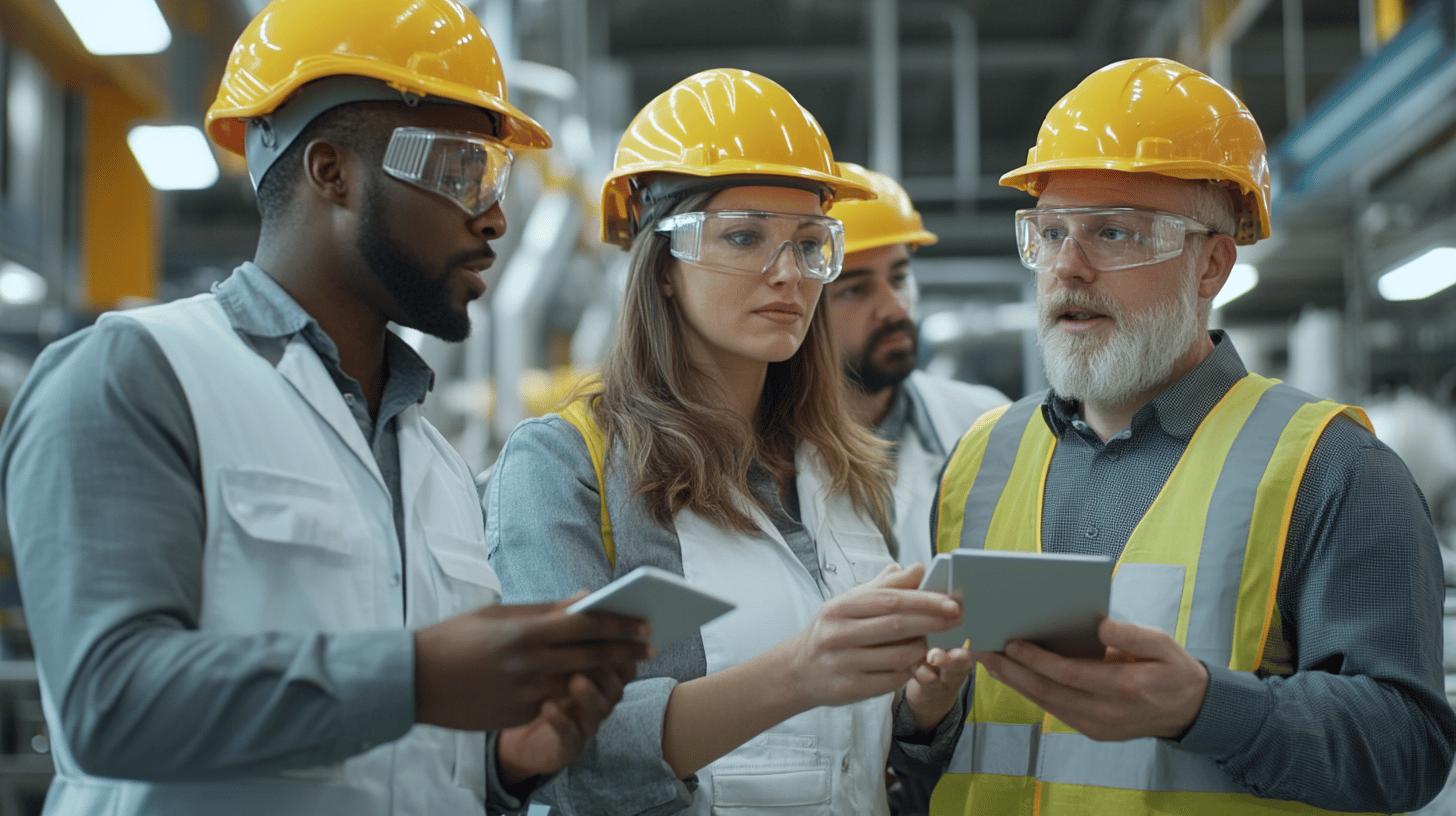
Supplier and Contractor Platforms Boost Compliance in Food Processing
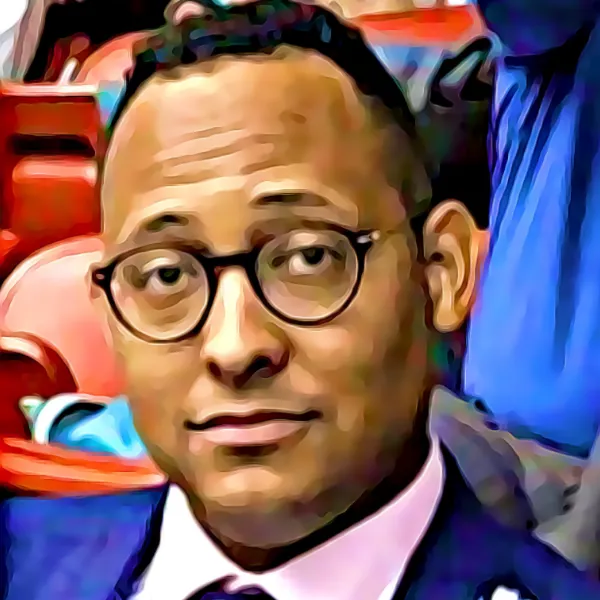
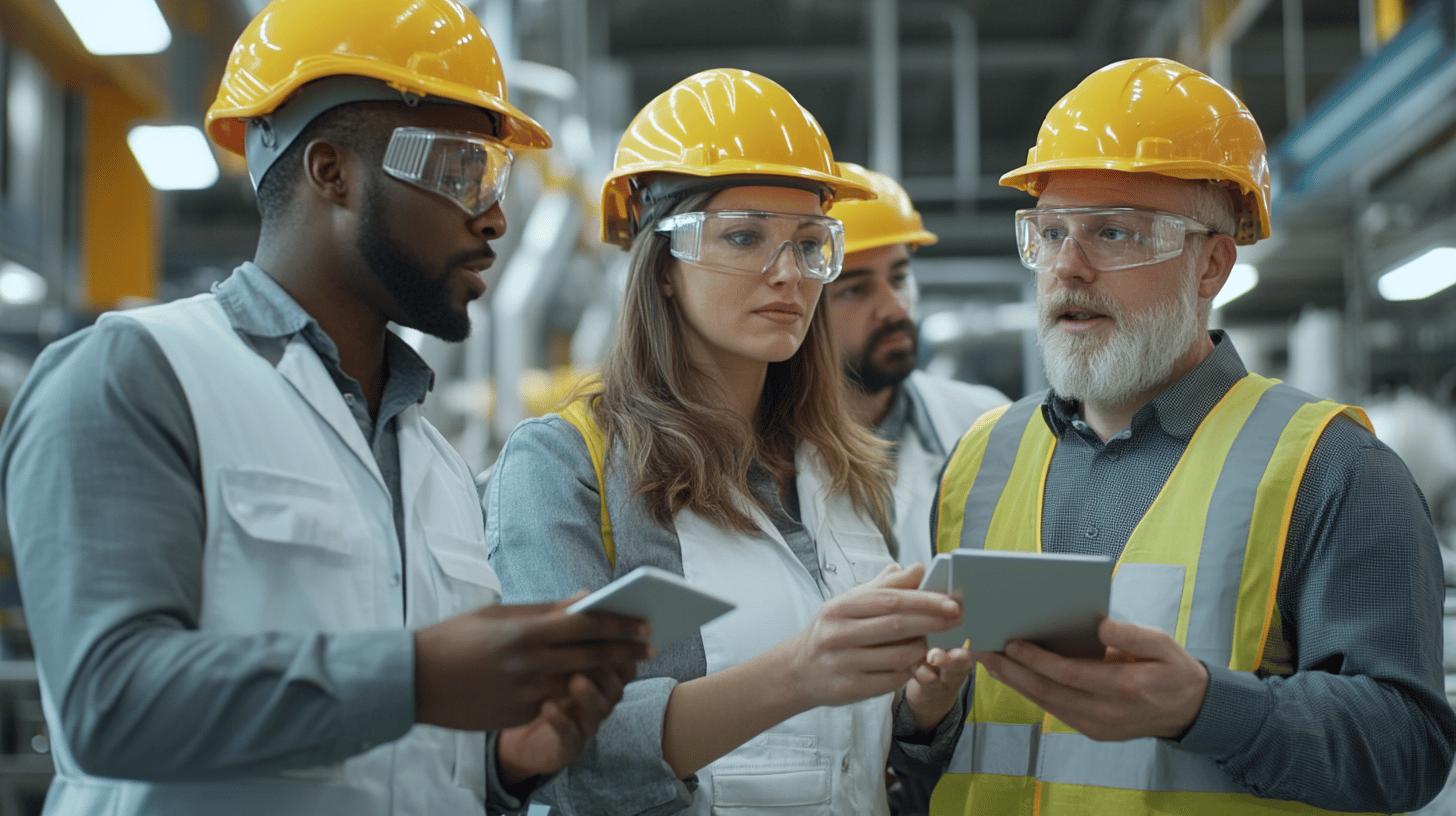
Supplier and Contractor Platforms Boost Compliance in Food Processing
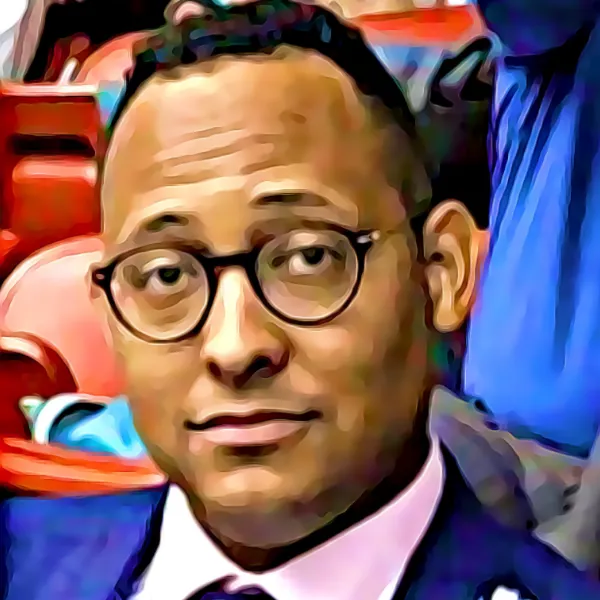
The Role of Supplier and Contractor Management Platforms in Compliance for Food Processing
Supplier and contractor management platforms have become essential tools in today's heavily regulated food processing industry. These digital solutions ensure businesses meet stringent regulatory requirements while maintaining operational efficiency. By providing real-time visibility into supplier and contractor activities, these platforms help food manufacturers avoid costly non-compliance issues and protect their operations from safety breaches and supply chain disruptions.
Without a proper system, verifying compliance across multiple suppliers against standards like the Food Safety Act 1990 or ISO 22000 can be overwhelming.
By integrating a robust supplier and contractor management system, food processors can centralize oversight and ensure real-time compliance across all suppliers. This enhanced management approach not only reduces manual reporting but also builds a strategic advantage in maintaining high standards in food safety and operational efficiency. Modern platforms address this challenge by automating workflows, sending certification reminders, flagging expired documentation, and conducting automated risk assessments based on real-time data.
