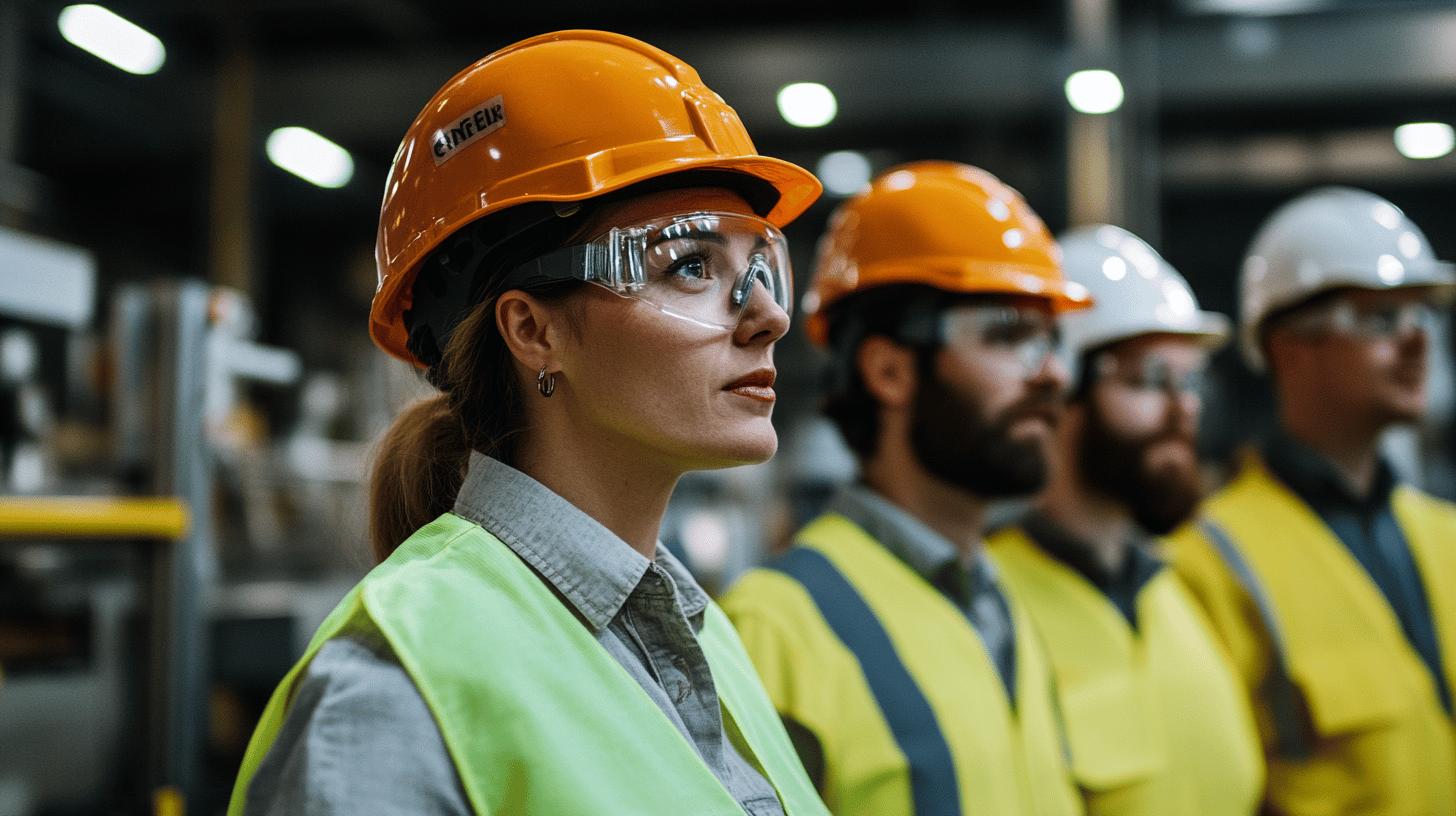
Safety Management Training Elevates Food Manufacturing Standards
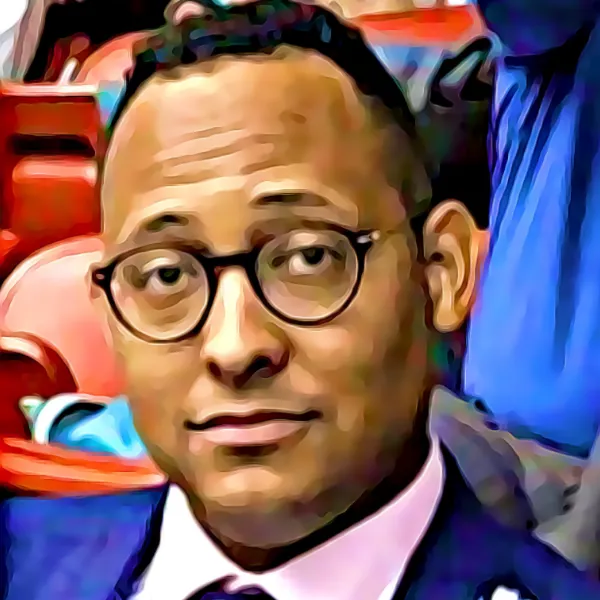
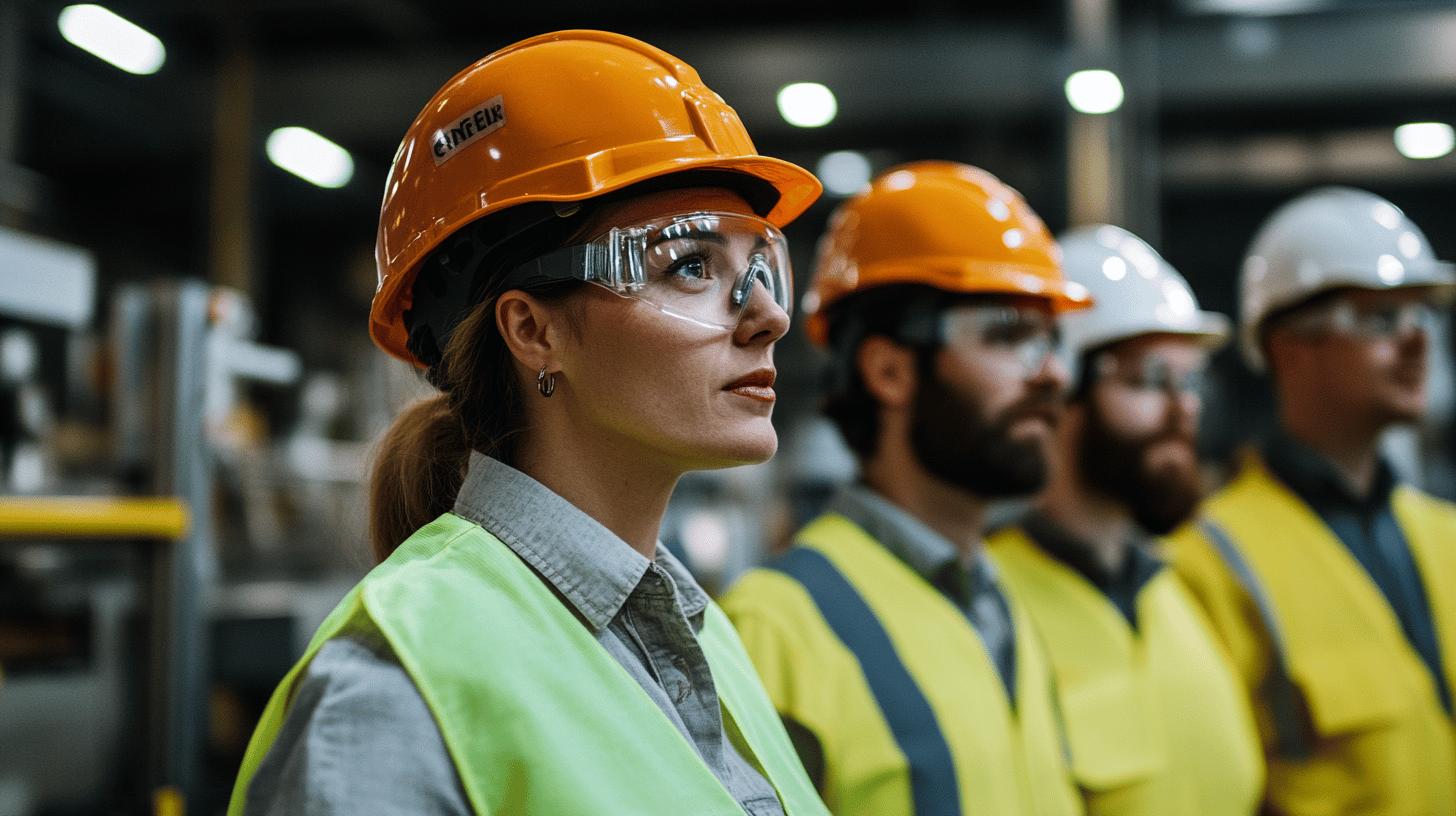
Safety Management Training Elevates Food Manufacturing Standards
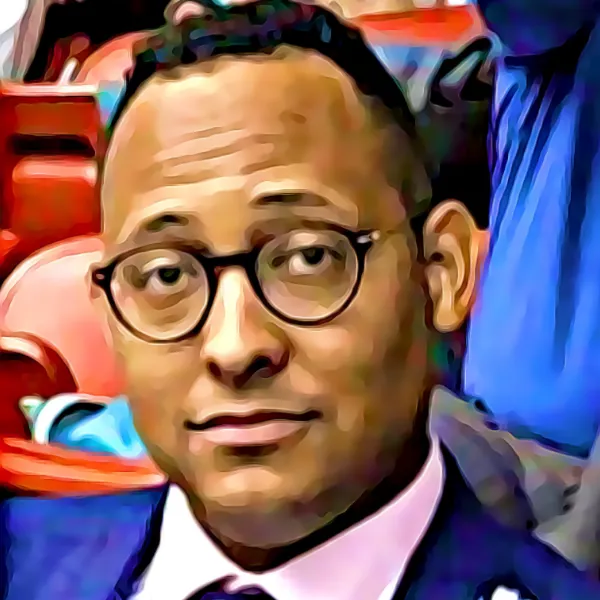
The Role of Safety Management User Training in Enhancing Food Manufacturing Standards
Safety management user training plays a vital role in food manufacturing excellence, ensuring operations meet regulatory requirements while maintaining product quality. Comprehensive training equips staff with essential knowledge to handle food safety challenges effectively, addressing hygiene practices, risk management, and cross-contamination prevention. Q-Hub's digital solutions support this critical process by streamlining training delivery and monitoring compliance across organisations.
