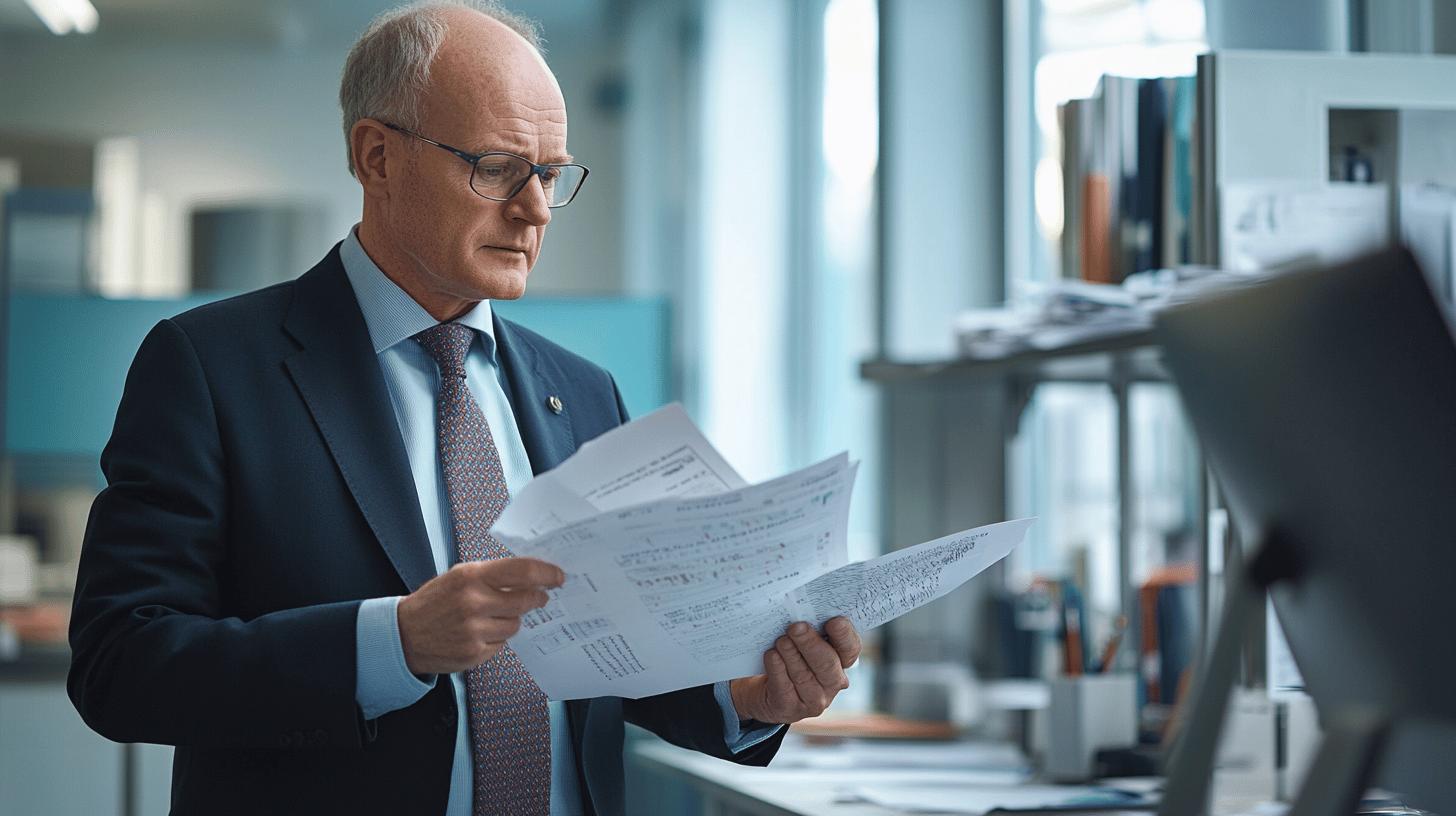
Continuous Improvement Programmes Enhance Pharma Audits
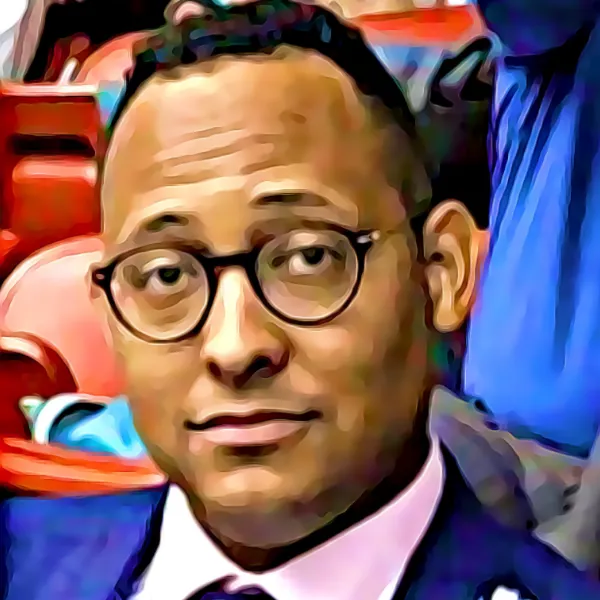
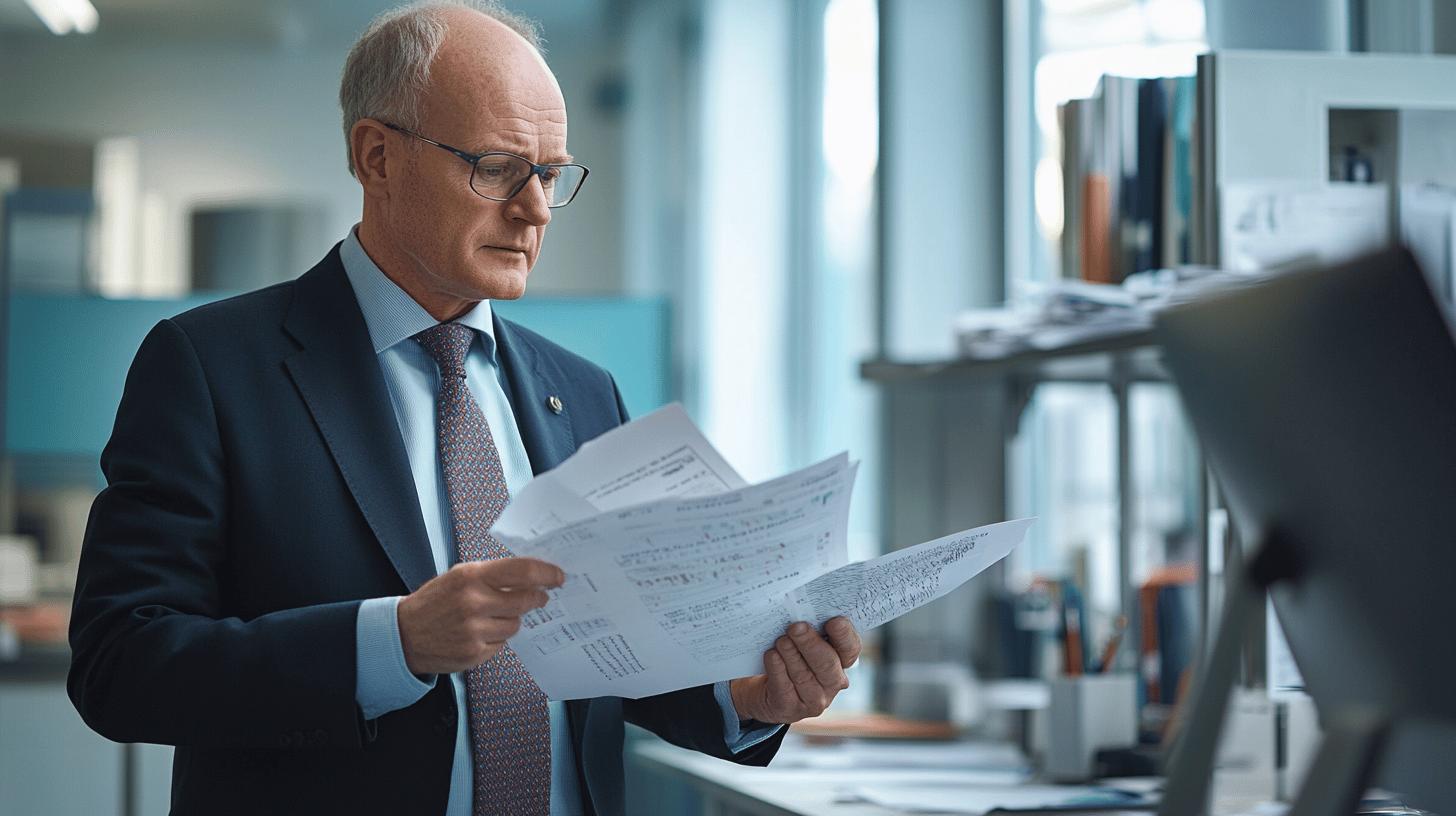
Continuous Improvement Programmes Enhance Pharma Audits
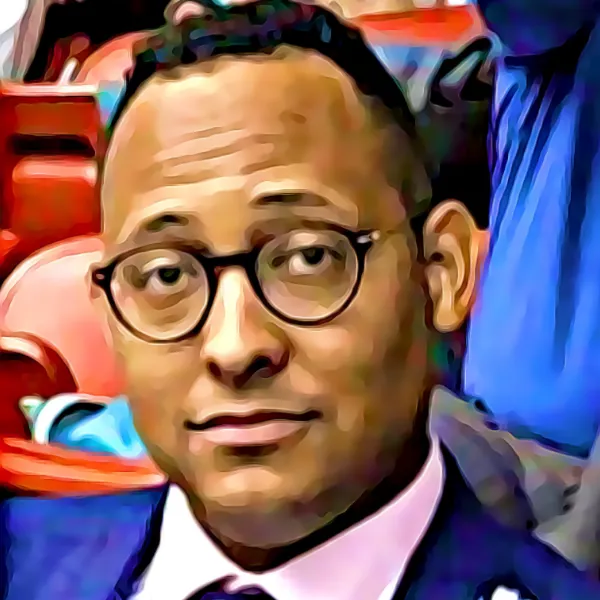
The Role of Continuous Improvement Programmes in Pharmaceutical Audits and Inspections
Continuous improvement programmes (CIPs) have revolutionised pharmaceutical audits and inspections by creating adaptive systems that ensure regulatory compliance whilst optimising processes. Unlike traditional approaches, these structured initiatives dynamically respond to evolving standards such as Good Manufacturing Practices (GMP), helping companies stay ahead of regulatory changes and avoid compliance gaps. Without