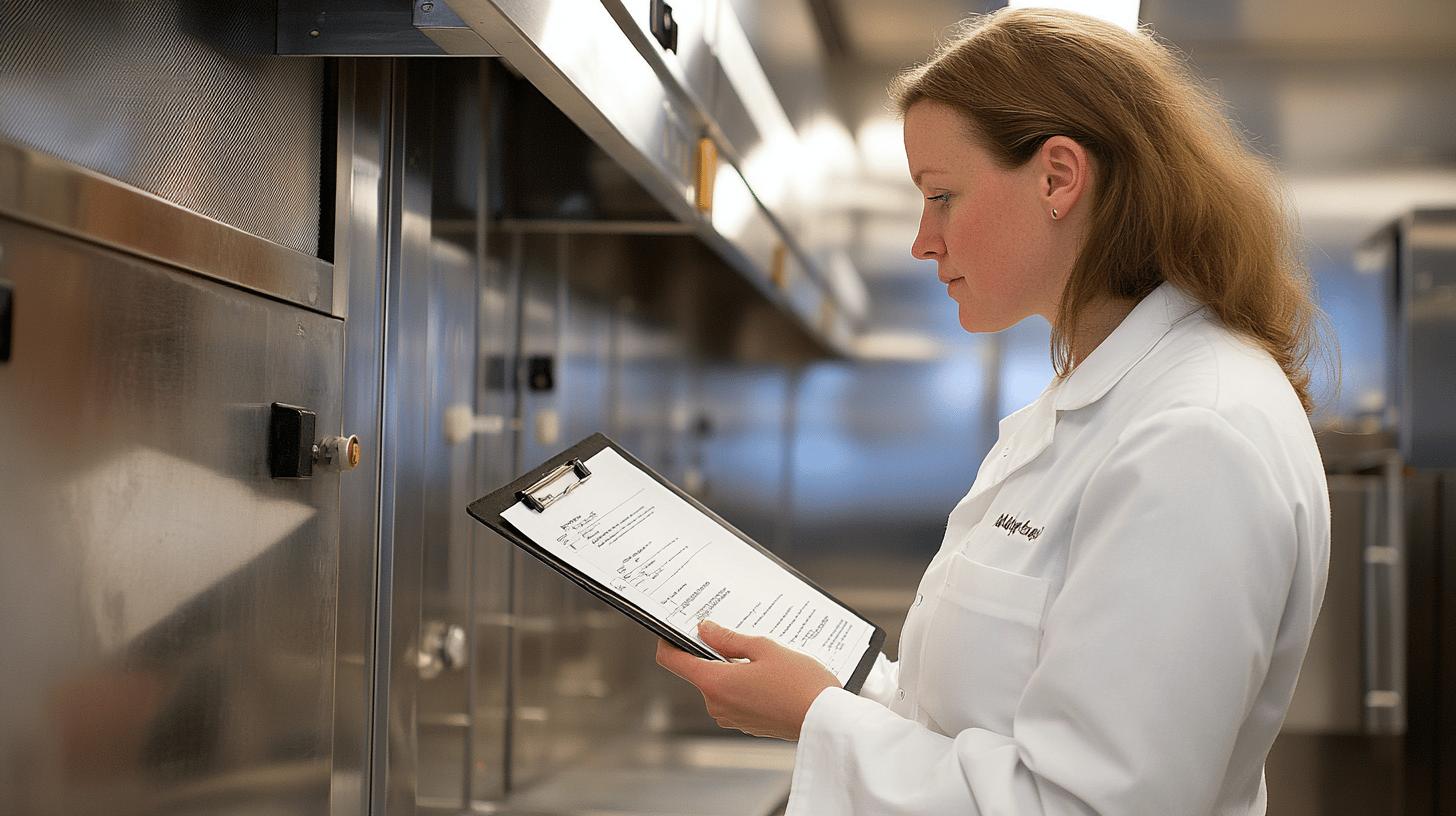
Enterprise Audit and Inspection Solutions for Food Industry
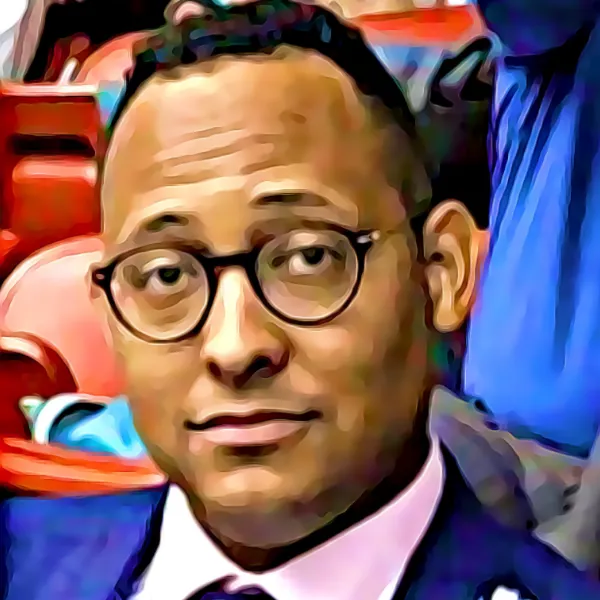
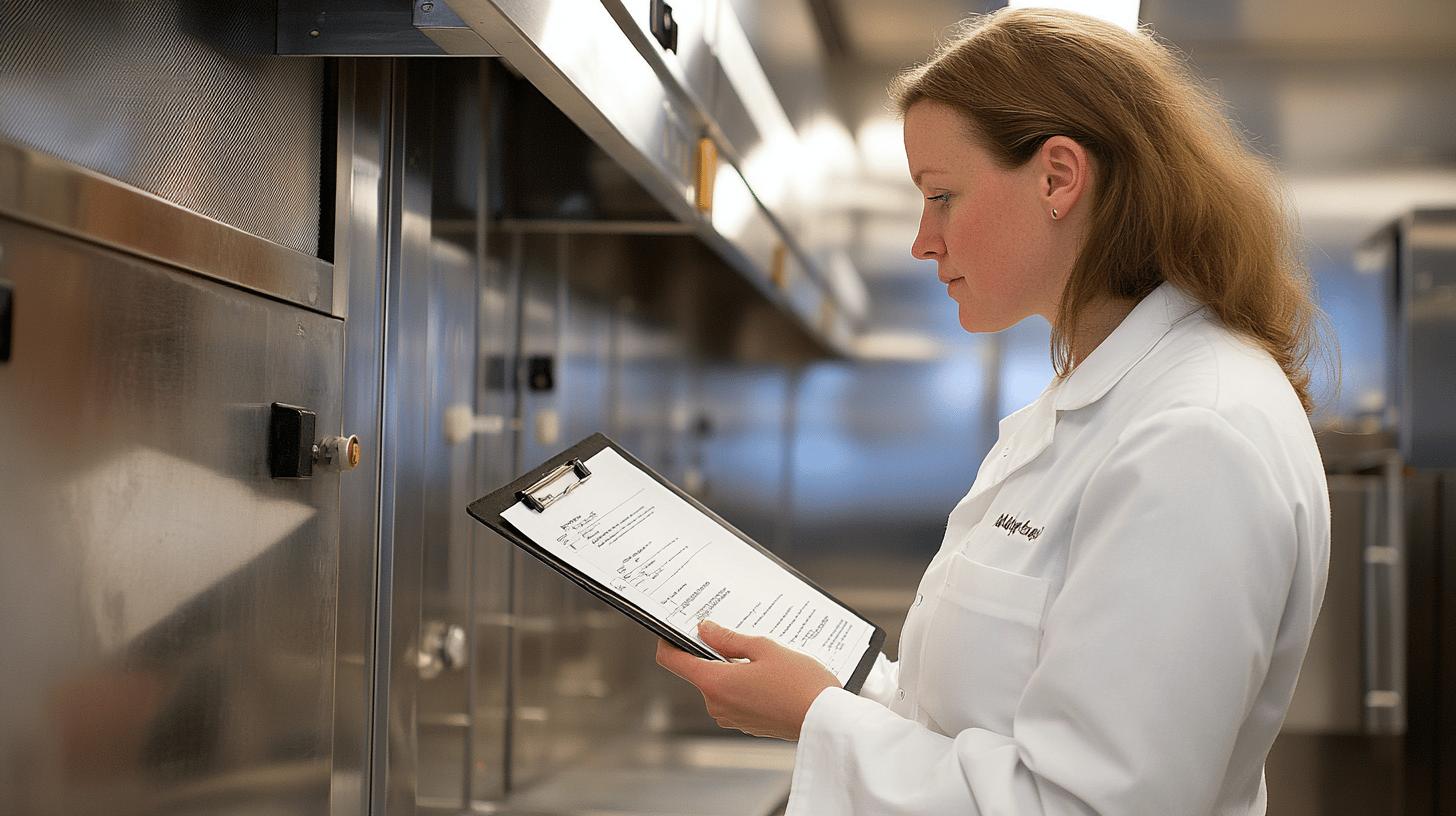
Enterprise Audit and Inspection Solutions for Food Industry
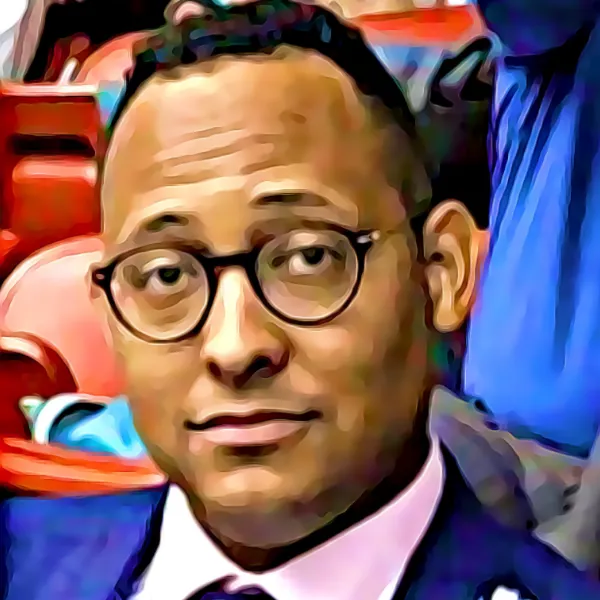
Key Features of Enterprise Audit and Inspection Solutions for the Food Processing Industry
Digital transformation has revolutionised food safety management, with enterprise audit and inspection solutions becoming essential tools for modern food processors. These systems replace outdated paper-based methods with streamlined digital workflows that enhance compliance, reduce risks, and drive operational efficiency. Q-Hub's specialised solutions help food processors navigate complex regulatory requirements whilst optimising quality control processes.