Integrating robust systems such as erp integration in food operations can further enhance the traceability and effectiveness of these training platforms, ensuring that every operational detail is captured and managed efficiently. This integration not only reinforces compliance but also provides a seamless workflow in managing safety protocols across various departments.
Without proper training systems, companies risk foodborne illness outbreaks, regulatory penalties, and significant damage to their reputation.- Reduces contamination risks through improved hygiene practices
- Ensures compliance with Food Standards Agency (FSA) regulations
- Enhances workforce confidence in executing safety protocols
- Minimises costly product recalls and brand reputation damage
- Strengthens organisational safety culture across all departments
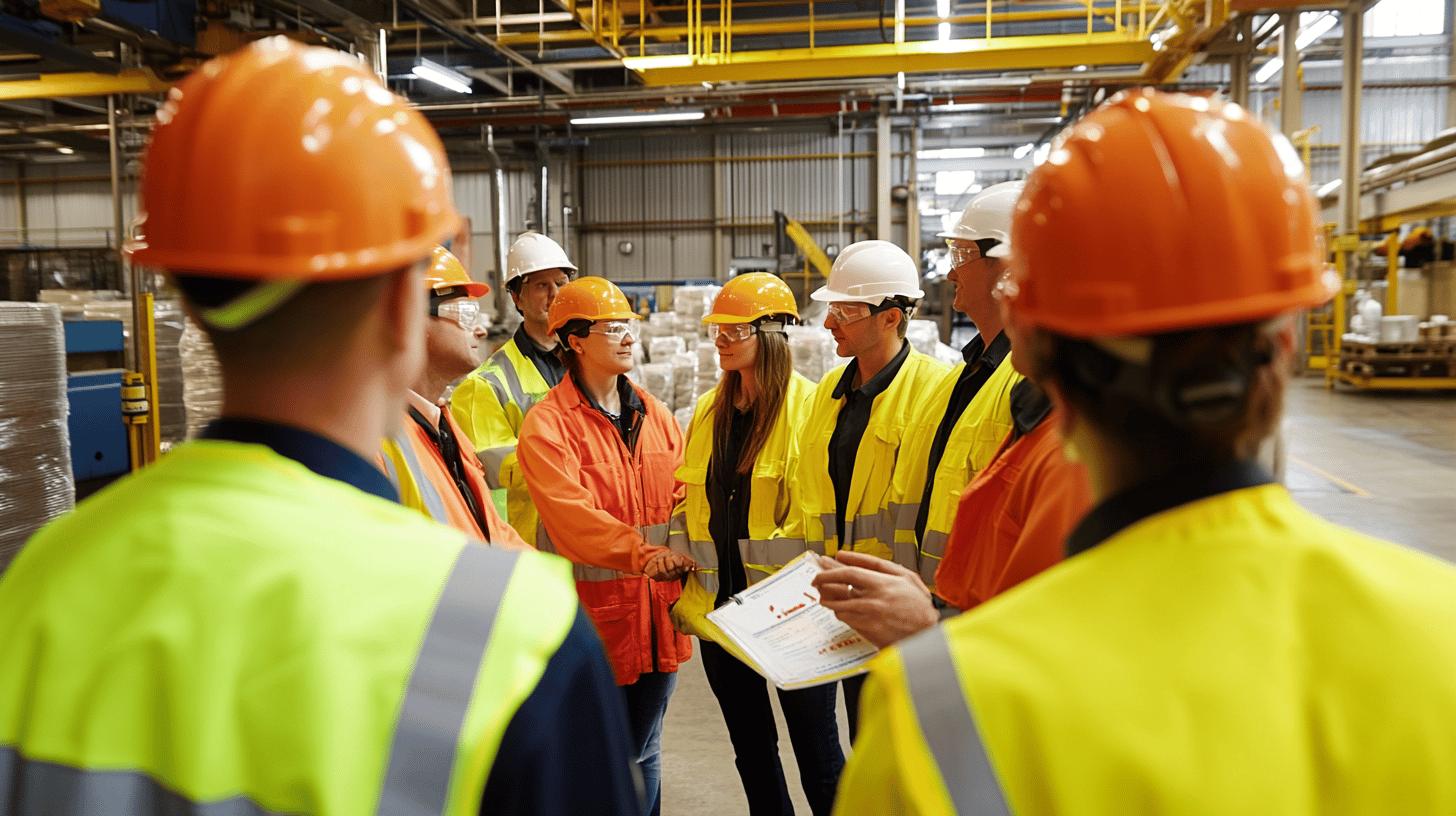
When aligned with global standards like ISO 22000 and HACCP principles, structured training programmes ensure food manufacturing processes remain consistent and safe. Q-Hub's software solutions centralise these training efforts, providing accessible platforms that adapt to evolving regulatory landscapes while fostering continuous improvement throughout the organisation.
Building Foundations Through Strategic Onboarding
Effective onboarding processes embed safety standards into food manufacturing operations from day one. Rather than simply orientating new employees, these programmes lay the groundwork for a safety-first culture that protects both consumers and the business. Digital onboarding platforms like those provided by Q-Hub streamline this critical phase, ensuring consistent knowledge transfer across departments.
As demonstrated by Rocal Insulating Panels, transitioning from paper-based systems to digital training platforms significantly enhances safety compliance. Their implementation of Q-Hub's digital solutions transformed accident reporting and investigations, enabling quicker resolution and better manager involvement throughout the process.
Key Elements of Effective Safety Training Systems
Creating impactful safety training requires focusing on elements that address both immediate and ongoing safety needs in food manufacturing:
By leveraging continuous digital innovation, enhancing safety in food manufacturing becomes a top priority. This approach enables companies to not only meet regulatory standards but also instill a culture of proactive safety and continuous improvement, ensuring the long-term success of food manufacturing operations.
