
Web Portal Creation Enhances Training for Food Producers
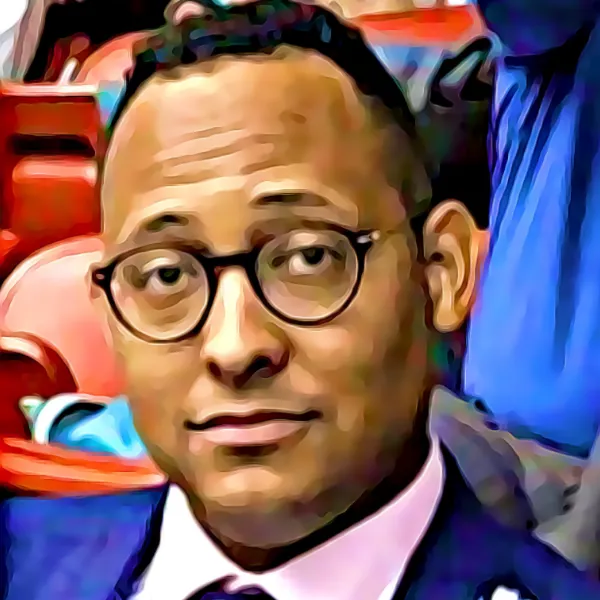

Web Portal Creation Enhances Training for Food Producers
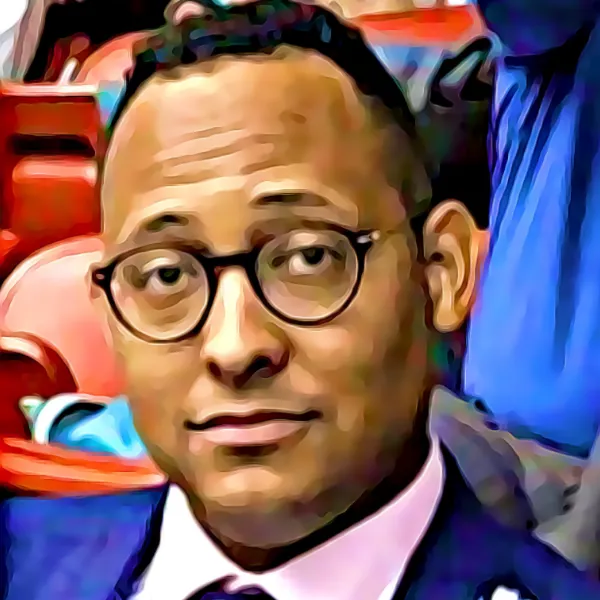
How Web Portal Creation Improves Training Management for Food Producers
Managing training and compliance oversight in the food industry often feels like juggling spinning plates. With constantly evolving regulations, dispersed resources, and employee development tracking needs, traditional paper-based methods simply can't keep up. This is where web portal creation facilitating training and competence management oversight for food producers transforms the landscape. These digital platforms centralise everything, making it easier to monitor, streamline, and enhance workforce training while maintaining compliance. Q-Hub's expertise in creating customised software solutions specifically addresses these challenges by providing unified, accessible systems tailored to food production environments.
Modern training portals integrate seamlessly with existing workflows, transforming fragmented approaches into cohesive frameworks. Onboarding becomes automated, compliance tracking is simplified through built-in alerts, and personalised dashboards offer managers real-time insight into workforce development. By consolidating these elements with industry-specific content (like food safety protocols and HACCP guidelines), food producers can focus on growth while maintaining rigorous standards for safety and quality.
Transforming Training Through Digital Innovation

The right digital portal acts as the backbone of effective training management. When Scottish Leather Group faced challenges managing compliance across multiple sites, Q-Hub's implementation of customised portals delivered immediate improvements. Their Audit Hub enabled efficient management of audits across multiple standards with pre-built templates and automated schedules that simplified previously complex processes.
Mobile accessibility represents another game-changing advantage. In the bustling environment of food production facilities, staff rarely sit at desks all day. Mobile-friendly interfaces allow employees to complete training modules, check compliance requirements, or access critical documents from anywhere in the facility – or even remotely.
"Without the Qhub portal, tracking NCRs was a challenge, with resolutions often delayed due to the lack of a structured system. The platform provided a centralised space for managing NCRs, linking them to audits, and ensuring accountability at each step."<table border="0"> <tr><th>Key Feature</th><th>Benefit to Food Producers</th></tr> <tr><td>Personalised Dashboards</td><td>Quick access to individual training progress and compliance metrics</td></tr> <tr><td>Automated Compliance Tracking</td><td>Proactive alerts prevent certification lapses and regulatory issues</td></tr> <tr><td>Industry-Specific Content</td><td>Targeted resources aligned with food safety requirements</td></tr> <tr><td>Mobile-Friendly Access</td><td>Training available anywhere, improving completion rates</td></tr> </table>
Unlocking Targeted Competency Development
Food safety depends entirely on comprehensive competency management. Traditional approaches often leave critical skills gaps unaddressed until they manifest as problems. Q-Hub's customised portals offer sophisticated competency tools that identify training needs before they impact operations.
These platforms employ competency gap analysis to pinpoint exactly where employees need additional training to meet industry standards. For example, when Fowlers of Bristol implemented Q-Hub's solution, they gained unprecedented visibility into team capabilities, allowing management to develop targeted training interventions that significantly improved quality outcomes.
The following competency tools make these platforms particularly valuable for food producers:
- Competency gap analysis that ensures precisely targeted training
- Real-time workforce tracking for instant capability assessment
- Role-specific learning paths aligned with regulatory requirements
- Automated compliance reporting for audit readiness
- Customised competency models specific to food production roles

