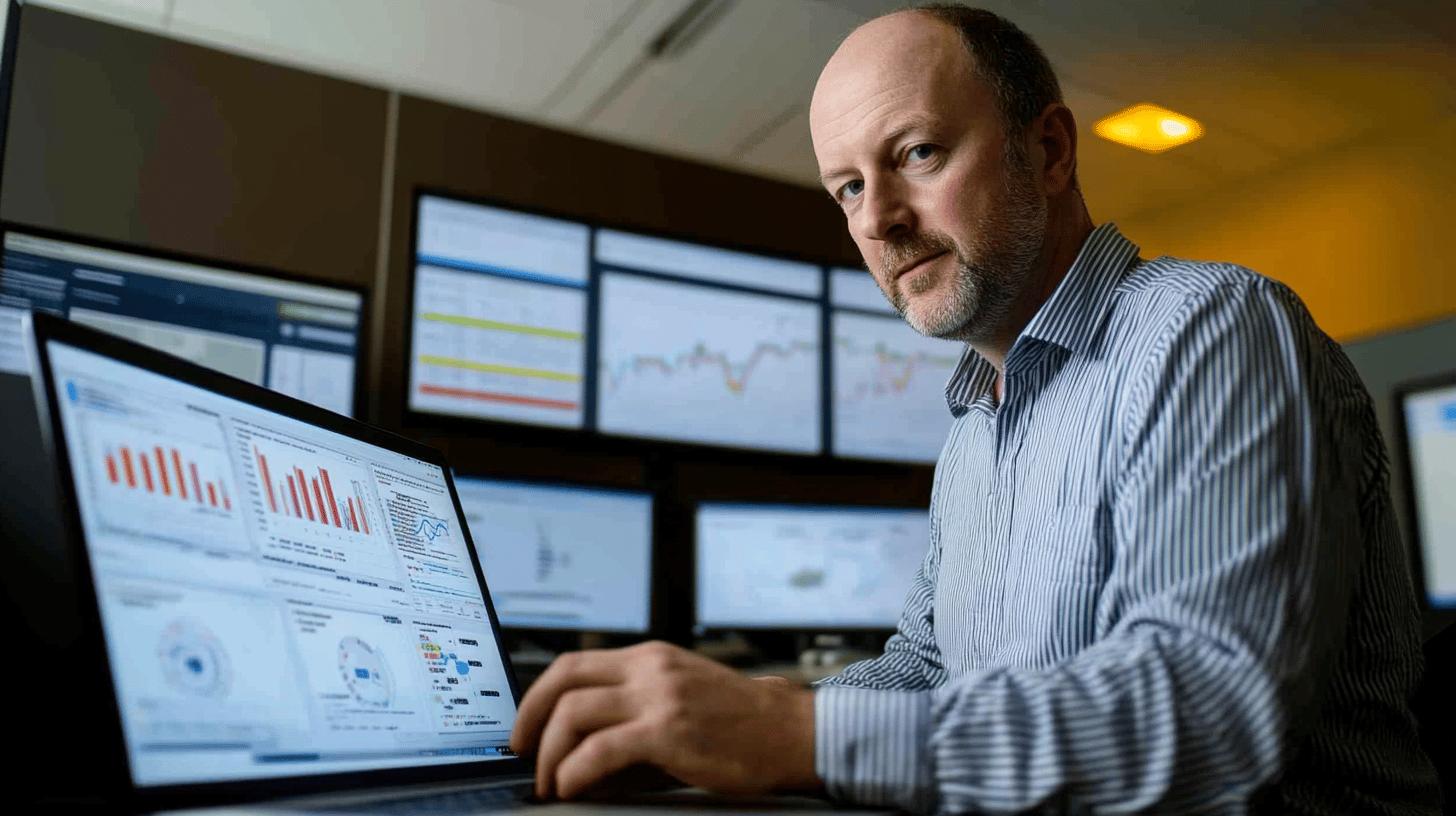
Custom Automation Tools Boost Engineering Reporting Efficiency
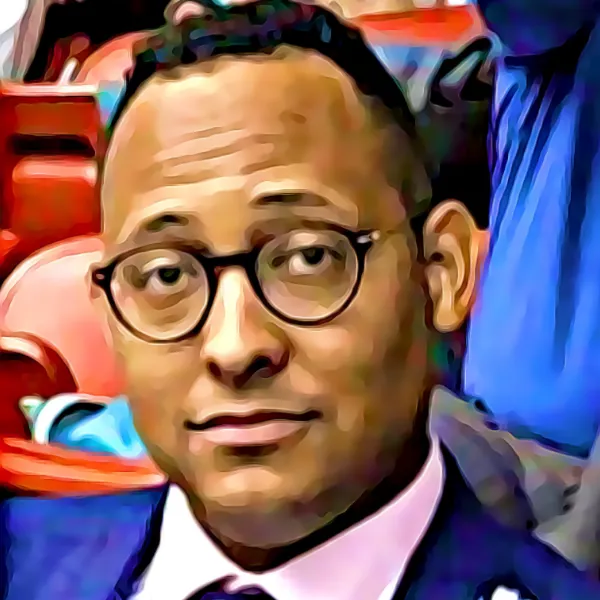
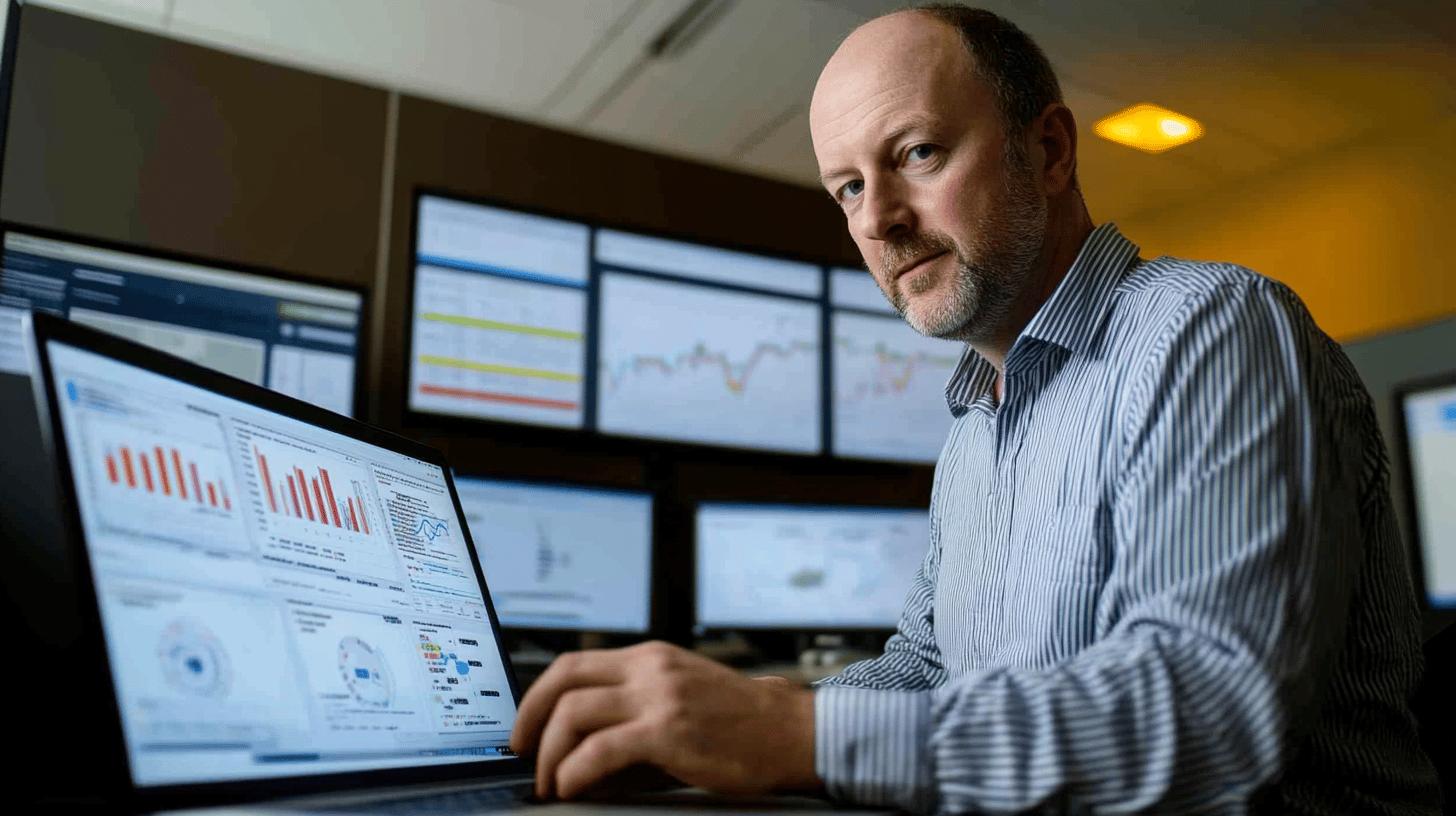
Custom Automation Tools Boost Engineering Reporting Efficiency
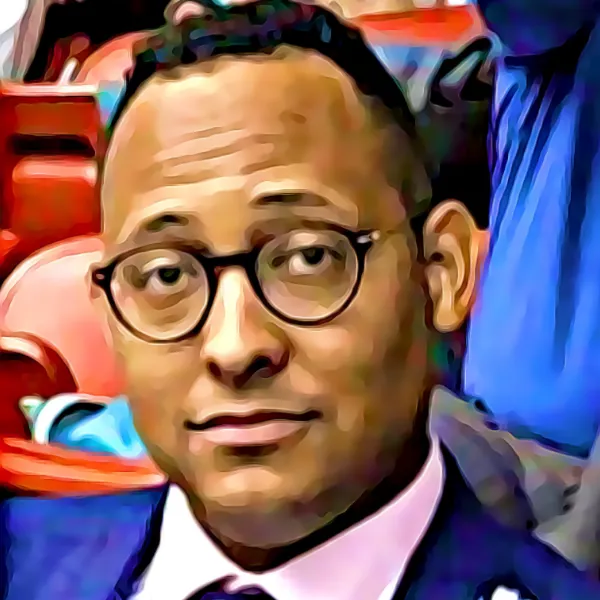
How Custom Automation Tools Enhance Incident Reporting Efficiency in Engineering Operations
Custom automation tools are revolutionising incident reporting in engineering operations, offering a strategic advantage over traditional manual processes. Q-Hub's bespoke automated solutions streamline workflows and significantly reduce the time teams spend documenting incidents. By eliminating repetitive tasks and standardising reporting procedures, these systems minimise human error while ensuring compliance with evolving industry standards. The impact is immediate—reduced Mean Time to Detection (MTTD) and Mean Time to Resolution (MTTR), enabling engineering teams to respond with unprecedented speed and accuracy.
Manual incident reporting creates substantial challenges for engineering teams, including inconsistent documentation and delayed responses that compromise workplace safety. Automation addresses these issues by ensuring systematic logging and intelligent prioritisation of incidents. When critical events occur, Q-Hub's systems immediately categorise them by severity and alert relevant personnel, drastically reducing response times. The real-time insights generated also help teams identify patterns and implement preventative measures before problems escalate.
