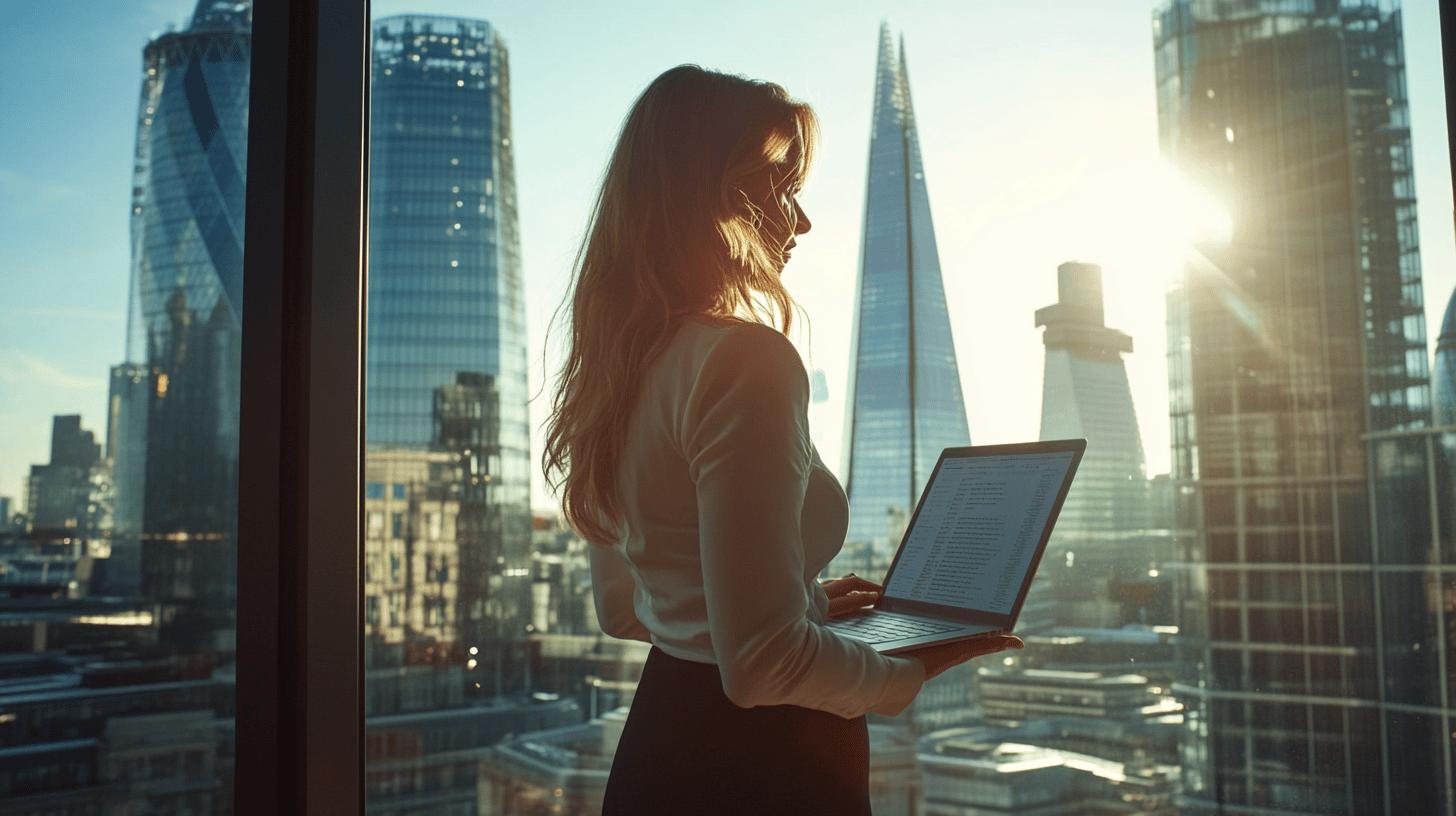
Integration with ERP Systems Enhances Risk Management
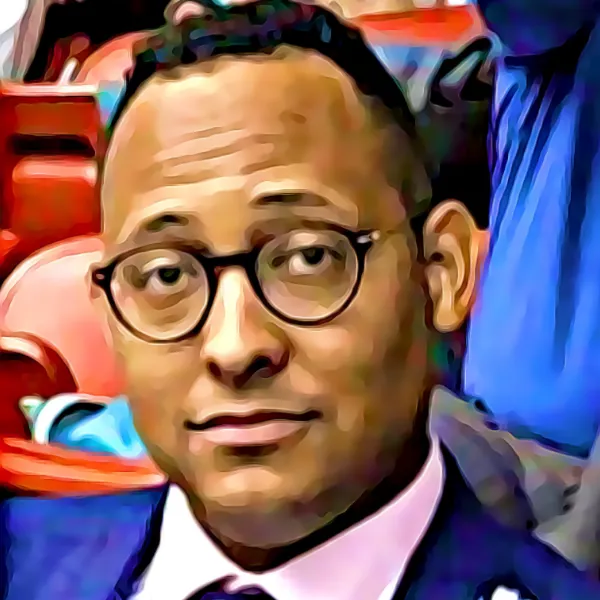
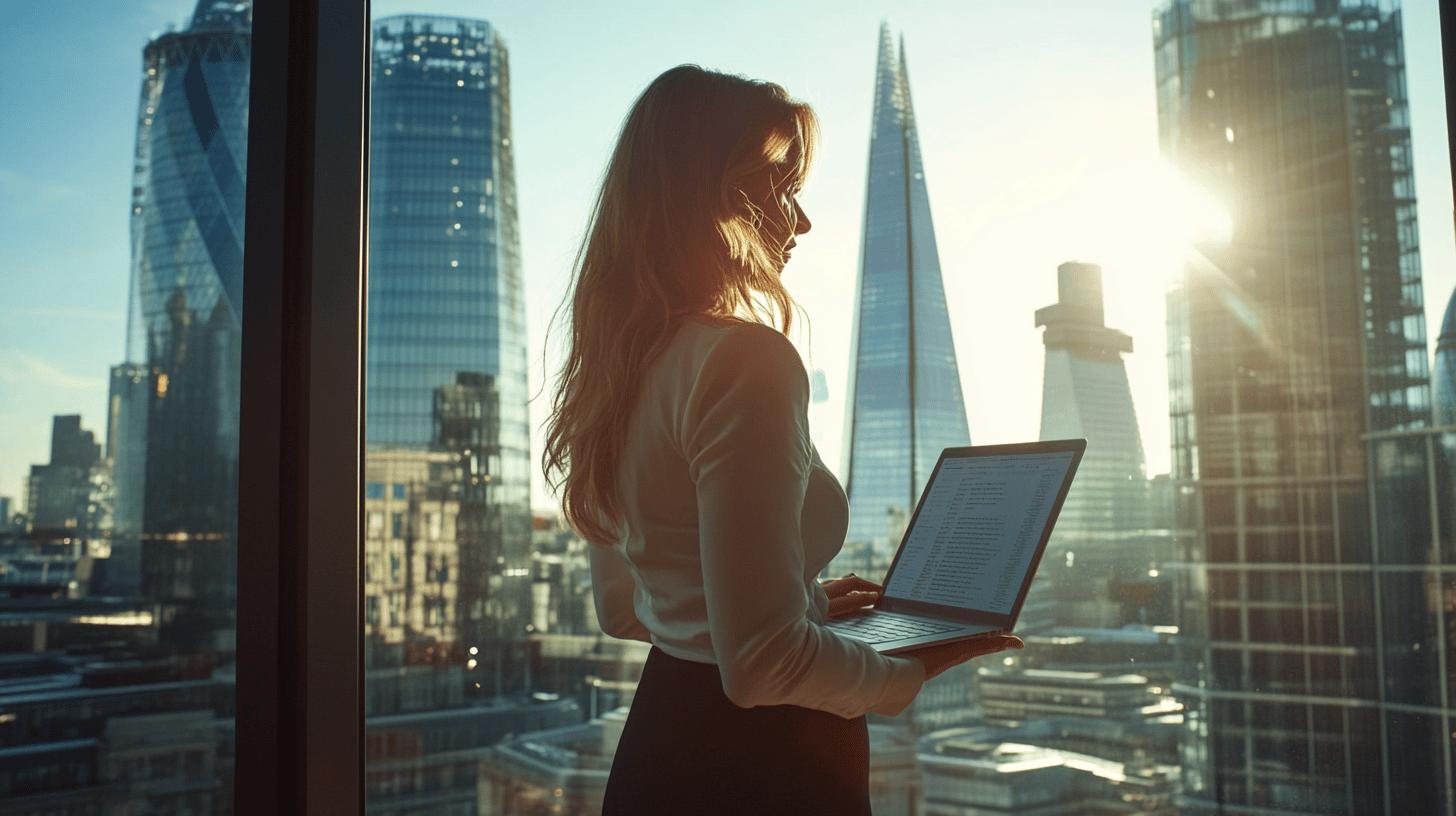
Integration with ERP Systems Enhances Risk Management
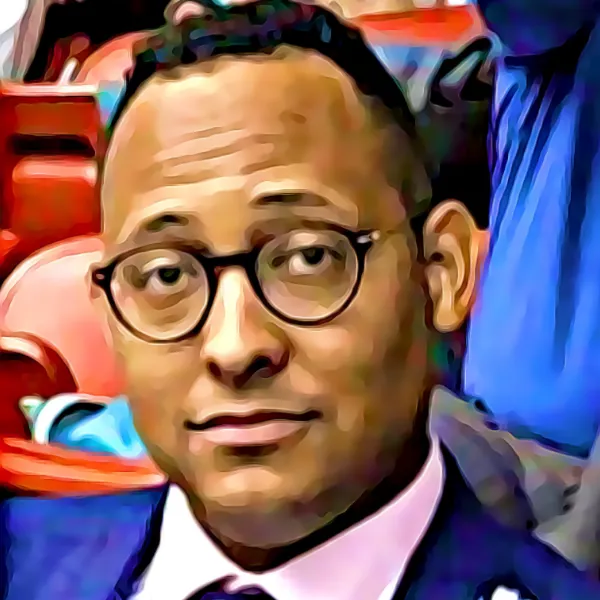
How ERP Integration Transforms Risk Management in Engineering Supply Chains
Integration with ERP systems improving risk management workflows in engineering supply chains has become essential for navigating today's complex industrial landscapes. These systems create a unified platform that connects departments, suppliers, and operations into a streamlined ecosystem. Q-Hub specialises in this digital transformation, helping engineering businesses transition from fragmented workflows to integrated systems that enable proactive risk management. Through automation, enhanced visibility, and