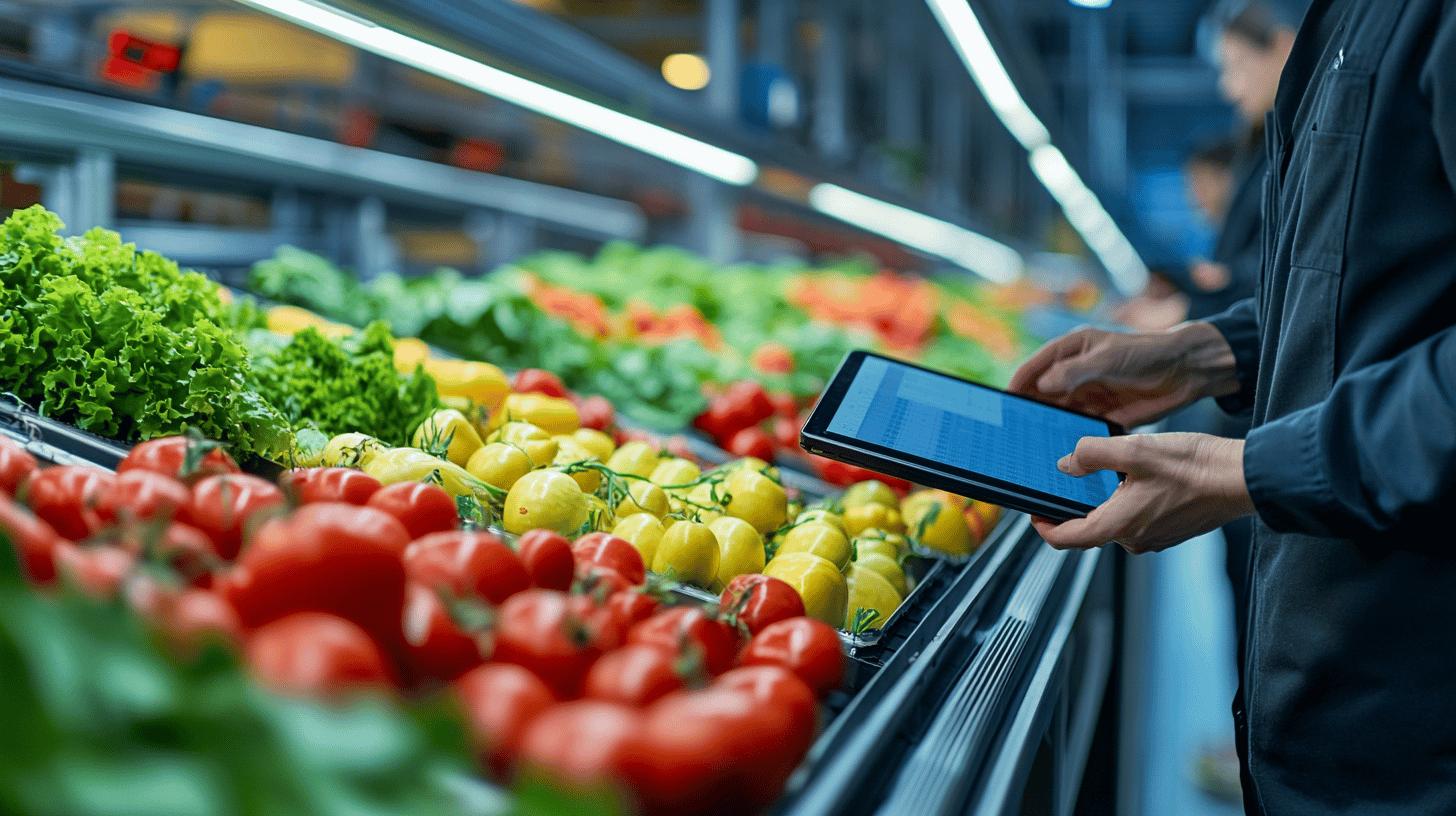
ERP Integration Boosts Compliance in Food Production
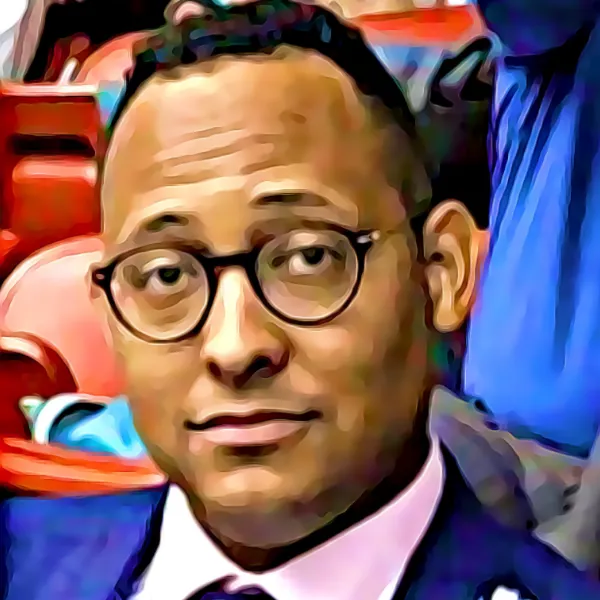
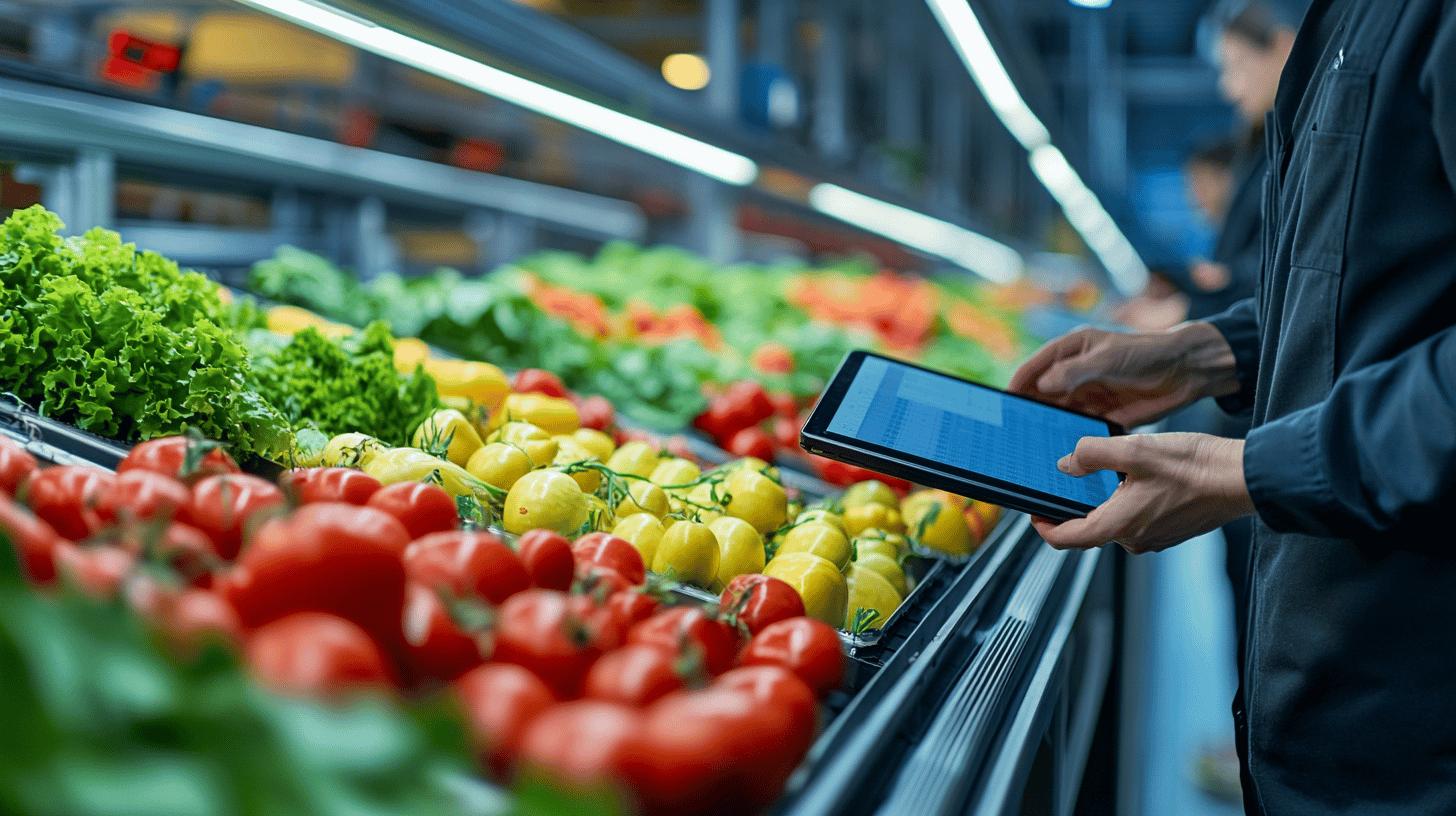
ERP Integration Boosts Compliance in Food Production
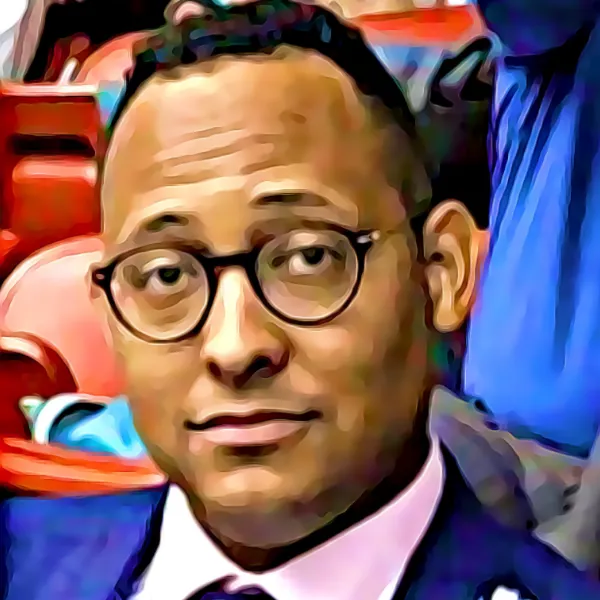
How ERP Integration Enhances Compliance Management in Food Production Lines
ERP integration enhancing compliance management across food production lines has transformed from luxury to necessity. Q-Hub's software solutions simplify the complex web of food safety regulations by embedding compliance directly into operational workflows. These systems consolidate fragmented processes, offering real-time monitoring and robust reporting capabilities that build a foundation for both efficiency and regulatory adherence.
Modern ERP systems proactively reduce compliance risks before they escalate. Real-time monitoring alerts teams to potential deviations, while automated compliance checks handle repetitive tasks like verifying supplier certifications and ensuring traceability—all without excessive manual intervention.
