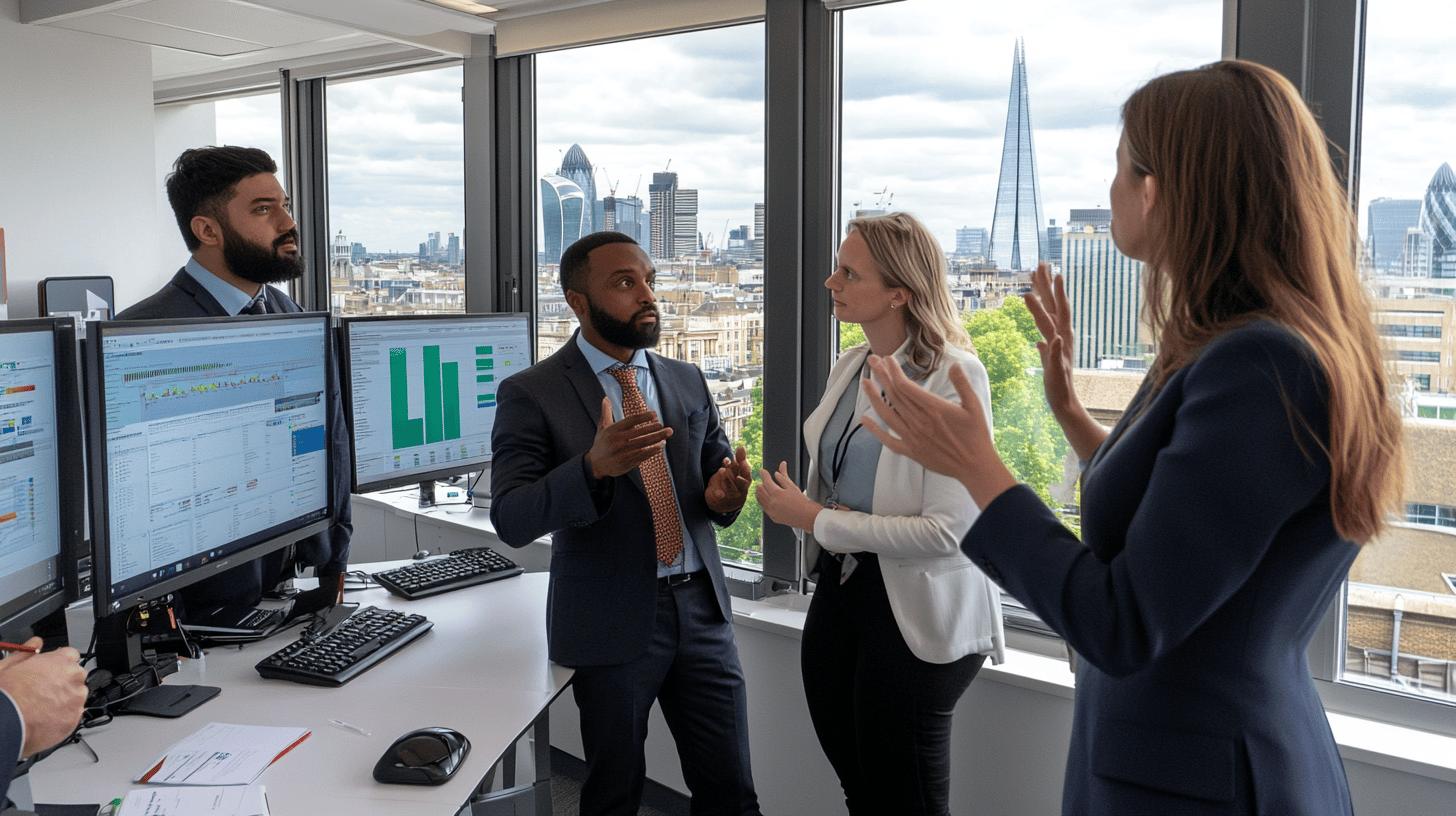
Web Portal Creation Boosts Transparent Oversight for Pharma
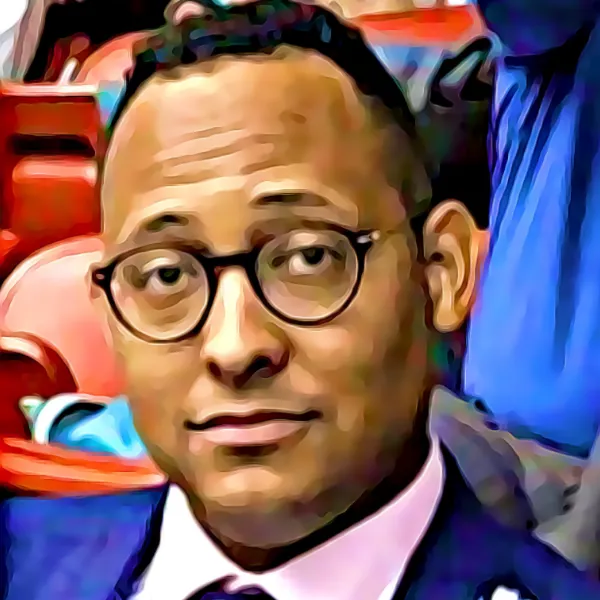
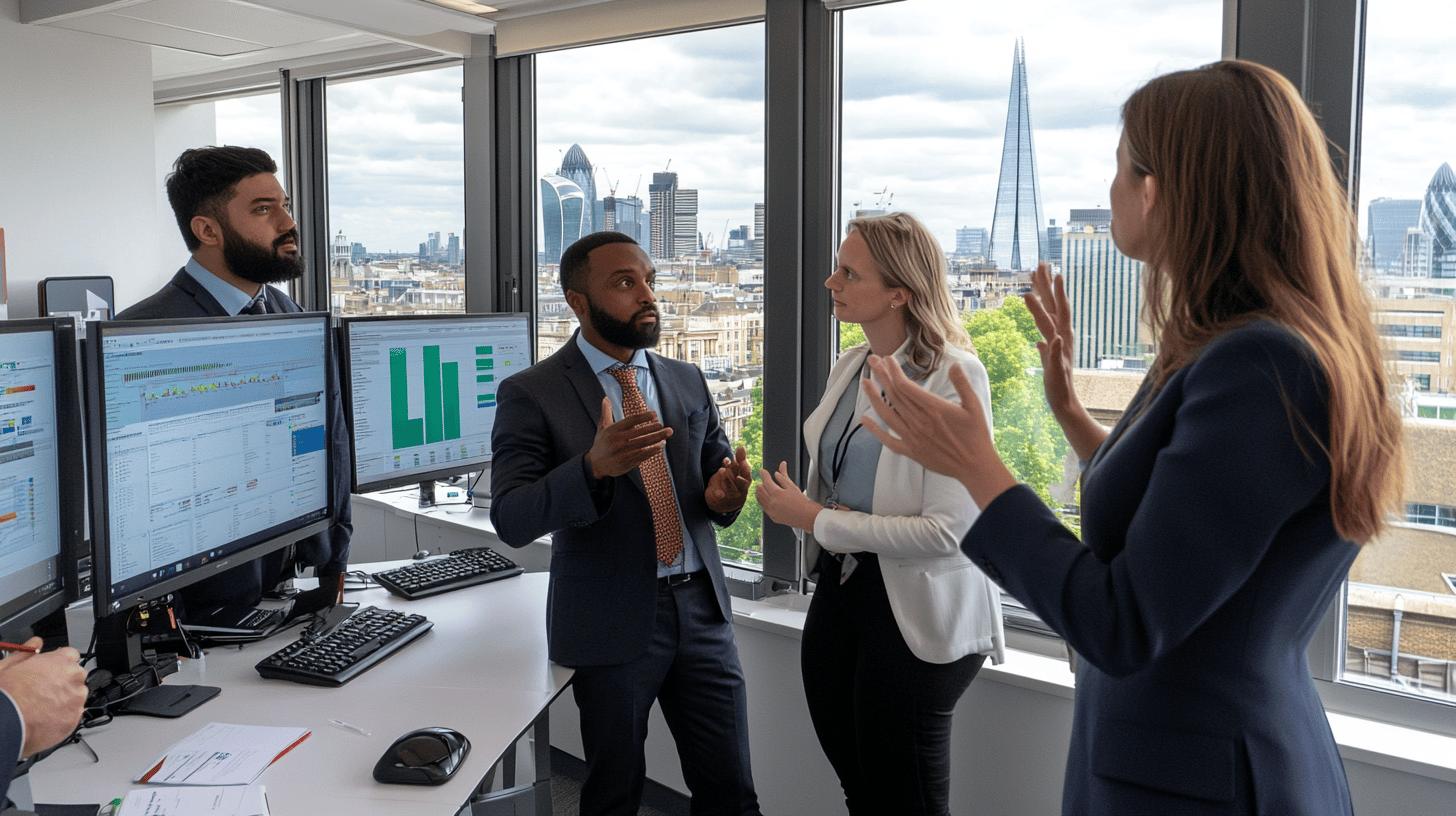
Web Portal Creation Boosts Transparent Oversight for Pharma
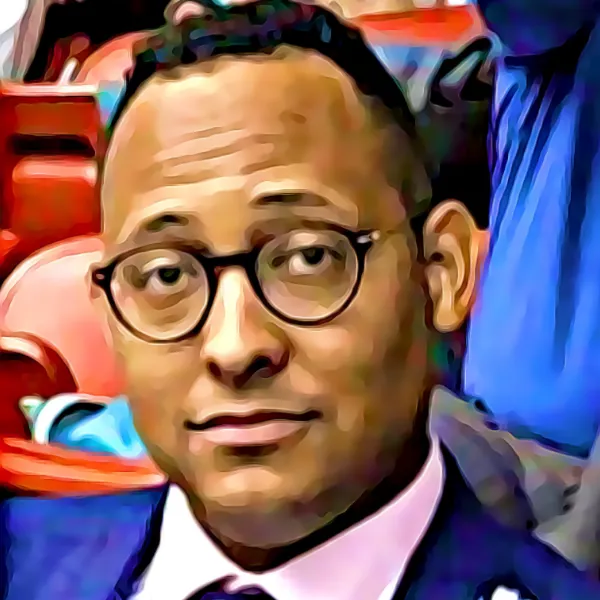
Key Features of Web Portals for Transparent Incident Reporting in Pharmaceutical Production
Web portal creation enabling transparent incident reporting oversight for pharmaceutical producers web portal creation. This innovative approach not only modernises compliance systems but also streamlines incident reporting, ensuring that regulatory