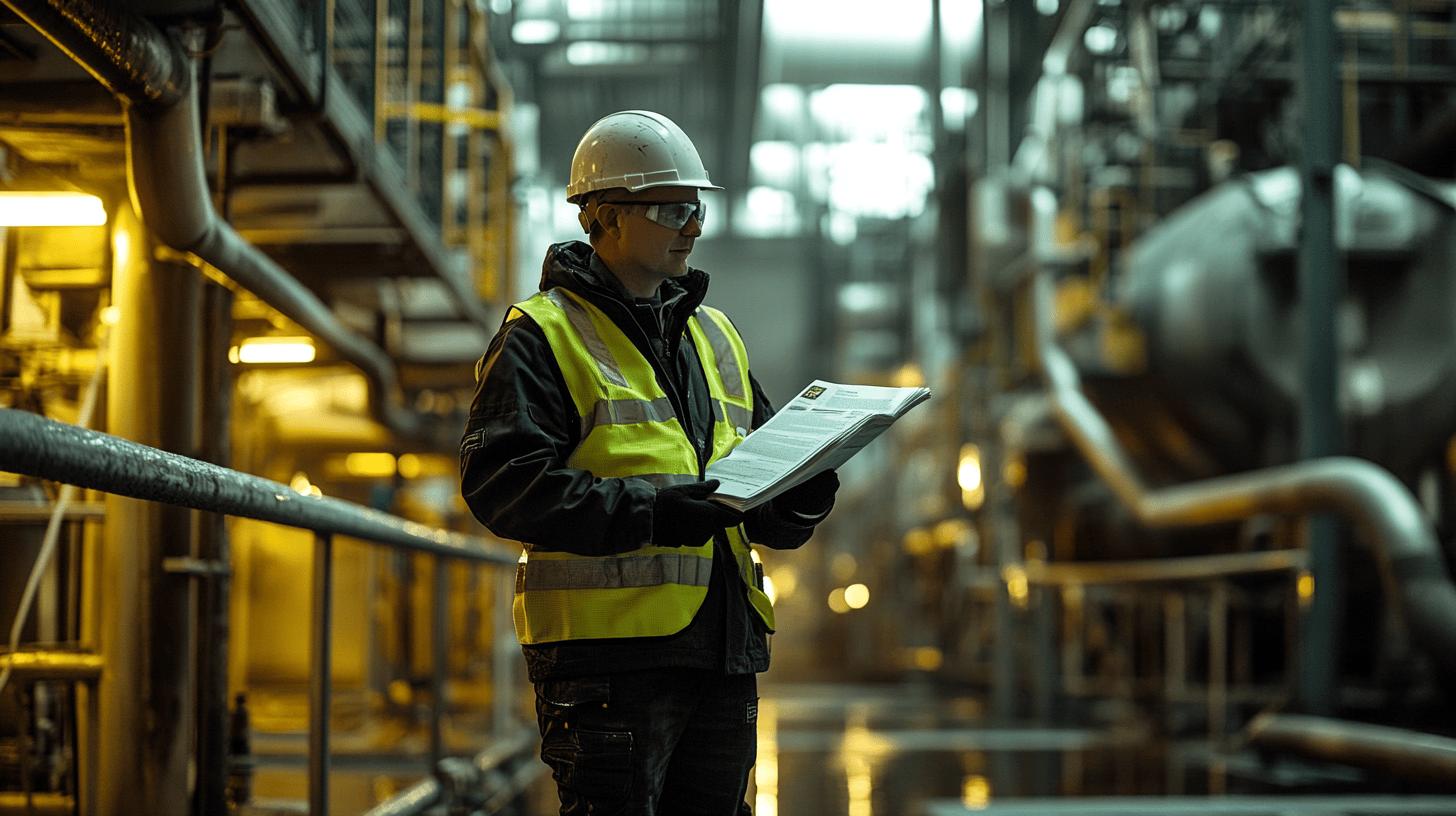
Continuous Improvement Programmes Strengthen Facility Incident Protocols
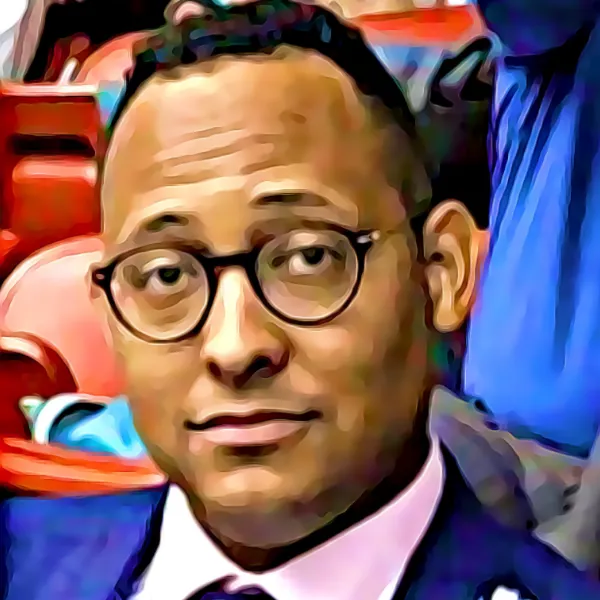
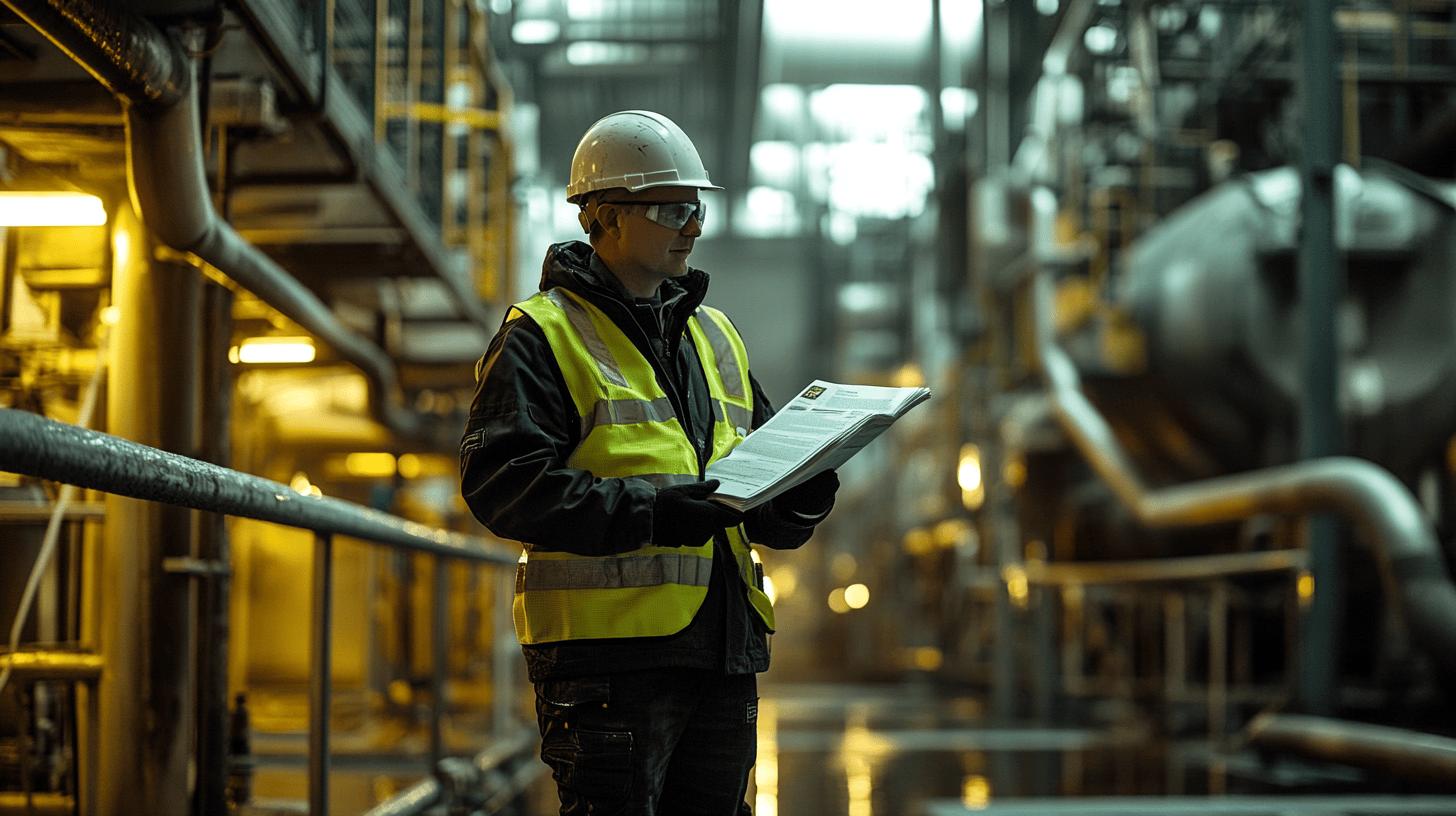
Continuous Improvement Programmes Strengthen Facility Incident Protocols
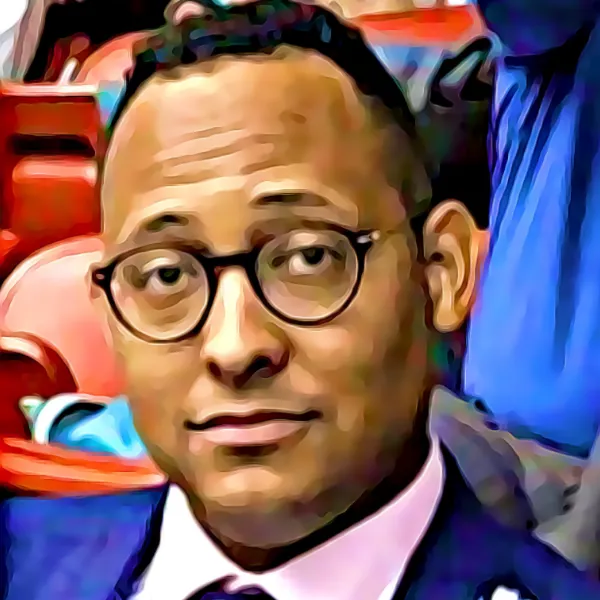
How Continuous Improvement Programmes Enhance Incident Reporting Protocols in Facilities Operations
Continuous improvement programmes (CIPs) transform incident reporting in facilities operations through systematic, iterative enhancements. Q-Hub's expertise in digital transformation shows that these programmes strengthen reporting protocols by addressing inefficiencies and embedding sustainable solutions. By incorporating feedback loops and lessons learned analyses, organisations create dynamic reporting mechanisms that adapt to changing operational needs. The result is a more robust safety culture, clearer communication channels, and standardised protocols that significantly reduce errors.
CIPs excel at uncovering gaps in existing systems that many facilities struggle with—inconsistent reporting formats, delayed submissions, and inadequate data collection. Rather than merely highlighting these issues, a structured improvement programme provides clear pathways to address them through standardised templates and strategic automation, ensuring data remains consistently reliable and actionable.
