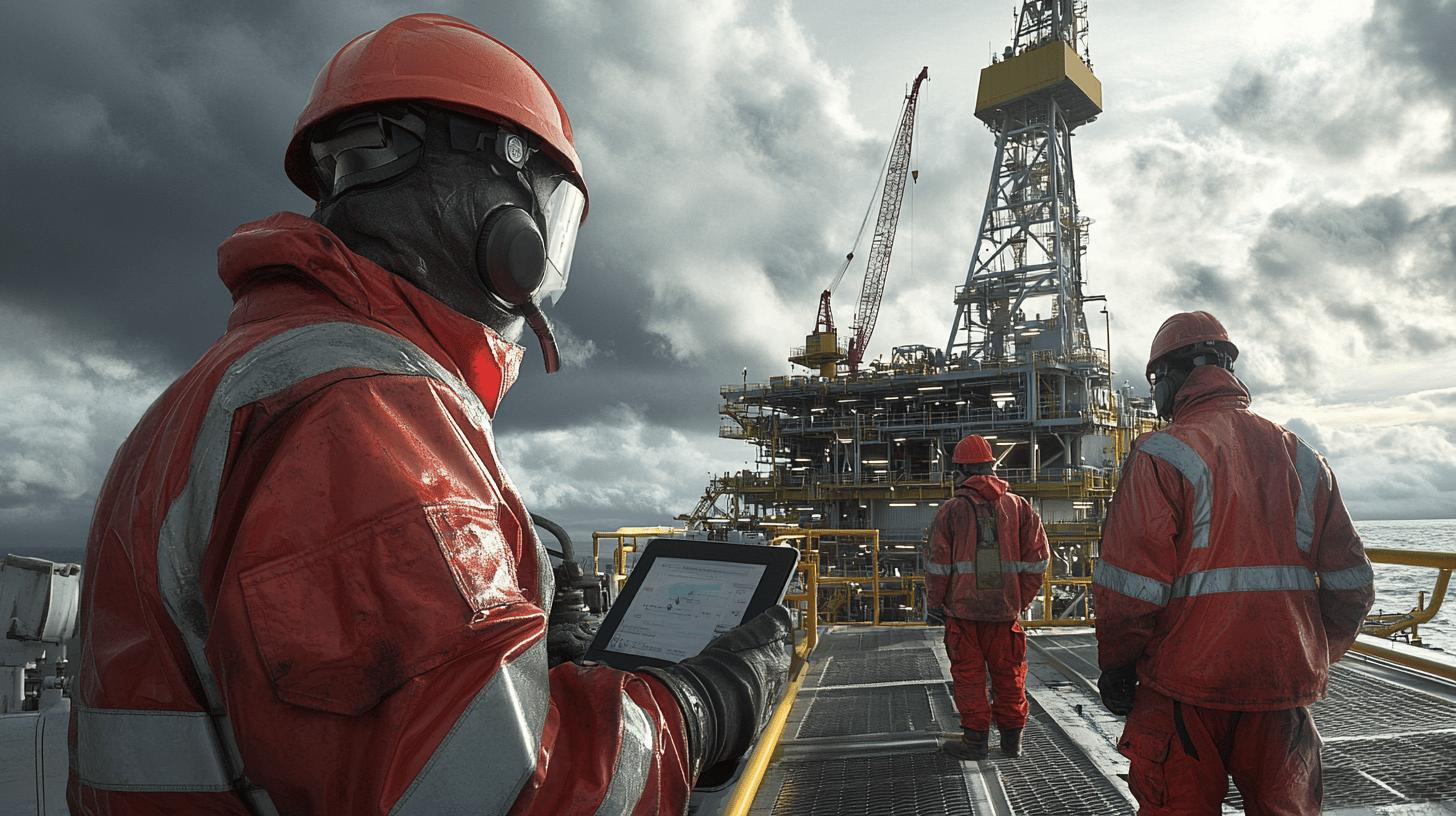
Enterprise Incident Reporting Solutions Boost Oil, Gas Response
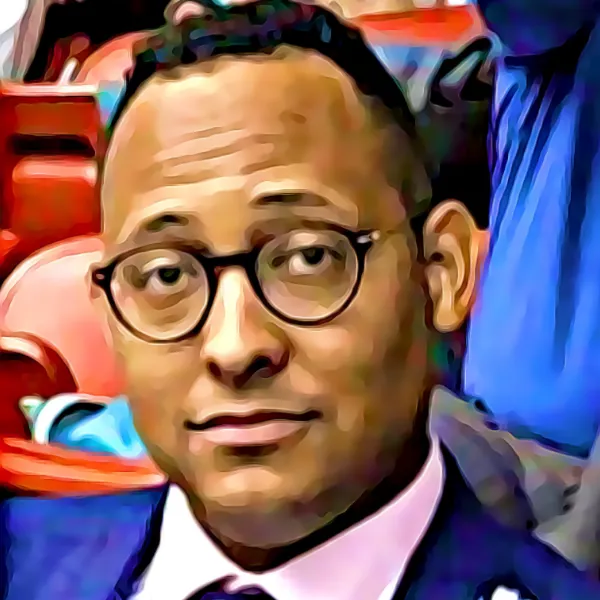
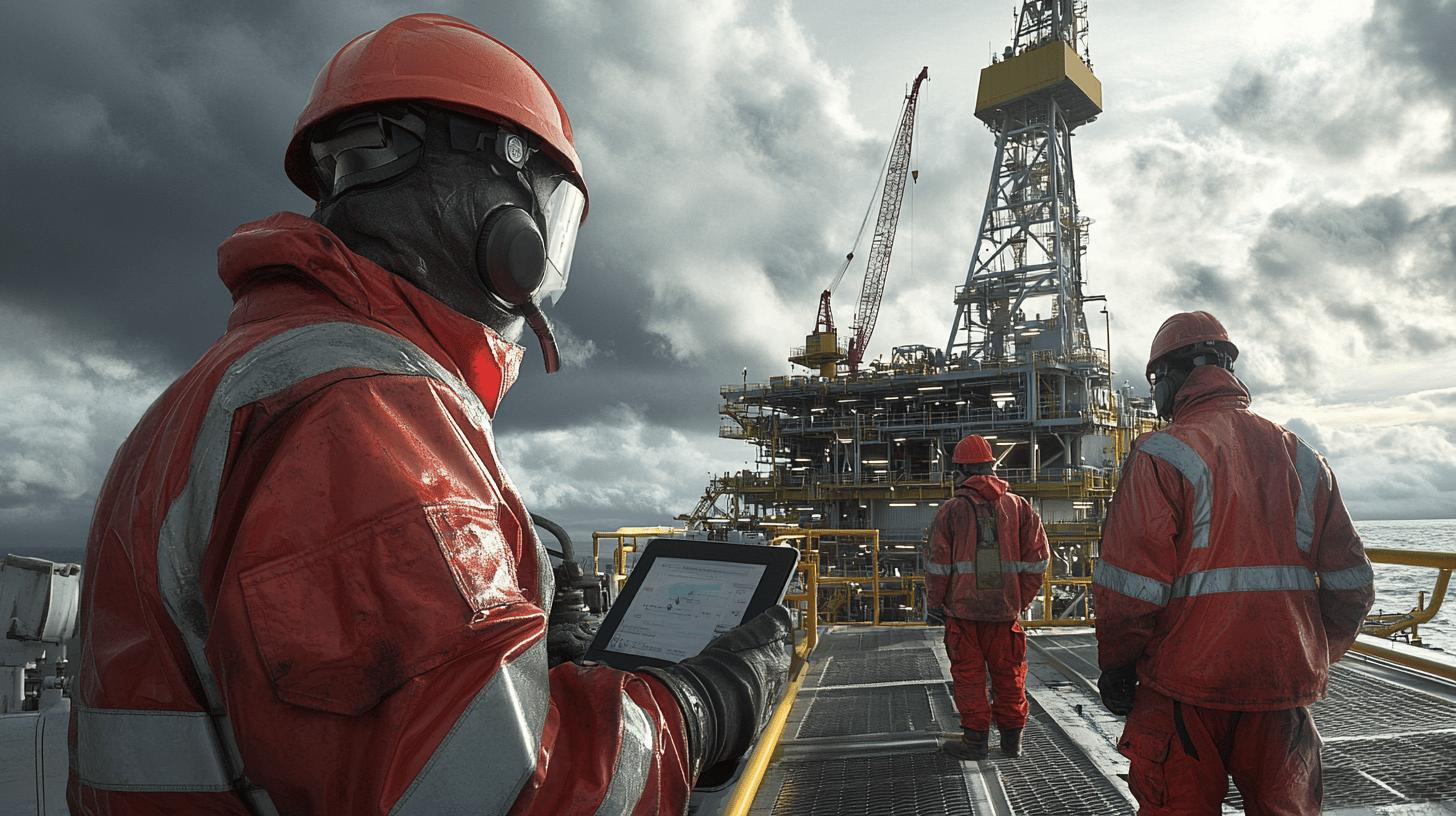
Enterprise Incident Reporting Solutions Boost Oil, Gas Response
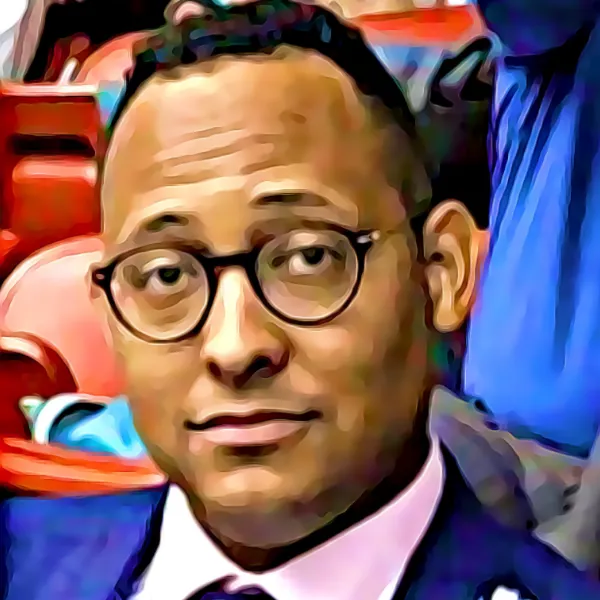
Key Features of Enterprise Incident Reporting Solutions for Oil and Gas Production
Enterprise incident reporting solutions are mission-critical systems for the oil and gas sector, delivering far more than simple documentation tools. These sophisticated platforms combine real-time alerts, automated workflows, and data analytics to create a safety ecosystem that responds instantly to emerging threats. Q-Hub specialises in developing such solutions that transform how oil and gas operations manage risk and maintain compliance in high-stakes environments.
When incidents occur in oil and gas production—whether equipment failures, safety breaches, or environmental concerns—every second counts. Modern reporting solutions eliminate manual processes that cause delays and potential escalation of minor issues into major crises. Instead, they enable immediate capture, notification, and resolution coordination.