requirements are met with precision. By embracing a digital transformation that parallels traditional oversight with cutting-edge technology, the industry is set to benefit from enhanced transparency and a faster incident response rate, much like building a robust bridge between legacy practices and modern solutions. is transforming compliance management and operational efficiency across the industry. These centralised platforms ensure comprehensive tracking of every incident, from near misses to corrective actions, with complete transparency. Q-Hub's innovative software solutions empower pharmaceutical companies to manage incidents precisely while meeting strict regulatory requirements.
Streamlining Complex Processes Through Intelligent Design
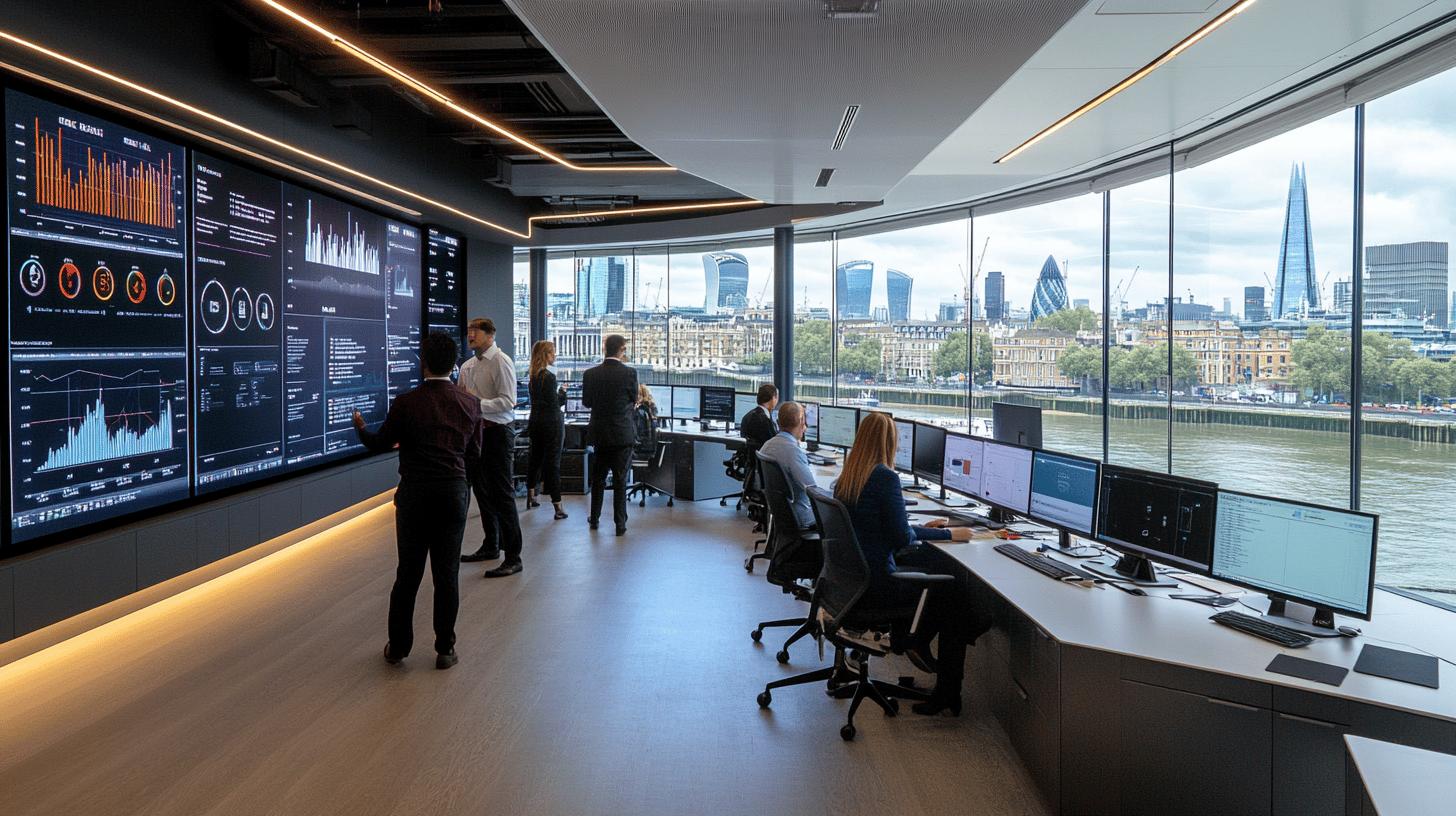
At their core, these reporting portals feature customisable dashboards that display critical data based on user preferences. This ensures nothing is overlooked in the fast-paced pharmaceutical environment. Automated alerts notify appropriate personnel immediately, dramatically reducing incident response times.
Secure data accessibility strikes the perfect balance between protection and availability—sensitive information remains protected while remaining accessible to authorised personnel. This seamless approach creates audit-ready records that significantly reduce regulatory inspection burdens.
The ability to customise workflows according to our specific processes has transformed how we manage incidents. What once took days now happens in hours, with complete traceability. Source: Scottish Leather Group case implementation
These platforms excel by integrating with existing systems like ERP and quality management software. This integration eliminates data silos and creates unified workflows where cross-functional teams can collaborate effectively and make informed decisions faster.