Building a Foundation for Safety Excellence
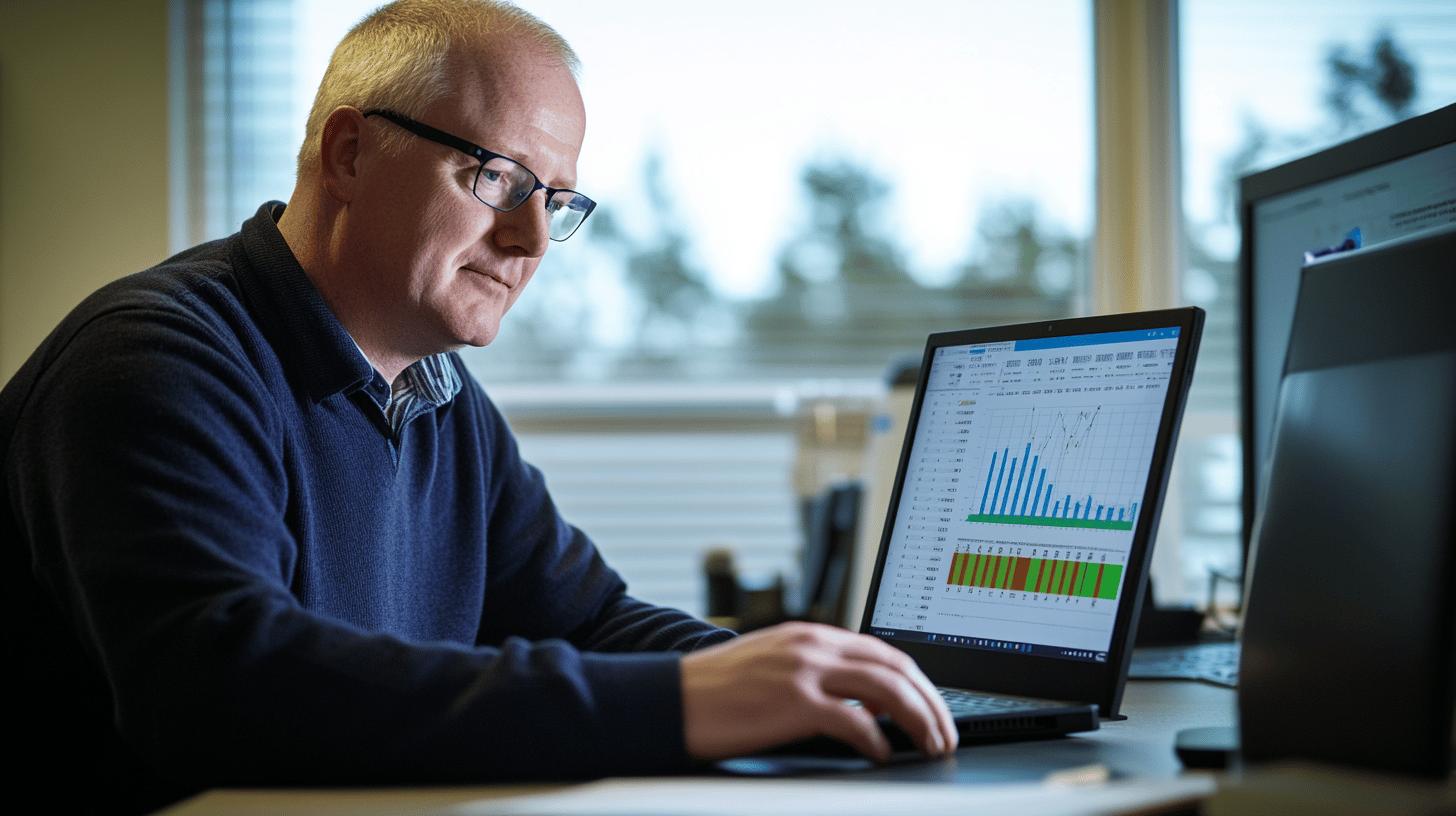
When employees see their incident reports driving meaningful changes, it fosters accountability and trust. This transforms safety from a mere compliance exercise into a shared responsibility across the organisation. The continuous improvement cycle creates an environment rich in feedback, where teams can effectively learn from past incidents to prevent future occurrences.
Our digital transformation with Qhub revolutionised our incident reporting. Document control became streamlined through a centralised digital library, eliminating hours of wasted time and improving compliance across our operations.
As demonstrated in Rocal Insulating Panels' transformation with Q-Hub, organisations can achieve remarkable improvements in safety management by implementing the right digital tools. Their paper-based system for accident reporting was completely revolutionised, enabling quicker resolution and better departmental involvement.
- Increased reporting accuracy and consistency
- Enhanced safety culture throughout the organisation
- Streamlined protocol standardisation
- Improved feedback and learning loops
- Greater operational resilience
Key Components of Effective Incident Reporting Protocols
In facilities operations, effective incident reporting protocols form the backbone of safety, compliance, and operational efficiency. Timeliness, accuracy, and clarity are foundational elements that reduce miscommunication and delayed actions. Without these essential components, reporting processes become fragmented, compromising both safety standards and organisational accountability.
