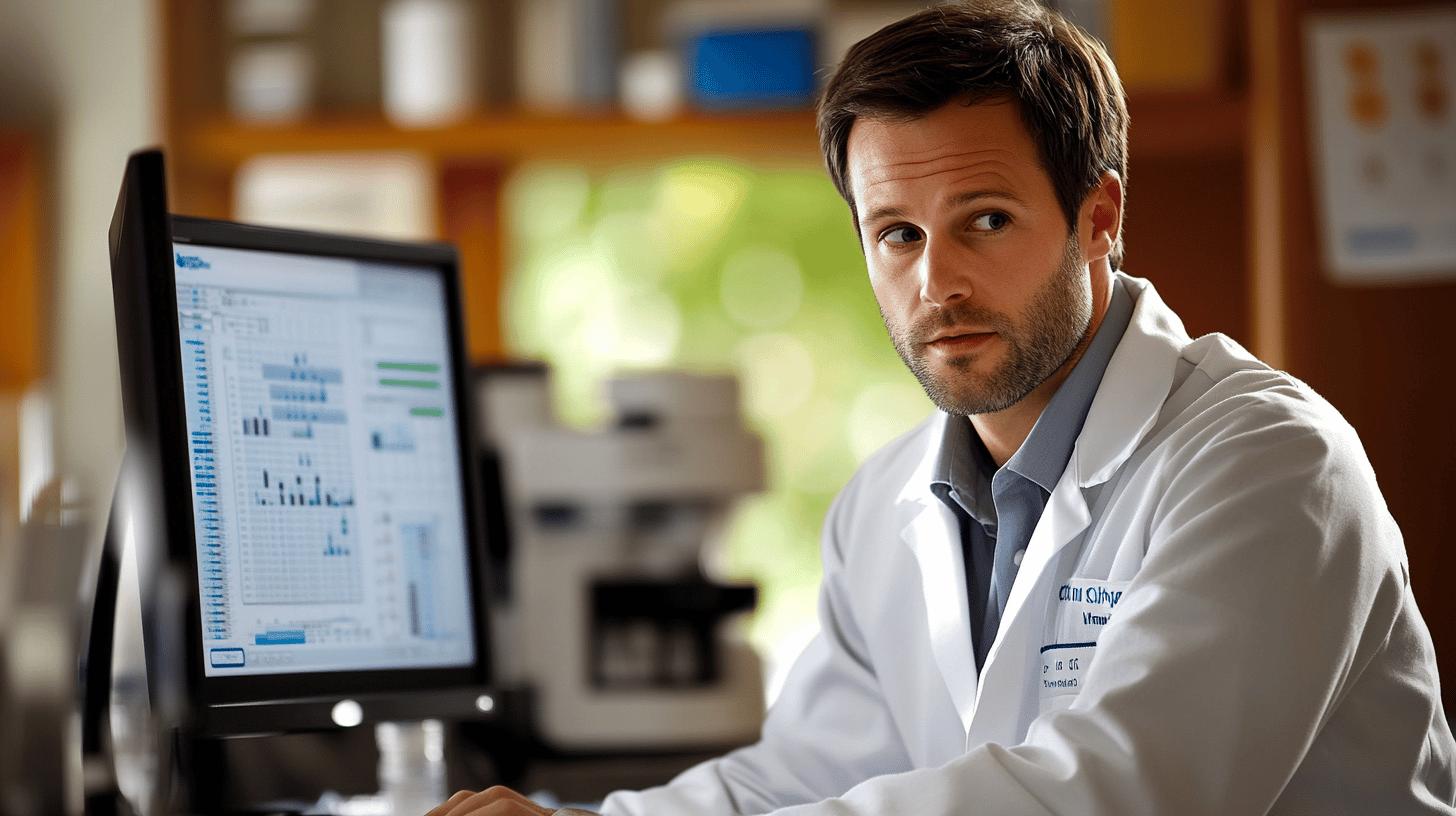
Integration with ERP Systems Boosts Safety in Pharma
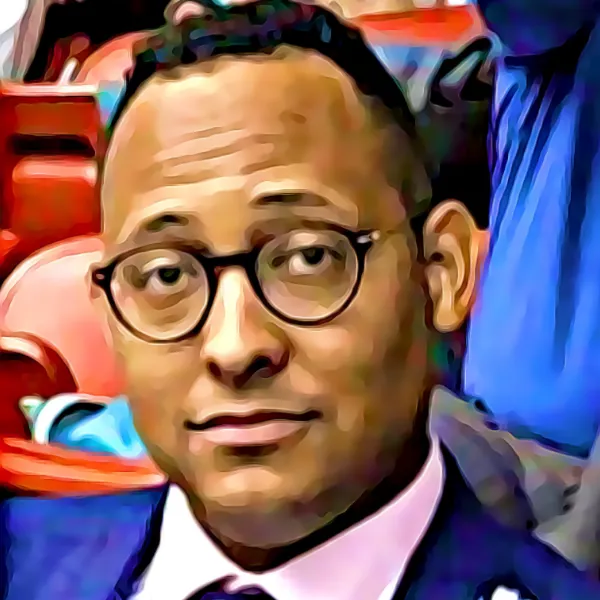
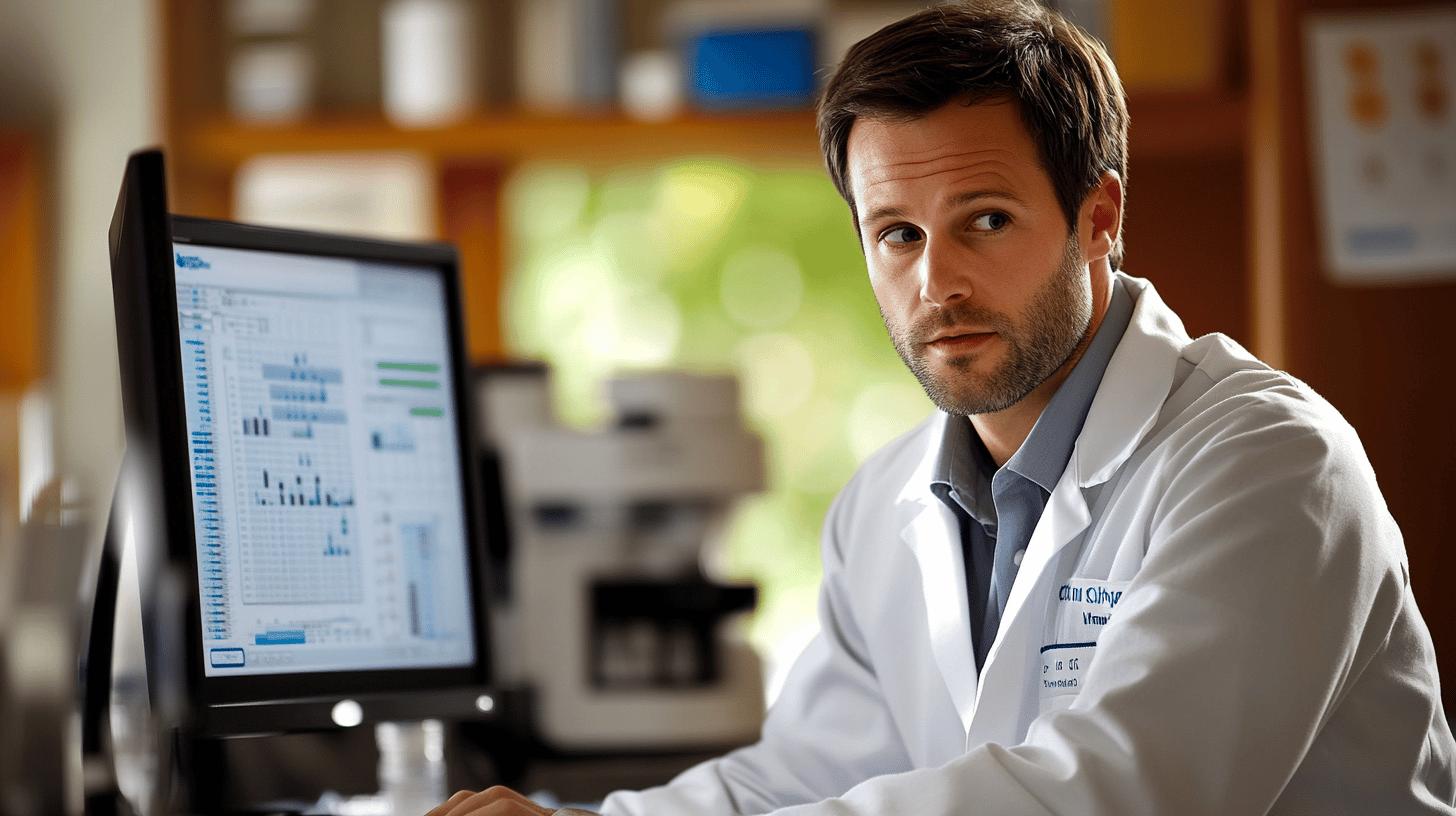
Integration with ERP Systems Boosts Safety in Pharma
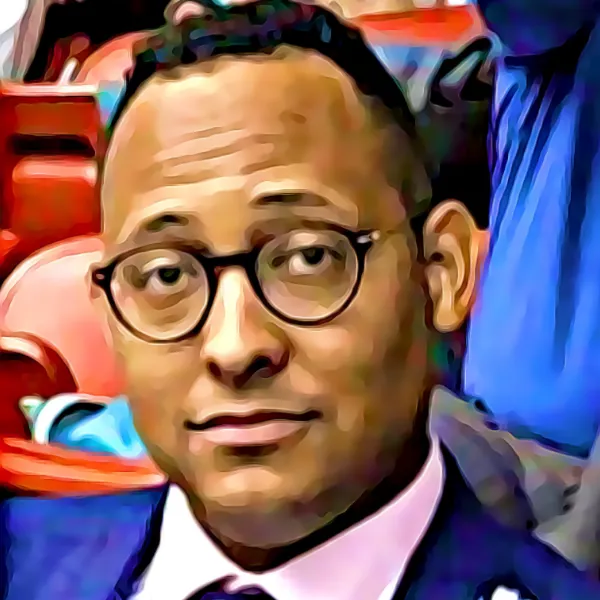
How Integrating ERP Systems Refines Safety Management Workflows in Pharmaceutical Facilities
Integration with ERP systems is transforming safety management in pharmaceutical facilities by creating unified platforms that streamline compliance processes and enhance operational efficiency. This digital convergence breaks down departmental silos, providing a centralised hub for safety data that enables proactive risk management while satisfying stringent regulatory requirements.
The impact on pharmaceutical operations is substantial. By connecting previously fragmented systems, ERP integration delivers measurable