
Custom Automation Tools Streamlining Food Safety Tasks
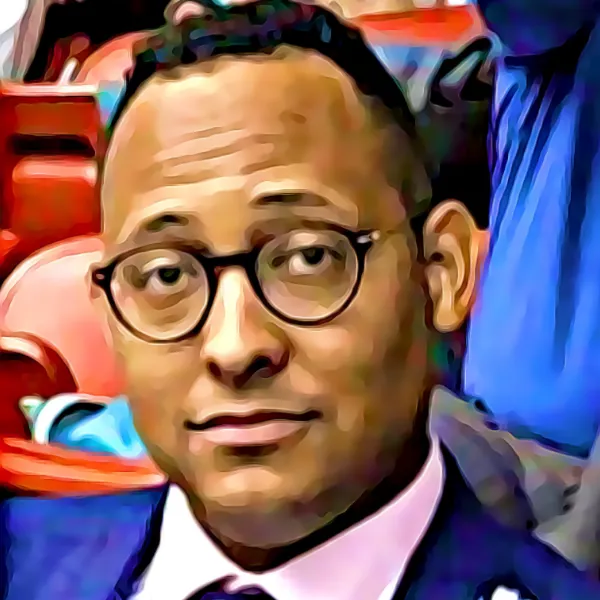

Custom Automation Tools Streamlining Food Safety Tasks
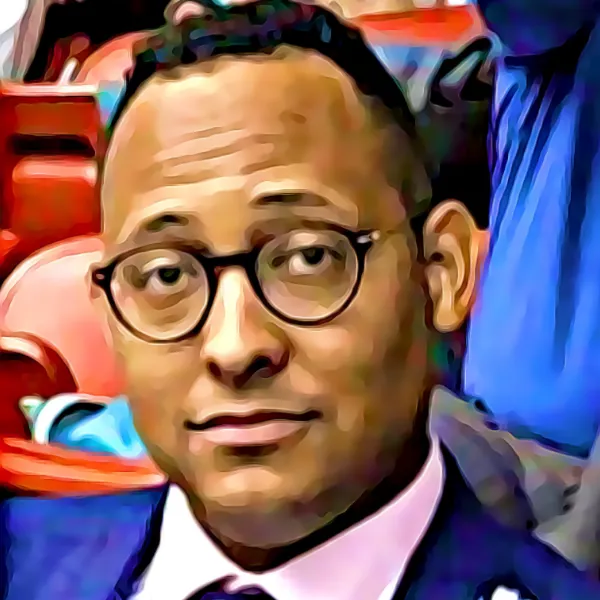
How Custom Automation Tools are Streamlining Safety Management in Food Manufacturing
In today's competitive food manufacturing landscape, custom automation tools are revolutionising safety management practices. Q-Hub's digital solutions are transforming how manufacturers handle complex safety protocols by replacing error-prone manual processes with streamlined digital workflows. These tailored systems dramatically reduce human error while ensuring consistent compliance with industry regulations—something traditional paper-based methods simply cannot match.
At their core, these smart systems digitise critical safety tasks including hazard analysis, compliance documentation, and quality inspections. Rather than relying on clipboards and spreadsheets, food producers can now manage these processes through integrated platforms that connect with existing enterprise systems. This creates a unified ecosystem where potential issues are identified before they escalate into serious problems.
"When implemented correctly, automation tools can reduce safety incidents by up to 25% while improving audit compliance scores by as much as 40%." Source: Food Safety Magazine
Let's explore how these powerful tools are transforming food safety management and delivering measurable results across the industry.