advanced analytics, ERP integration replaces reactive approaches with predictive models—vital in engineering where precision and timing are critical.
Leveraging integration with erp systems empowers organizations to forecast risks with greater accuracy. This approach not only minimizes vulnerabilities but also drives efficient decision-making, ensuring that every process aligns with the dynamic demands of modern supply chains.
The implementation of systems that predict and mitigate risk exemplifies how digital transformation fortifies the precision required in today's engineering environments.
ERP platforms offer sophisticated tools that extend beyond basic monitoring. Compliance tracking ensures alignment with evolving regulations like ISO standards, while predictive analytics uses real-time data to forecast risks such as material shortages or supplier delays. This allows businesses to allocate resources effectively and address issues before they escalate. By automating repetitive tasks and maintaining centralised data, these systems provide the agility needed to navigate market shifts with minimal disruption.
- Real-time risk analysis
- Enhanced regulatory compliance
- Improved supplier performance
Key Benefits of ERP Systems for Engineering Supply Chain Efficiency
Engineering supply chains demand precision, adaptability and streamlined workflows. Without proper optimisation, inefficiencies quickly escalate into delays, miscommunication, and resource waste. By unifying procurement, inventory, and production planning, ERP systems create a solid foundation for improved efficiency. Companies that fail to adopt such systems often struggle with fragmented operations and missed opportunities for process automation.