improvements in compliance rates and incident response times. Q-Hub's experience implementing such solutions has shown that properly configured systems can reduce safety-related downtime by up to 30% while significantly enhancing regulatory compliance.
The true power of ERP integration in pharmaceutical safety lies not just in the technology itself, but in how it transforms organisational culture toward proactive risk management.
Transforming Compliance Through Digital Integration
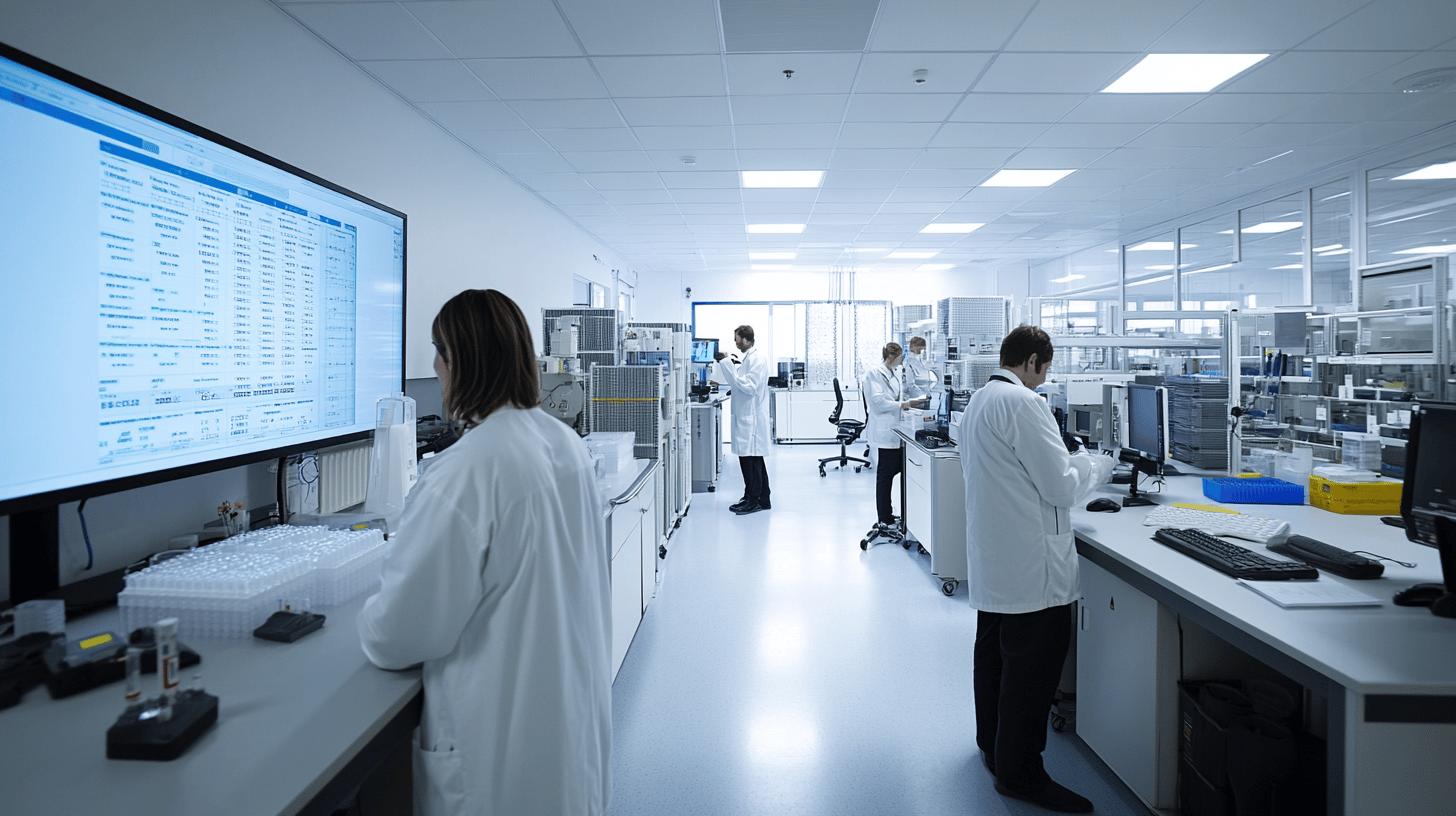
Modern pharmaceutical facilities face complex safety challenges that manual systems struggle to address effectively. The integration of ERP systems provides a structured framework that eliminates regulatory blind spots and operational inefficiencies.
