
Custom Automation Tools Transform Incident Reporting Efficiency
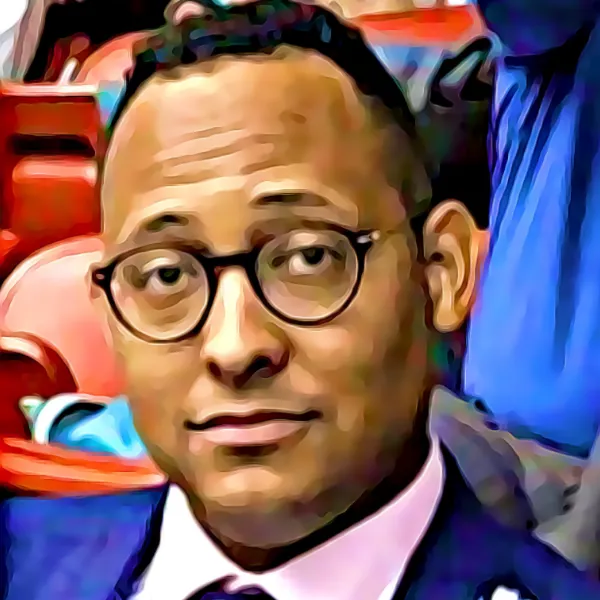

Custom Automation Tools Transform Incident Reporting Efficiency
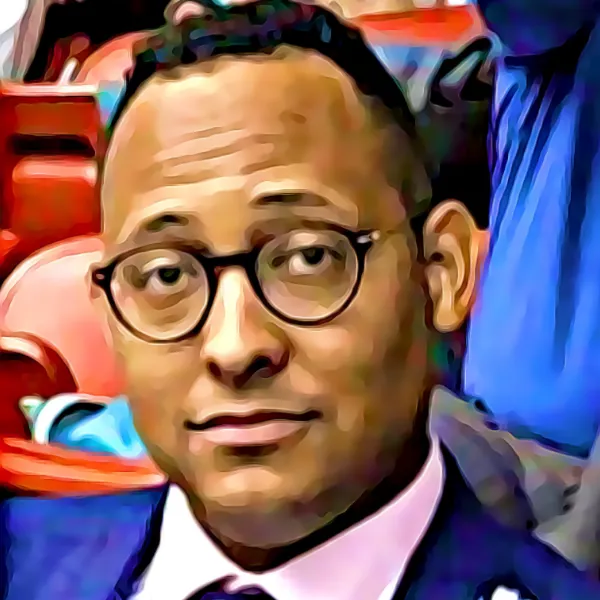
The Role of Custom Automation Tools in Pharmaceutical Incident Reporting
Incident reporting in pharmaceutical manufacturing forms the cornerstone of product integrity, patient safety, and regulatory compliance. Manual reporting systems often struggle with complex processes and documentation, creating opportunities for human error. Custom automation tools from specialists like Q-Hub transform these challenges, streamlining workflows and ensuring consistency. These tailored systems reduce errors, accelerate response times, and safeguard against compliance risks—making them essential rather than optional in today's pharmaceutical landscape.
Automation doesn't just make incident reporting easier; it fundamentally transforms how manufacturers respond to and learn from production anomalies.
Automation tools address key pain points by standardising data entry, ensuring uniform reporting structures, and enabling real-time notifications. When integrated with production systems like SCADA, these tools can automatically detect anomalies, notify stakeholders, and initiate corrective actions without manual intervention—creating seamless transparency and precision throughout the incident management lifecycle.
Revolutionising Response Times Through Intelligent Monitoring

Custom automation tools have transformed pharmaceutical incident management by eliminating manual bottlenecks. These systems provide real-time monitoring capabilities that track every stage of the incident management process as it happens, delivering instant insights when they matter most.
Automated notifications serve as an early warning system, immediately alerting relevant personnel when incidents occur. Imagine a critical deviation being flagged within seconds—this rapid response capability prevents minor issues from cascading into major problems. The system doesn't just passively record; it actively guides the response.
Regulatory compliance becomes significantly more manageable with these tools. Systems designed to align with EMA, FDA, and MHRA requirements ensure every report meets necessary standards. Standardised templates create consistent, audit-ready documentation that reduces inspection risks and penalties.
Here are the essential capabilities these systems offer:
- Real-time alerts for immediate incident response
- Automated categorisation based on incident severity
- Compliance tracking aligned with industry regulations
- Secure data protection for sensitive information
- Streamlined report generation for consistent documentation