CIPs, pharmaceutical organisations risk falling into reactive patterns that can compromise both operational efficiency and regulatory standing.
Building the Foundation for Excellence Through Methodology
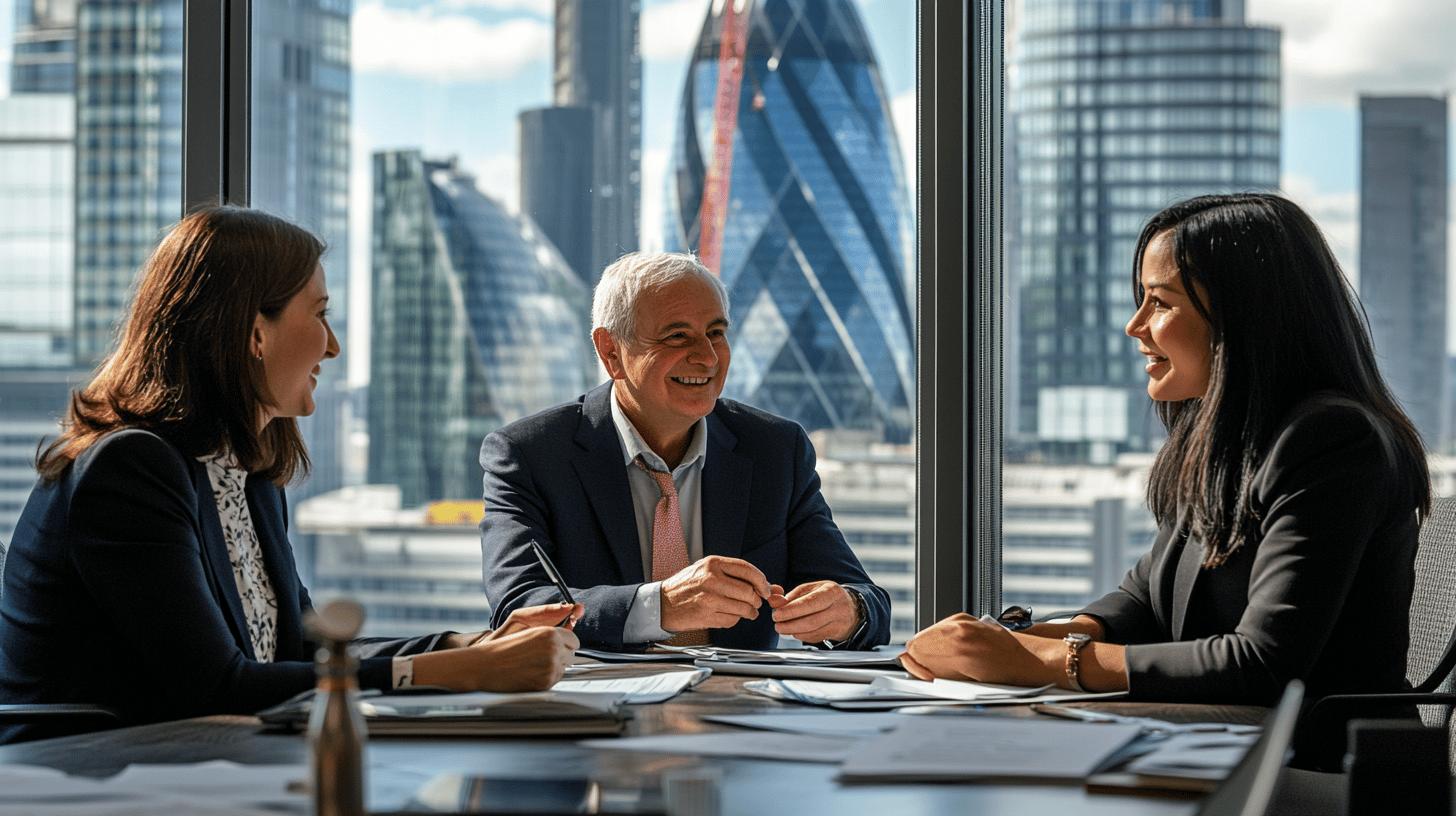
CIPs succeed by integrating proven methodologies like Six Sigma and lean management principles. Six Sigma drives data-based decisions to eliminate variability during audits, while lean management identifies and removes wasteful processes and documentation. Together, these approaches create audit-ready systems that consistently meet or exceed inspection requirements.
A typical challenge—documentation errors—demonstrates CIPs' effectiveness. When auditors flag incomplete records (a common non-compliance issue), CIPs respond with automated document control systems that ensure real-time updates and version tracking. Similarly, continuous monitoring tools embedded within CIPs provide actionable insights, allowing teams to address potential issues before external inspections occur.
Effective continuous improvement transforms audit preparation from a periodic scramble into an ongoing process of excellence that delivers consistent compliance results.
Leveraging Technology for Transformative Audit Management
Technology integration stands at the heart of modern audit excellence. Advanced audit management software centralises data, automates scheduling, and generates comprehensive reports efficiently. These platforms include automated workflows that alert teams to approaching deadlines, ensuring critical tasks remain on track. Similarly, compliance monitoring tools continuously track GMP adherence, flagging deviations before they become major issues.
Electronic document management systems (EDMS) have particularly transformed pharmaceutical audits. By automating version control and providing instant record access, these systems dramatically reduce non-compliance risks related to documentation—a notorious pain point in pharmaceutical audits.
Data analytics capabilities further enhance audit effectiveness. By analysing trends in internal findings, companies can identify recurring issues and address root causes systematically. One company working with Q-Hub reduced their audit cycle time by 30% after implementing digital document management and streamlined review workflows, while improving corrective action closure rates by 40%.