The Building Blocks of Effective Incident Management
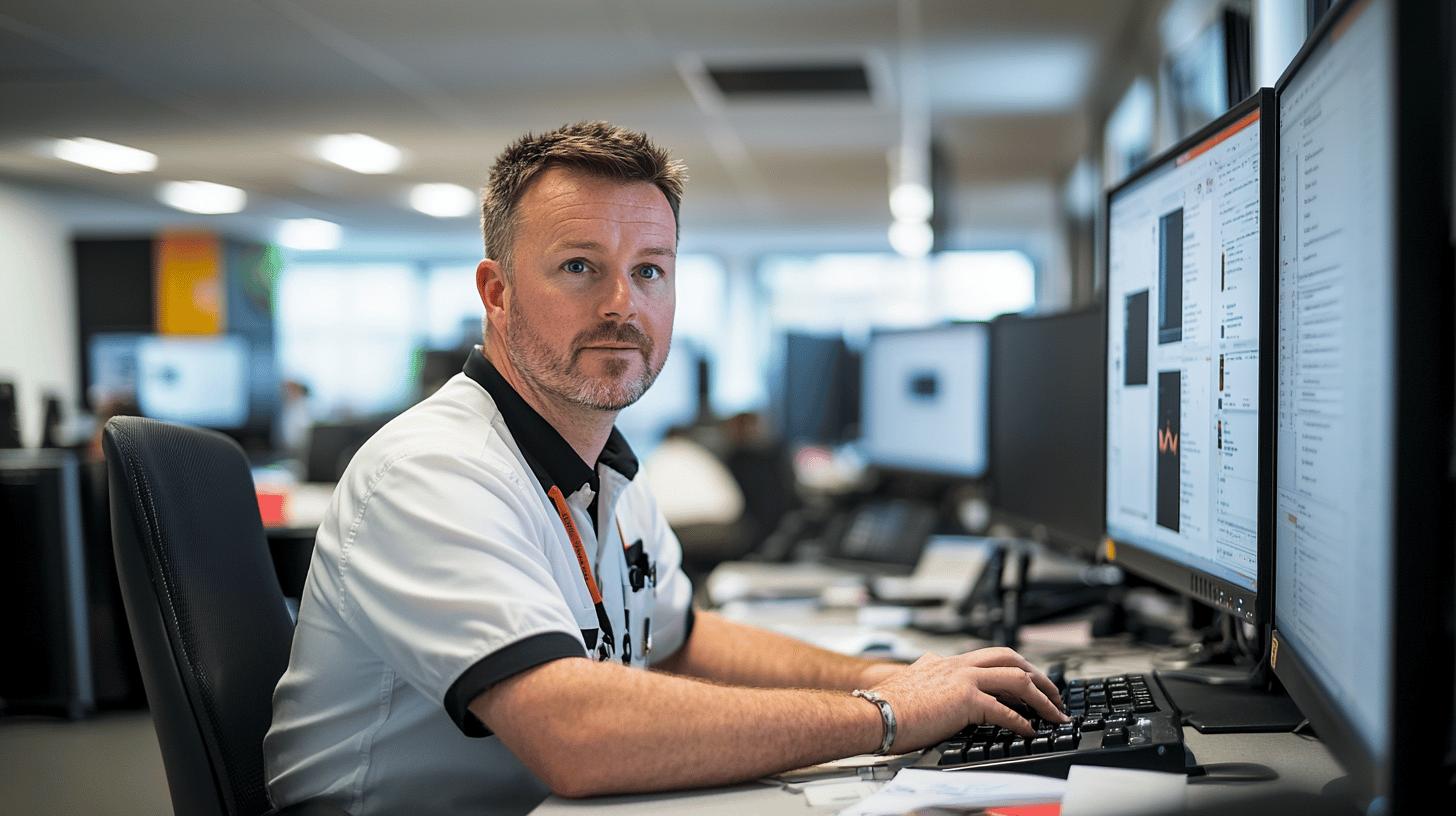
At their core, effective incident reporting systems for oil and gas operations include several essential components. Real-time alerting capabilities ensure the right personnel receive immediate notifications when issues arise. Meanwhile, automated workflows direct responses according to pre-defined protocols, eliminating guesswork during critical moments.
Integration capabilities allow these systems to communicate seamlessly with existing safety frameworks, ERP systems, and compliance tools. This creates a unified approach to incident management rather than isolated processes that create information silos.
The ability to instantly capture, categorise, and respond to incidents transformed our safety culture. What previously took hours now happens within minutes, giving us crucial time to prevent escalation of safety issues.
Advanced analytics provide perhaps the most significant long-term value. By examining incident patterns, these systems identify recurring issues and potential weak points before they cause problems. This shifts operations from reactive to proactive safety management—a crucial advantage in high-risk environments.
