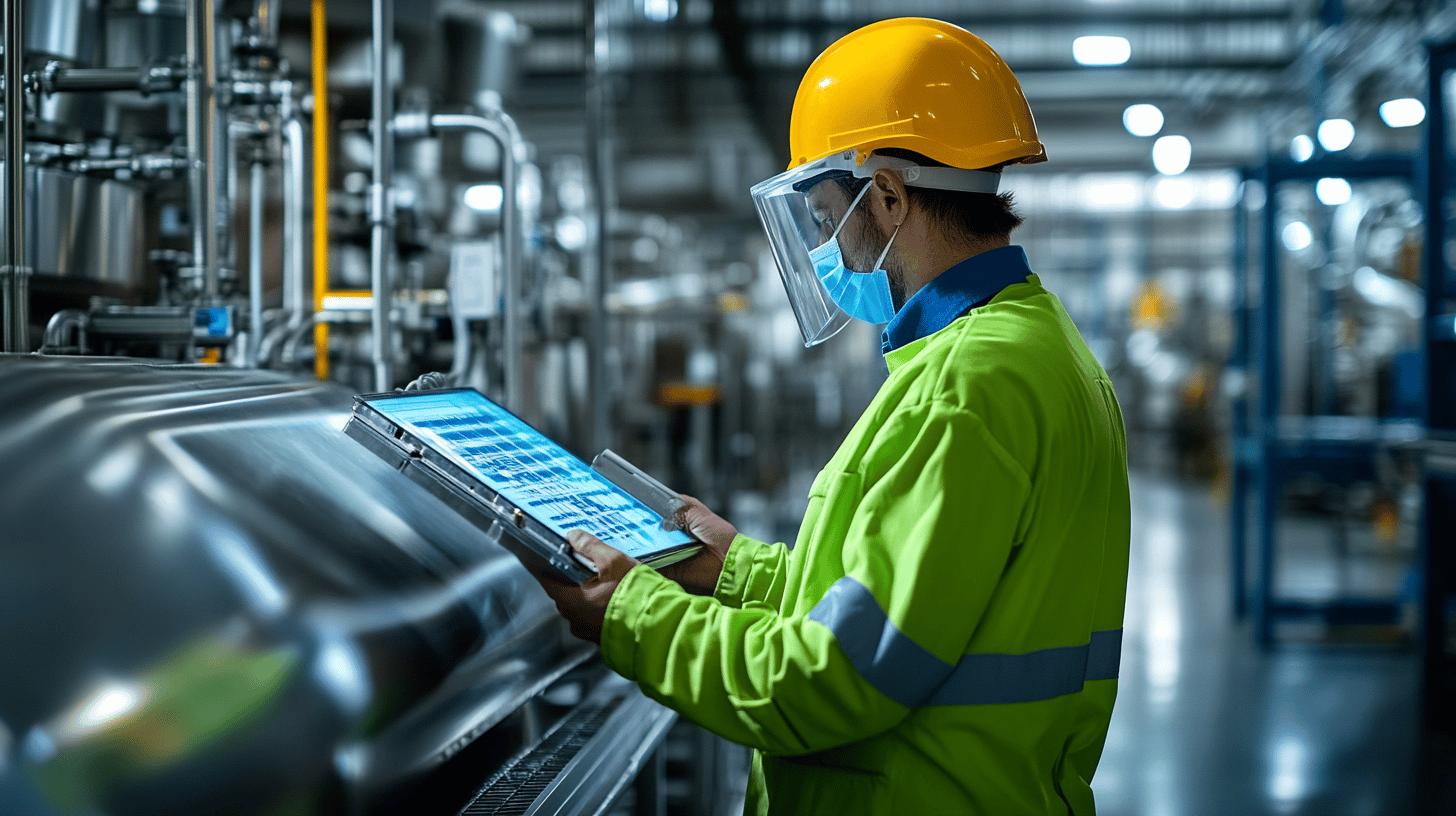
Custom Automation Tools Boost Compliance in Food Manufacturing
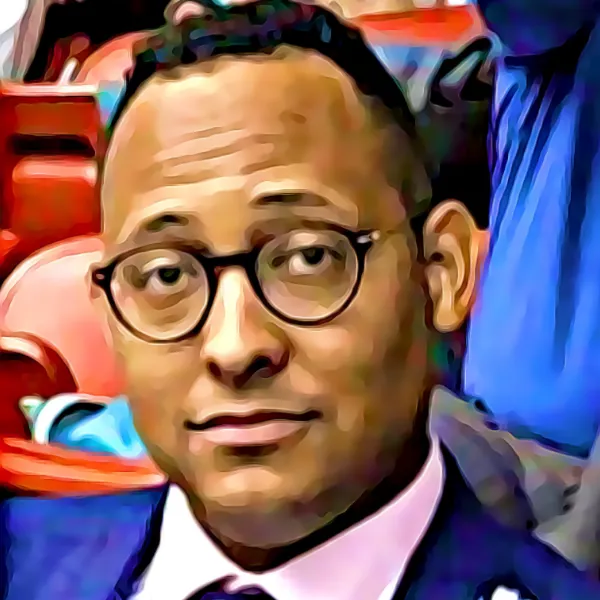
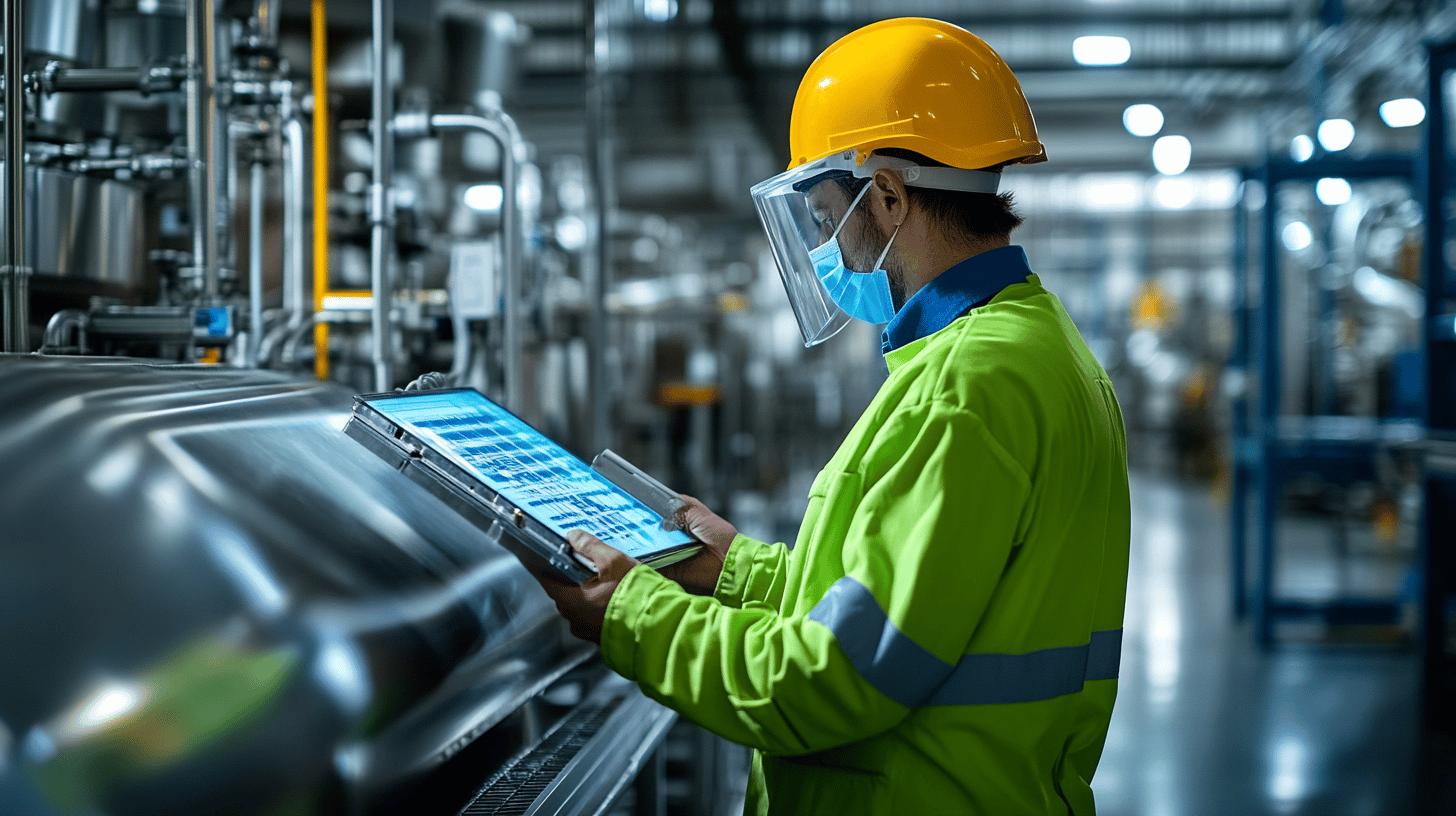
Custom Automation Tools Boost Compliance in Food Manufacturing
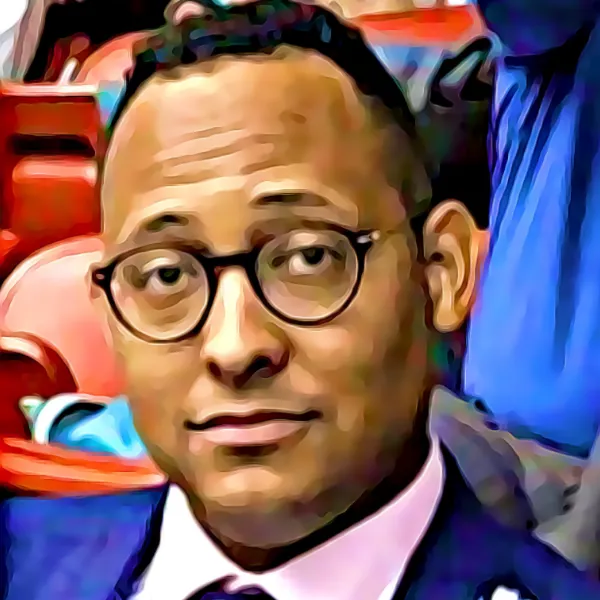
The Role of Custom Automation Tools in Compliance Management for Food Manufacturing
Custom automation tools have revolutionised compliance management in food manufacturing, transforming complex regulatory adherence into streamlined, efficient processes. These intelligent systems continuously monitor operations, automating critical checks while significantly reducing human error in food safety procedures. For food producers navigating the increasingly complex web of regulations, from allergen controls to HACCP protocols, automation has become essential rather than optional.
Q-Hub's tailored compliance solutions address the specific challenges of food manufacturing by integrating seamlessly with existing production systems. These platforms don't just digitise paperwork—they fundamentally transform how companies approach regulatory requirements by providing real-time visibility and proactive risk management.
