced employee engagement in safety reporting
The User Experience Factor: Why Interface Design Matters
Even the most powerful incident reporting system fails if people don't use it properly. That's why user-friendly interfaces are essential for successful implementation in food environments – particularly on production floors where conditions can be challenging and time is limited.
Q-Hub's approach prioritises intuitive design that requires minimal training while maximising adoption. This is crucial in food production environments where staff turnover can be high and digital literacy varies significantly across teams.
Effective interfaces for food sector incident reporting should include:
- Simplified navigation with clear visual cues for essential functions
- Mobile-optimised design for reporting directly from production areas
- Customisable dashboard views tailored to different roles and responsibilities
- Language support for diverse workforces common in food production
When staff can report incidents quickly and accurately without interrupting their workflow, compliance improves naturally. This is why Q-Hub focuses extensively on user experience design in our custom development projects.
Seamless Integration: The Foundation of Operational Excellence
Custom incident reporting solutions deliver their greatest value when they connect seamlessly with existing business systems. This integration eliminates data silos and creates a unified information ecosystem that supports both compliance and operational efficiency.
For food businesses, integration typically involves connecting reporting systems with production management software, quality control platforms, and enterprise resource planning (ERP) systems. This comprehensive connectivity provides crucial context for incident data.
Q-Hub's clients have experienced significant benefits from integration, including:
- Automated tracking of temperature, humidity and other critical parameters
- Streamlined workflows that eliminate duplicate data entry
- Centralised reporting dashboards showing holistic operational health
- Improved traceability throughout production and distribution
Integration also future-proofs your incident reporting system. As your business evolves and adopts new technologies, a well-designed custom solution can adapt and incorporate these changes without requiring complete replacement.
As regulatory demands increase and consumer expectations around food safety continue to rise, custom development offers food businesses a significant competitive advantage. Q-Hub's specialised expertise in creating tailored digital solutions helps organisations not just meet compliance requirements but transform them into operational strengths that support sustainable growth.
Ready to revolutionise your food safety incident reporting with a solution designed specifically for your unique processes? Discover how Q-Hub's custom development approach can enhance compliance while streamlining operations across your organisation.
Start using Q-Hub today
- Manage compliance in one place
- Streamline your teams and tasks
- Use Q-Hub free for 30 days