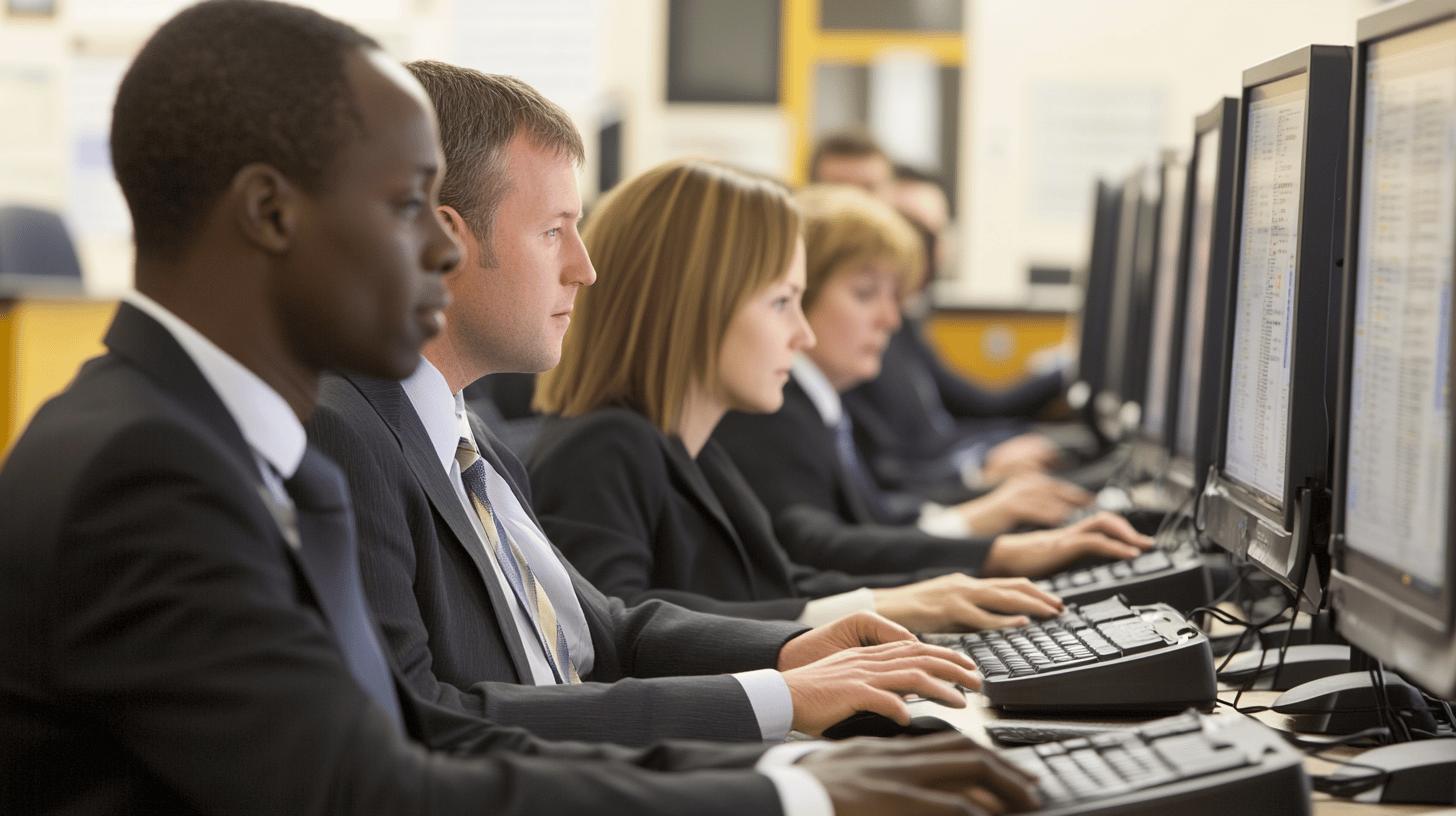
Data Management Solutions Boost Traceability Compliance
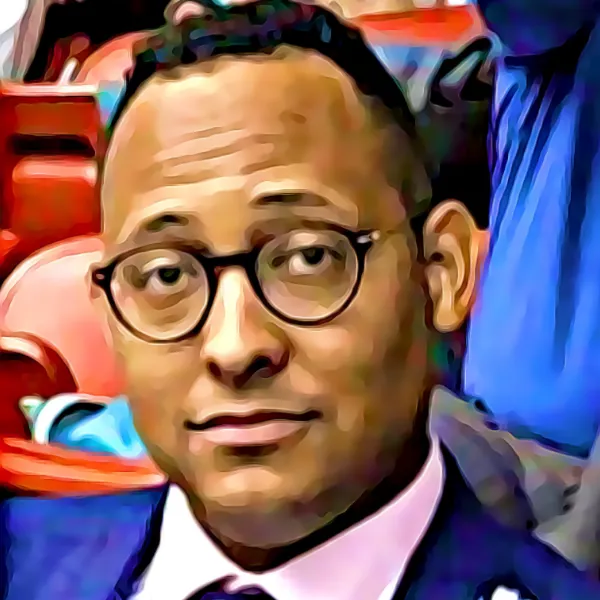
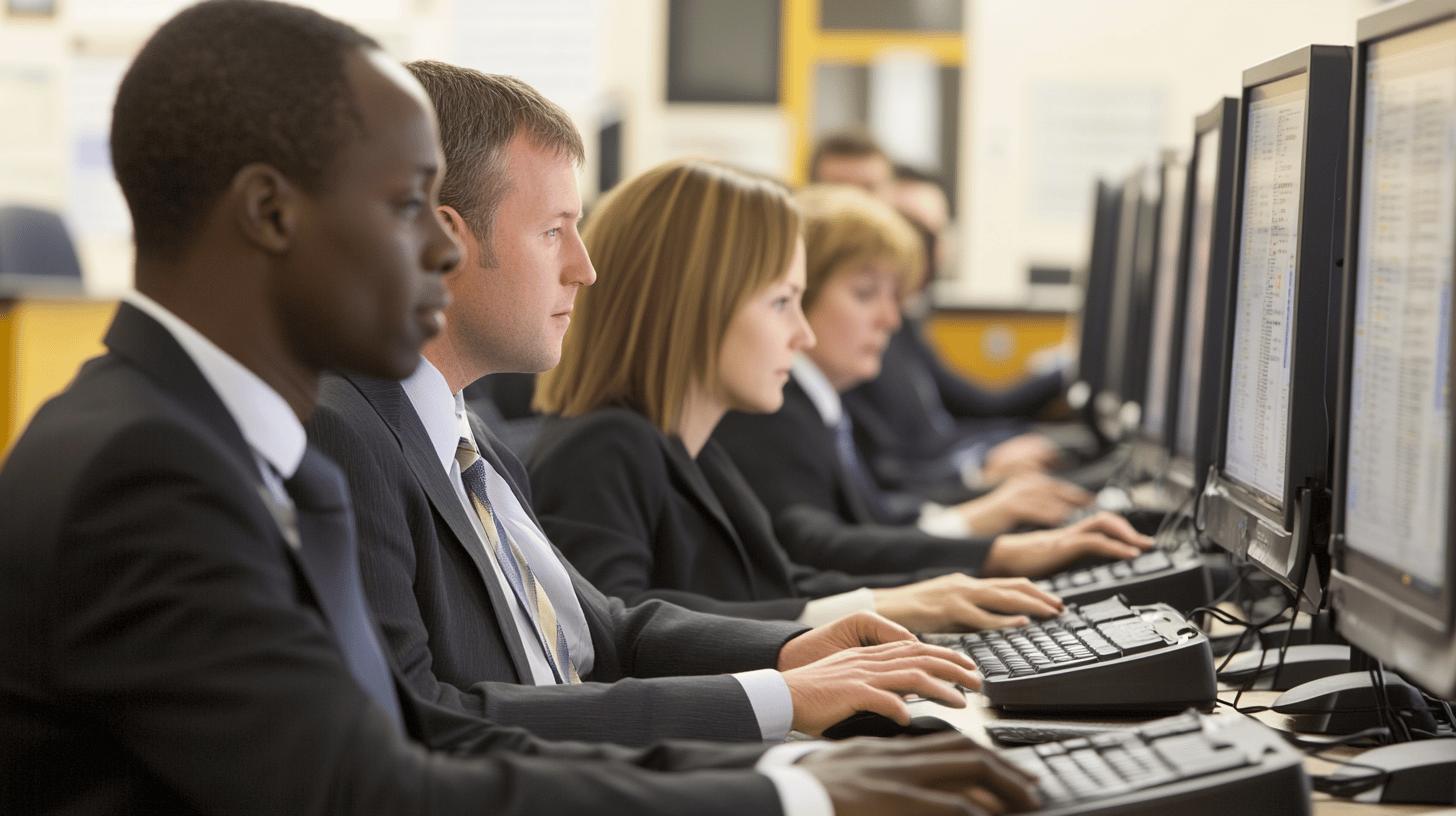
Data Management Solutions Boost Traceability Compliance
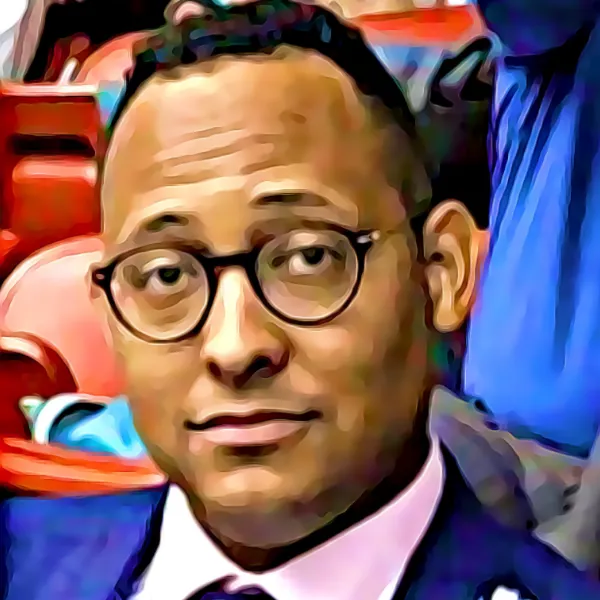
The Role of Data Management Solutions in Ensuring Traceability Compliance for Food Processors
Data management solutions for food processors have evolved from optional tools to critical necessities. In today's complex regulatory environment, these digital compliance platforms address the growing maze of requirements including FSMA, HACCP, and ISO standards. Q-Hub's specialised solutions centralise traceability efforts, providing real-time tracking and automated reporting where manual systems leave dangerous gaps. Without robust systems, food processors face significant risks of errors, inefficiencies, and potential non-compliance penalties.
Regulatory precision is non-negotiable in the food industry. When trying to trace a contaminated ingredient through a complex supply chain, manual methods aren't just inefficient—they're potentially dangerous. Digital solutions automate data collection across the entire production cycle, creating seamless documentation that reduces errors while streamlining workflows.
When implementing digital traceability systems, we saw audit preparation time decrease by 75% while simultaneously improving our response capability during mock recalls by nearly 90%.