Beyond Manual Monitoring: How Automation Creates 24/7 Compliance Vigilance
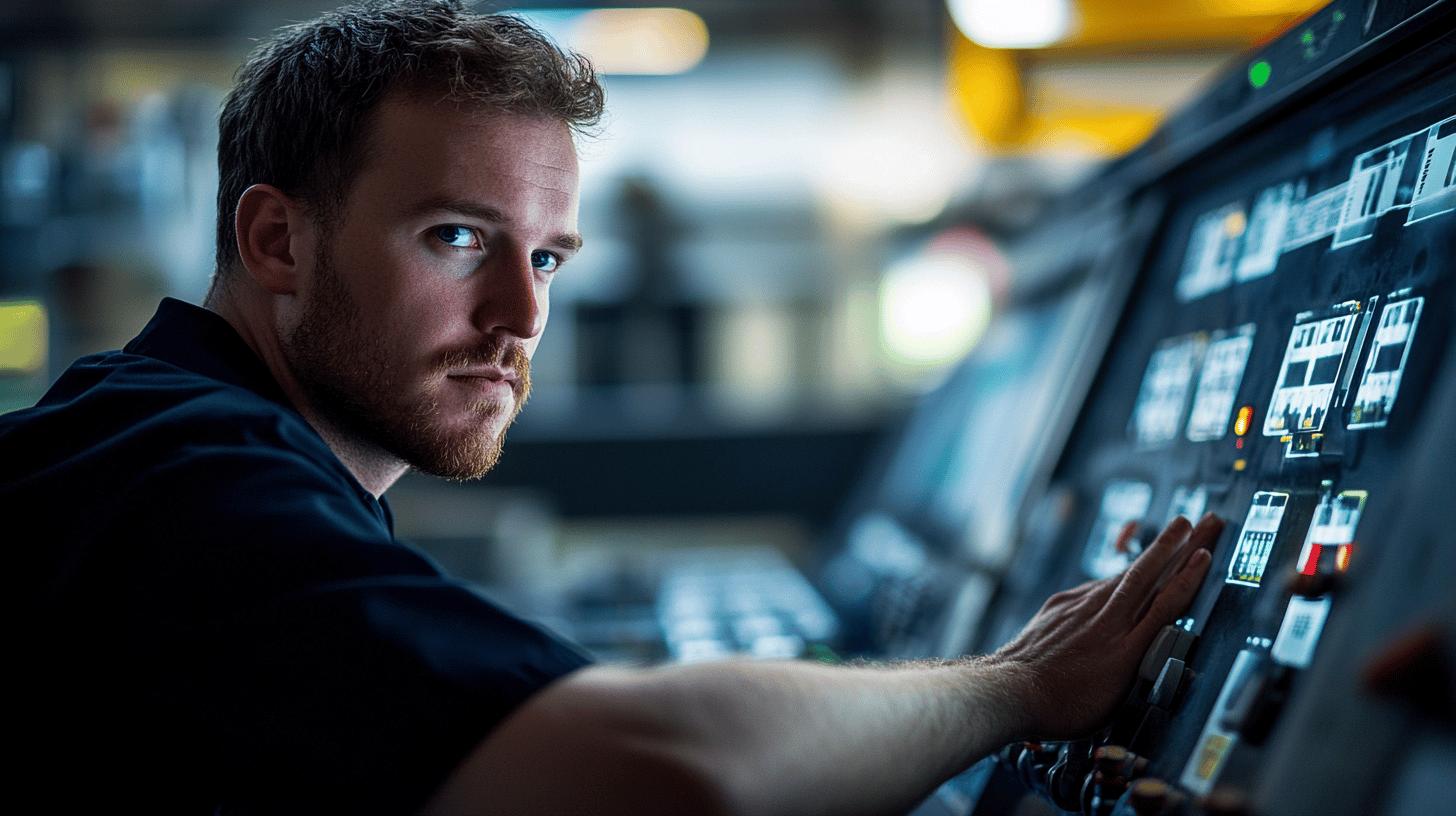
Real-time monitoring serves as a relentless compliance watchdog, continuously tracking operations against evolving food safety standards. When a cold storage unit exceeds temperature thresholds, the system immediately alerts responsible personnel, preventing violations before they escalate into costly incidents.
Automated reporting represents another significant advancement. Instead of manually compiling data for audits—a process notoriously prone to errors—these systems generate accurate, audit-ready reports with minimal effort. This not only saves valuable time but dramatically enhances reporting accuracy.
The transformation we've witnessed at Anglia Cathodic Protection after implementing digital compliance tools was remarkable. What once took days of preparation now happens at the touch of a button, freeing our quality team to focus on improvement rather than paperwork.
Perhaps most impressive is predictive risk management capability. Advanced systems analyse historical data to identify potential compliance risks before they materialise. This level of foresight significantly reduces operational disruptions and minimises the likelihood of regulatory penalties.
Measuring Real Impact: The Financial Case for Compliance Automation
The financial benefits of implementing custom automation in food manufacturing compliance are substantial and measurable. Most businesses see a return on investment within 12-24 months, primarily through reduced labour costs and eliminated compliance penalties.