Essential Best Practices for Sustainable Improvement
Three core practices underpin effective continuous improvement in pharmaceutical audits:
- Benchmarking: Comparing internal processes against industry standards identifies improvement opportunities. Metrics like non-conformance rates and corrective action closure times pinpoint areas needing attention.
- CAPA Frameworks: These ensure issues aren't just corrected but prevented from recurring through systematic changes to processes, training, or documentation.
- Root Cause Analysis: Techniques like the "Five Whys" help teams address underlying problems rather than symptoms, creating lasting solutions.
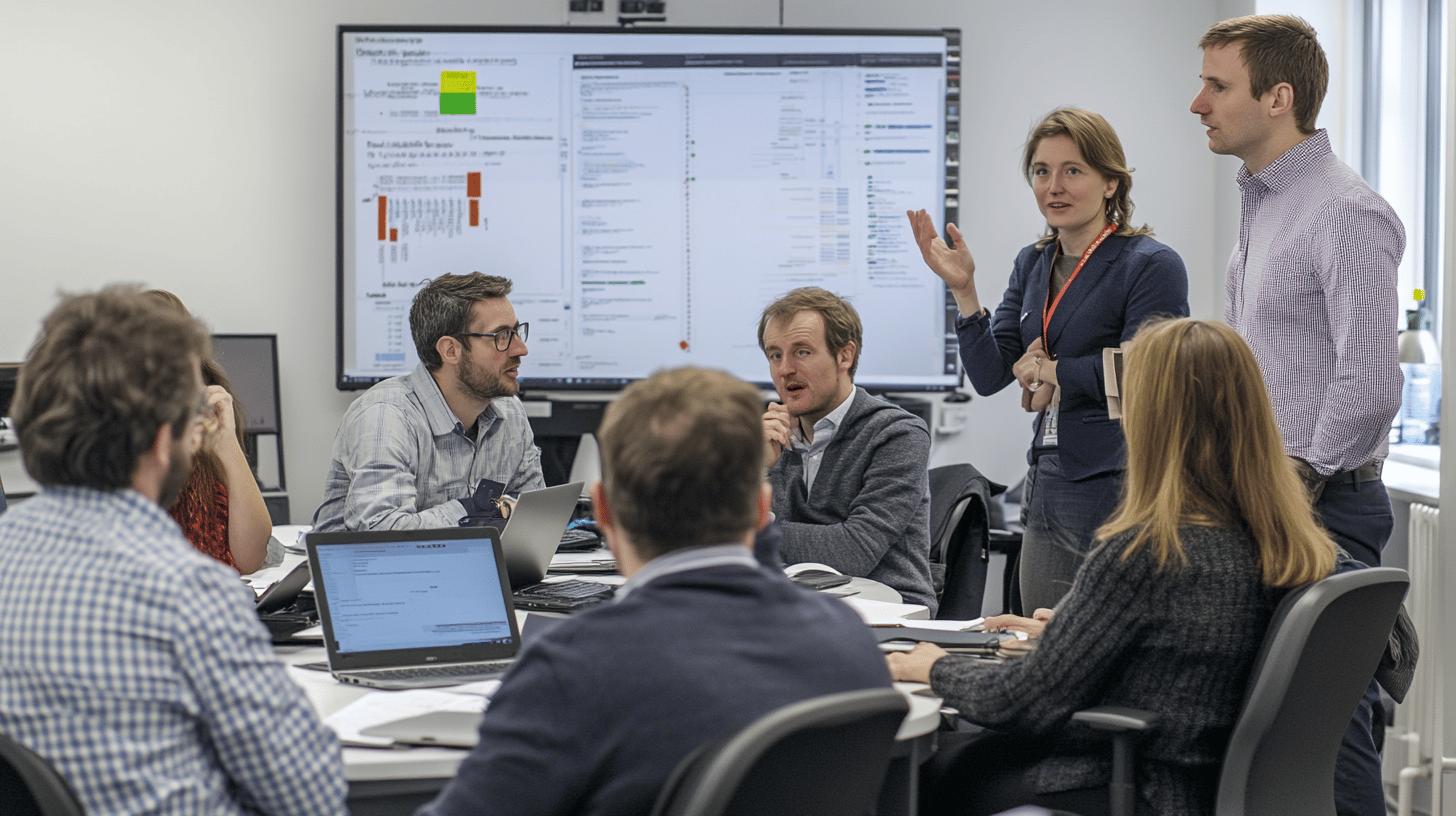
When Weston Aerospace implemented these practices through Q-Hub's platform, they transformed their audit management, centralising compliance oversight and automating previously manual processes. The digitisation allowed them to respond rapidly to findings and maintain rigorous standards across multiple ISO frameworks.