- Real-time tracking capabilities for proactive risk management
- Cross-functional data access enhancing stakeholder transparency
- Seamless integration with existing quality systems
- Automated alerts accelerating critical incident response
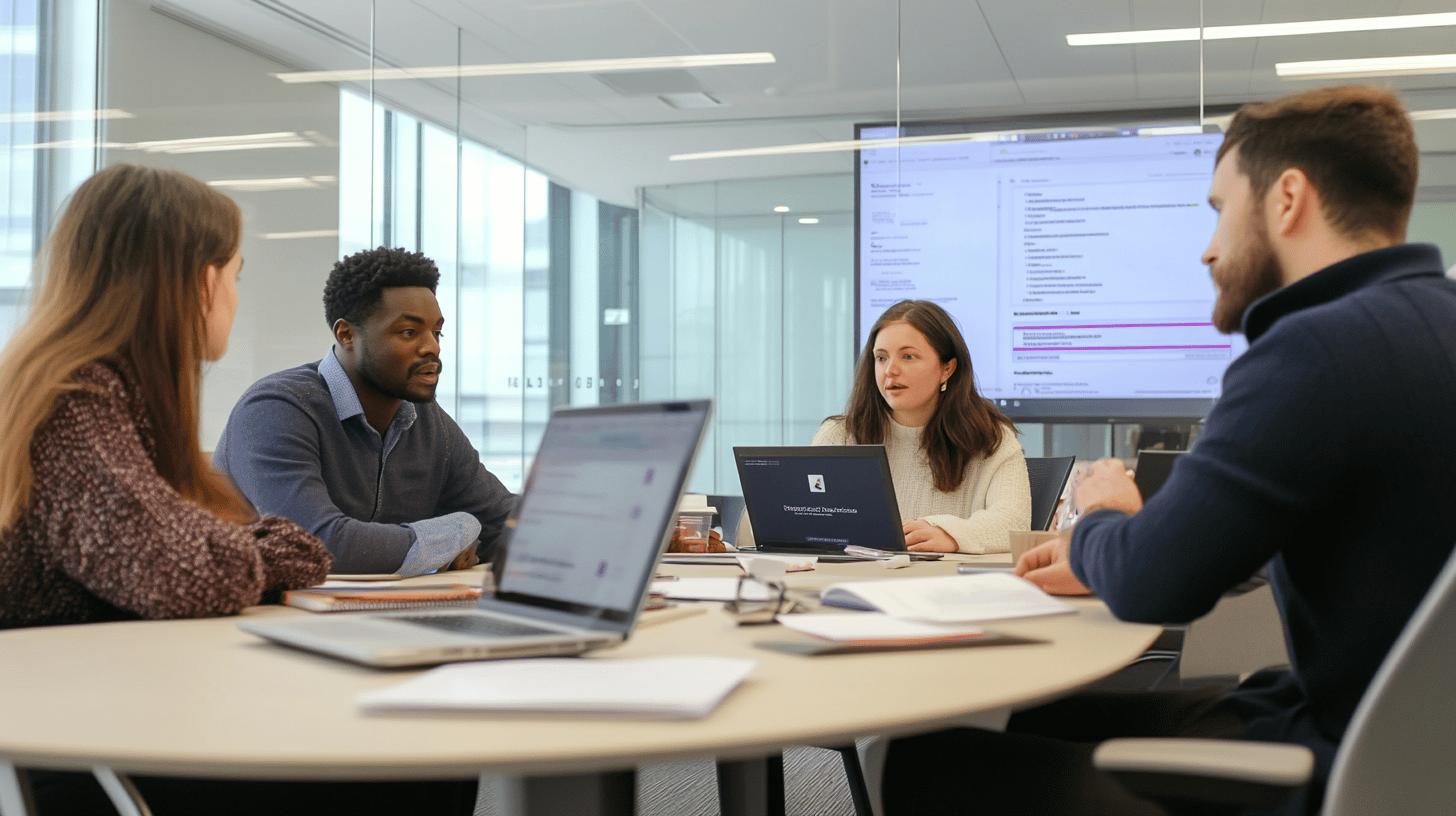
Navigating Complex Regulatory Requirements with Confidence
The pharmaceutical sector operates under intense regulatory scrutiny from bodies like the FDA, EMA, and under GDPR guidelines. Modern incident reporting portals provide centralised solutions to meet these demands confidently. By automating key compliance processes such as documentation and reporting, these systems minimise human error while ensuring consistent accuracy esg-driven strategies pharmaceutical governance. The incorporation of ESG principles can be seen as an additional layer of security and accountability in the pharmaceutical industry. As companies integrate sustainable, governance-focused strategies, the digital platforms evolve not just to meet regulatory obligations but also to foster long-term sustainable excellence, ensuring that every incident report contributes to an overarching commitment to ethical and environmental stewardship.
Perhaps most valuable is the ability to generate audit-ready records instantly. When regulatory inspections arise, organised and accurate data is available with minimal preparation. Tools for compliance gap analysis allow producers to identify vulnerabilities proactively, addressing issues before they escalate into regulatory concerns.