Unlocking Productivity Through Intelligent Automation
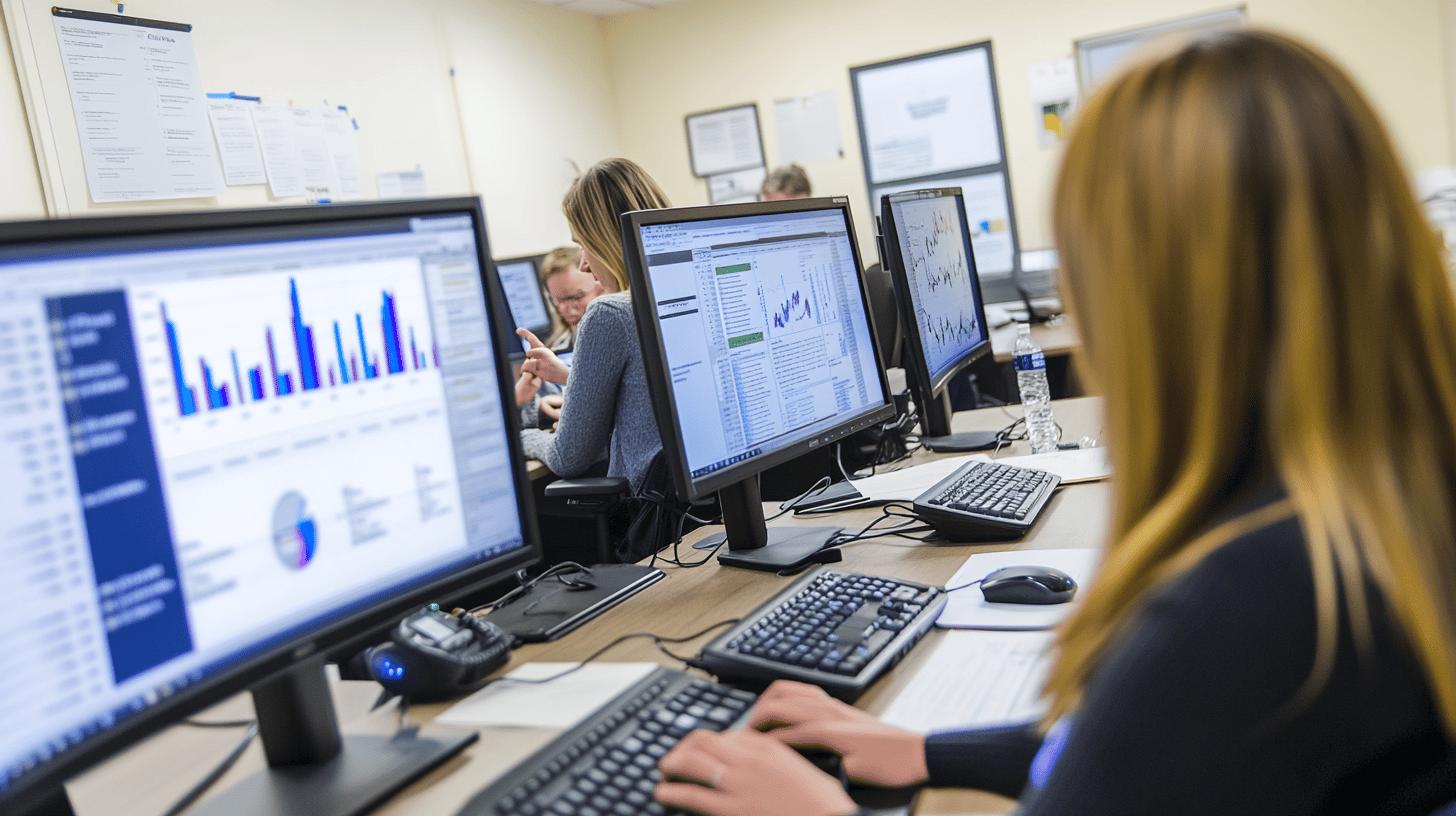
Automation represents one of the most transformative aspects of ERP integration. By handling repetitive tasks like order processing and inventory updates, these systems dramatically reduce manual errors while freeing staff to focus on strategic activities. For instance, procurement becomes more precise, ensuring materials are available without overstocking.