The Backbone of Food Safety Compliance
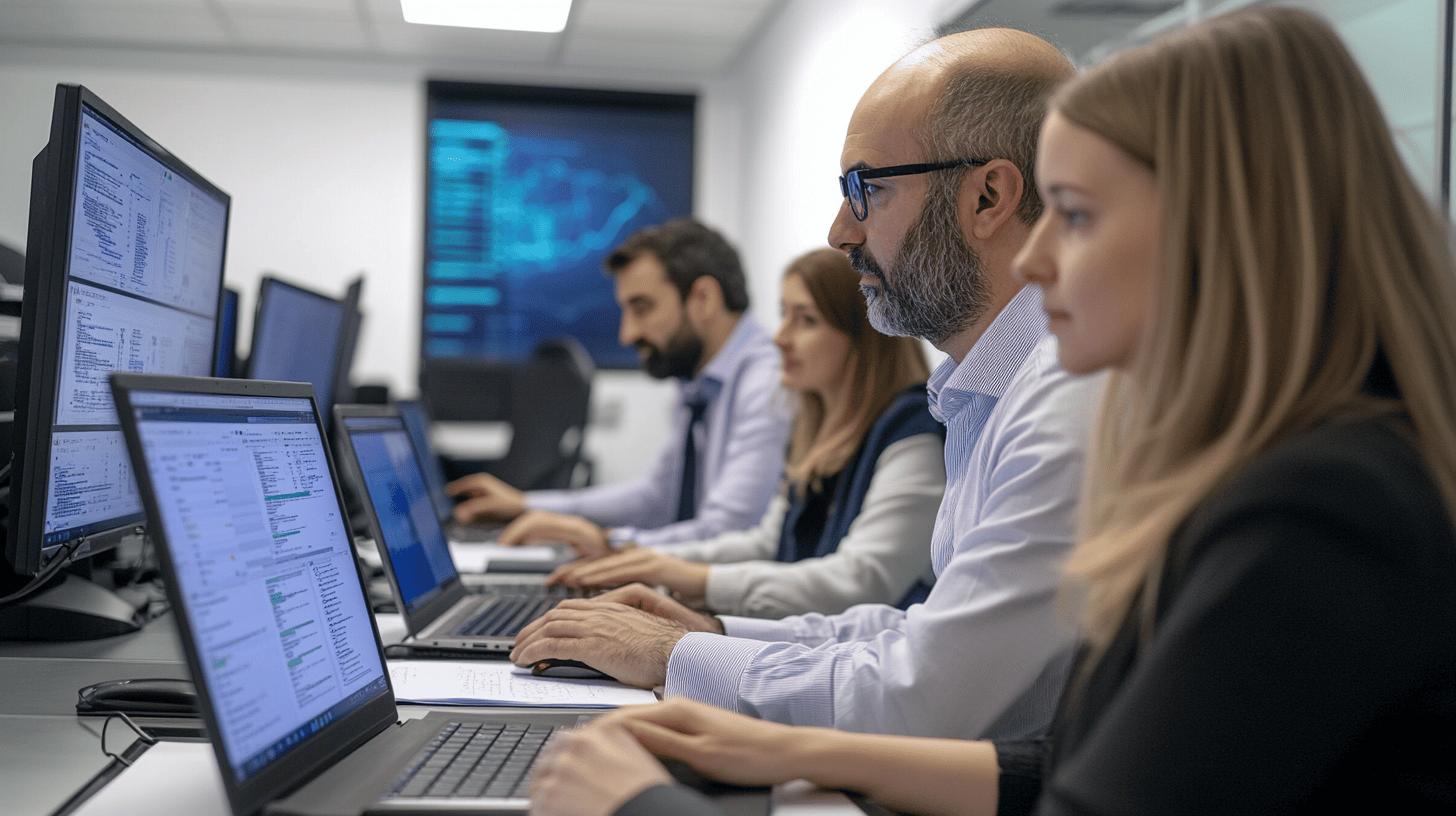
One of the most powerful aspects of integrated ERP systems is their ability to centralise operational data. This creates a single source of truth that eliminates the inconsistencies that often plague paper-based or fragmented systems. For food manufacturers, this means having instant access to critical compliance documentation when it matters most.
This integration is particularly valuable for companies managing complex supply chains with multiple ingredients and production stages. Every component can be tracked from source to finished product, ensuring complete visibility throughout the manufacturing process.
By transforming how we approach compliance, ERP systems don't just help us meet regulations—they embed quality control into our daily operations, making excellence the default rather than the exception.