- Customisable reporting templates that align with RIDDOR and ISO requirements
- Root cause analysis tools to prevent incident recurrence
- Mobile accessibility for field reporting and response
- Automated compliance documentation and audit trails
- Visual dashboards for monitoring safety performance metrics
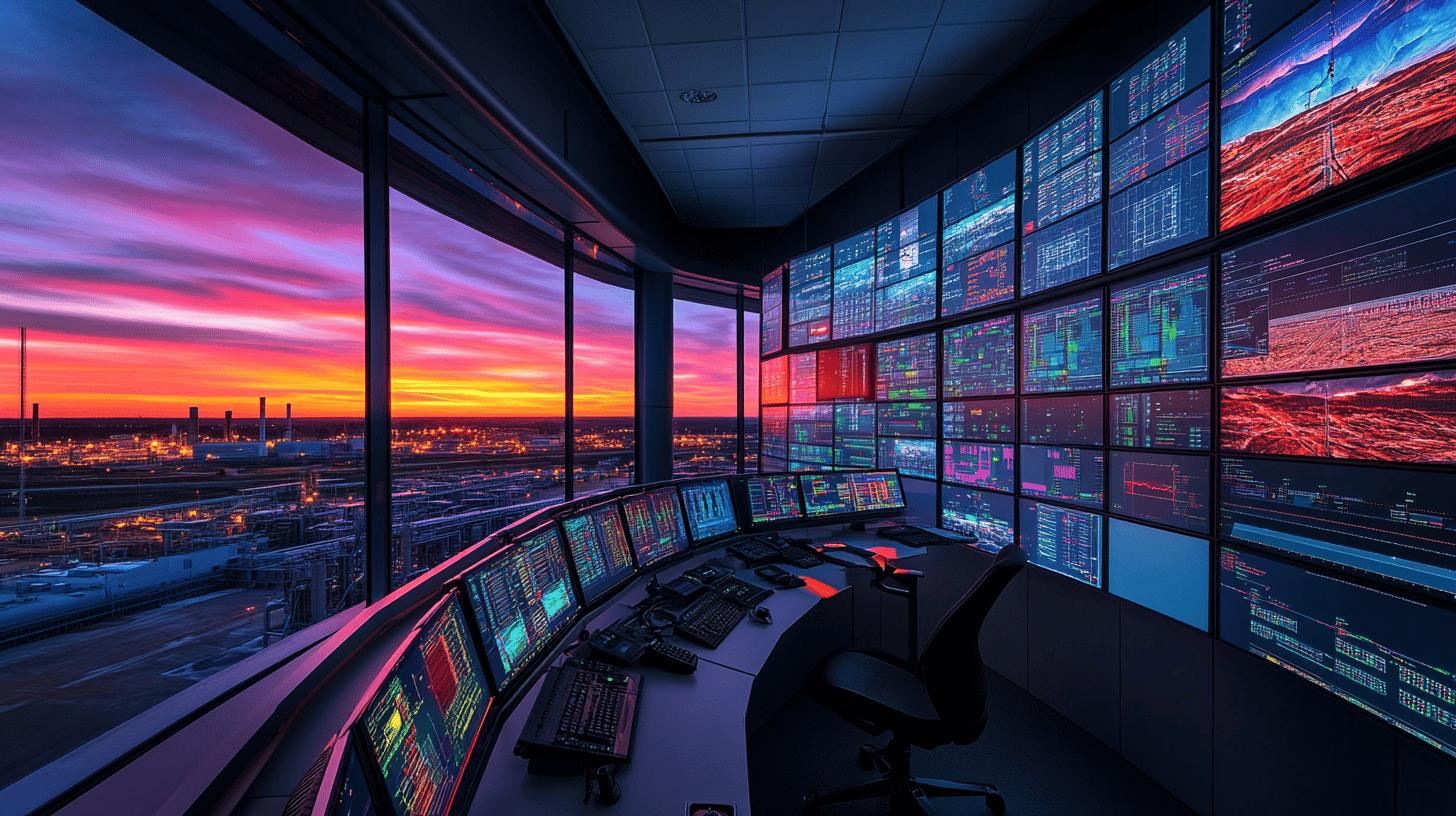
Benefits of Swift Incident Response in Oil and Gas Production
In the high-stakes world of oil and gas operations, the speed and quality of incident response directly impact operational continuity, regulatory compliance, and environmental protection. Enterprise incident reporting solutions ensuring swift response to issues in oil and gas production create a structured framework that transforms chaotic emergency situations into organised response efforts.