Integrating aspects of supplier and contractor management into ERP systems brings another layer of efficiency to risk management. This connectivity allows companies to monitor supplier reliability and contractor performance in real-time, drawing a parallel to a well-coordinated team where every member plays a critical role in maintaining balance and safety during operations.
By fostering stronger links between procurement and risk analysis, businesses can significantly reduce disruptions and ensure a smoother operational flow.
Production schedules can adapt dynamically to demand fluctuations, eliminating costly downtime.The efficiency gains extend beyond automation to create collaborative ecosystems. ERP platforms provide a single source of truth for all stakeholders, ensuring everyone works with the same information. Suppliers can track order statuses in real-time, while decision-makers gain instant visibility into inventory levels and production bottlenecks. This interconnectedness enables better resource allocation and faster responses to disruptions.
<table border="0"> <tr><th>Feature</th><th>Impact on Supply Chain</th></tr> <tr><td>Centralised Data Management</td><td>Eliminates information silos and reduces communication errors</td></tr> <tr><td>Automated Workflows</td><td>Reduces manual processing time by up to 70%</td></tr> <tr><td>Real-time Inventory Tracking</td><td>Decreases stockouts and overstock situations</td></tr> <tr><td>Predictive Analytics</td><td>Enables proactive risk management and resource planning</td></tr> </table>How ERP Systems Reduce Risks in Supply Chains
Unifying ERP systems into supply chain processes creates a dynamic approach to operational risk management, where potential issues can be anticipated and mitigated proactively. Without this integration, engineering supply chains often struggle with fragmented workflows, outdated information, and unpredictable disruptions. Q-Hub's solutions address these challenges by implementing systems that enable businesses to respond effectively to unforeseen challenges, ensuring operational stability.
Transforming Compliance into a Competitive Advantage
Automation significantly reduces supply chain risks. Tasks like compliance monitoring, once tedious and error-prone, become streamlined to ensure adherence to regulations such as ISO 9001 or ISO 45001. These systems leverage predictive analytics to forecast issues like supplier delays or inventory shortages well in advance. For example, when a supplier consistently delivers late, the ERP system highlights this trend, allowing you to take corrective action before it impacts production.