- Hazard identification training: Equipping employees to recognise potential risks from allergens, cross-contamination, and equipment issues
- Scenario-based learning: Using real-world examples to help staff apply knowledge to practical situations
- Regular regulatory updates: Incorporating changes from authorities like the FSA to maintain compliance
- Continuous learning pathways: Providing refresher courses to ensure knowledge retention over time
- Performance monitoring: Tracking employee progress through assessments to validate effectiveness
Scottish Leather Group demonstrated these principles by implementing Q-Hub's Audit Hub to efficiently manage compliance across multiple ISO standards. Their digital transformation enabled streamlined audit preparation and reporting, freeing resources for more value-added activities.
Measuring What Matters: Tracking Training Impact
Evaluating safety training effectiveness requires clear metrics that connect learning activities to operational outcomes. These measurements provide insight into how well programmes meet both regulatory requirements and business objectives.
<table border="0"> <tr><th>Training Metric</th><th>Before Digital Systems</th><th>After Q-Hub Implementation</th></tr> <tr><td>Audit Preparation Time</td><td>Days of manual document gathering</td><td>Hours with centralised documentation</td></tr> <tr><td>Safety Document Access</td><td>Fragmented across papers and drives</td><td>Instant access through centralised library</td></tr> <tr><td>Training Completion Tracking</td><td>Manual sign-off sheets</td><td>Automated tracking with notifications</td></tr> <tr><td>Non-Conformance Resolution</td><td>Often delayed with limited visibility</td><td>Prompt with clear accountability</td></tr> </table>Fowlers of Bristol experienced these improvements firsthand when they centralised their safety operations with Q-Hub. Their transition from fragmented email communications to an integrated digital platform significantly improved document control and cross-team collaboration, enhancing overall safety outcomes.
Technology-Driven Training: The Digital Advantage
Digital platforms are revolutionising safety training in food manufacturing. Q-Hub's solutions provide interactive, accessible learning experiences that traditional methods simply cannot match. These technologies ensure consistent knowledge transfer while enabling personalised learning pathways that adapt to individual needs.
- Mobile learning applications: Provide on-demand access to critical safety information anywhere on the production floor
- Virtual simulations: Allow practice of safety protocols in controlled digital environments
- AI-enhanced learning: Deliver personalised training paths based on individual performance data