The most immediate benefit is operational resilience. When issues are identified and addressed rapidly, production disruptions are minimised, preventing the cascade of delays that typically follow incidents. This operational continuity translates directly to financial savings—studies show that production downtime in oil and gas can cost between £15,000-£250,000 per hour depending on facility size.
From Reactive to Proactive: Transforming Safety Culture
Beyond immediate incident handling, swift response systems fundamentally change how organisations approach safety. With proper implementation, these digital tools create transparency around safety incidents, making them visible rather than hidden. This visibility encourages reporting and establishes accountability at all levels.
Environmental protection becomes significantly more effective with rapid response capabilities. When containment actions begin within minutes rather than hours, the environmental impact of spills or releases can be reduced by up to 60%. This not only protects ecosystems but also reduces remediation costs and regulatory penalties.
Here's how these systems transform operational performance across key metrics:
<table border="0"> <tr><th>Metric</th><th>Before Digital Reporting</th><th>After Implementation</th></tr> <tr><td>Average Incident Response Time</td><td>45-90 minutes</td><td>5-15 minutes</td></tr> <tr><td>Compliance Documentation</td><td>Hours</td><td>Automated</td></tr> <tr><td>Recurring Incidents</td><td>25-30%</td><td>Below 10%</td></tr> <tr><td>Near-Miss Reporting</td><td>Limited</td><td>Comprehensive</td></tr> </table>Beyond Compliance: Building Stakeholder Trust
Swift incident reporting creates value beyond operational improvements. As Scottish Leather Group discovered when implementing Q-Hub's solutions, digital transformation of safety processes builds confidence among employees, regulators, and clients. Their implementation of a comprehensive incident management system improved not just response times but also interdepartmental communication and overall operational visibility.
Perhaps most importantly, these systems support continuous improvement. By capturing detailed data on each incident, they enable sophisticated trend analysis that reveals systemic issues. This allows organisations to address root causes rather than symptoms, creating lasting safety improvements.
Integration Capabilities: The Power of Connected Systems
Enterprise incident reporting solutions are only as effective as their ability to communicate with existing operational systems. In oil and gas environments—where operations often span multiple platforms, involve diverse teams, and generate enormous data volumes—this integration capability becomes essential for success.
Q-Hub's approach to integration focuses on eliminating information silos that typically hinder incident response. When reporting systems operate in isolation, critical data remains trapped, slowing decision-making and creating fragmented views of operational status.
Seamless Connections Through Custom APIs
The key to effective integration lies in custom Application Programming Interfaces (APIs) that connect incident reporting systems with other enterprise software. These digital bridges allow information to flow automatically between platforms without manual intervention.
For example, when an incident is reported through a field device, the system can simultaneously update maintenance management systems, notify relevant personnel, and create compliance documentation. This automation eliminates delays and ensures consistent information across all platforms.
Real-world implementations demonstrate the value of this approach. One offshore operator integrated their incident reporting system with equipment monitoring tools, creating automatic alerts when parameters deviated from safe ranges. This proactive approach reduced reportable incidents by 35% in the first year.
Centralised Data: Creating a Single Source of Truth
Beyond technical connections, effective integration creates centralised data repositories that serve as a unified source of truth. This consolidation provides critical advantages during incident response, when accessing accurate information quickly can prevent escalation.
Centralisation allows operators to quickly find historical data, identify patterns, and coordinate responses without switching between systems. This comprehensive view transforms disjointed information into actionable intelligence, enhancing both routine operations and emergency response.
As Weston Aerospace discovered when implementing Q-Hub's solutions, centralised data repositories dramatically reduce the time required for compliance activities while improving data accuracy. Their experience demonstrates how integration capabilities deliver benefits well beyond basic incident reporting.
Cost Implications and ROI of Incident Reporting Solutions
Implementing comprehensive incident reporting solutions represents a significant investment for oil and gas operations. Beyond the initial software costs, organisations must consider implementation, training, and system maintenance expenses. However, when evaluated against the financial impact of incidents, these investments typically deliver substantial returns.
The business case begins with quantifying the true cost of incidents. Beyond the immediate operational disruption, organisations must consider regulatory penalties, potential litigation, insurance implications, remediation costs, and reputational damage. A single major incident can cost millions in direct expenses alone.