The Hidden Cost of Manual Safety Management
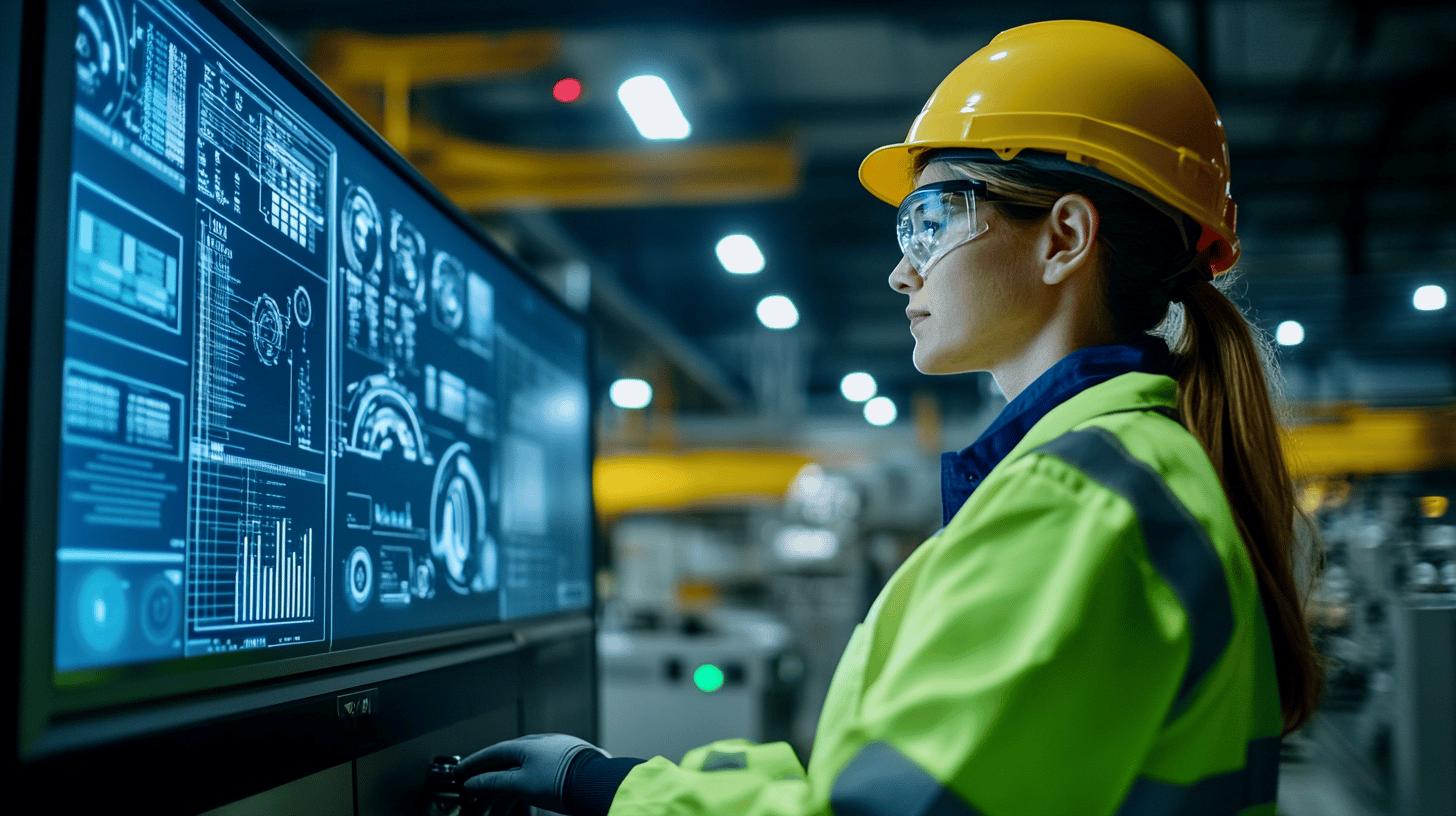
Traditional safety management in food manufacturing relies heavily on paper forms, manual checks, and disconnected systems. This approach might feel familiar, but it creates significant hidden costs that impact both safety and productivity.
Human error is perhaps the most concerning issue. Even your most diligent employees occasionally make mistakes when repetitively filling out forms or conducting manual inspections. These small oversights can potentially lead to contamination risks, product recalls, or compliance violations.
The administrative burden is another major drain. Staff often spend hours on paperwork instead of focusing on more valuable activities. I've seen quality managers who dedicate entire days just preparing documentation for audits—time that could be spent improving processes instead.
Delayed response to safety issues is another critical weakness of manual systems. Without real-time monitoring, problems might go undetected until they've already affected product quality or caused equipment failures. By then, the damage is already done.