Real-time data access minimises risks related to outdated information. In complex supply chains with multiple stakeholders, timely and accurate data is critical. ERP systems create a single source of truth, ensuring everyone works with current information. When material availability suddenly changes, decision-makers can immediately adapt production schedules to avoid costly delays.
- Automated compliance monitoring
- Early risk identification through data analysis
- Comprehensive supplier performance evaluation
- Centralised real-time information access
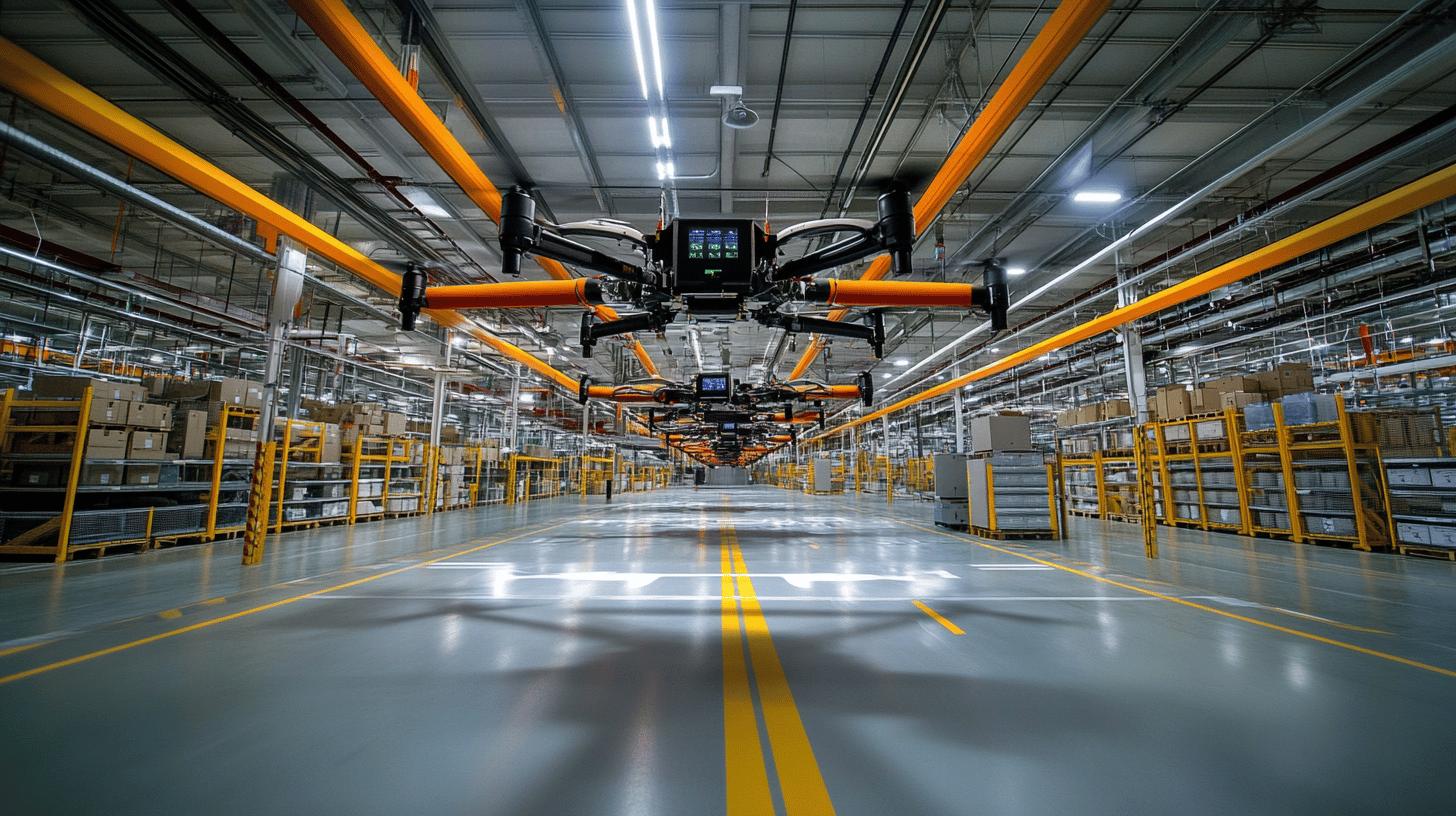
Case Studies: ERP Integration Success Stories in Engineering Supply Chains
The integration of ERP systems to improve risk management in engineering supply chains delivers measurable results across various industries. Q-Hub has helped numerous organisations transform their operations through customised software solutions. These real-world examples demonstrate how businesses have successfully navigated supply chain challenges through effective digital transformation.
From Paper to Digital: Streamlining Compliance at Anglia Cathodic Protection
Anglia Cathodic Protection Services faced challenges with their paper and spreadsheet-based systems as their workload and client base grew. Their fragmented processes hindered effective compliance management across multiple sites. By implementing Q-Hub's platform, they digitalised previously disjointed systems, making information more accessible and actionable for all employees. The new system enabled scheduled audits and improved compliance monitoring, eliminating bottlenecks that had previously slowed operations.
"Tracking NCRs was a challenge, with resolutions often delayed due to the lack of a structured system. Q-Hub's Process Hub provided a centralised space for managing NCRs, linking them to audits, and ensuring accountability at each step."
Revolutionising Safety Management at Rocal
Rocal Insulating Panels struggled with paper-based processes and fragmented data systems for managing their Safety Management System. Their accident reporting and non-conformance tracking were time-consuming and error-prone. Q-Hub transformed their approach by centralising document control through a digital library with version tracking and instant access. This eliminated hours of wasted time searching for critical files and improved overall compliance efficiency.