Root cause analysis stands as another critical pillar in robust reporting systems. Rather than addressing surface-level symptoms, this process digs deeper into underlying causes, preventing recurrences and fostering proactive safety management. When recurring equipment failures are traced back to improper maintenance scheduling, for example, implementing a digital maintenance tracker can serve as an effective corrective measure.
Transforming Communication Through Standardisation
Standardised templates and streamlined communication channels bind incident reporting systems together. When employees have access to clear, pre-designed reporting formats, inconsistencies diminish and data capture improves. Digital platforms, reporting apps, and centralised dashboards facilitate faster response times and enhanced collaboration, ensuring incident details reach appropriate stakeholders without delay.
The Scottish Leather Group's experience with Q-Hub demonstrates this principle in action. Facing challenges managing compliance across multiple sites and ISO standards, they implemented Q-Hub's digital platform to unify processes and streamline communication. The result was enhanced compliance management and significantly improved interdepartmental communication.
Key Element | Description |
---|---|
Timeliness | Reporting incidents promptly to enable swift action |
Accuracy | Ensuring precise documentation of all incident details |
Root Cause Analysis | Identifying and addressing underlying issues |
Standardised Templates | Providing consistent formats for reporting |
Digital Communication | Enabling efficient information sharing and follow-up |
The Role of Continuous Improvement Cycles in Incident Management
Improvement cycles systematically refine incident management processes through structured methodologies like Plan-Do-Check-Act (PDCA). At their core is continuous process evaluation—an ongoing effort to identify weaknesses and ensure protocols remain relevant and effective. For instance, when facilities struggle with delayed incident responses, Q-Hub's improvement framework can identify communication bottlenecks and implement streamlined workflows, transforming reactive incident handling into proactive management.
Measuring Success Through Performance Metrics
Performance metrics tracking serves as a cornerstone of effective improvement cycles. Facilities managers rely on measurable data such as incident frequency reduction, resolution times, and recurrence rates to gauge programme success. These metrics provide actionable insights that drive meaningful improvements in safety protocols.
BMC Analysis experienced this transformation when they implemented Q-Hub's Process Hub to revolutionise their NCR management. With automated tracking and reporting, they resolved non-conformances more efficiently while gaining immediate insights through live KPIs—a significant improvement over their previous fragmented approach using Word documents and emails.
Creating Self-Reinforcing Safety Systems
Feedback loops ensure lessons learned from past incidents inform future actions. For example, when data analysis reveals equipment malfunctions occurring repeatedly due to improper maintenance, adjustments to preventive maintenance schedules can address root causes. These insights foster accountability and learning, embedding resilience into operational systems.
Weston Aerospace exemplifies this approach in their journey with Q-Hub. Their legacy systems created bottlenecks in key operations, with NCRs often delayed in resolution due to manual tracking. By digitising these processes through Q-Hub's platform, they gained real-time visibility into resolution progress, enabling faster and more accurate decision-making.
Best Practices for Strengthening Incident Reporting Through CIPs
Strengthening incident reporting protocols through continuous improvement programmes requires both structured strategies and dynamic adaptability. Q-Hub specialises in creating improvement frameworks that address inefficiencies while embedding sustainable solutions, ensuring reporting processes remain accurate, timely, and actionable.
Empowering Staff Through Continuous Training
Continuous training forms the foundation of robust reporting frameworks. Well-trained employees provide more accurate and timely reports because they understand both how to report incidents and why accurate reporting matters. Regular training sessions help staff avoid common pitfalls like incomplete entries or delayed submissions, particularly when using standardised digital reporting tools.
Anglia Cathodic Protection Services experienced this benefit firsthand when implementing Q-Hub's platform. By digitising their fragmented paper and spreadsheet-based systems, they made compliance processes more accessible and actionable for all employees, eliminating bottlenecks and enhancing operational oversight.