This digital transformation extends beyond mere automation. When properly implemented, ERP systems create a compliance ecosystem where safety protocols become embedded in daily operations rather than existing as separate processes.
In the case of Weston Aerospace, implementing a centralised compliance platform resulted in a dramatic reduction in audit preparation time. Their legacy systems required days of manual work to compile regulatory documentation, but after ERP integration, this was reduced to hours—a transformation that mirrors what's possible in pharmaceutical environments.
Key Benefits That Drive Operational Excellence
Pharmaceutical operations experience several distinct advantages when implementing integrated ERP safety solutions. The most significant improvements include:
- Automated regulatory reporting - Systems that continuously track compliance against MHRA and HSE standards, generating real-time reports that once required days of manual compilation
- Centralised compliance tracking - A unified platform providing comprehensive visibility across multiple facilities, enabling trend identification and proactive gap management
- Predictive risk management - Advanced analytics that identify potential safety issues before they develop into incidents, particularly valuable for maintenance scheduling and equipment monitoring
- Streamlined incident response - Automated workflows that accelerate reporting, investigation and resolution of safety events while maintaining comprehensive documentation
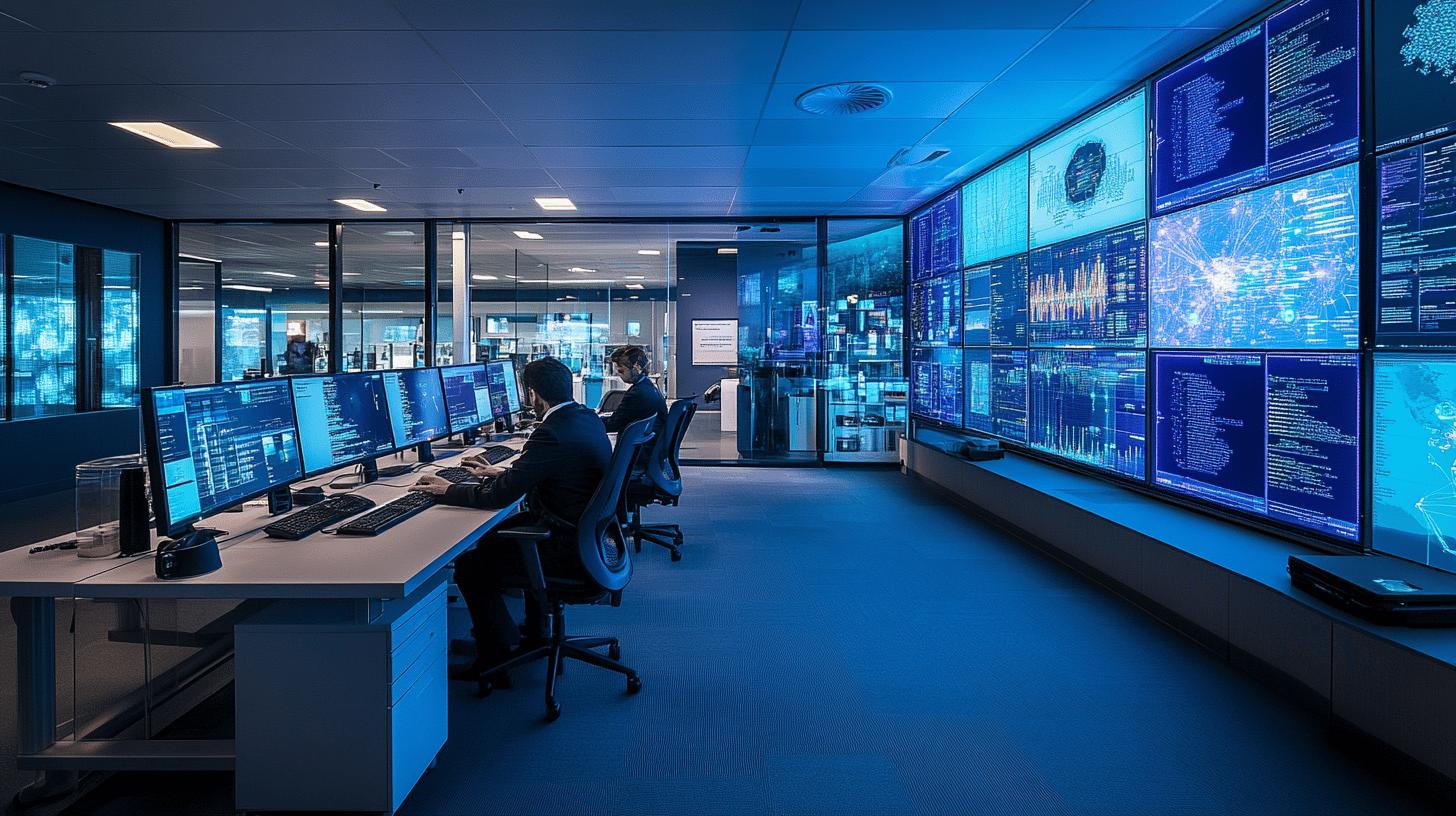
These benefits translate into measurable operational improvements. Companies implementing comprehensive ERP safety systems typically see significant reductions in compliance-related administrative work alongside improved safety outcomes.
<table border="0"> <tr><th>Safety Management Metric</th><th>Before ERP Integration</th><th>After ERP Integration</th></tr> <tr><td>Audit Preparation Time</td><td>1-2 weeks</td><td>1-2 days</td></tr> <tr><td>Incident Response Time</td><td>24-48 hours</td><td>2-4 hours</td></tr> <tr><td>Compliance Documentation Errors</td><td>15-20%</td><td>Under 5%</td></tr> <tr><td>Preventable Safety Incidents</td><td>Baseline</td><td>25% reduction</td></tr> </table>Essential Features That Power Safety Excellence
The most effective ERP implementations for pharmaceutical safety management incorporate several critical capabilities that work in concert to elevate operational safety:
Automated safety audits provide systematic compliance verification against regulatory frameworks like those established by the MHRA. These systems replace sporadic manual checks with continuous monitoring, ensuring consistent application of safety standards across facilities.