Streamlining Regulatory Compliance Through Automation
Food producers face some of the most rigorous compliance requirements of any industry. A single compliance lapse can lead to serious consequences including product recalls, reputational damage, or regulatory penalties. Training portals equipped with automated compliance features provide essential protection against these risks.
BMC Analysis found that Q-Hub's Process Hub revolutionised their previously fragmented workflow by offering a centralised, digital platform for managing non-conformances. With automated tracking and reporting, issues could be resolved efficiently without anything falling through the cracks. This level of systematic oversight is particularly crucial in food production environments where safety standards must be meticulously maintained.
These compliance automation features deliver significant advantages:
- Real-time monitoring of certification statuses prevents compliance gaps
- Automated alerts ensure training deadlines and recertifications are never missed
- Centralised documentation provides instant access during inspections
- Custom reports tailored to specific audit requirements save preparation time
- Automatic incorporation of new regulatory requirements into training programmes
Driving Data-Informed Training Decisions
One of the most powerful aspects of digital training platforms is the wealth of actionable data they generate. Food producers using Q-Hub's solutions gain valuable insights through advanced analytics that transform how workforce development is managed and measured.
Visual dashboards consolidate complex training metrics into clear, meaningful displays that highlight trends, gaps, and opportunities. This data-driven approach allows training managers to make informed decisions about resource allocation, identify high-performing teams, and address compliance risks before they become problems.
When Weston Aerospace implemented Q-Hub's platform, they gained unprecedented visibility into their training effectiveness through real-time dashboards. These visualisation tools didn't just save time; they made it easier to identify trends and adjust training strategies proactively. The impact was measurable in terms of both compliance improvement and operational efficiency.
Ensuring Seamless User Experiences
Even the most advanced training platform fails if employees find it difficult to use. Successful implementation depends on intuitive interfaces that make accessing training materials straightforward for all staff, regardless of technical proficiency. Q-Hub's approach focuses on creating user-friendly experiences that encourage engagement rather than frustration.
For Rocal Insulating Panels, the transition from cluttered document storage to Q-Hub's centralised digital library eliminated hours of wasted time searching for critical files. The intuitive design ensured shop floor workers could easily access relevant safety information without extensive training on the system itself.
Key interface elements that contribute to successful adoption include:
- Clean, uncluttered designs that highlight priority information
- Consistent navigation patterns that remain familiar across all sections
- Mobile-responsive layouts that function effectively on any device
- Customisable views that prioritise relevant content for different roles
- Simplified access to frequently used features and documents
Scaling Training Capabilities As Your Business Grows
Food producers constantly face evolving challenges as they expand operations, enter new markets, or adapt to changing regulations. Training systems must scale accordingly without creating additional administrative burden or compliance risks. Q-Hub's platforms are specifically designed with scalability as a core feature.
Anglia Cathodic Protection's experience demonstrates this scalability in action. As their workload and client base rapidly increased, their paper-based systems simply couldn't keep pace. Q-Hub provided a robust, scalable platform that not only handled their current requirements but could expand as needed to accommodate future growth.
What makes these solutions truly scalable is their architectural flexibility:
- Cloud-based access ensures training availability regardless of location
- Role-specific learning paths maintain relevance as teams diversify
- Automated updates incorporate new regulations without manual intervention
- Modular design allows adding features as needs evolve
By implementing Q-Hub's digital training solutions, food producers gain not just a tool for current needs, but a foundation for future growth that adapts as their business evolves. Through centralised management, automated compliance tracking, and data-driven insights, these platforms transform training from an administrative burden into a strategic advantage that supports food safety, regulatory compliance, and operational excellence even as organisations scale. Ready to revolutionise your training and compliance management? Discover how Q-Hub's specialised solutions can create a tailored system that grows with your food production business.
Start using Q-Hub today
- Manage compliance in one place
- Streamline your teams and tasks
- Use Q-Hub free for 30 days