
Continuous Improvement Programmes Elevating Safety in Engineering
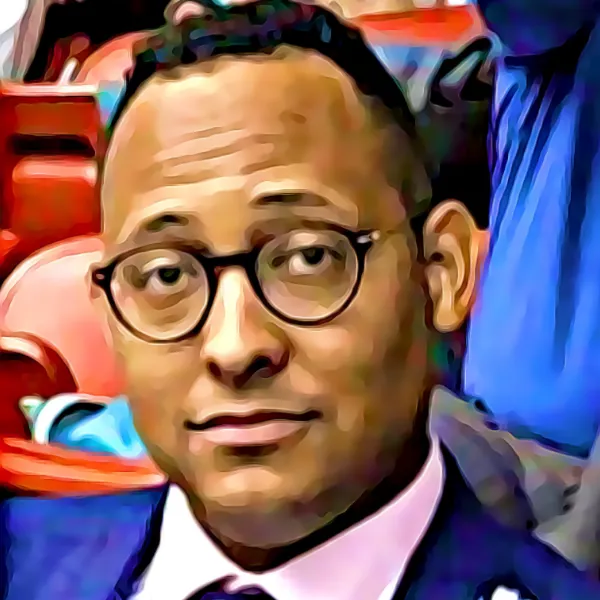

Continuous Improvement Programmes Elevating Safety in Engineering
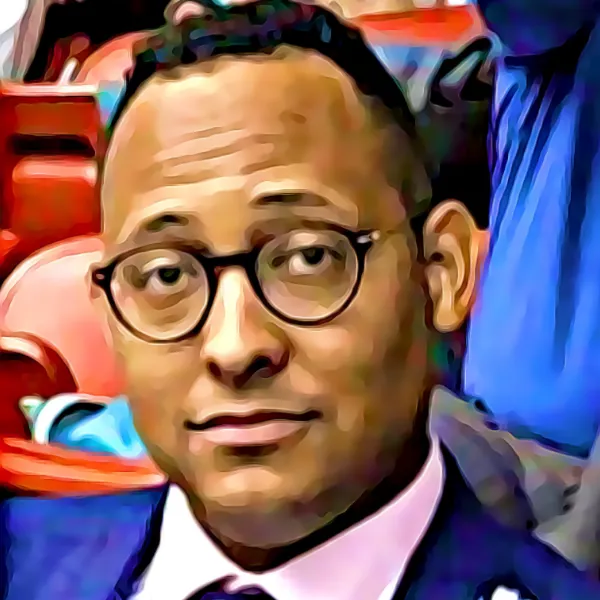
How Continuous Improvement Programmes Enhance Safety Management Protocols in Engineering
Continuous improvement programmes play a vital role in transforming safety management in engineering environments from reactive to proactive. These systematic approaches help organisations identify risks before they become incidents, streamline safety processes, and foster a culture of prevention. Q-Hub's digital solutions support these initiatives by providing the tools needed to implement, monitor, and refine safety protocols across complex engineering operations.
These methodologies, including PDCA and Six Sigma, create structured frameworks for addressing safety challenges in high-risk engineering environments. They provide the foundation for consistent improvement while ensuring compliance with essential standards like ISO 45001 for occupational health and safety.
"Organizations that implement continuous improvement programmes see up to 30% reduction in workplace incidents and significant improvements in operational efficiency." Source: Health and Safety Executive (HSE) Annual Statistics
When properly implemented, these programmes deliver tangible benefits that extend beyond mere compliance:
- Reduced workplace injuries through proactive risk identification
- Enhanced regulatory compliance with frameworks like ISO 9001 and ISO 14001
- Streamlined safety processes that eliminate redundancies
- Improved employee engagement and ownership of safety protocols
- Decreased operational downtime related to safety incidents

Let's explore how these methodologies work in practice and why they're essential for engineering organisations looking to elevate their safety performance.