<table border="0"> <tr><th>Feature</th><th>Regulatory Benefit</th></tr> <tr><td>Automated Documentation</td><td>Reduces errors, ensures accuracy</td></tr> <tr><td>Incident Trend Analysis</td><td>Identifies recurring issues for mitigation</td></tr> <tr><td>Audit Trail Management</td><td>Simplifies regulatory preparation</td></tr> <tr><td>Compliance Gap Analysis</td><td>Highlights improvement areas</td></tr> </table>Revolutionising Pharmaceutical Operations Through Process Automation
Process automation transforms complex pharmaceutical incident management into manageable, error-free workflows. By standardising resolution protocols and minimising manual interventions, these systems ensure consistency in an industry where precision isn't optional—it's mandatory.
Response times improve dramatically with automation. Critical incidents get flagged instantly, ensuring urgent issues like contamination risks receive immediate attention. In manual systems, such alerts might face delays, but automated workflows notify key personnel within seconds, significantly reducing potential consequences.
For pharmaceutical producers, the long-term benefits extend beyond faster responses. Automated systems provide continuous monitoring that offers insights into recurring issues and improvement areas. This data-driven approach helps companies refine operations, reduce risks, and optimise resources—essential capabilities in the dynamic pharmaceutical landscape.
- Automated incident logging captures data in real-time
- Priority-based alerts ensure critical incidents receive immediate attention
- Standardised workflows maintain consistency across all processes
Ensuring Seamless Growth Through Integration and Scalability
Web portal creation enabling transparent incident reporting oversight for pharmaceutical producers web portal creation. This innovative approach not only modernises compliance systems but also streamlines incident reporting, ensuring that regulatory requirements are met with precision. By embracing a digital transformation that parallels traditional oversight with cutting-edge technology, the industry is set to benefit from enhanced transparency and a faster incident response rate, much like building a robust bridge between legacy practices and modern solutions. plays a crucial role in modernising operational workflows. When these systems integrate with existing platforms, incident reporting transforms from fragmented into centralised, streamlined processes that reduce redundancies and improve efficiency.
As Weston Aerospace discovered after implementing Q-Hub's solutions, systems that "talk to each other" eliminate data silos and enable greater team collaboration. This interconnectedness provides a single source of truth for audits and inspections—essentially creating a digital bridge unifying operations and compliance in real-time.
Scalability proves equally critical for growing pharmaceutical operations. As companies expand into new markets or face increased regulatory demands, scalable platforms grow alongside these changing needs. This flexibility ensures businesses are empowered rather than constrained by their tools.
Transforming Reactive Responses into Proactive Solutions
Advanced incident report analytics are revolutionising pharmaceutical decision-making processes. By uncovering hidden patterns and root causes, these tools facilitate a shift from reactive to proactive problem-solving—critical in an industry where minor oversights can have significant consequences.
Transparency metrics foster trust among stakeholders by ensuring data is shared clearly and consistently. Incident trend analysis reveals recurring issues that might otherwise go unnoticed, reassuring both internal teams and external regulatory bodies that accountability and improvement remain priorities.
Analytics also enable preventive, insights-driven decision-making. By analysing trends and predictive insights, pharmaceutical producers can anticipate risks before they escalate. For instance, if a specific manufacturing process consistently triggers minor incidents, predictive analytics can highlight this as an improvement area, facilitating timely interventions and reducing compliance breach risks.
Real Results: Pharmaceutical Excellence Through Digital Transformation
A leading UK pharmaceutical company encountered significant challenges with their manual incident tracking systems, resulting in delays and poor cross-departmental visibility. Compliance with MHRA and EMA requirements became increasingly difficult due to fragmented data and inconsistent documentation. The organisation implemented a centralised incident reporting web portal to address these inefficiencies.
The transformation produced immediate, measurable results. Incident reporting transparency increased by 40%, while response times decreased by 30% through real-time tracking and automated alerts. Automated documentation features ensured audit-ready reports, significantly reducing regulatory inspection burdens.
Q-Hub specialises in creating precisely these types of transformative software solutions that streamline compliance while enhancing operational efficiency. By implementing tailored incident reporting portals, pharmaceutical producers can achieve remarkable improvements in transparency, response times, and regulatory readiness—turning compliance challenges into opportunities for operational excellence.
Start using Q-Hub today
- Manage compliance in one place
- Streamline your teams and tasks
- Use Q-Hub free for 30 days