- Automated compliance reporting dramatically reduces human error
- Real-time tracking provides immediate visibility into your supply chain
- Digital audit trails simplify regulatory inspections, saving valuable time
- Enhanced transparency significantly reduces recall risks and contamination
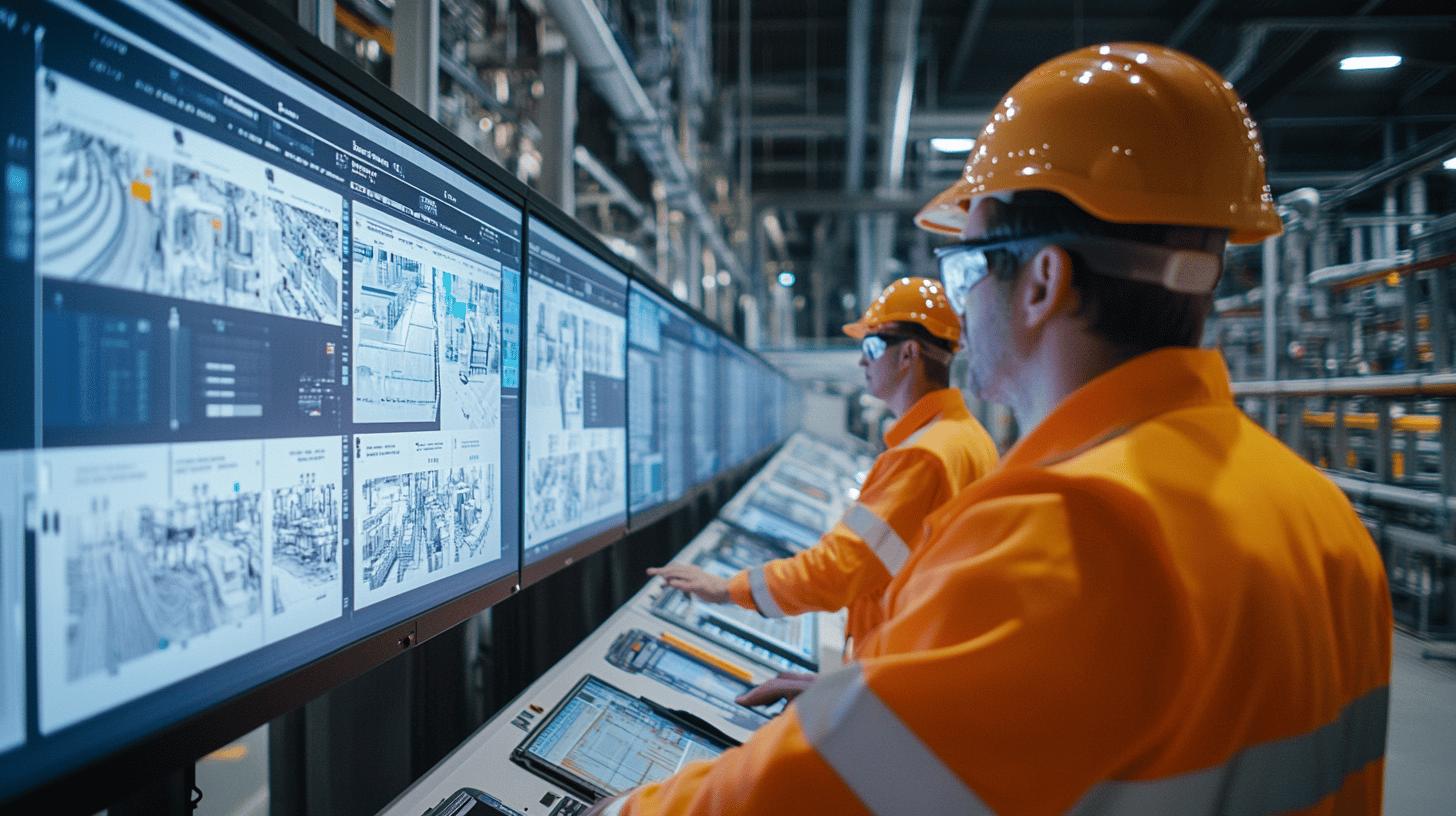
Beyond Spreadsheets: The Evolution of Food Traceability Technology
Modern food traceability software has rendered traditional paper methods obsolete. These comprehensive systems create structured frameworks for tracking data across increasingly complex global supply chains. For companies still relying on fragmented methods, the gap between their capabilities and industry standards grows wider daily. As Scottish Leather Group discovered when implementing Q-Hub's solutions, centralised systems transform operational visibility while ensuring compliance.