The automation of accident reporting and investigation processes was particularly impactful. Managers previously struggled with incomplete records and lengthy investigation delays. With Q-Hub's automated workflows, resolutions became quicker, with better departmental manager involvement and more detailed reporting capabilities.
Unifying Operations at Fowlers of Bristol
Fowlers of Bristol faced operational hurdles due to outdated, paper-based systems and siloed data processes. Communication between teams relied heavily on emails and in-person follow-ups, creating delays. After implementing Q-Hub's portal, they brought all critical workflows and communications into a single digital space, enabling instant access to real-time data and fostering collaboration between engineering teams, shop floor workers, and compliance managers.
<table border="0"> <tr><th>Company</th><th>Challenge</th><th>Solution</th><th>Result</th></tr> <tr><td>Anglia Cathodic Protection</td><td>Fragmented compliance management</td><td>Centralised digital platform</td><td>Enhanced operational oversight and accountability</td></tr> <tr><td>Rocal Insulating Panels</td><td>Time-consuming safety management</td><td>Automated workflows and reporting</td><td>Faster resolution and improved visibility</td></tr> <tr><td>Fowlers of Bristol</td><td>Siloed communication and data</td><td>Integrated portal with real-time access</td><td>Improved collaboration and decision-making</td></tr> </table>Best Practices for Successful ERP Implementation in Risk Management
Integrating ERP systems to enhance risk management workflows in engineering supply chains requires careful planning. The process presents several challenges, including data migration, user adoption, and aligning system functionalities with business goals. Q-Hub's experience in digital transformation has shown that addressing these challenges methodically leads to successful implementations.
Overcoming Implementation Hurdles with Strategic Planning
Data migration represents one of the most significant challenges. Transferring information from legacy systems requires meticulous planning to avoid inaccuracies or data loss. Equally important is the human factor—staff need proper training and support to become proficient with new systems. Without adequate guidance, resistance to change can stall the implementation process and limit the benefits realised.
Aligning ERP functionalities with specific business objectives is crucial for success. When implementing risk management solutions, organisations should conduct thorough needs assessments to identify their unique requirements. This ensures the system addresses actual pain points rather than becoming an underutilised expense.
- Conduct thorough needs analysis before implementation
- Invest in comprehensive user training and support
- Prioritise data accuracy during migration
- Ensure ERP functionalities align with business goals
- Choose scalable solutions that can grow with your business
By taking a structured approach to implementation, engineering businesses can maximise the value of ERP integration in managing supply chain risks. Q-Hub's implementation methodology focuses on ensuring systems are tailored to organisational needs while providing the support necessary for successful adoption across all levels of the business.
Future Trends: The Role of Advanced ERP Features in Supply Chain Risk Management
The integration of ERP systems for improving risk management in engineering supply chains continues to evolve with emerging technologies. Q-Hub remains at the forefront of these developments, incorporating cutting-edge capabilities into their solutions. Technologies like Internet of Things (IoT) and Artificial Intelligence are redefining what ERP platforms can achieve in risk management.
Embracing Smart Technologies for Predictive Risk Management
IoT sensors now provide real-time updates on inventory levels, equipment performance, and logistics, enabling supply chains to address potential disruptions before they occur. AI algorithms analyse vast datasets to forecast risks such as supplier delays or demand fluctuations, offering proactive rather than reactive solutions. This convergence transforms risk management into a predictive, data-driven process that far surpasses traditional approaches.
Enhanced cybersecurity features are becoming increasingly important as supply chains grow more interconnected. Advanced ERP systems now incorporate robust security protocols to safeguard sensitive information across global networks. On the analytics front, predictive maintenance tools use real-time data to identify potential equipment failures before they happen, allowing organisations to schedule maintenance proactively and prevent costly disruptions.
As engineering supply chains continue to face complex challenges, Q-Hub's software solutions evolve to provide the tools needed for effective risk management. By embracing these technological advancements and integrating
Start using Q-Hub today
- Manage compliance in one place
- Streamline your teams and tasks
- Use Q-Hub free for 30 days