<table border="0"> <tr><th>Process Element</th><th>Before Digital CIP</th><th>After Implementation</th></tr> <tr><td>Document retrieval</td><td>Hours/days</td><td>Seconds/minutes</td></tr> <tr><td>Audit preparation</td><td>Weeks</td><td>Days</td></tr> <tr><td>Issue tracking</td><td>Manual, often delayed</td><td>Automated, real-time</td></tr> <tr><td>Compliance visibility</td><td>Limited, retrospective</td><td>Comprehensive, proactive</td></tr> </table>Regulatory Alignment Through Proactive Compliance
CIPs excel at aligning with regulatory requirements through adaptability. As regulations evolve, these programmes integrate new requirements into existing workflows without operational disruption. The shift towards data integrity standards exemplifies this advantage—companies using CIPs implement electronic quality management systems that ensure accurate data tracking and documentation, meeting compliance requirements while enhancing audit readiness.
Proactive compliance strategies, particularly internal audits, allow organisations to identify and address gaps before external inspections. When Scottish Leather Group needed to simultaneously manage multiple ISO standards, Q-Hub's digital system provided a unified platform that streamlined compliance across frameworks, making regulatory management considerably more efficient.
Fortifying Risk Management for Audit Success
Risk management fundamentally improves through CIPs. Methods like Failure Mode and Effects Analysis (FMEA) systematically evaluate potential process failures, prioritising them by severity, likelihood, and detectability. This approach enables teams to allocate resources effectively, addressing high-priority risks first.
Real-time monitoring systems further enhance risk management by providing continuous oversight of critical operations. For example, when Fowlers of Bristol implemented Q-Hub's continuous improvement platform, they gained immediate visibility into quality performance metrics, enabling them to monitor their "Right First Time" rates and proactively address deviations before they impacted compliance.
Building a Culture of Knowledge and Continuous Learning
Training and knowledge sharing remain crucial for sustained improvement. Regular workshops on regulatory updates help teams adapt to new requirements, while digital knowledge sharing platforms foster collaboration across departments. As BMC Analysis discovered when implementing Q-Hub, centralised document acknowledgment tracking ensured that staff consistently accessed the most current procedures and standards.
Digital platforms particularly excel at democratising access to compliance information. When Rocal Insulating Panels adopted Q-Hub's system, they transformed safety reporting by giving shop floor and mobile workers direct access to the reporting system. This widespread access improved accountability and engagement across all organisational levels.
The Future: AI-Powered Predictive Compliance
Looking ahead, artificial intelligence and machine learning will transform pharmaceutical audits through predictive compliance monitoring. AI algorithms will analyse historical data to identify patterns and forecast potential compliance risks before they materialise. This capability will shift audits from reactive exercises to proactive risk management tools.
Sustainability will also influence future audit strategies, with digital systems reducing resource consumption while improving efficiency. Q-Hub's solutions already demonstrate this transition, with companies like Anglia Cathodic Protection replacing paper-based systems with digital alternatives that both streamline operations and reduce environmental impact.
As regulatory complexity continues to increase, pharmaceutical companies will increasingly rely on comprehensive digital platforms like Q-Hub to maintain compliance while optimising operations. By providing unified systems for document control, audit management, and compliance tracking, these solutions help organisations not just meet standards but exceed them, turning regulatory requirements into opportunities for operational excellence.
Start using Q-Hub today
- Manage compliance in one place
- Streamline your teams and tasks
- Use Q-Hub free for 30 days