Beyond Efficiency: The Strategic Impact of Automated Reporting
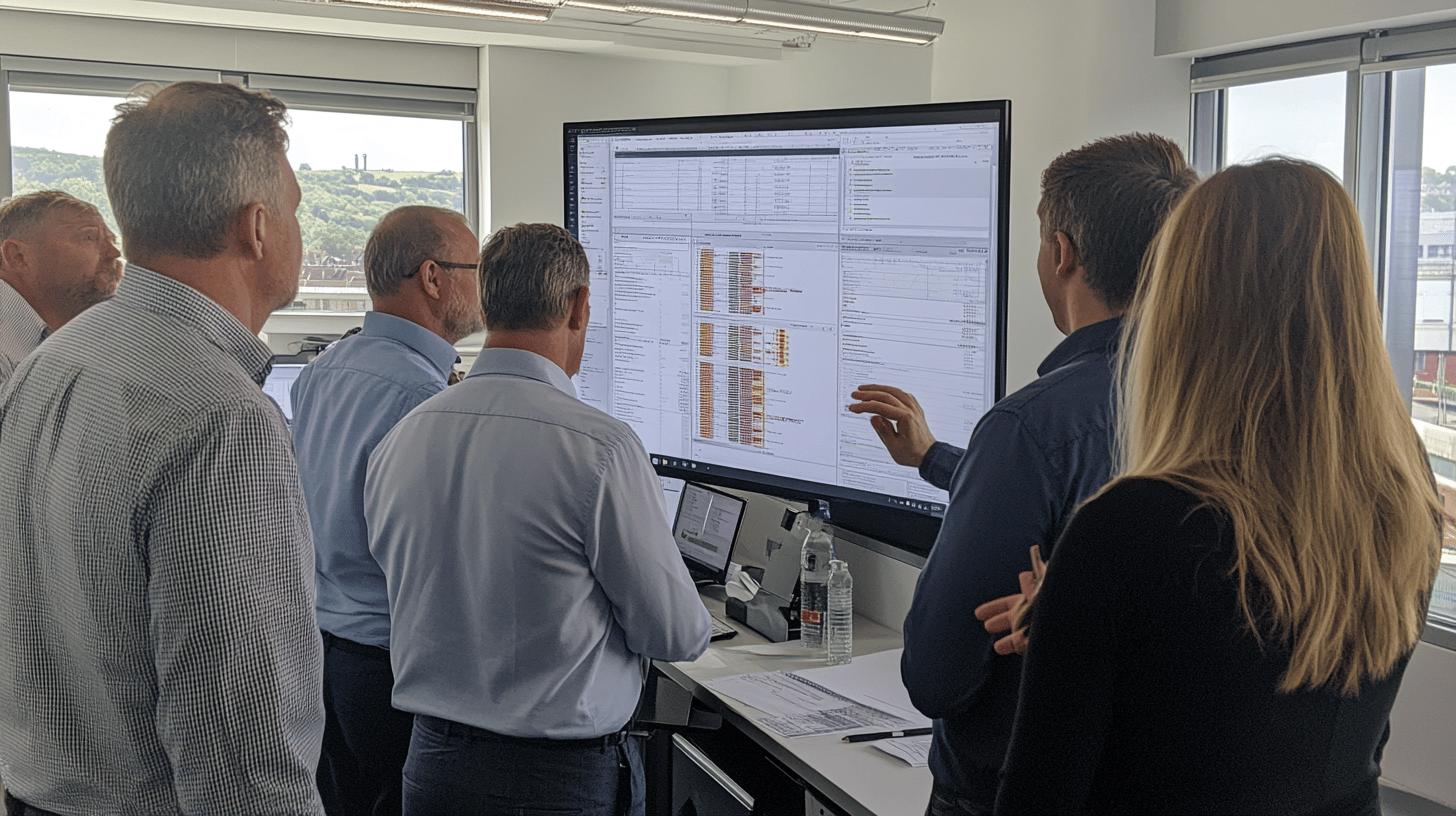
When engineering operations implement tailored automation solutions, they don't just save time—they fundamentally transform their approach to safety and compliance. Companies using Q-Hub's incident management systems typically experience up to 60% faster incident resolution and 40% fewer recurring issues.
The shift from reactive to proactive incident management has been transformative for our operations. What once took hours now happens in minutes, allowing our teams to focus on prevention rather than constantly fighting fires.
Benefits of custom automation extend beyond immediate time savings. Engineering teams using Q-Hub's solutions report significant improvements in data quality, enabling more informed decision-making and enhanced safety cultures. The consistency automated systems provide is particularly valuable in heavily regulated industries where documentation quality directly impacts compliance.