Batch tracking represents the foundation of effective traceability. It provides food processors with complete product journey visibility—from raw materials through final packaging. During recalls, this precision can save millions by isolating specific affected batches rather than conducting widespread recalls. This level of granular control remains impossible with legacy systems like paper logs or basic spreadsheets.
Real-Time Insights: Transforming Food Safety Management
Imagine watching your ingredients and finished products move through the supply chain with complete visibility. Real-time data makes this possible, giving food processors instant access to critical information. This capability allows teams to address issues immediately rather than discovering problems days later, eliminating costly blind spots and ensuring all stakeholders remain aligned.
Integration with existing ERP systems further amplifies these benefits. When traceability software connects seamlessly with other business systems, data flows naturally between departments. This integration reduces duplicate work, improves accuracy, and creates streamlined operations that significantly enhance productivity.
<table border="0"> <tr><th>Metric</th><th>Before Digital Traceability</th><th>After Q-Hub Implementation</th></tr> <tr><td>Audit Preparation Time</td><td>3-5 Days</td><td>4-6 Hours</td></tr> <tr><td>Recall Response Time</td><td>24+ Hours</td><td>Under 2 Hours</td></tr> <tr><td>Documentation Errors</td><td>15-20%</td><td>Under 2%</td></tr> <tr><td>Staff Time on Manual Tasks</td><td>30+ Hours Weekly</td><td>8 Hours Weekly</td></tr> </table>How Food Processors Can Leverage Data Management Solutions for End-to-End Traceability
End-to-end traceability represents the gold standard in food safety management. These systems track products throughout their entire lifecycle—from ingredient sourcing to final delivery. Without comprehensive digital platforms like those offered by Q-Hub, food processors risk compliance failures, inefficiencies, and damaged stakeholder relationships. Companies transitioning from paper-based systems, like Anglia Cathodic Protection, report dramatic improvements in operational visibility and compliance management.
Breaking Down Supply Chain Barriers with Integrated Data