Breaking Down the Investment vs. Returns
Initial implementation costs typically include software licensing or subscription fees, implementation services, data migration, integration with existing systems, and staff training. For mid-sized operations, this investment often ranges from £50,000-£150,000 depending on complexity and scope.
However, the returns begin accumulating immediately. Companies implementing Q-Hub's incident management solutions typically report 30-40% reductions in administrative time spent on compliance documentation. The automation of routine tasks liberates staff to focus on higher-value activities while ensuring nothing falls through the cracks.
More significantly, effective incident management systems dramatically reduce incident frequency and severity through improved risk identification and proactive intervention. Industry data suggests that comprehensive reporting systems can reduce recordable incidents by 20-30% within the first year of implementation.
The financial implications of these improvements include:
- Reduced production downtime and associated revenue losses
- Lower insurance premiums through demonstrated safety improvements
- Decreased compliance costs and potential regulatory penalties
- Reduced investigation and remediation expenses
- Improved workforce retention through enhanced safety culture
The Intangible Benefits: Culture and Reputation
Beyond quantifiable returns, incident reporting solutions deliver substantial intangible benefits. Most notably, they transform safety culture by increasing transparency, accountability, and engagement. When employees see that reported issues receive prompt attention, reporting rates increase—creating a virtuous cycle of continuous improvement.
Similarly, robust incident management enhances reputation with clients, regulators, and communities. In an industry where stakeholder trust is increasingly valuable, these reputational benefits translate to concrete business advantages, from preferential contract consideration to smoother regulatory relationships.
As BMC Analysis discovered when implementing Q-Hub's solutions, the combination of tangible efficiency gains and cultural improvements delivers a compelling return on investment that extends far beyond simple cost reduction.
Future Trends: What's Next for Incident Management
The evolution of incident reporting in oil and gas continues at a rapid pace, with emerging technologies promising even greater capabilities. These innovations aren't just incremental improvements—they represent fundamental shifts in how organisations identify, manage, and prevent incidents.
AI-Powered Prediction: Stopping Incidents Before They Happen
Artificial intelligence and machine learning are transforming incident management from reactive to predictive. These technologies analyse vast datasets to identify subtle patterns that human observers might miss. In practice, this means detecting potential equipment failures, process deviations, or safety risks before they cause incidents.
Advanced predictive systems can evaluate combinations of factors—weather conditions, equipment status, maintenance history, and operational parameters—to calculate risk probabilities with remarkable accuracy. This foresight allows operations to intervene proactively, scheduling maintenance or modifying procedures to prevent emerging issues.
The impact of these capabilities is substantial. Early adopters report 15-25% reductions in unplanned downtime through predictive maintenance alone. When combined with comprehensive safety systems, the prevention potential grows even further.
IoT and Edge Computing: Real-Time Awareness
The proliferation of IoT sensors throughout oil and gas operations creates unprecedented visibility into operational conditions. Modern facilities may deploy thousands of sensors monitoring everything from pressure and temperature to vibration patterns and emissions levels.
These sensors generate enormous data volumes that, when processed through edge computing systems, provide real-time operational awareness. Rather than waiting for manual inspection or reporting, these systems continuously monitor conditions and automatically trigger alerts when parameters deviate from safe ranges.
The combination of IoT and edge computing dramatically reduces response times while increasing detection accuracy. A pipeline monitoring system using distributed sensors, for example, can detect and locate potential leaks within seconds rather than hours, enabling immediate containment actions.
Augmented Reality: Enhancing Response Effectiveness
Augmented reality (AR) is emerging as a powerful tool for incident response in complex operational environments. These systems overlay digital information onto the physical world, providing responders with critical data exactly when and where they need it.
In practice, field personnel equipped with AR devices can access equipment specifications, procedural guidance, and real-time sensor data while maintaining situational awareness. This capability is particularly valuable during emergency response, when quick access to accurate information can prevent escalation.
These technological advances aren't developing in isolation—they
Start using Q-Hub today
- Manage compliance in one place
- Streamline your teams and tasks
- Use Q-Hub free for 30 days