- Automated compliance checks streamline certification verification
- Real-time monitoring detects deviations from standards immediately
- Centralised documentation simplifies audit preparation
- Risk tracking identifies compliance vulnerabilities before they become problems
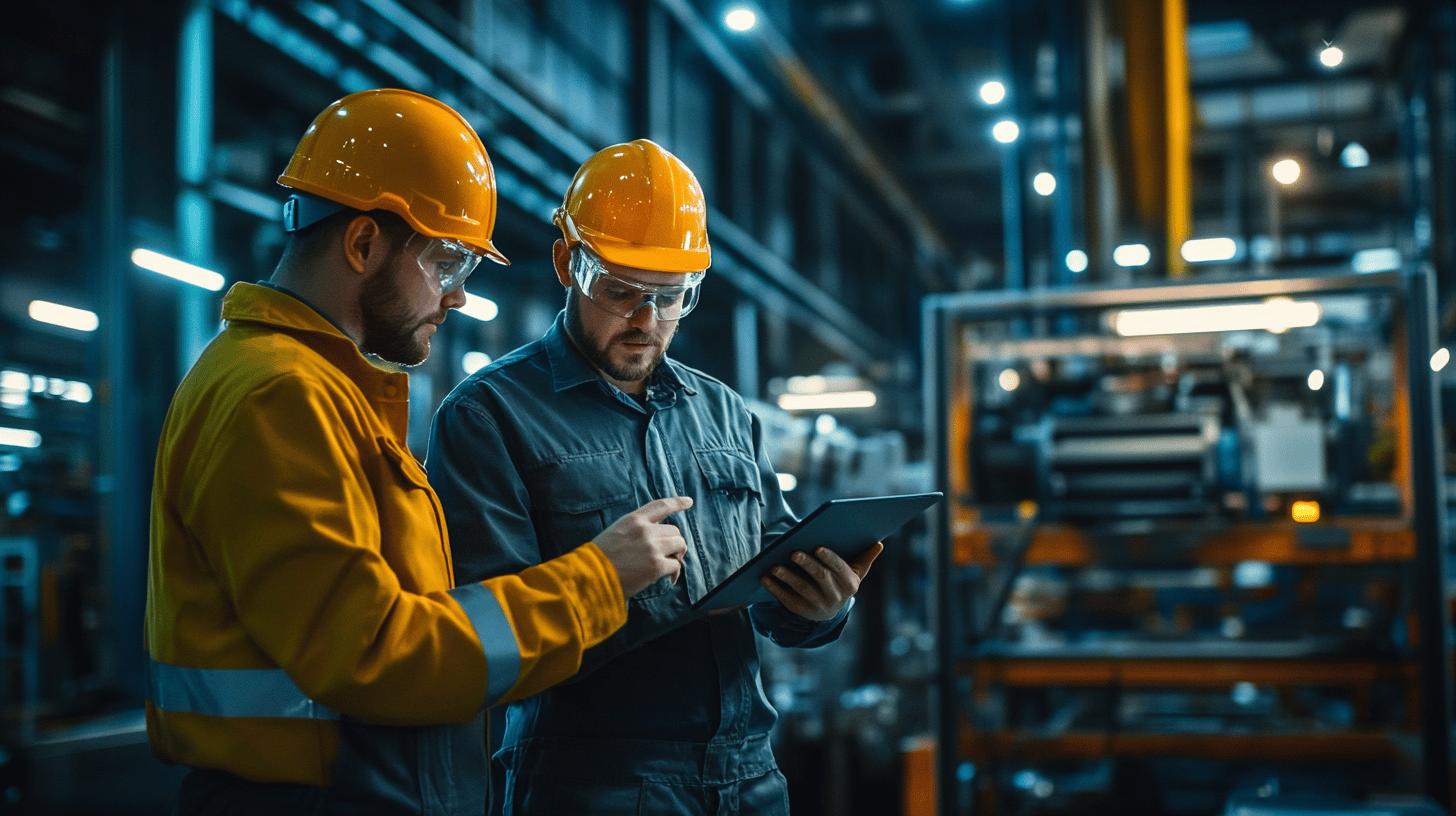
Mastering Traceability and Recall Management
In food production, comprehensive traceability isn't optional—it's essential. ERP systems excel in providing end-to-end visibility of every ingredient and product batch throughout the supply chain. If contamination concerns arise, these systems can quickly pinpoint affected batches, minimising recall scope and protecting consumer safety.
Compliance reporting tools within these systems track key data points like supplier certifications and production timestamps, generating audit-ready reports with minimal effort. This level of detail ensures regulatory compliance while enabling swift action during critical situations.