Traceability effectiveness depends on eliminating weak links in your data chain. When food processors can't seamlessly track ingredients from farm to table, the entire system becomes vulnerable. Modern solutions bridge these gaps by consolidating information across stakeholders—allowing processors to verify material sources, monitor production metrics, and verify distribution records within a unified platform.
This integration enables swift responses during contamination events. Rather than spending days investigating an issue, companies using Q-Hub's solutions can identify affected products, their distribution paths, and potentially impacted customers within hours. For food processors, this responsiveness can mean the difference between a minor incident and a brand-damaging recall.
- Improved regulatory compliance through consistent, accessible documentation
- Dramatic reduction in recall scope and financial impact
- Enhanced customer trust through demonstrable supply chain transparency
- Streamlined operations across production processes
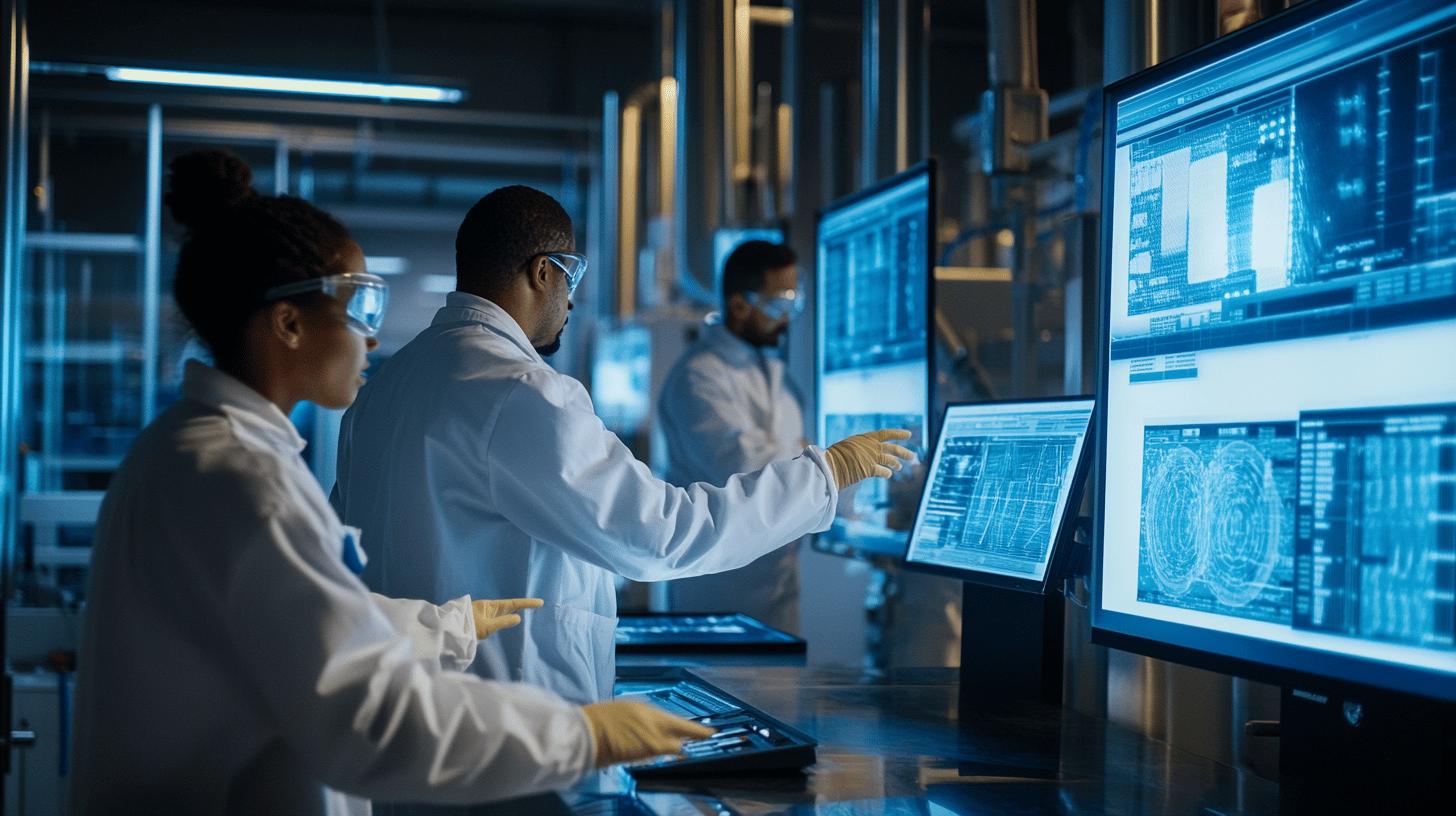
Overcoming Compliance Challenges in Food Processing with Data-Driven Practices
Food processors navigate an increasingly complex regulatory landscape while maintaining precise traceability. Traditional manual record-keeping simply can't address modern challenges in auditing, data accuracy, and supply chain transparency. As demonstrated by Rocal Insulating Panels after implementing Q-Hub solutions, digital systems transform compliance practices through real-time monitoring and advanced technologies that streamline workflows while maintaining consistent adherence to regulations like EC 178/2002 and HACCP.
From Reactive to Proactive: Preventing Problems Before They Occur
Modern compliance software does more than simplify audits—it fundamentally shifts operations from reactive to proactive. Automated systems flag temperature deviations or contamination risks in real time, allowing immediate corrective action. This capability transforms how teams operate, freeing them from manual data collection to focus on strategic decisions that improve food safety outcomes.
Predictive analytics represents the next evolution in risk management for food processors. By analysing historical patterns and current data, these tools forecast potential compliance issues before they manifest. For example, the system might identify supplier patterns that correlate with quality problems, enabling processors to address root causes before products are compromised. This proactive approach significantly enhances operational efficiency while reducing compliance risks.