- Real-time analytics: Track progress and identify knowledge gaps requiring additional focus
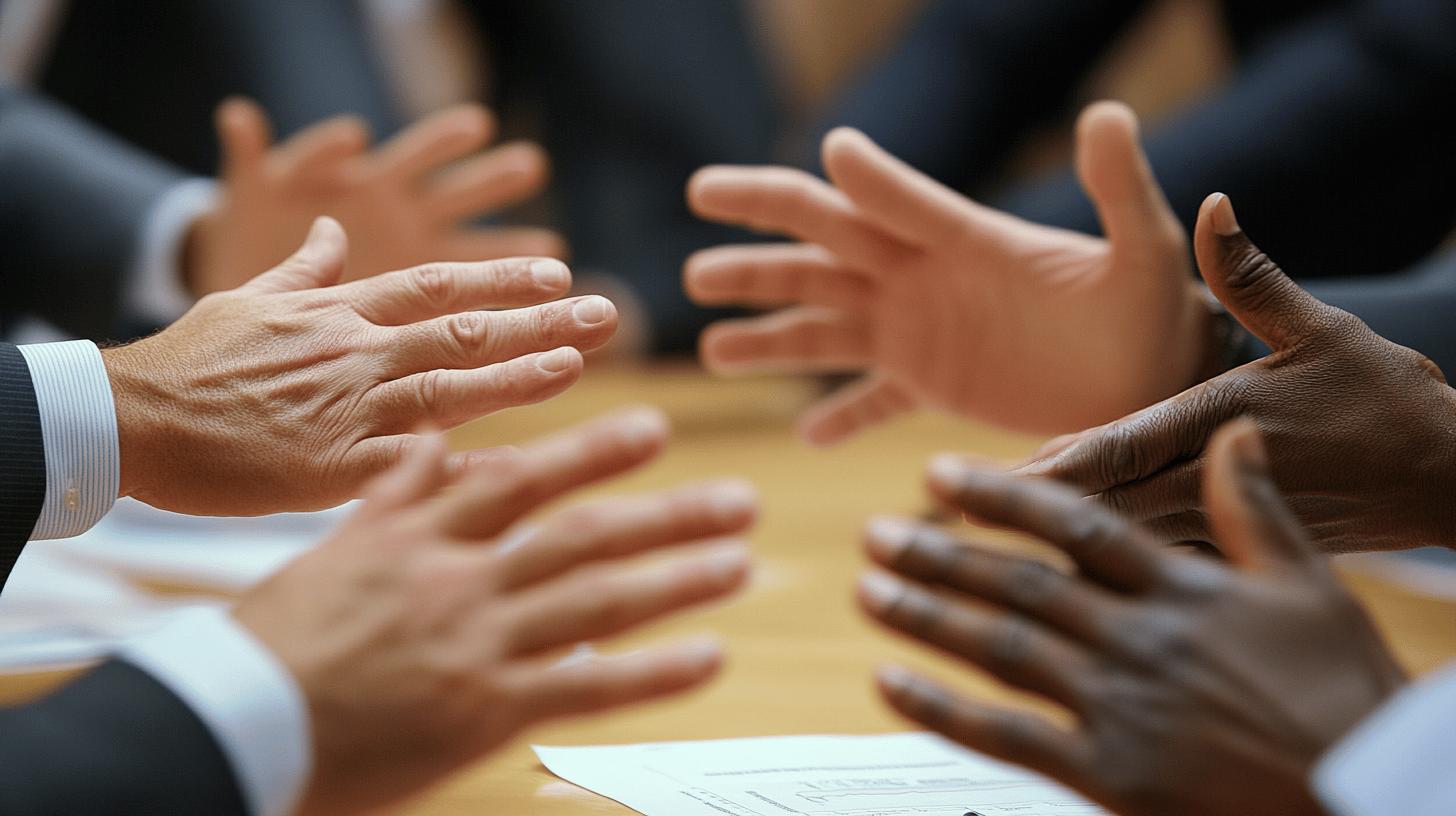
Anglia Cathodic Protection Services transformed their fragmented paper-based systems with Q-Hub's digital platform, making compliance materials more accessible and actionable for all employees. Their implementation specifically improved non-conformance tracking and audit processes, demonstrating how technology can overcome traditional training limitations.
Fostering a Culture Where Safety Becomes Second Nature
Continuous professional development forms the backbone of a sustainable safety culture in food manufacturing. Leadership engagement is essential - when management visibly prioritises safety training, it signals its importance throughout the organisation. Q-Hub's platforms support this cultural development by providing tools that make safety initiatives visible and engaging across all levels.
Effective strategies for building this culture include regular safety workshops, leadership-led training sessions, and employee-driven improvement initiatives. BMC Analysis leveraged Q-Hub's Process Hub to revolutionise their non-conformance management, creating a system where actions were tracked automatically and nothing was overlooked, reinforcing accountability throughout the organisation.
Adapting to Evolving Industry Standards
Food manufacturing regulations continuously evolve, requiring training programmes to adapt accordingly. Staying current with Food Standards Agency updates and other regulatory changes is essential for maintaining compliance and operational excellence. Q-Hub's configurable platform enables food manufacturers to quickly update training materials and document acknowledgments as standards change.
Weston Aerospace demonstrated this adaptability by implementing Q-Hub's Audit Hub to manage compliance across changing ISO standards. Their digital transformation streamlined audit preparation and reporting, allowing them to quickly adapt to new requirements while maintaining operational efficiency.
As food safety standards continue to evolve, Q-Hub's customisable QHSE software solutions provide the flexibility and oversight needed to maintain compliance while enhancing operational efficiency. By digitising safety training and compliance monitoring, food manufacturers can build resilient safety cultures that adapt to changing regulations while supporting long-term business growth. Ready to transform your safety training approach? Discover how Q-Hub's digital solutions can streamline compliance while elevating your food manufacturing standards.
Start using Q-Hub today
- Manage compliance in one place
- Streamline your teams and tasks
- Use Q-Hub free for 30 days