- Faster detection and resolution of incidents
- Improved data accuracy and reliability
- Enhanced compliance with industry regulations
- Reduced manual effort and administrative overhead
- Real-time reporting for proactive decision-making
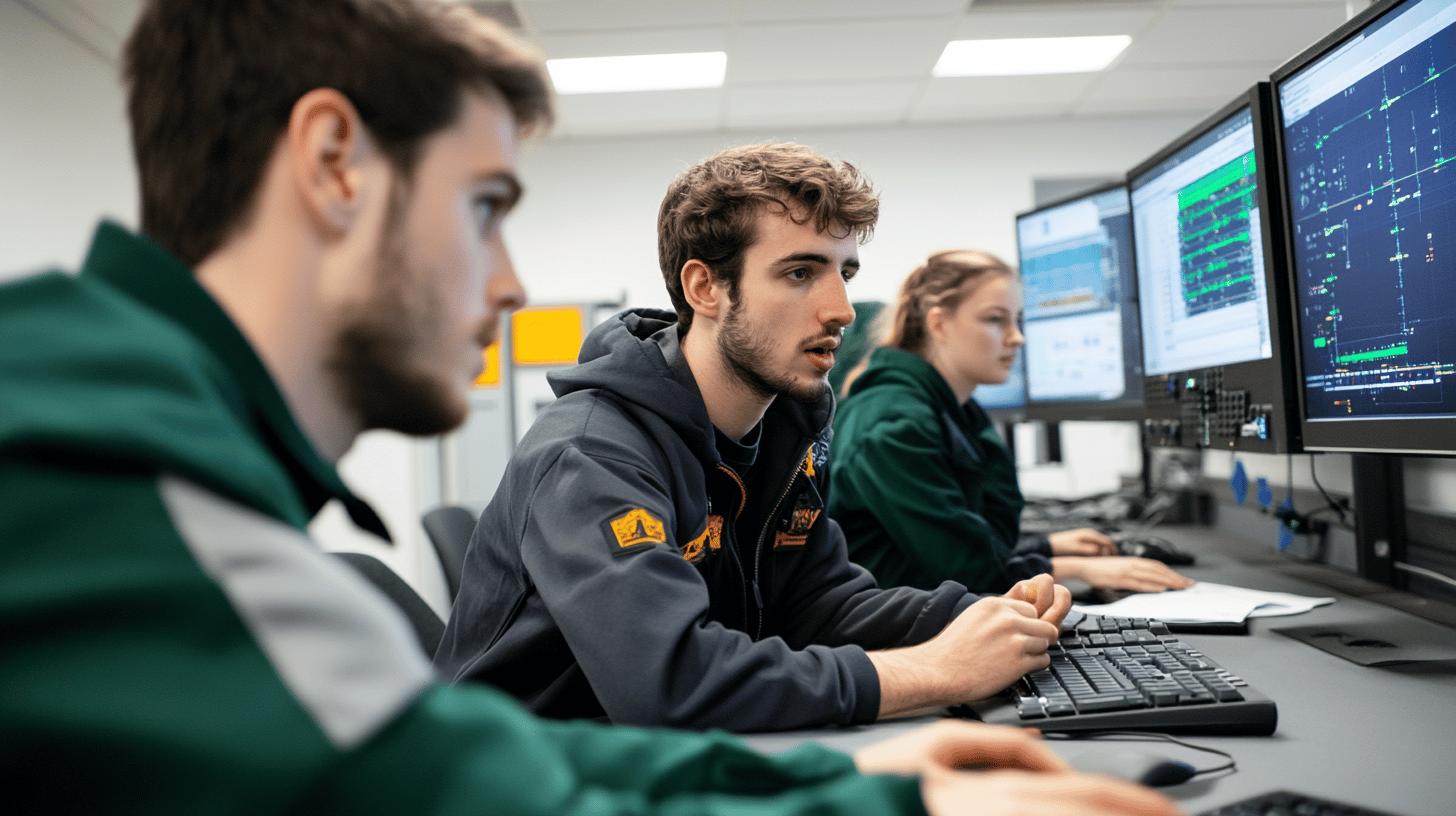
The Role of Customised Software Development in Incident Reporting
Customised software development has transformed how engineering teams handle incident reporting. Unlike generic solutions, Q-Hub's bespoke reporting systems align precisely with specific operational requirements, significantly enhancing their effectiveness. These tailored platforms streamline critical processes like data collection and analysis, ensuring complete visibility across incidents.