The Four Pillars of Safety Excellence
Successful safety management in engineering relies on four key methodologies that work together to create comprehensive improvement. Each brings unique strengths to the table while complementing the others perfectly.
Lean principles focus on eliminating waste in safety processes, removing unnecessary steps that might create confusion or risk. For example, rethinking tool placement in a manufacturing facility can reduce unnecessary movement, directly lowering accident risk. It's about making safety protocols more efficient without compromising effectiveness.
Kaizen takes a different approach by emphasizing small, incremental changes rather than massive overhauls. In safety management, this might involve daily five-minute team huddles to discuss near-misses or weekly reviews of specific procedures. These small adjustments accumulate over time, creating significant improvements without disrupting operations.
Six Sigma brings data-driven precision to safety management by identifying patterns in incidents or near-misses. By applying statistical analysis to safety data, engineering firms can pinpoint specific risk factors - perhaps discovering that incidents increase during shift changes or when using particular equipment configurations. This insight enables targeted interventions rather than blanket solutions.
The PDCA cycle (Plan-Do-Check-Act) ties everything together by creating a framework for continuous evaluation and improvement. This methodical approach ensures that safety initiatives aren't implemented and forgotten but constantly refined based on real-world outcomes.
<table border="0"> <tr><th>Methodology</th><th>Primary Focus</th><th>Key Benefit</th></tr> <tr><td>Lean</td><td>Eliminating waste</td><td>Streamlined processes</td></tr> <tr><td>Kaizen</td><td>Small improvements</td><td>Continuous adaptation</td></tr> <tr><td>Six Sigma</td><td>Data analysis</td><td>Targeted solutions</td></tr> <tr><td>PDCA</td><td>Systematic approach</td><td>Structured improvement</td></tr> </table>Practical Implementation Steps for Engineering Environments
Implementing continuous improvement in safety management doesn't have to be overwhelming. Here's a practical roadmap that engineering organisations can follow:
First, establish clear safety KPIs aligned with your broader business objectives. These might include incident rates, near-miss reporting percentages, or audit compliance scores. What gets measured gets managed, and these metrics will guide your improvement journey.
Next, form cross-functional safety teams that include representatives from engineering, operations, management, and shop floor workers. This diverse perspective ensures that safety improvements address real-world challenges rather than theoretical problems.
Regular safety audits are essential for identifying gaps and tracking progress. These shouldn't be viewed as punitive exercises but as valuable learning opportunities. Q-Hub's Audit Hub streamlines this process by digitalising audit schedules, findings, and corrective actions, making the entire process more efficient.
- Integrate safety into project planning - Make safety considerations a core component of design and implementation phases
- Implement transparent reporting systems - Create channels for anonymous hazard reporting without fear of blame
- Conduct regular training - Ensure all team members understand safety protocols and improvement methodologies
- Use data analytics - Apply predictive tools to identify potential risks before incidents occur

Leveraging Technology for Enhanced Safety Outcomes
Technology has revolutionised how engineering firms approach safety management. Digital tools now form the backbone of effective continuous improvement programmes, providing real-time data, streamlined communication, and unprecedented visibility into safety performance.
In this digital era, leveraging enterprise safety management solutions becomes essential not only for compliance but for fostering an environment where continuous enhancement is at the forefront. These solutions ensure that every technological advancement is integrated seamlessly into safety protocols, making data-driven decisions both accessible and actionable in high-stakes engineering environments.
IoT sensors have become game-changers for engineering safety. These devices monitor everything from air quality to equipment vibration patterns, detecting anomalies that might indicate potential failures. For example, in a manufacturing environment, sensors can detect unusual machine temperatures or vibrations that precede breakdowns, allowing maintenance before catastrophic failures occur.
Wearable technology takes personal safety monitoring to new levels. Smart helmets, vests, and watches can track worker location, detect falls, monitor vital signs, and even measure exposure to harmful substances. This real-time monitoring enables immediate intervention when workers enter dangerous areas or show signs of fatigue.
