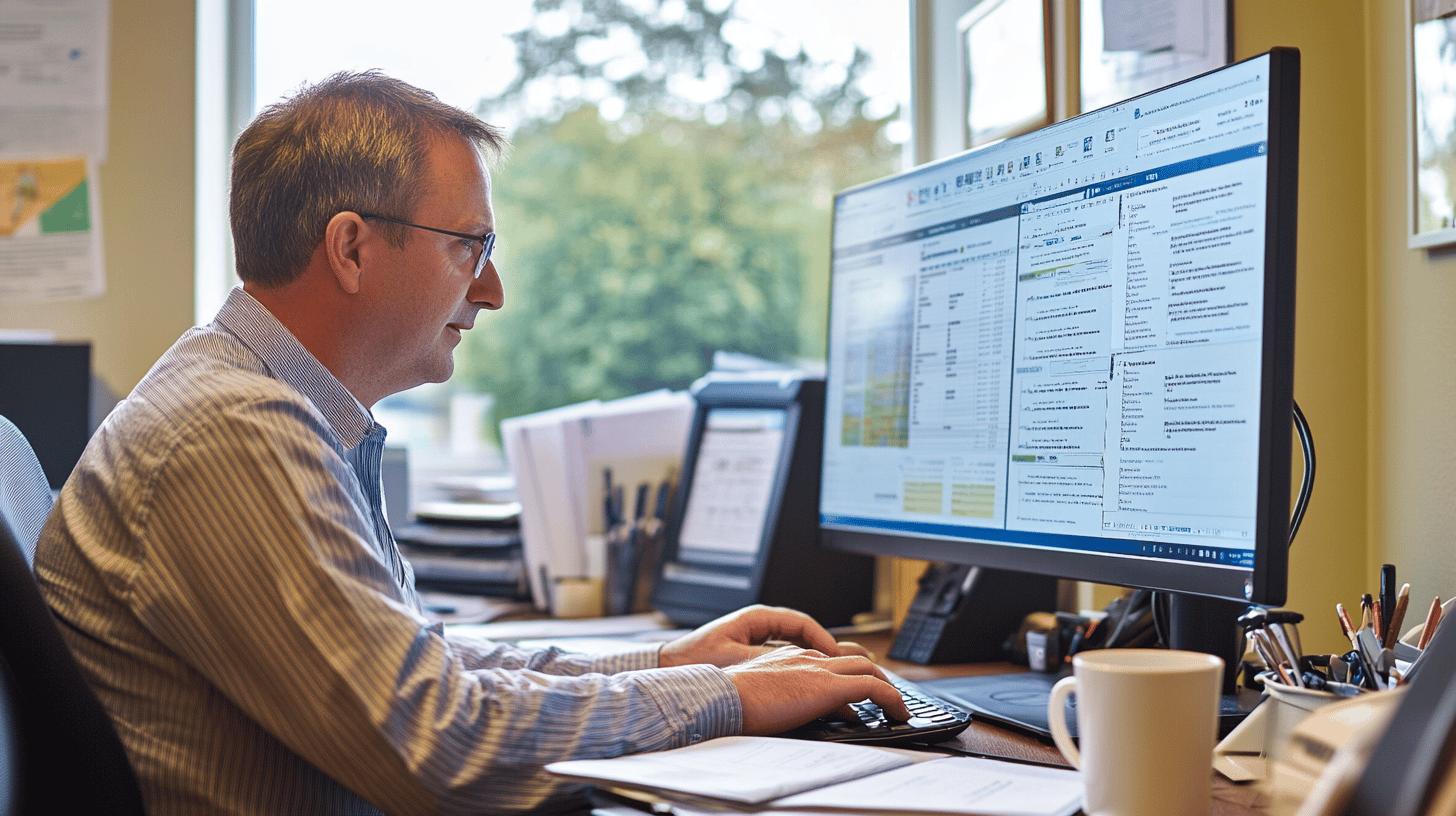
Web Portal Creation Boosts Audit Efficiency in Food Production
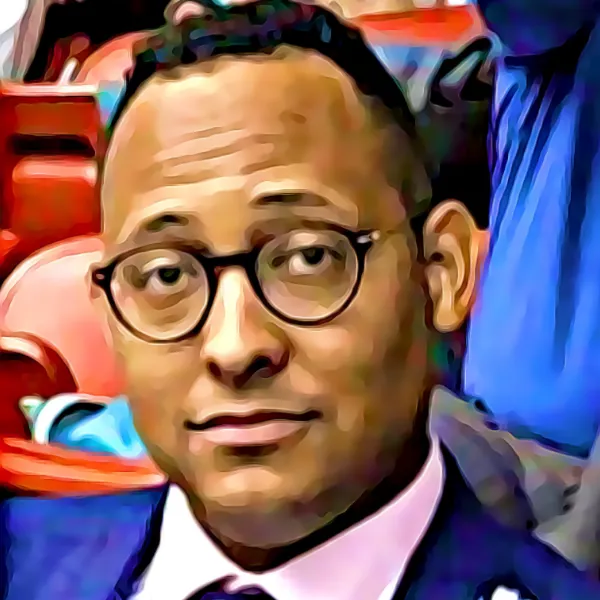
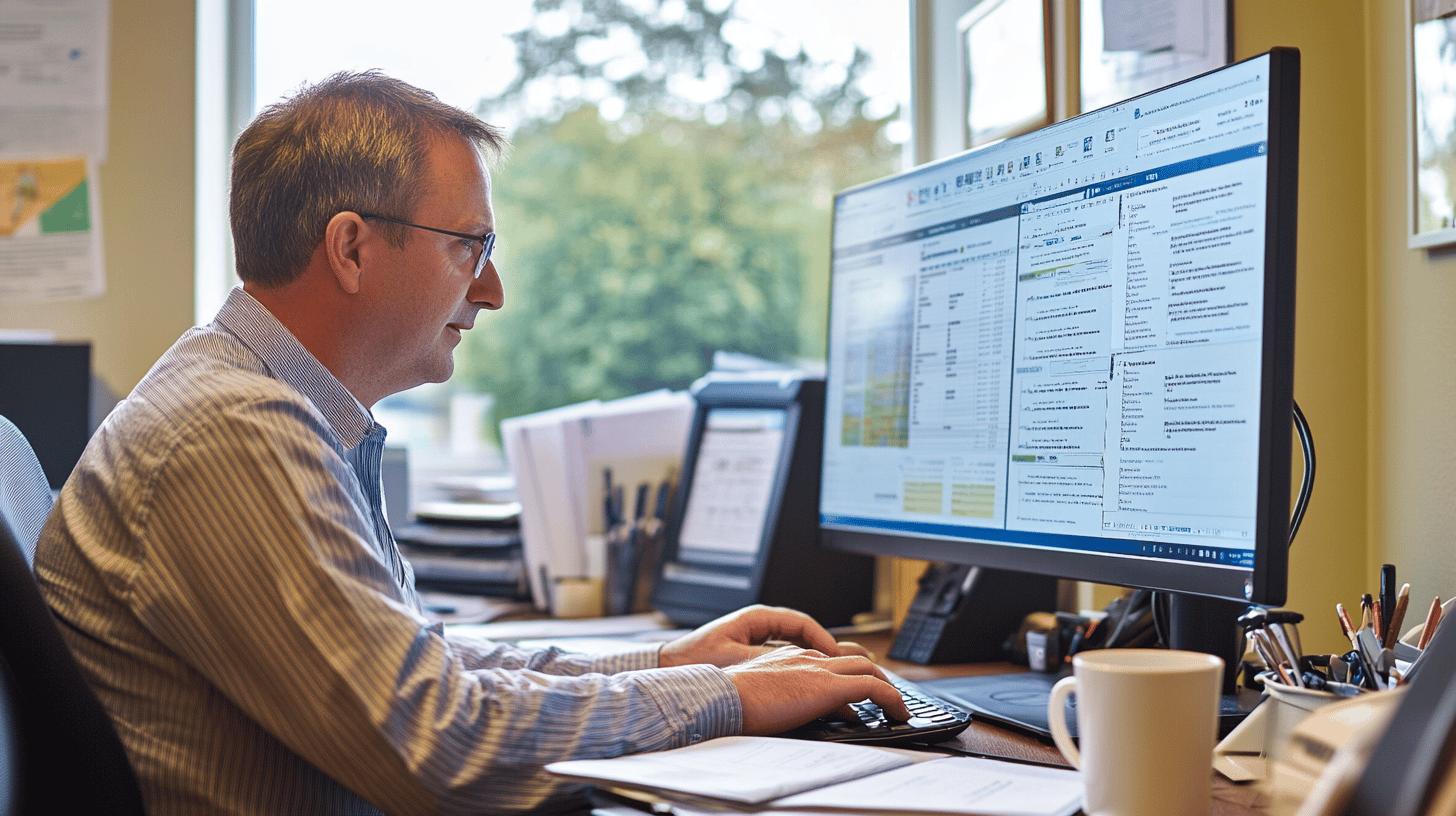
Web Portal Creation Boosts Audit Efficiency in Food Production
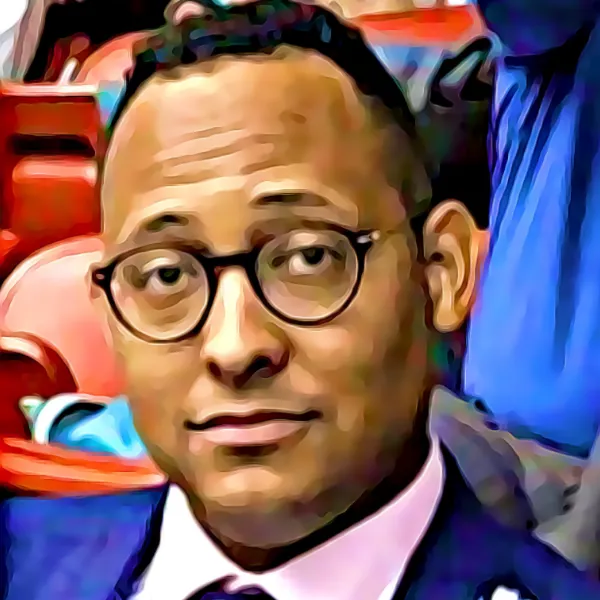
How Web Portal Creation Streamlines Audits and Inspections for Food Production Teams
Food production teams face mounting challenges when managing compliance alongside complex audits and inspections. Manual systems often lead to inefficiencies, missed deadlines, and communication gaps – issues that web portal creation directly addresses. Q-Hub's digital solutions transform outdated methods into streamlined processes with enhanced operational clarity. By centralising workflows, these specialised platforms provide food production teams with tools that simplify, standardise, and optimise their compliance efforts.
Regulatory compliance demands in the food sector are particularly rigorous. With strict standards like the Food Safety and Hygiene (England) Regulations 2013 and over 170,000 food hygiene checks conducted annually in England alone, manual processes simply can't keep pace. Common issues like temperature control problems and inadequate cleaning practices require robust monitoring systems to prevent compliance failures.
Digital portals tackle these challenges by integrating audit schedules, task management, and real-time reporting into one cohesive system. This allows teams to focus on ensuring safety and quality rather than wrestling with spreadsheets and disjointed tools.