By combining these features, pharmaceutical manufacturers can drastically reduce errors while enhancing data integrity. The administrative burden decreases substantially, allowing teams to focus on maintaining product quality and patient safety rather than paperwork.
Transforming Compliance from Burden to Strategic Advantage
In pharmaceutical manufacturing, regulatory compliance isn't optional—it's fundamental to operations. Manual processes remain vulnerable to human error and inconsistent reporting, which can trigger costly consequences from regulatory bodies like the FDA and EMA.
Q-Hub's automation solutions streamline compliance tasks by ensuring complete, accurate documentation that meets regulatory standards. This becomes particularly valuable during audits, where documentation gaps can result in severe penalties. Real-time validation processes immediately flag discrepancies, allowing teams to address issues before they escalate.
These systems create audit readiness by generating standardised reports that satisfy requirements across multiple regulatory agencies. By reducing administrative overhead, teams can shift focus from managing paperwork to enhancing product quality—a strategic advantage in a competitive market.
<table border="0"> <tr><th>Compliance Metric</th><th>Before Automation</th><th>After Automation</th></tr> <tr><td>Audit Preparation Time</td><td>5-7 days</td><td>Hours</td></tr> <tr><td>Documentation Errors</td><td>15-30%</td><td><5%</td></tr> <tr><td>Incident Resolution Time</td><td>Days-Weeks</td><td>Hours-Days</td></tr> <tr><td>Regulatory Findings</td><td>Frequent</td><td>Rare</td></tr> </table>Real-World Success Stories: Measuring Tangible Results
When a UK-based pharmaceutical manufacturer implemented SCADA automation, the impact was immediate and measurable. Prior to this solution, their manual processes created delays in identifying production anomalies, leading to extended downtime and compliance risks with MHRA guidelines.
After implementation, incident resolution times decreased by 40%, allowing teams to address issues before they escalated. Data accuracy improved dramatically as automated capture eliminated typical manual errors. The system's ability to flag compliance risks in real-time kept the company audit-ready, while reducing downtime costs delivered ROI within just one year.
Similarly, a global pharmaceutical company struggling with data discrepancies adopted a tailored incident analytics platform from Q-Hub. This system offered advanced categorisation, real-time notifications, and automated reporting that integrated with their existing IT infrastructure.
The results were compelling—reporting errors dropped by 30%, transforming audit compliance from a stressful scramble into a streamlined process. The platform also revealed patterns in recurring issues, enabling proactive improvements that enhanced overall efficiency and significantly reduced costs.
The Intelligence Revolution: AI and the Future of Incident Reporting
Artificial intelligence and machine learning are transforming incident reporting from reactive to proactive. These technologies analyze historical data to identify patterns that might indicate future incidents, enabling preventative action before problems occur.
As these tools evolve, data security has become increasingly sophisticated. Advanced encryption and multi-layered security frameworks protect sensitive pharmaceutical data from breaches or tampering. This protection is essential for maintaining both regulatory compliance and stakeholder trust in an industry where data integrity is paramount.
How AI Enables Predictive Incident Management
AI systems continuously analyze operational data, identifying subtle patterns that might indicate developing issues. For example, if production equipment shows slight deviations under specific conditions, the system flags this as a potential risk before it becomes a reportable incident. This shift toward prediction rather than reaction represents a fundamental change in pharmaceutical risk management.
Looking ahead, the integration of AI, big data, and machine learning will create even more sophisticated incident management systems. Future platforms will likely not only predict risks but also suggest specific corrective actions based on global pharmaceutical data trends—redefining compliance by positioning companies ahead of evolving regulations rather than merely responding to them.
Measuring the Bottom-Line Impact of Automation
Q-Hub's custom automation tools deliver measurable improvements in productivity and efficiency. By streamlining processes previously bogged down by manual tasks, pharmaceutical companies eliminate bottlenecks and accelerate report processing. This productivity boost allows teams to focus on critical tasks rather than repetitive data entry.
These solutions also drive significant cost savings by minimizing errors, reducing rework, and preventing costly compliance violations. A system that automatically categorizes incidents and generates audit-ready reports drastically reduces administrative overhead. Over time, these efficiency gains translate into substantial financial benefits—making automation a strategic investment rather than simply an operational expense.
Beyond immediate benefits, automation creates a foundation for long-term operational excellence. Enhanced data accuracy provides better insights for decision-making, empowering teams to identify recurring issues and optimize overall performance. These improvements align operations with strategic goals like faster product delivery and higher quality standards.
Companies implementing Q-Hub's automation solutions gain a competitive advantage through faster incident resolution, reduced downtime, and improved compliance. In an industry where reputation depends on precision, these advantages enhance standing with regulators, stakeholders, and customers alike. Ready to transform your incident reporting processes with Q-Hub's tailored digital solutions? Discover how custom automation can elevate your compliance standards while driving operational excellence.
Start using Q-Hub today
- Manage compliance in one place
- Streamline your teams and tasks
- Use Q-Hub free for 30 days