Securing Leadership Buy-in for Lasting Change
Leadership involvement signals that safety and accountability are organisational priorities. This engagement might include reviewing incident data during management meetings, allocating resources for staff training, or supporting the implementation of digital tools. Such commitment builds trust among employees and encourages serious engagement with reporting protocols.
Regular audits and proactive monitoring complete the framework, providing structured evaluation of reporting protocols and early identification of trends or recurring problems. When combined with Q-Hub's technology solutions, such as digital dashboards and automated alerts, these practices ensure incident reporting systems remain effective and efficient.
- Implement regular, focused training sessions for all staff
- Develop awareness programmes highlighting the importance of reporting
- Secure visible leadership commitment to improvement initiatives
- Utilise digital tools for streamlined, consistent reporting
- Establish proactive monitoring systems to identify emerging issues
- Conduct regular protocol audits to evaluate effectiveness
- Encourage cross-team collaboration for problem-solving
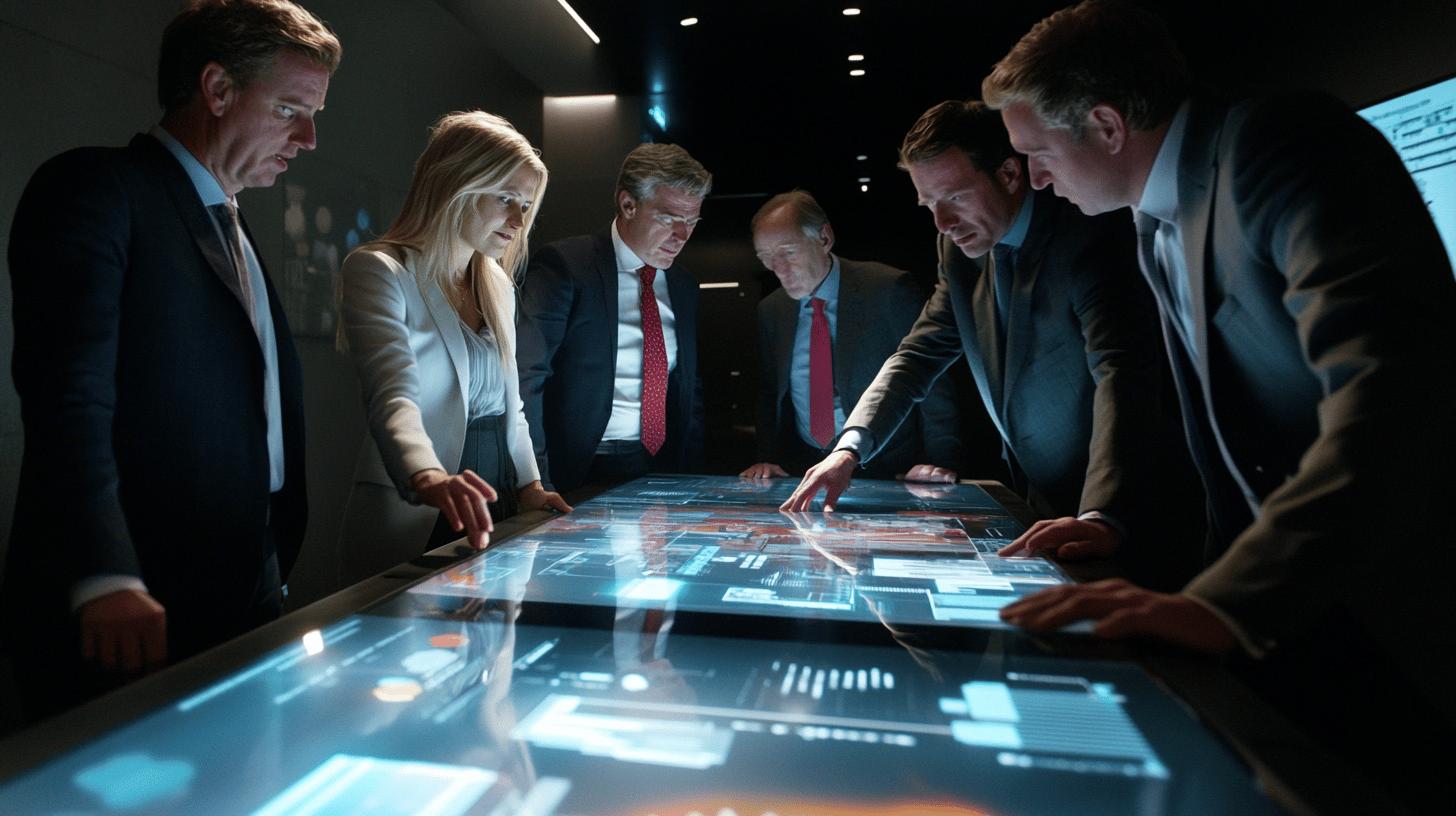
Overcoming Implementation Challenges
Implementing CIPs to refine incident reporting protocols often encounters resistance to change. Employees may hesitate to adopt new processes due to concerns about disruption or doubts regarding effectiveness. A robust change management approach is essential, beginning with early employee involvement to ensure their perspectives are heard and valued.