Off-the-shelf systems typically lack the flexibility needed for complex engineering environments, where subtleties in workflows can make tremendous differences in outcomes. Q-Hub's customised solutions integrate seamlessly with existing systems, allowing engineering teams to address inefficiencies directly while maintaining regulatory compliance. This tailored approach helps businesses shift from reactive incident management to proactive risk mitigation.
Building Systems That Grow With Your Organisation
A significant advantage of Q-Hub's bespoke reporting systems is their ability to evolve alongside organisational needs. As engineering teams expand or regulatory requirements change, the software adapts without disruption, preserving operational continuity. This scalability is particularly valuable in industries like aerospace and manufacturing, where regulatory landscapes shift frequently.
For instance, Weston Aerospace implemented Q-Hub's customised incident reporting solution to help manage their complex compliance requirements. The platform's ability to align with ISO standards while providing flexible workflows eliminated bottlenecks in their quality management processes. Engineers now resolve incidents 40% faster while maintaining higher documentation standards.
<table border="0"> <tr><th>Benefit</th><th>Description</th></tr> <tr><td>Enhanced Integration</td><td>Seamlessly connects with existing enterprise systems</td></tr> <tr><td>Scalability Features</td><td>Adapts to organisational growth and regulatory changes</td></tr> <tr><td>Compliance Support</td><td>Meets industry-specific standards (ISO 9001, ISO 45001, etc.)</td></tr> <tr><td>Tailored Analytics</td><td>Provides insights relevant to unique engineering challenges</td></tr> </table>Key Features of Automated Incident Reporting Tools for Engineering Teams
Modern incident reporting tools are transforming how engineering teams manage safety and compliance. Q-Hub's solutions provide comprehensive incident tracking capabilities that ensure nothing falls through the cracks. Unlike traditional systems that rely on manual inputs, these automated tools offer real-time notifications and intuitive dashboards that significantly reduce reporting time while enhancing data accuracy.
Intelligent Workflows That Eliminate Bottlenecks
The most effective incident reporting systems incorporate intelligent workflow automation. Q-Hub's platform automatically routes incidents to appropriate team members, tracks resolution progress, and escalates issues when necessary. This eliminates the delays typical in manual systems where incidents might sit unaddressed in someone's inbox or on a desk.
For example, Scottish Leather Group implemented Q-Hub's incident management solution to streamline their ISO compliance processes. The system's automated workflows reduced their audit preparation time from days to hours while ensuring consistent documentation across multiple sites. This transformation allowed their safety team to focus on prevention rather than paperwork.
- Real-time notifications for instant incident awareness
- Customisable reporting templates that ensure complete data capture
- Integration with collaboration tools like Teams and Slack
- Advanced analytics for identifying incident patterns
- Automated workflows for consistent resolution processes
- Secure audit trails that simplify compliance requirements
How Automation Reduces Incident Response Times in Engineering Operations
Custom automation tools have dramatically transformed incident response times in engineering environments. By eliminating manual steps and standardising workflows, Q-Hub's solutions enable immediate detection and response to critical incidents. The impact is substantial—what once took hours now happens in minutes, allowing engineering teams to minimise downtime and reduce safety risks.
From Hours to Minutes: The Time-Saving Reality
The efficiency gains from automation are perhaps most evident in the incident notification process. When incidents occur in an automated environment, the system instantly identifies the event, categorises its severity, and alerts appropriate personnel. This immediate response capability eliminates the delays inherent in manual reporting chains.