As one health and safety manager at Rocal Insulating Panels noted after implementing Q-Hub's digital safety system: "We've transformed our incident reporting from a paper-based nightmare to a streamlined digital process. Response times have improved dramatically, and we now have data that actually helps prevent future incidents."
Measuring What Matters: Tracking Safety Improvement
The true value of continuous improvement programmes lies in their measurable impact on safety outcomes. Effective measurement goes beyond simply tracking incidents to understanding patterns, identifying root causes, and verifying the effectiveness of interventions.
Key performance indicators should focus on both lagging indicators (incidents that have already occurred) and leading indicators (activities that help prevent incidents). This balanced approach provides a more complete picture of safety performance.
Essential KPIs to consider include:
- Incident frequency and severity rates - Track accidents and their impact
- Near-miss reporting - Monitor potential incidents that didn't result in harm
- Safety training completion - Ensure workforce preparedness
- Audit findings and corrective actions - Measure compliance improvements
- Employee safety perception - Gauge cultural attitudes toward safety
Regular safety performance reviews should examine these metrics to identify trends and opportunities for improvement. The most effective reviews involve cross-functional teams and focus on systemic issues rather than individual blame.
Scottish Leather Group experienced this transformation firsthand after implementing Q-Hub's solutions. Their compliance team now generates real-time safety performance reports that previously took days to compile, allowing them to identify and address issues promptly.
Real-World Success Stories: Transformation Through Technology
The impact of continuous improvement programmes on engineering safety becomes clear when examining real-world case studies. These examples demonstrate how systematic approaches combined with the right technology create measurable safety improvements.
A UK manufacturing firm specialising in automotive components implemented Kaizen principles to address recurring workplace injuries. By engaging workers at all levels to identify small, incremental improvements, they reduced lost-time injuries by 25% within a year. Simple changes like reorganising workstations and implementing daily safety checks made a significant difference when applied consistently.
Similarly, Fowlers of Bristol transformed their engineering operations using Q-Hub's digital platform. By centralising communication and implementing robust document management, they created a more coordinated approach to safety management. Their "Zero Defects" initiative became measurable through digital dashboards that tracked key performance indicators, making quality and safety visible to everyone.
In another striking example, Weston Aerospace adopted Q-Hub's Process Hub to manage non-conformance reports and compliance workflows. This digital transformation eliminated delays in addressing safety issues and provided real-time visibility into resolution progress. The result was faster response to potential hazards and better coordination between departments.
<table border="0"> <tr><th>Improvement Area</th><th>Before Digital Tools</th><th>After Q-Hub Implementation</th></tr> <tr><td>Audit Preparation</td><td>Days of manual work</td><td>Hours with automated systems</td></tr> <tr><td>Incident Response Time</td><td>24-48 hours</td><td>Under 4 hours</td></tr> <tr><td>Safety Document Access</td><td>Limited to office staff</td><td>Universal, including shop floor</td></tr> <tr><td>Compliance Reporting</td><td>Monthly manual reports</td><td>Real-time digital dashboards</td></tr> </table>These success stories share common elements: leadership commitment, employee engagement, and the smart application of technology. Together, these factors create an environment where continuous improvement becomes part of the organisational culture rather than just another initiative.
Engineering firms looking to enhance their safety protocols can learn valuable lessons from these examples. The path to improvement doesn't require massive overhauls but rather consistent application of proven methodologies supported by the right digital tools.
Ready to transform your engineering safety management with continuous improvement programmes? Q-Hub offers comprehensive digital solutions that streamline compliance, enhance visibility, and drive measurable safety improvements across your operations. Discover how our tailored QHSE software can help you build a more proactive safety culture while reducing administrative burden.
Start using Q-Hub today
- Manage compliance in one place
- Streamline your teams and tasks
- Use Q-Hub free for 30 days