Transforming Inspections Through Real-Time Capabilities
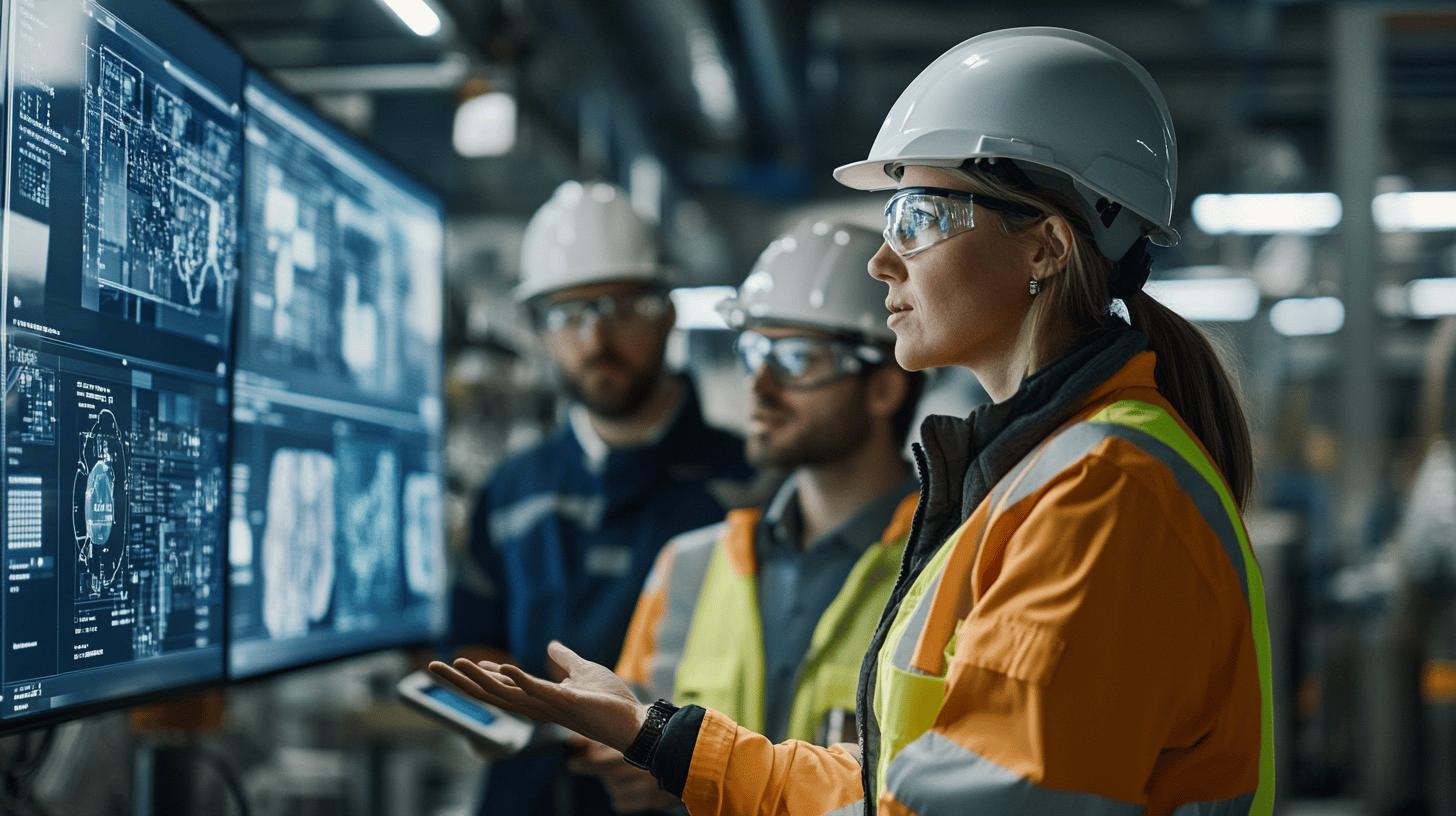
The ability to capture and analyse data in real time represents a fundamental shift in how food safety inspections are conducted. When inspectors identify issues during hygiene checks, the system immediately flags deviations from standards, allowing for instant corrective action.
Mobile accessibility has similarly revolutionised on-site auditing. Inspectors now conduct thorough evaluations using tablets or smartphones directly on the production floor, even in areas with limited connectivity. This eliminates the inefficient process of recording observations manually and later transferring them to digital systems.
The implementation of Qhub transformed our audit processes, reducing preparation time from days to mere hours while improving overall compliance visibility across all our facilities.
Customisable digital forms adapt to specific inspection requirements, whether for allergen control in bakeries or temperature monitoring in meat processing. These flexible templates ensure comprehensive data collection without overwhelming users with unnecessary fields.