Transforming Inspection Workflows with Real-Time Intelligence
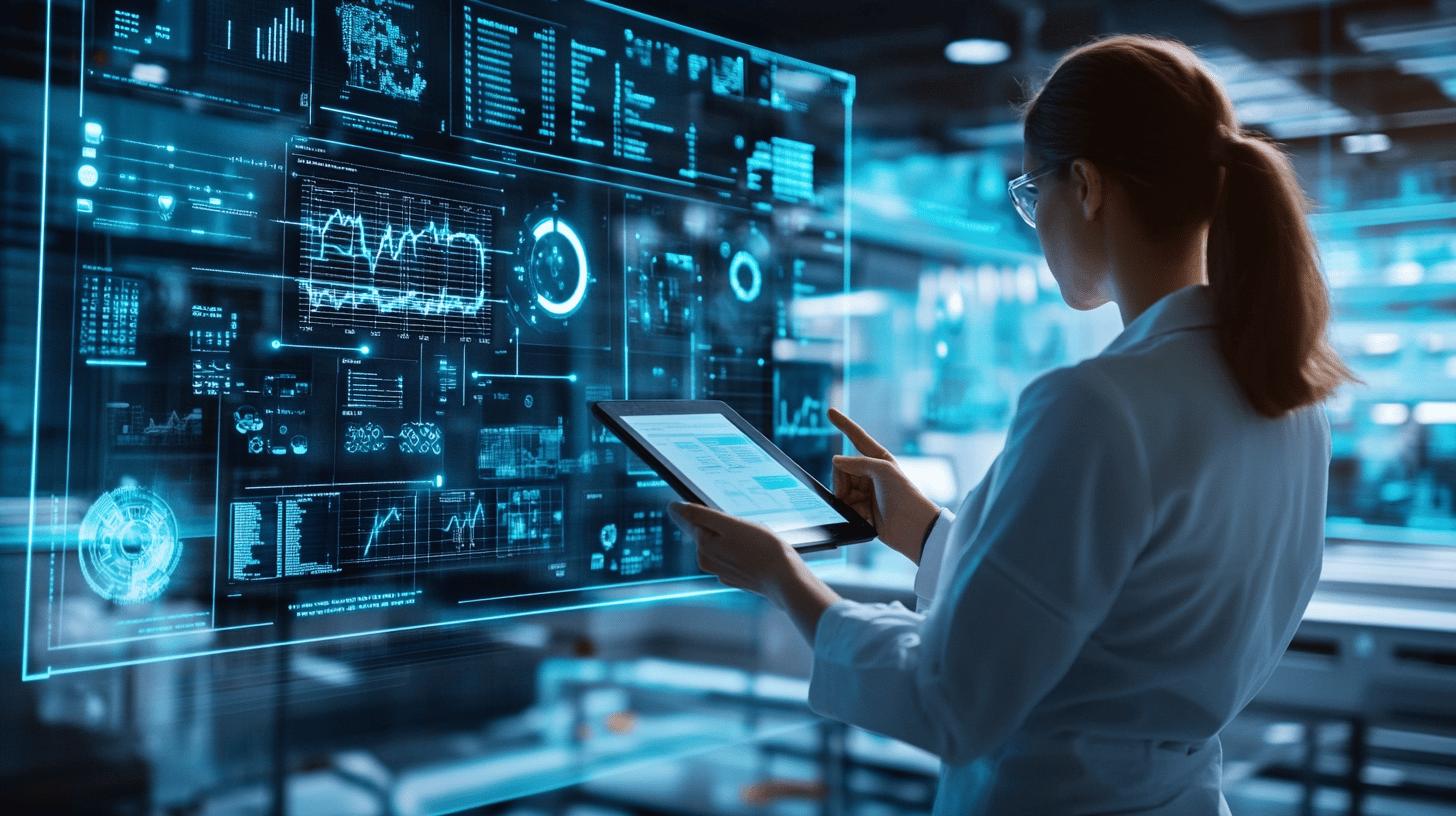
The power of real-time data access cannot be overstated in food production environments. When inspectors can upload temperature readings, photographic evidence, or checklist results directly from the production floor, the lag between discovery and action disappears. These updates sync instantly across the system, giving supervisors immediate visibility into operations and significantly improving response times.
Think about what happens in traditional settings – an inspector spots a temperature issue, records it on paper, and perhaps hours later that information reaches the right person. With web portals, that delay vanishes entirely.
Before implementing Q-Hub's digital solution, we spent hours transferring inspection data between systems. Now our teams capture findings instantly, and everyone who needs that information has it immediately. Issues get resolved before they become problems." Source: Scottish Leather Group case study.
Customisable dashboards further enhance this efficiency by allowing each team member to focus on metrics that matter to their role. Quality managers might prioritise overdue inspections, while compliance officers monitor overall standards adherence. This personalisation ensures the right data reaches the right people at the right time.
Automated notifications form the final piece of this transformation, eliminating the risk of missed inspections or forgotten corrective actions. These proactive alerts keep everyone accountable and informed, regardless of their location.
Building Unbreakable Compliance Frameworks
In food production, regulatory compliance isn't optional – it's essential for business survival and public safety. Digital solutions create robust compliance frameworks that minimise risk and maximise confidence during official inspections.