<table border="0"> <tr><th>Feature</th><th>Function</th><th>Benefit</th></tr> <tr><td>Batch Tracking</td><td>Monitors materials from receipt to finished product</td><td>Enables precise recalls and ensures compliance</td></tr> <tr><td>Automated Alerts</td><td>Notifies teams of deviations in real-time</td><td>Prevents compliance issues before escalation</td></tr> <tr><td>Supplier Management</td><td>Verifies supplier compliance with standards</td><td>Reduces non-compliant material risks</td></tr> </table>Transforming Audit Readiness
Traditional audit preparation often means scrambling to piece together records from multiple systems—a frustrating and time-consuming process. ERP systems eliminate this challenge by centralising all operational data in one accessible platform, creating complete, transparent audit trails that document every action.
With Q-Hub's solutions, food manufacturers can access detailed, transparent records with a few clicks instead of digging through emails or spreadsheets. Automated workflows ensure quality assurance processes are followed consistently, turning audit preparation from a headache into a routine activity.
- Centralise operational data for immediate access during audits
- Automate workflows to standardise compliance processes
- Maintain clear audit trails of all production activities
- Generate accurate, audit-ready documentation quickly
Bridging Technology Gaps for Seamless Integration
While the benefits of ERP integration are clear, implementation isn't without challenges. IT and OT systems often speak different "languages," making communication difficult. Data silos, outdated storage methods, and inconsistent formats further complicate integration efforts.
For multi-site operations, these issues multiply exponentially. Each location may operate under different protocols, creating disjointed processes and compliance gaps. Successful implementation requires addressing these challenges with careful planning and specialised expertise—precisely what Q-Hub offers through its tailored solutions.
- Conduct thorough system assessments to identify compatibility issues early
- Use advanced technologies to automate data mapping and streamline integration
- Ensure cross-departmental collaboration throughout implementation
- Implement phased rollouts to address location-specific challenges
Measuring Real-World ROI from Compliance Integration
The investment in ERP integration delivers measurable returns beyond improved compliance. By reducing manual errors and streamlining resource allocation, these systems allow businesses to operate with greater precision and lower costs. This is particularly valuable in food manufacturing, where margins can be tight and efficiency paramount.
Before ERP integration, many food producers rely on fragmented processes and manual data entry, increasing labour costs and compliance risks. After implementation, production volumes can align with demand forecasts, reducing waste, while automated compliance workflows cut audit preparation time dramatically.
<table border="0"> <tr><th>Metric</th><th>Before Integration</th><th>After Integration</th></tr> <tr><td>Audit Preparation</td><td>Days of work</td><td>Hours of work</td></tr> <tr><td>Traceability Speed</td><td>Hours to trace issues</td><td>Minutes to trace issues</td></tr> <tr><td>Compliance Visibility</td><td>Limited, delayed reporting</td><td>Real-time dashboards</td></tr> </table>Learning from Success Stories
The Scottish Leather Group demonstrates how effective compliance management systems can transform operations. Before implementing Q-Hub's solution, they struggled with paper-based systems across multiple sites, making ISO compliance a resource-intensive challenge. Their digital transformation journey resulted in significantly reduced audit preparation time and streamlined communication between departments and sites.
Similarly, Weston Aerospace leveraged Q-Hub's platform to overcome inefficiencies in their compliance processes. Legacy systems that failed to deliver actionable data were replaced with a comprehensive solution that streamlined audit scheduling, reporting, and NCR management. This transformation freed staff from repetitive tasks to focus on strategic improvements.
These case studies emphasise that successful implementations share common elements: customisable solutions addressing unique compliance needs, proactive monitoring strategies, and automation of repetitive tasks to free resources for strategic activities.
As regulatory demands continue to evolve, Q-Hub's software solutions provide food manufacturers with the tools to adapt quickly while maintaining operational efficiency. By centralising compliance management, automating critical processes, and providing real-time visibility, these systems transform regulatory requirements from burdens into opportunities for operational excellence.
Ready to transform your food production compliance management? Discover how Q-Hub's tailored ERP solutions can help you achieve regulatory excellence while driving operational efficiency.
Start using Q-Hub today
- Manage compliance in one place
- Streamline your teams and tasks
- Use Q-Hub free for 30 days