Companies adopting these solutions typically experience several key benefits:
- Up to 50% reduction in total audit completion time
- Significant decrease in compliance-related incidents
- Enhanced traceability across the entire production process
- Improved interdepartmental communication
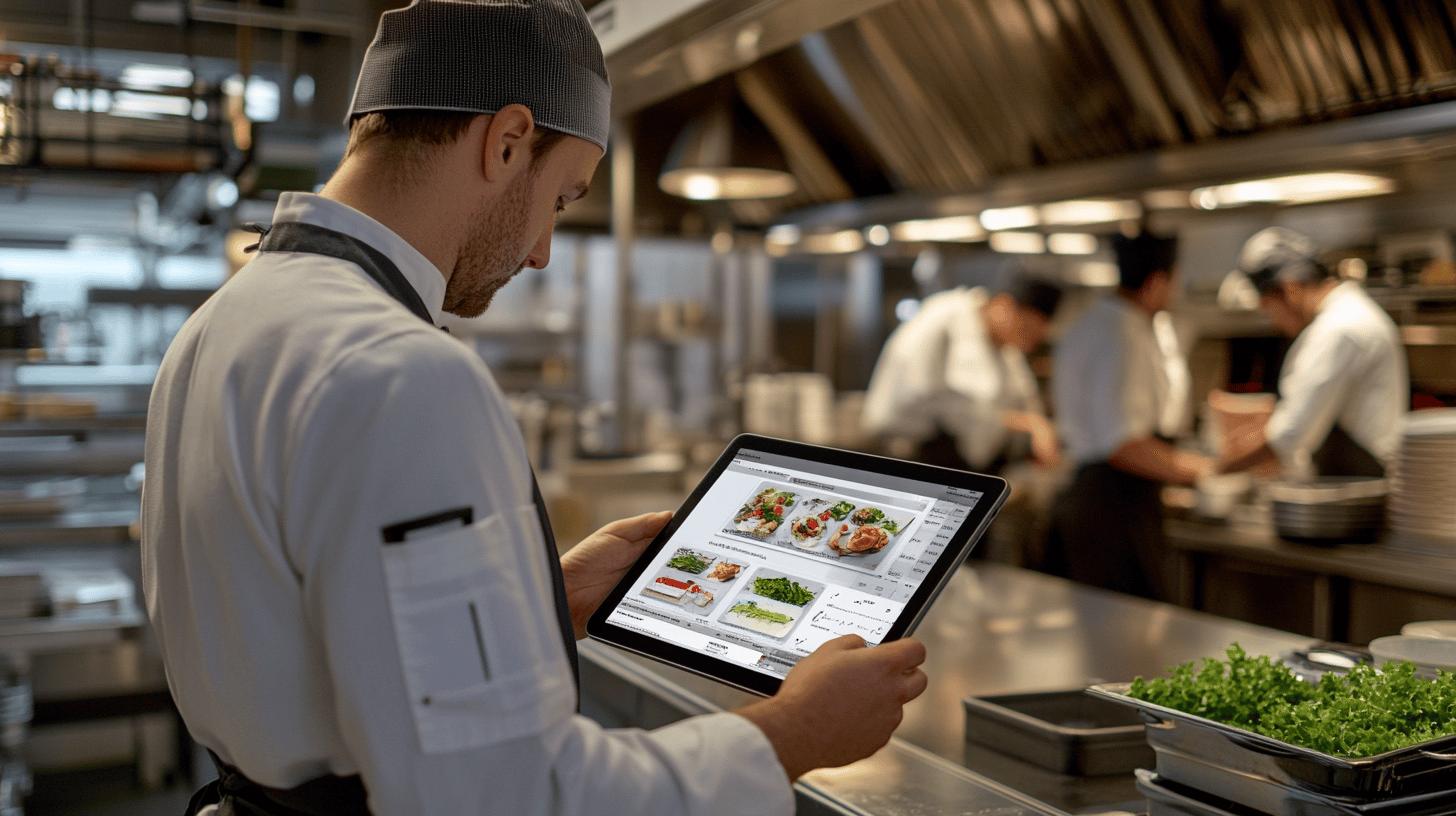
Breaking Down Regulatory Complexity with Intelligent Systems
Food safety frameworks like HACCP, FSMA and FSSC 22000 present complex compliance challenges. Modern audit platforms simplify these requirements by providing structured workflows that guide users through every stage of compliance management.