Fowlers of Bristol experienced this transformation firsthand after implementing Q-Hub's incident reporting solution. Their previous manual system required multiple handoffs and paperwork completion before response teams were notified—often taking 30+ minutes for critical incidents. With automation, notifications now reach response teams in under 60 seconds, dramatically reducing potential impact.
<table border="0"> <tr><th>Metric</th><th>Before Automation</th><th>After Automation</th></tr> <tr><td>Incident Detection</td><td>10-30 minutes</td><td>Instant</td></tr> <tr><td>Team Notification</td><td>5-15 minutes</td><td>Under 1 minute</td></tr> <tr><td>Resolution Workflow</td><td>1-3 hours</td><td>30-60 minutes</td></tr> </table>Implementation Strategies for Custom Automation Tools in Engineering
Successfully implementing custom automation tools requires thoughtful planning and a phased approach. Q-Hub's implementation methodology focuses on minimising disruption while maximising adoption. Rather than attempting a complete system overhaul, the most successful engineering teams identify high-impact processes to automate first, creating quick wins that build momentum for broader changes.
Creating a Foundation for Sustainable Change
Integration with existing systems is often the most challenging aspect of implementation. Q-Hub's specialists work with engineering teams to map current workflows and identify integration points before any technical work begins. This preparation ensures automation enhances rather than disrupts established processes, reducing resistance and accelerating adoption.
Rocal Insulating Panels followed this approach when implementing Q-Hub's incident reporting solution. Their team began by automating accident investigations—a process that previously caused significant delays and inconsistencies. By starting with this high-visibility process, they demonstrated immediate value to stakeholders before expanding automation to other areas like near-miss reporting and safety inspections.
- Assess existing workflows to identify automation priorities
- Select tools that align with operational requirements
- Integrate with current systems using established APIs
- Conduct focused pilot tests with key stakeholders
- Provide comprehensive training for all system users
- Monitor performance metrics and refine as needed
Case Studies: Real-Life Examples of Automation in Engineering Incident Reporting
Custom automation tools have transformed incident reporting for numerous engineering operations. Q-Hub's solutions have helped organisations overcome common challenges like delayed reporting, inconsistent documentation, and ineffective follow-up processes. The results consistently demonstrate substantial improvements in both efficiency and safety outcomes.
Transforming Safety Management Through Digital Innovation
Anglia Cathodic Protection Services faced significant challenges managing their incident reporting processes as their business grew. Their paper-based systems created bottlenecks in documenting and resolving safety issues, particularly across multiple sites. After implementing Q-Hub's digital incident management solution, they experienced dramatic improvements in visibility and accountability.
The platform's automated workflows ensured incidents were properly documented, routed to appropriate personnel, and tracked through resolution. This eliminated communication gaps and ensured consistent follow-up. According to their Safety Manager, "What previously took days now happens automatically, allowing our team to focus on prevention rather than paperwork chase."
BMC Analysis: From Manual Struggles to Streamlined Efficiency
BMC Analysis struggled with tracking non-conformances (NCRs) through fragmented Word documents and email chains. Implementation of Q-Hub's Process Hub transformed their workflow with automated tracking, notifications, and reporting. The system's structured approach eliminated accountability gaps and provided immediate visibility into outstanding issues. This resulted in a 40% reduction in NCR resolution time and significant improvements in regulatory compliance.
- Anglia Cathodic Protection reduced incident resolution time by 60%
- Rocal Insulating Panels improved compliance documentation by 40%
- BMC Analysis decreased recurring incidents by 35% through better tracking
Future Trends in Automation for Engineering Incident Reporting
The landscape of incident reporting automation continues to evolve rapidly, with Q-Hub at the forefront of innovation. Emerging technologies are creating new possibilities for prediction, prevention, and response that were unimaginable just a few years ago. These advancements are reshaping how engineering teams approach safety and compliance management.
AI-Powered Prevention: The Next Frontier
The most significant emerging trend is the
Start using Q-Hub today
- Manage compliance in one place
- Streamline your teams and tasks
- Use Q-Hub free for 30 days