Companies embracing automation typically experience the following benefits:
- Enhanced compliance: Automated systems ensure consistent adherence to regulations like HACCP, FSMA and ISO 22000, with up-to-date documentation always available
- Significant time savings: Routine safety tasks that once took hours can be completed in minutes through digital workflows
- Improved traceability: Digital systems create comprehensive records that allow for instant recall management and accountability
- Data-driven decisions: Access to real-time safety metrics enables proactive risk management rather than reactive responses
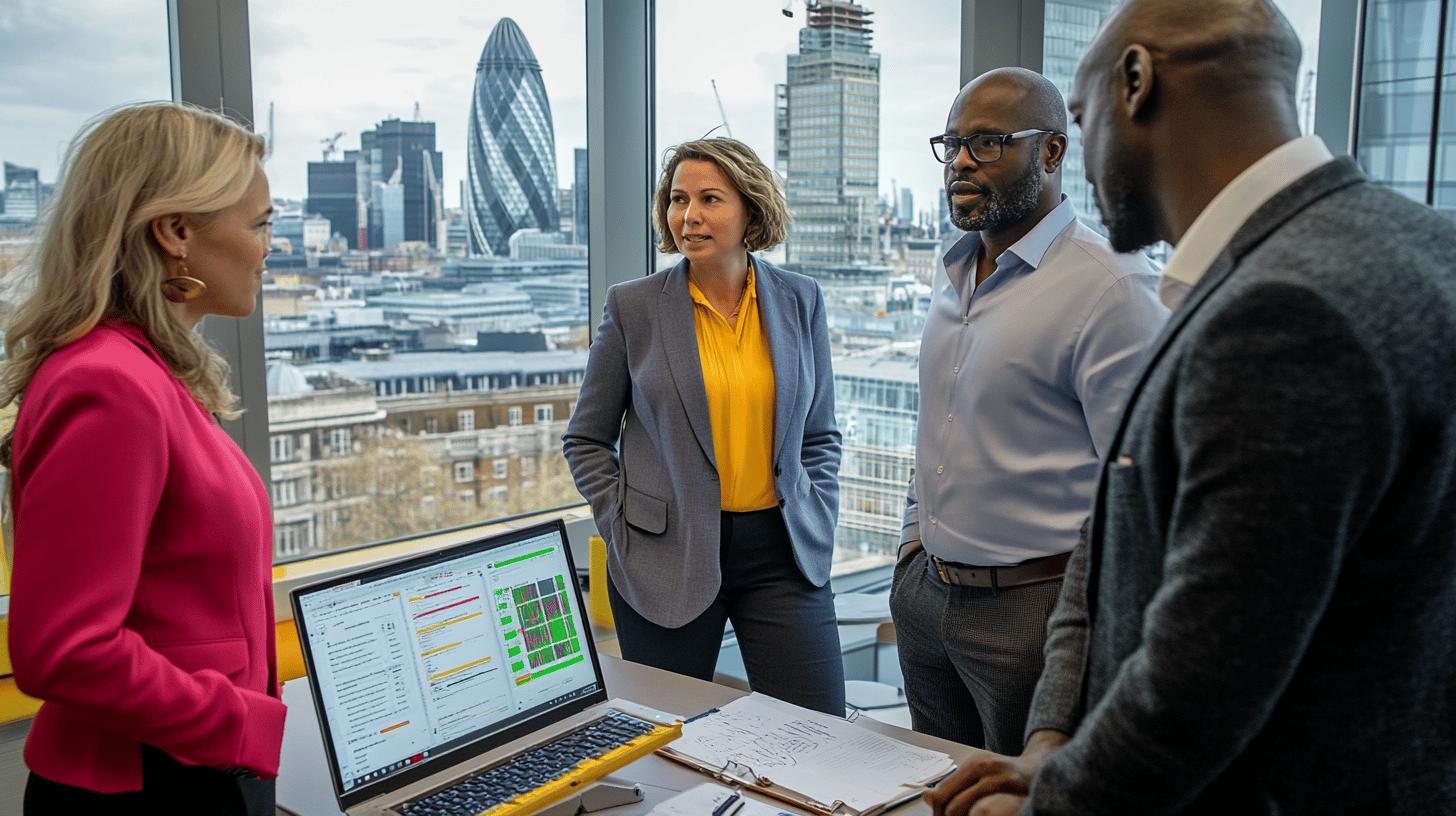
Transforming Food Safety Through Intelligent Automation
What makes automation tools so effective for food manufacturers? The answer lies in how they fundamentally change safety management from a reactive process to a proactive one. Q-Hub's digital solutions integrate multiple safety functions into a cohesive system that anticipates problems before they occur.
Automated quality checks represent one of the most valuable features. Rather than relying on spotty manual inspections, these systems continuously monitor critical control points according to predefined parameters. When something falls outside acceptable ranges—like temperature fluctuations in cold storage—the system immediately alerts relevant personnel.
Real-time hazard analysis tools also dramatically improve risk management. They systematically evaluate potential threats throughout the production process, from raw material handling to finished product storage. This consistent approach eliminates the variability that comes with human judgment alone.
Customisable dashboards give managers instant visibility into safety performance across their operation. Instead of waiting for monthly reports, they can identify trends, spot problems, and implement corrective actions immediately. This visual approach makes complex data accessible and actionable.
Key Features of Effective Food Safety Automation Tools
Automated quality checks: Ensures consistent adherence to safety standards without constant human oversight
Digital documentation management: Centralises all compliance records with version control and audit trails
Real-time monitoring: Provides continuous visibility into critical control points throughout production
Mobile accessibility: Allows safety checks to be performed on the floor via smartphones or tablets
Integration capabilities: Connects with existing business systems to create a unified data environment
Real-World Success: From Challenges to Transformation
The practical impact of automation on food safety management is best illustrated through real-world examples. While each implementation is unique, certain patterns emerge that demonstrate how these tools deliver tangible benefits.