These comprehensive platforms deliver several critical capabilities:
- Automatic regulatory updates that keep teams informed of changing legislation
- Digital audit trails providing tamper-proof records for full traceability
- Real-time compliance monitoring that flags issues as they emerge
- Automated report generation saving hours of preparation time
- Integration with regulatory databases for seamless validation
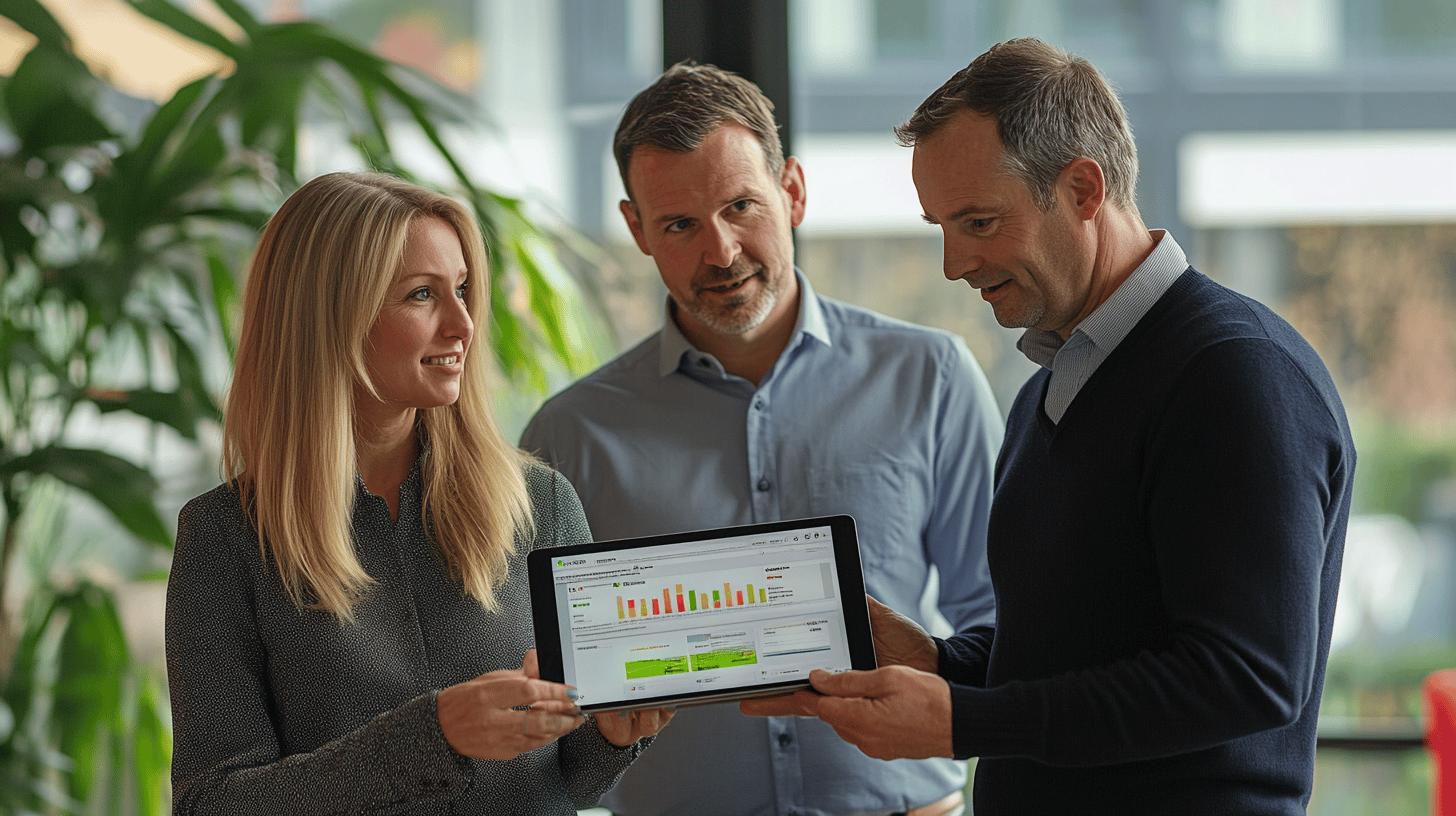
These features transform compliance from a reactive scramble into a proactive, systematic approach. Teams can demonstrate due diligence instantly during inspections, substantially reducing stress and uncertainty.