Transforming Traceability in Food Supply Chains
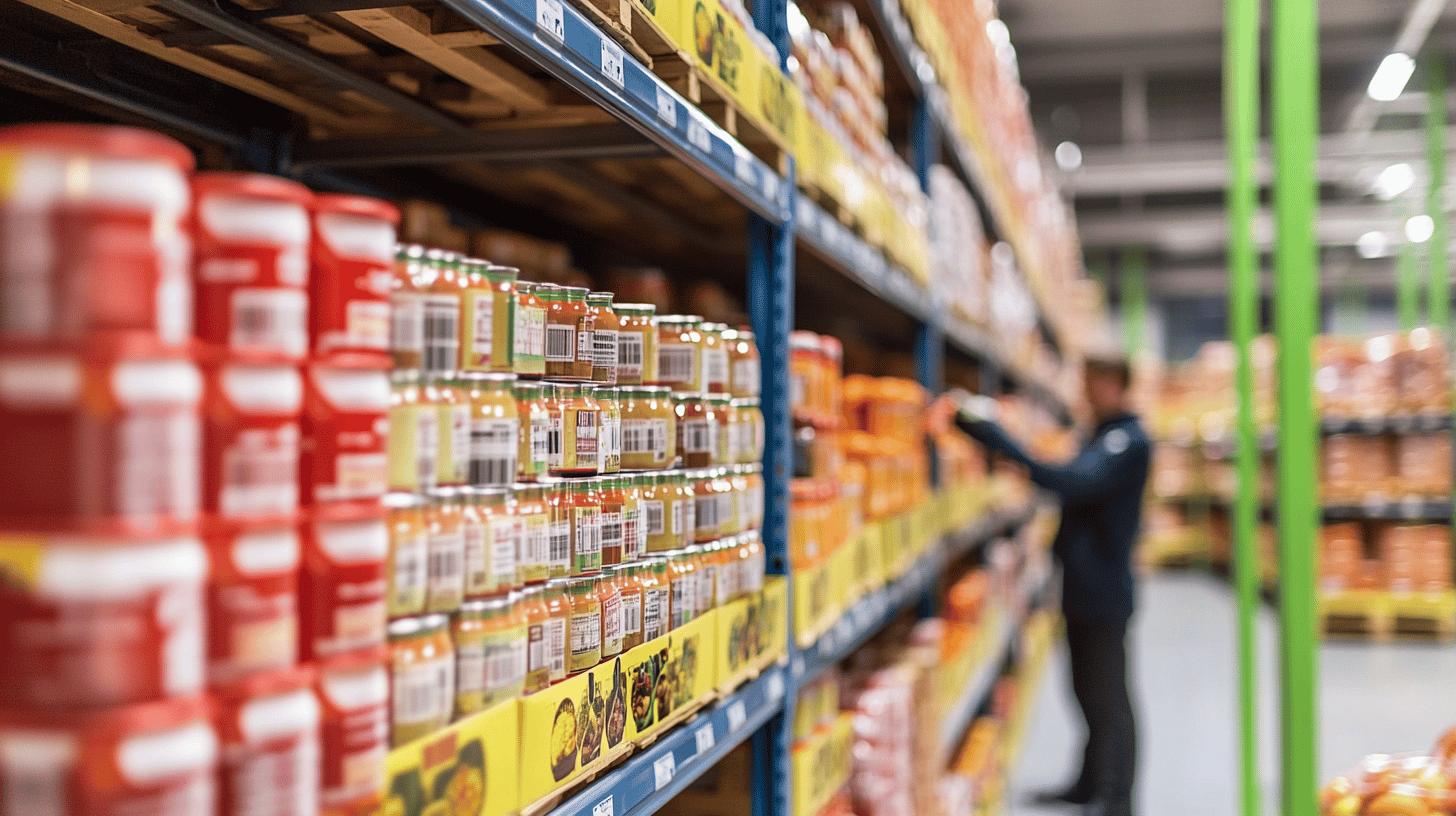
The food industry's reliance on traceability is non-negotiable for both safety and quality. Traditional tracking methods might take days to trace an ingredient through a complex supply chain, but digital platforms centralise this data, making it possible to pinpoint sources in minutes rather than hours.
This capability proves invaluable during product recalls, where rapid response can preserve consumer trust and protect brand reputation. A single search can identify affected products and enable swift corrective action when contamination issues arise.
By implementing a digital compliance platform, we reduced our trace-back time from days to under two hours during a recent recall situation, dramatically minimizing potential market impact.