Consider how automation transformed safety management for Weston Aerospace. Although not a food manufacturer, their experience with compliance management offers valuable lessons. Before implementing Q-Hub's solutions, they struggled with time-consuming manual processes for quality control and compliance documentation. After digitising these workflows, they experienced dramatic improvements in audit readiness and compliance visibility.
Similarly, Scottish Leather Group faced challenges managing complex ISO standards across multiple sites—a situation familiar to many food manufacturers. By implementing Q-Hub's Audit Hub and Doc Hub solutions, they unified their compliance processes and significantly reduced preparation time for regulatory inspections.
These implementations weren't without challenges. Staff resistance initially slowed adoption at both companies, but comprehensive training and demonstrating clear benefits eventually won employees over. The key was showing how automation supported their work rather than replacing it.
<table border="0"> <tr><th>Metric</th><th>Before Automation</th><th>After Automation</th></tr> <tr><td>Audit Preparation Time</td><td>3-5 days</td><td>4-6 hours</td></tr> <tr><td>Documentation Retrieval</td><td>20-30 minutes</td><td>Seconds</td></tr> <tr><td>Safety Incident Response</td><td>Hours/Days</td><td>Minutes</td></tr> <tr><td>Compliance Visibility</td><td>Monthly reports</td><td>Real-time dashboards</td></tr> </table>Seamless Integration: The Key to Effective Implementation
The most successful automation implementations share one crucial characteristic: seamless integration with existing systems. When safety management tools work alongside your ERP and SCM systems, the value multiplies exponentially.
Q-Hub's approach to integration focuses on creating connections that eliminate data silos between departments. This means your production data, quality metrics, and safety records all flow into a unified system, giving you complete visibility across operations.
Cloud-based deployment offers particular advantages for food manufacturers with multiple facilities. Teams can access safety information from anywhere, whether they're on the production floor or at a remote location. This flexibility proved especially valuable for companies like Fowlers of Bristol, who needed to centralise communications across different teams.
But what about legacy systems? Many food manufacturers worry about compatibility with existing technology investments. Customisable APIs (Application Programming Interfaces) address this concern by creating bridges between modern automation tools and older systems. This means you can modernise your safety management without replacing your entire technological infrastructure.
Overcoming Implementation Hurdles
While the benefits of automation are clear, implementing these tools does come with challenges. Understanding these potential obstacles—and how to overcome them—is essential for successful adoption.
Staff resistance often tops the list of concerns. Many employees worry that automation might make their roles redundant or dramatically change how they work. The solution lies in comprehensive training that emphasises how these tools enhance rather than replace human expertise. Involving team members early in the selection process also increases buy-in.
Initial investment costs can also seem daunting. However, when viewed against the potential costs of compliance failures, product recalls, or safety incidents, the return on investment becomes much clearer. Many companies find that phased implementation helps manage upfront expenses while still delivering incremental benefits.
Integration complexities present technical challenges, especially for companies with legacy systems. Q-Hub addresses this through customisable solutions that adapt to existing infrastructure rather than forcing complete system overhauls. This approach minimises disruption while maximising benefit.
Companies considering automation should approach implementation as a strategic transformation rather than merely a technical project. Success depends on addressing both the technological and human aspects of change management.
The Future of Food Safety: Beyond Basic Automation
As automation technology continues to evolve, we're seeing exciting new developments that will further transform food safety management. Predictive analytics represents the next frontier, using historical data to forecast potential safety issues before they occur.
Artificial intelligence and machine learning are enhancing the capabilities of automation systems, enabling them to identify patterns and anomalies that might escape human notice. These technologies don't replace human judgment but rather augment it with data-driven insights.
Mobile technologies are making safety management more accessible and immediate. Staff can conduct inspections, report issues, and access critical information from tablets or smartphones, increasing efficiency and responsiveness.
The integration of Internet of Things (IoT) sensors throughout production facilities is creating unprecedented visibility into environmental conditions and equipment performance. These connected devices continuously monitor critical parameters and feed data into central safety management systems.
Ready to transform your food safety management with custom automation tools? Q-Hub offers comprehensive digital solutions designed specifically for the unique challenges of food manufacturing. Our platform streamlines compliance, enhances operational efficiency, and provides the real-time visibility needed to maintain the highest safety standards in today's competitive market.
Start using Q-Hub today
- Manage compliance in one place
- Streamline your teams and tasks
- Use Q-Hub free for 30 days