Let's examine how automation transforms key compliance metrics:
<table border="0"> <tr><th>Compliance Metric</th><th>Before Automation</th><th>After Automation</th></tr> <tr><td>Audit Preparation Time</td><td>3-5 days</td><td>2-4 hours</td></tr> <tr><td>Documentation Errors</td><td>8-12% of records</td><td><1% of records</td></tr> <tr><td>Time to Identify Non-Compliance</td><td>Hours/Days</td><td>Minutes/Real-time</td></tr> <tr><td>Staff Time on Compliance Tasks</td><td>25-30% of workday</td><td>8-12% of workday</td></tr> </table>These efficiency gains allow food manufacturers to redirect resources toward innovation and quality improvement rather than administrative compliance tasks. The Scottish Leather Group achieved remarkable results after implementing Q-Hub's solutions, with audit preparation time reduced from days to mere hours while significantly improving compliance accuracy.
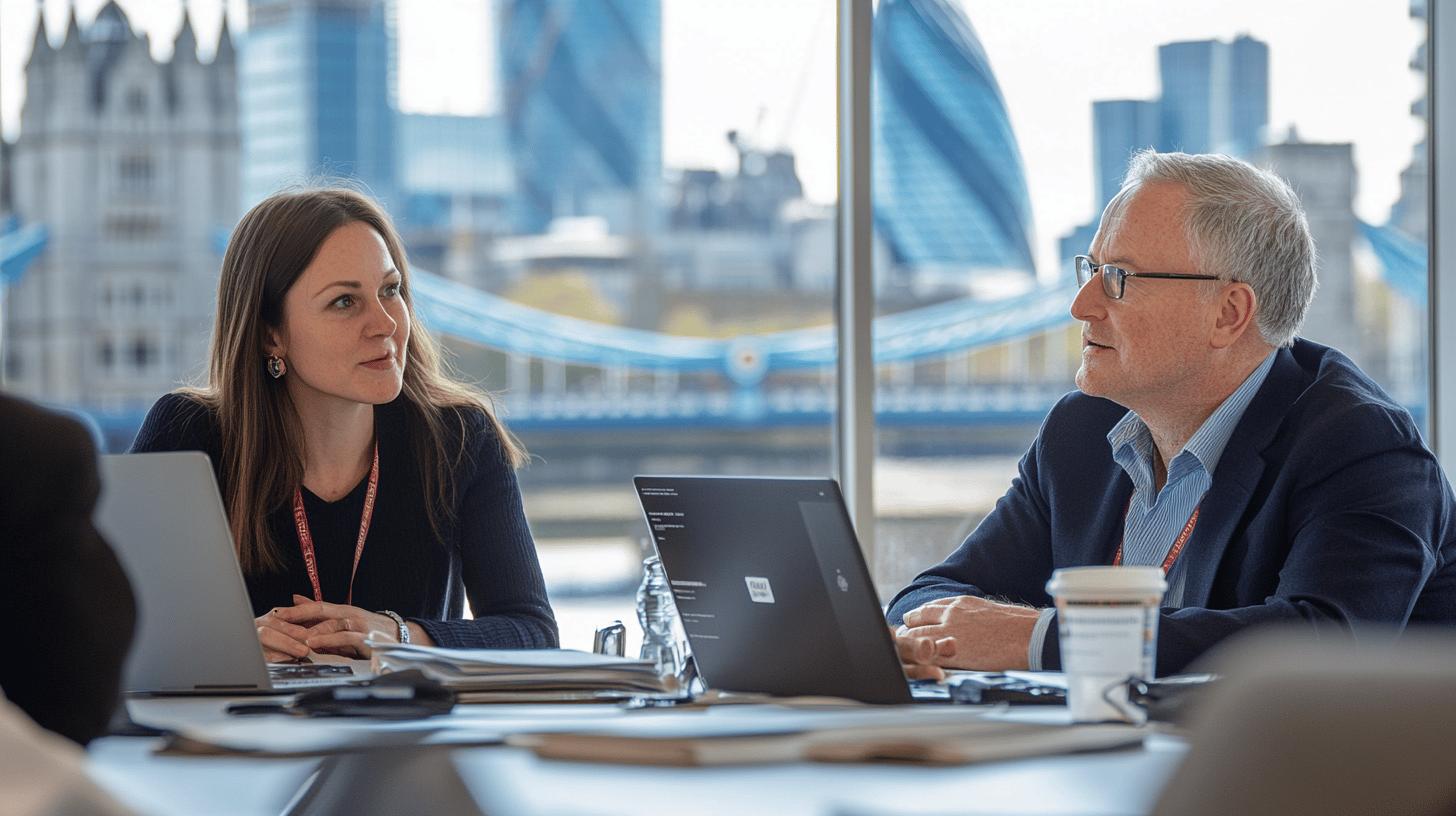
Strategic Implementation: Building a Roadmap for Compliance Transformation
Implementing automation in food manufacturing compliance requires thoughtful planning and execution. Begin with a thorough assessment of current workflows to identify specific pain points—are manual allergen checks slowing production? Is documentation fragmented across systems? Understanding these challenges helps prioritise automation efforts.