Key Benefits of Predictive Analytics in Food Safety
Predictive analytics transforms food safety management by identifying patterns that humans might miss. By analysing thousands of data points across production cycles, these systems can:
- Flag anomalies in temperature, humidity, or other critical parameters before they cause contamination
- Identify correlations between specific suppliers and quality issues
- Predict maintenance needs before equipment failures impact product safety
- Optimise inspection schedules based on risk assessments
Companies implementing these solutions report 40-60% improvements in early detection rates for potential safety issues.
The Cost-Benefit Analysis of Investing in Traceability Solutions
Digital traceability systems require initial investment, but their long-term advantages typically outweigh these costs. While purchasing software, training staff, and integrating systems represents significant expenditure for smaller operations, these costs pale compared to potential savings. Studies show automating traceability processes can reduce labour costs by up to 30%—a substantial shift that allows teams to focus on strategy rather than repetitive documentation tasks.
Intangible benefits further strengthen the business case. Improved supply chain transparency builds trust with both regulators and customers. When food processors demonstrate clear, accurate data management, it reassures stakeholders and enhances brand reputation. Consider the alternative: a recall without robust traceability could mean extensive financial penalties, lost business, and irreparable reputation damage. For forward-thinking processors, Q-Hub's solutions represent not just compliance tools but strategic business assets.
Measuring Success: The Metrics That Matter
The ROI for traceability solutions becomes clear through several key metrics. First, recall scope reduction—digital systems can precisely identify affected products rather than requiring broad-based recalls that waste unaffected inventory. Second, audit preparation time decreases dramatically, with many Q-Hub clients reporting 75-90% reductions. Finally, improved data accuracy reduces compliance risks, potentially saving substantial regulatory penalties.
For food processors weighing investment decisions, conducting a thorough cost-benefit analysis reveals digital traceability isn't merely an expense—it's a strategic advantage that enhances operational excellence while protecting the business from significant risks. By implementing Q-Hub's customised solutions, companies continuously report improved supply chain visibility and strengthened compliance capabilities that ultimately drive business growth.
Preparing for Regulatory Audits with Digital Traceability Tools
Regulatory audits often create stress and disruption when relying on manual systems. Digital platforms transform this experience by automating data collection and centralising documentation. Rather than frantically gathering scattered records, food processors using Q-Hub's solutions generate accurate, real-time compliance reports instantly. This capability not only saves time but drastically reduces human error, which remains the leading cause of compliance failures.
Building Confidence Through Digital Audit Trails
The digital audit trail represents a cornerstone feature of modern traceability systems. By creating chronological records of all actions and data changes, these tools ensure complete transparency throughout production. Fowlers of Bristol experienced this transformation firsthand when implementing Q-Hub's document management tools, which revolutionised their ability to maintain accurate records and demonstrate compliance.
Centralised document storage transforms audit experiences. Every critical record—from batch information to supplier certifications—becomes accessible with a simple search. These systems enforce consistent reporting formats, eliminating discrepancies that commonly trigger deeper investigation during audits. Food processors using digital tools can instantly demonstrate compliance, building confidence among auditors and internal stakeholders alike.
- Automated data retrieval enables instant responses to audit queries
- Standardised reporting formats significantly reduce documentation errors
- Detailed digital audit trails provide complete process visibility
- Centralised document management eliminates information silos
As regulatory requirements continue evolving, food processors must embrace digital transformation to maintain compliance while improving operational efficiency. Q-Hub's specialised solutions offer comprehensive tools designed specifically for food industry challenges, enabling companies to transform traceability from a compliance burden into a strategic advantage. Ready to elevate your traceability capabilities? Discover how Q-Hub's customised solutions can streamline compliance while enhancing operational excellence across your food processing operations.
<Start using Q-Hub today
- Manage compliance in one place
- Streamline your teams and tasks
- Use Q-Hub free for 30 days