These systems also enhance operational efficiency by eliminating redundant processes and reducing manual intervention. Instead of managing piles of paperwork for audits, digital dashboards provide instant access to all necessary documentation, saving valuable time and ensuring accuracy during inspections.
Key Features That Drive Compliance Excellence
Modern compliance management platforms offer several game-changing capabilities that transform how food processors approach regulatory requirements. These features work together to create a comprehensive compliance ecosystem.
Automated compliance checks represent a significant advancement. For instance, when a supplier's certification approaches expiration, the system automatically alerts all relevant parties, ensuring issues are addressed before they become problems. This proactive approach prevents compliance gaps that could lead to penalties or operational disruptions.
Real-time compliance tracking provides immediate visibility through centralised dashboards. During food safety audits, teams can instantly access current supplier status, certifications, and historical compliance data—saving hours of manual preparation and ensuring more successful outcomes.
Document management capabilities eliminate paper trails by digitising and organising essential records. In an industry where traceability is mandatory, having secure yet accessible digital records of supplier contracts, health certificates, and audit reports prevents documentation failures that could compromise food safety.
Strategic Approaches to Supplier Management
Effective supplier and contractor oversight requires a structured approach. Q-Hub's customisable compliance platforms help food processors implement the following essential strategies:
- Establish Clear Standards - Define and communicate compliance requirements for all suppliers and contractors, including necessary certifications and safety protocols
- Implement Thorough Evaluations - Create structured, repeatable assessment processes with automated risk scoring and gap identification
- Utilise Digital Checklists - Deploy customised compliance checklists that ensure consistent evaluation across different supplier types
- Prioritise Risk Management - Leverage real-time analytics to identify and address compliance issues before they escalate
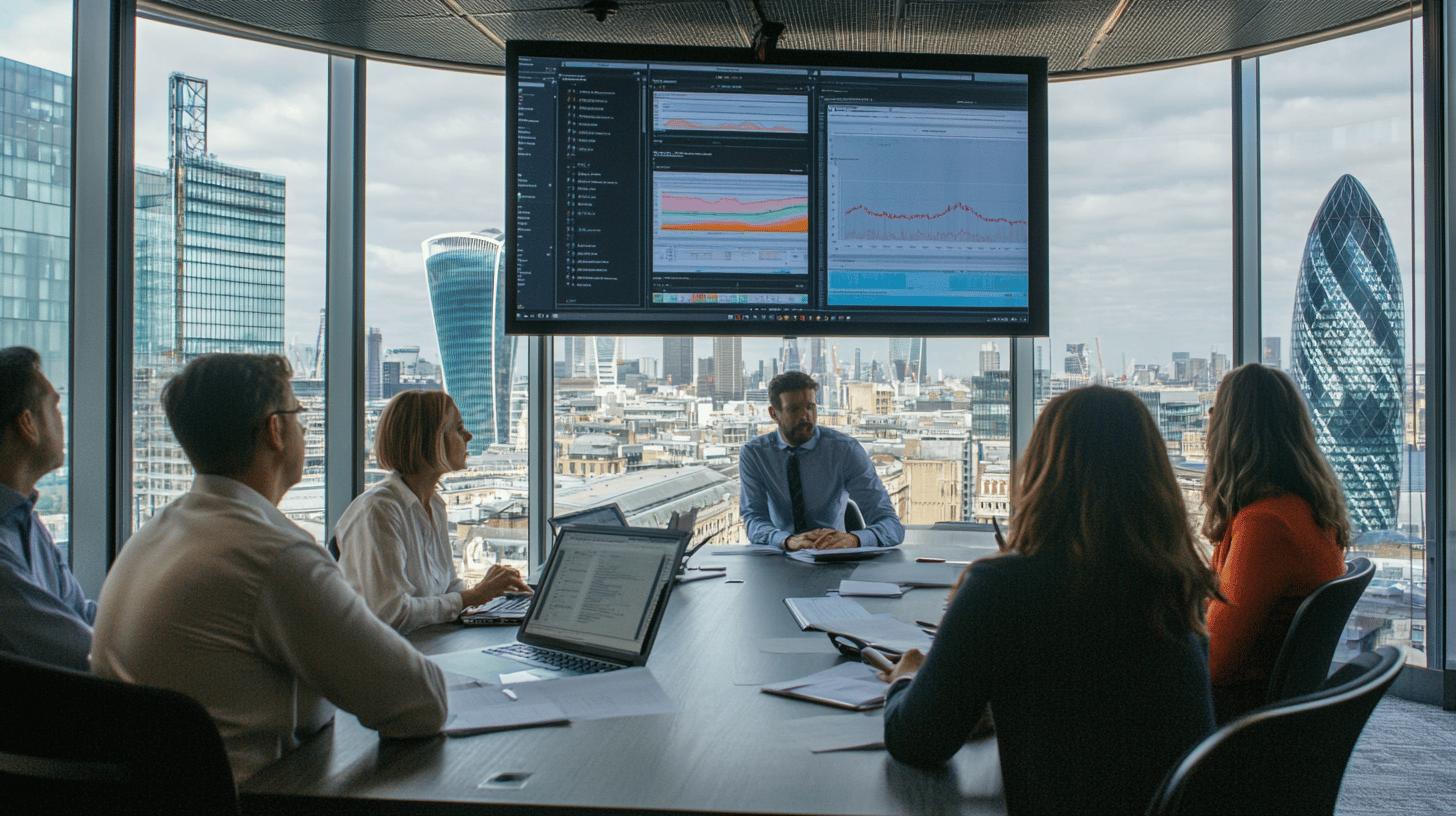
These strategies transform supplier management from a reactive task into a proactive, strategic advantage.