Incident management solutions transform how facilities handle safety events. When a chemical spill or equipment malfunction occurs, these systems enable immediate digital documentation, assign corrective actions, and track resolution—all from a central platform that maintains complete audit trails.
Real-time monitoring dashboards deliver actionable safety intelligence to managers. For example, Scottish Leather Group implemented similar monitoring systems through Q-Hub that transformed their visibility into safety metrics across multiple facilities, providing early warning of potential compliance issues.
Advanced Risk Assessment Integration
Modern ERP systems incorporate sophisticated risk assessment tools that continuously evaluate facility operations. These tools can identify that a production line frequently operates near safety thresholds during peak production periods and automatically generate preventive maintenance schedules or operational adjustments to maintain safety margins.
Implementation Best Practices for Pharmaceutical Environments
Successfully integrating ERP systems requires a structured approach that addresses the unique challenges of pharmaceutical operations. The following framework has proven effective across multiple implementations:
Comprehensive needs assessment forms the foundation of successful implementation. This process identifies specific pain points in existing safety workflows—such as manual compliance reporting or delayed incident response—and maps them to appropriate ERP capabilities.
Meticulous data migration ensures operational continuity during transition. This includes validation of historical compliance records, incident reports, and safety documentation. Proper validation prevents data integrity issues that could compromise safety or regulatory standing.
Cross-functional collaboration is essential for adoption. When Fowlers of Bristol implemented their compliance platform with Q-Hub, they found that early involvement of shop floor staff, compliance teams, and management was crucial for successful adoption and sustained engagement.
Phased implementation reduces disruption while managing costs. Many facilities begin with core safety functions like incident reporting before expanding to more complex capabilities such as predictive maintenance or advanced risk assessment.
Overcoming Implementation Challenges
Pharmaceutical facilities face several common obstacles when integrating ERP systems into safety workflows. Understanding these challenges in advance allows for effective mitigation strategies:
Legacy system compatibility often presents the first hurdle. Many facilities rely on older software not designed to communicate with modern ERP platforms. This typically requires either system upgrades or implementation of middleware solutions that bridge technological gaps.
Data migration complexity can undermine implementation if not properly managed. The solution lies in comprehensive validation protocols and staged migrations that verify data integrity at each step. This approach mirrors how Q-Hub helped BMC Analysis transition from fragmented spreadsheet-based systems to a unified digital platform.
Staff resistance frequently emerges during implementation. The most effective countermeasure involves early stakeholder engagement combined with role-specific training. When staff understand how the system simplifies their daily responsibilities rather than adding complexity, adoption rates significantly improve.
Budget constraints can limit implementation scope. A modular approach that prioritises high-impact safety functions allows facilities to spread investment over time while demonstrating early value that justifies continued development.
Future-Proofing Pharmaceutical Safety Management
ERP systems for pharmaceutical safety continue to evolve rapidly, with several emerging technologies poised to further transform operations:
AI-driven predictive analytics represents the most significant advancement on the horizon. These systems analyse operational patterns to identify potential safety issues before they manifest, shifting facilities from reactive to truly preventive safety management.
Cloud-based platforms are becoming increasingly important for multi-site operations. They provide real-time safety data access regardless of location, enabling consistent application of safety protocols across distributed facilities while simplifying regulatory reporting.
IoT integration is expanding the scope of safety monitoring. Connected sensors continuously monitor equipment status, environmental conditions, and even personnel movements, feeding data to ERP systems for comprehensive risk analysis.
These technological advancements aren't merely theoretical—they're already delivering measurable improvements in pharmaceutical operations. Facilities implementing these capabilities report significant enhancements in compliance rates, incident reduction, and operational efficiency.
Q-Hub specialises in helping pharmaceutical facilities navigate this digital transformation journey, delivering customised safety management solutions that address specific operational challenges while ensuring regulatory compliance. By combining deep industry knowledge with flexible implementation methodologies, Q-Hub enables pharmaceutical operations to achieve new levels of safety excellence through streamlined digital workflows and comprehensive compliance oversight.
Start using Q-Hub today
- Manage compliance in one place
- Streamline your teams and tasks
- Use Q-Hub free for 30 days