For instance, Scottish Leather Group implemented Q-Hub's Audit Hub to manage multiple ISO standards within a single platform, significantly reducing audit preparation time while improving reporting capabilities across their facilities.
The integration capabilities of these systems further enhance their value. By connecting with existing ERP and QMS platforms, audit solutions ensure that critical inspection data flows seamlessly between departments. When non-conformities are flagged, the information instantly reaches relevant teams, triggering appropriate responses without manual intervention.
Here's how enterprise solutions compare to traditional methods:
<table border="0"> <tr><th>Metric</th><th>Before Automation</th><th>After Automation</th></tr> <tr><td>Audit Preparation Time</td><td>Days</td><td>Hours</td></tr> <tr><td>Issue Response Time</td><td>48+ hours</td><td>Same day</td></tr> <tr><td>Document Control</td><td>Manual version tracking</td><td>Automated with validation</td></tr> <tr><td>Cross-Department Visibility</td><td>Limited</td><td>Real-time shared access</td></tr> </table>Enhancing Risk Prevention Through Predictive Intelligence
The preventative power of AI-driven analytics represents perhaps the most significant advancement in food safety management. These systems analyse historical and real-time data to identify potential hazards before they materialise.
Consider temperature monitoring in cold storage. Traditional systems might only alert when temperatures exceed thresholds. Advanced predictive systems detect subtle patterns indicating potential refrigeration failures hours or days before critical issues develop, preventing costly product loss.
Case Study: Proactive Risk Management in Action
When Fowlers of Bristol implemented Q-Hub's quality management system, they gained unprecedented visibility into their "Right First Time" performance metrics. The platform linked actions to forms and registers, streamlining issue identification and resolution while driving their "Zero Defects" initiative. Learn more about Fowlers' transformation.
Continuous monitoring capabilities ensure round-the-clock vigilance over critical control points. If sanitation processes fall short of standards, the system immediately triggers alerts, prompting swift corrective action before contamination risks emerge.
Implementing Success: Strategic Approaches to Digital Transformation
Successful implementation requires more than just software installation. Based on Q-Hub's experience helping food processors digitalise their compliance processes, several best practices have emerged.
First, clearly define audit objectives and align them with business goals. When BMC Analysis implemented Q-Hub's Process Hub, they specifically targeted NCR management inefficiencies, resulting in dramatically improved resolution times and tracking capabilities.
Staff training represents another critical factor. The most sophisticated system provides limited value if users don't understand how to leverage its capabilities effectively. Comprehensive training ensures that everyone from shop floor workers to quality managers can navigate the platform confidently.
Establishing dynamic inspection schedules that adapt to production volumes, seasonal demands, and regulatory changes helps maintain consistent compliance. These schedules should incorporate continuous improvement methodologies like PDCA (Plan-Do-Check-Act) to refine processes over time.
The Future of Food Safety: Connected Compliance Ecosystems
The evolution of enterprise audit solutions is moving toward fully integrated compliance ecosystems. These platforms will increasingly incorporate Internet of Things (IoT) sensors that automatically feed real-time production data directly into audit systems, further reducing manual monitoring.
Cloud-based architecture offers particular advantages for multi-site operations. When Anglia Cathodic Protection Services implemented Q-Hub's platform, they were able to unify their previously fragmented compliance systems, creating centralised visibility across their expanding operations.
Remote auditing capabilities will continue expanding, allowing food processors to maintain robust compliance oversight even in challenging circumstances. This flexibility proved especially valuable during recent global disruptions when on-site inspections faced significant limitations.
By embracing these advanced digital tools, food processors don't just meet current compliance standards—they position themselves to adapt seamlessly to evolving regulatory requirements while optimising operational efficiency. Ready to transform your food safety management approach? Discover how Q-Hub's tailored digital solutions can help you build a more responsive, efficient compliance ecosystem.
Start using Q-Hub today
- Manage compliance in one place
- Streamline your teams and tasks
- Use Q-Hub free for 30 days