Incorporating custom development projects food compliance initiatives further strengthens the overall framework, ensuring tailored solutions that meet the unique challenges of the food processing industry. This approach leverages technology to create a seamless link between regulatory standards and operational execution, ultimately driving compliance excellence. By digitising and automating these processes, food processors can maintain consistent standards while significantly reducing manual effort.
Real-World Impact: Measurable Benefits of Digital Compliance
The transformation from manual to digital compliance management delivers quantifiable improvements for food processors. Consider these real-world outcomes:
<table border="0"> <tr><th>Metric</th><th>Before Automation</th><th>After Automation</th></tr> <tr><td>Audit Preparation Time</td><td>20+ hours</td><td>10 hours (50% reduction)</td></tr> <tr><td>Supplier Delivery Compliance</td><td>Variable</td><td>30% improvement</td></tr> <tr><td>Recall Trace-back Time</td><td>Days</td><td>Under 2 hours</td></tr> <tr><td>Non-compliance Incidents</td><td>Regular occurrences</td><td>40% reduction</td></tr> </table>Similar to how the Anglia Cathodic Protection case study demonstrates, centralising documentation and processes delivers transformative efficiency gains. When fragmented systems are replaced with integrated digital platforms, visibility improves across operations.
The Future: AI-Powered Compliance Intelligence
The evolution of compliance management continues at pace, with several emerging trends reshaping how food processors approach regulatory requirements. Proactive risk management stands at the forefront, with modern platforms now incorporating predictive analytics to identify potential issues before they occur.
AI and machine learning technologies are revolutionising how companies handle compliance tasks. These systems can analyse supplier performance patterns, automatically verify documentation, and even predict potential supply chain disruptions based on historical data. This shift from reactive to proactive oversight represents a fundamental change in compliance philosophy.
As demonstrated in the Scottish Leather Group case study, organisations that adopt digital transformation for compliance management gain significant competitive advantages through improved efficiency and reduced risk.
Supplier and contractor management platforms aren't just technological solutions—they're strategic business tools that enable food processors to navigate increasingly complex regulations while improving operational performance. Companies that partner with experienced providers like Q-Hub to implement these systems position themselves for sustainable growth and excellence in food safety compliance.
Start using Q-Hub today
- Manage compliance in one place
- Streamline your teams and tasks
- Use Q-Hub free for 30 days