Clear communication about programme benefits can transform scepticism into support. For example, explaining how refined reporting leads to fewer safety incidents provides tangible motivation for adoption. Celebrating early wins further reduces resistance by demonstrating immediate benefits from initial improvements.
Maximising Resources for Sustainable Implementation
Resource allocation presents another common challenge. Without adequate funding, time, or personnel, even well-designed improvement strategies can falter. Stakeholder engagement becomes crucial to ensure CIPs receive proper prioritisation and resources. When decision-makers understand the financial and legal risks of inadequate reporting, they're more likely to support necessary investments.
Fowlers of Bristol addressed these challenges successfully during their implementation of Q-Hub. By centralising all critical workflows, datasets, and communications into a single digital space, they overcame initial resistance and created lasting improvements in their safety and quality management systems.
Leveraging Technology for Enhanced Reporting
Q-Hub's digital solutions have made continuous improvement programmes more accessible and efficient for facilities operations. Digital reporting tools enable real-time data collection, ensuring prompt and accurate incident logging. Cloud-based platforms automatically timestamp entries, reducing manual errors and creating reliable audit trails for compliance purposes.
Harnessing Data for Predictive Safety Management
Safety data analytics represent a significant advancement in incident management capabilities. These tools help facilities identify recurring trends and high-risk areas by analysing historical incident reports. This data-driven approach enables proactive decision-making, such as reallocating resources to mitigate risks before they escalate.
Rocal Insulating Panels leveraged Q-Hub's intuitive dashboards to centralise safety operations, making it easier to track near misses, daily inspections, and accident trends. This visibility extended throughout their organisation, ensuring consistent safety processes across all operational levels.
Mobile Solutions for Field-Based Reporting
Mobile reporting applications empower employees to document incidents immediately and accurately, regardless of location. This ensures no critical details are overlooked during the reporting process. When combined with AI-driven technologies that offer predictive insights, these tools create comprehensive incident management systems that exceed traditional capabilities.
Q-Hub's specialised QHSE software solutions enable organisations to transform their incident reporting protocols through strategic digital implementation. By combining continuous improvement methodologies with tailored technology, facilities can achieve heightened safety standards, operational efficiency, and regulatory compliance.
<table> <tr> <th>Improvement Area</th> <th>Before Digital Transformation</th> <th>After Q-Hub Implementation</th> </tr> <tr> <td>Document Management</td> <td>Hours spent searching through files</td> <td>Instant access via centralised library</td> </tr> <tr> <td>Incident Resolution</td> <td>Days or weeks to process</td> <td>Same-day acknowledgment and tracking</td> </tr> <tr> <td>Cross-Department Communication</td> <td>Siloed information in emails</td> <td>Real-time visibility across teams</td> </tr> <tr> <td>Compliance Reporting</td> <td>Manual compilation taking days</td>Start using Q-Hub today
- Manage compliance in one place
- Streamline your teams and tasks
- Use Q-Hub free for 30 days