When selecting compliance automation tools, compatibility with existing systems is paramount. Q-Hub's solutions are designed to integrate seamlessly with common ERP platforms, preventing the creation of technological silos while ensuring data flows smoothly throughout the organisation.
Overcoming Implementation Challenges
Staff resistance often presents the biggest hurdle when introducing new compliance systems. Overcome this by highlighting tangible benefits—reduced administrative burden, fewer errors, and protection from costly penalties. Incremental implementation also eases the transition, allowing teams to adapt gradually to new processes while maintaining productivity.
Comprehensive training is essential, ensuring all users understand both technical operation and the broader compliance objectives. Establish clear feedback channels so team members can highlight issues during implementation, creating a cycle of continuous improvement.
Future Horizons: AI and IoT Reshaping Compliance Technology
The next generation of compliance automation in food manufacturing will be driven by artificial intelligence and IoT integration. These technologies move beyond simple process automation to provide predictive capabilities and real-time operational intelligence.
AI systems analyse vast quantities of production and compliance data to identify potential risks before they manifest. For instance, patterns in supplier deliveries or subtle equipment performance shifts might indicate emerging compliance issues long before they would typically be detected.
IoT sensors embedded throughout production environments provide continuous monitoring of critical parameters like temperature, humidity, and contamination levels. These systems don't just detect problems—they trigger automated remediation processes, often resolving issues before human intervention becomes necessary.
Sustainability compliance is another emerging frontier. As regulatory requirements around waste, energy usage, and carbon footprint intensify, automated systems are increasingly tracking environmental metrics alongside traditional food safety parameters.
Real-World Success: Transforming Paper-Based Headaches into Digital Efficiency
The transformation from manual to automated compliance management delivers remarkable results across various food manufacturing operations. When BMC Analysis implemented Q-Hub's digital solutions, their NCR management shifted from fragmented, delay-prone processes to streamlined workflows with automated tracking.
Similarly, Rocal Insulating Panels revolutionised their safety reporting system, eliminating paper-based processes that frequently resulted in incomplete records and delayed investigations. Their automated system now enables immediate incident documentation and rapid resolution, significantly improving overall compliance rates.
These real-world examples demonstrate the transformative impact of well-implemented compliance automation. The value extends beyond mere efficiency gains—companies report stronger quality cultures, better employee engagement, and more effective use of specialist expertise when routine compliance tasks are automated.
Q-Hub specialises in developing custom automation tools that transform compliance management in food manufacturing, helping businesses not only meet regulatory requirements but gain competitive advantage through operational excellence. By implementing tailored digital solutions, companies can achieve the dual benefits of rigorous compliance and streamlined operations—positioning themselves for sustainable growth in a highly regulated industry.
Ready to transform your food manufacturing compliance approach with Q-Hub? Discover how customised automation solutions can enhance regulatory adherence while driving operational efficiency across your organisation.
Start using Q-Hub today
- Manage compliance in one place
- Streamline your teams and tasks
- Use Q-Hub free for 30 days