Breaking Down Communication Barriers
Traditional audit and inspection processes often suffer from communication breakdowns. A temperature issue flagged during one shift might not reach the operations team until problems have escalated. Web portals eliminate these silos by establishing a single source of truth for all compliance data.
Shared dashboards ensure everyone has access to the same information simultaneously. Task assignment tools allow managers to delegate responsibilities clearly, while peer review functions add an extra layer of quality control.
This enhanced collaboration creates a more cohesive team environment where challenges are tackled collectively rather than in isolation. The impact on productivity is substantial:
<table border="0"> <tr><th>Process</th><th>Before Digital Portal</th><th>After Implementation</th></tr> <tr><td>Audit preparation time</td><td>2-3 days</td><td>3-4 hours</td></tr> <tr><td>Issue resolution time</td><td>5+ days</td><td>Same day</td></tr> <tr><td>Report generation</td><td>Manual compilation</td><td>Automated</td></tr> <tr><td>Cross-department visibility</td><td>Limited</td><td>Complete</td></tr> </table>Real-World Success Stories: Measuring Transformation
The true value of web portal creation for food production teams becomes clear when examining real-world implementations. Consider how digital transformation revolutionised operations for these organisations:
Anglia Cathodic Protection experienced rapid growth that stretched their paper-based systems beyond capacity. After implementing Q-Hub's platform, they digitised their fragmented compliance processes, making information accessible and actionable for all employees. The system streamlined non-conformance tracking and audits while fostering engagement across teams – from shop floor to remote workers.
Similarly, Scottish Leather Group faced significant challenges managing compliance across multiple sites and departments. Their implementation of Q-Hub's Audit Hub, Asset Hub, and Doc Hub created a unified approach to compliance management. The company now seamlessly handles multiple ISO standards within a single platform, with substantially reduced audit preparation time and improved cross-departmental communication.
These case studies demonstrate consistent outcomes: reduced audit cycle times (typically 30%), improved compliance rates, and significant resource efficiency gains – all while maintaining or enhancing quality standards.
The Future of Food Production Compliance
The evolution of web portals for food production inspections continues at pace, with several technologies poised to deliver even greater benefits:
Predictive analytics represents perhaps the most exciting frontier. By analysing historical data, these systems can identify potential compliance risks before they materialise. For instance, if temperature control issues frequently occur in specific production areas, predictive tools can alert teams to investigate before formal inspections uncover problems.
Similarly, AI-powered inspection tools are transforming data collection and analysis. These systems can process inputs from IoT sensors in real-time, automatically flagging irregularities and suggesting corrective actions. The result is a shift from reactive to proactive compliance management.
Equally important is the growing emphasis on scalability and flexibility. Modern portals can adapt to operations of any size, from small facilities to multinational networks, ensuring consistent compliance regardless of organisational complexity.
Finding Your Perfect Compliance Partner
Selecting the right web portal for your food production team requires careful consideration of several key factors. Start with usability – does the interface support intuitive navigation without extensive training? Next, evaluate cost-effectiveness by looking beyond upfront expenses to long-term ROI in terms of time savings and error reduction.
Training support and scalability are equally crucial. As your business grows and regulations evolve, you'll need a platform that can adapt without requiring complete system overhauls.
Integration capabilities represent another essential consideration. The ideal portal should seamlessly connect with your existing systems – from inventory management to quality control software – to eliminate data silos and create unified workflows.
Finally, prioritise industry-specific features designed specifically for food production environments, such as HACCP compliance tracking and temperature monitoring.
Q-Hub specialises in creating customised QHSE software solutions that address these specific requirements for food production teams. By focusing on digital transformation that enhances compliance, streamlines processes, and improves efficiency, Q-Hub enables organisations to achieve long-term growth while maintaining the highest safety and quality standards.
Ready to transform your food production team's approach to audits and inspections? Discover how Q-Hub's tailored digital solutions can streamline your compliance processes and boost operational efficiency today.
Start using Q-Hub today
- Manage compliance in one place
- Streamline your teams and tasks
- Use Q-Hub free for 30 days